前言:臻驅科技(上海)有限公司(以下簡稱“臻驅科技”)是一家以研發、生產和銷售新能源車動力總成及其功率半導體模塊為核心業務的高科技公司。2019年底,臻驅科技與日本羅姆半導體公司成立了聯合實驗室,并簽訂戰略合作協議,合作內容包含了基于某些客戶的需求,進行基于羅姆碳化硅芯片的功率半導體模塊,及對應電機控制器的開發。本文即介紹臻驅對碳化硅功率模塊的開發、測試及系統評估。
?
Introduction
碳化硅功率半導體近年來在能源轉換應用中正在成為一個熱門的話題:由于材料屬性,使得它具有比硅基半導體器件更高的最大結溫、更小的損耗,以及更小的材料熱阻系數等。
?
因此,很多人宣稱,當碳化硅功率器件應用于能源轉換后,變頻器系統將有更高的功率密度、更小的體積、更高的允許工作溫度,以及更低的損耗,從而給應用系統帶來更大優勢。
?
臻驅科技計劃將碳化硅芯片封裝至功率模塊,并應用于新能源車的電機驅動器中(以下簡稱“電控”),用于取代其現有的硅基IGBT功率模塊(峰值功率約為150?kW)。
?
進行開發之前,應用者需要進行評估,哪些碳化硅的特性能給主驅應用帶來最大的價值。例如,對于此類DC-AC的拓撲結構,碳化硅技術的導入對于電控體積的減小并沒有顯著的作用,因為電控的體積主要取決于其各子部件的封裝技術而功率模塊只占其中很小的百分比;另一些人宣稱可以利用碳化硅更高工作結溫的優勢,少安裝芯片數量并使其工作在高溫,從而降低成本。也許,此特性適用于如地下鉆探等環境溫度很高的應用,但對于新能源車而言,是否有必要將結溫推高而犧牲效率(注:碳化硅在高溫下的損耗會顯著增加),以及是否因為節省了芯片數量就能節省系統成本,是需要被質疑的。
?
在臻驅看來,碳化硅技術應用于主驅電控的主要系統優勢,是在于效率的提升,以及峰值輸出功率的增加。前者可以提升續航里程或減少電池安裝數量,后者可以給整車帶來更大的百公里加速度。臻驅第一款開發的是750V的碳化硅模塊,針對A級及以上的乘用車型;第二款是1200V碳化硅模塊,應用于800V系統的乘用車或商用車。在臻驅開發的碳化硅模塊中,臻驅采用的是羅姆最新的第四代750V及1200V芯片,以1200V芯片為例,其綜合性能較上一代產品有顯著提升,見表1。
?
本文介紹了該項目的研發過程:包含系統性能評估(top-down flow),用于選擇芯片并聯數量;碳化硅模塊的本體設計,包括封裝形式、電磁、熱、結構、可制造性等;模塊性能測試,對標某知名IGBT功率模塊;根據模塊的標定結果迭代系統性能評估,包括最大輸出功率、高效區并輔以臺架實測結果,并展開其對續航里程影響的分析。基于以上結果,本文最后將總結一下關于碳化硅模塊應用于主驅設計的方法論。
?
系統分析
根據羅姆提供的第四代SiC芯片規格書,作者將其相關參數導入至臻驅的系統分析工具——ScanTool中。ScanTool是一種時域-頻域混合的穩態仿真工具,主要用于電力電子系統的前期方案設計,可用于計算系統在不同軟硬件配置下的功率、效率、輸出波形失真、母線電容的電壓紋波及電流應力等。ScanTool的計算原理是將時域激勵波形轉成頻域的頻譜,同時將負載用頻域矩陣的形式表述,兩者相乘從而獲得頻域的響應,再對該頻域響應逆變換成時域波形。通過此種方式,該工具的輸出波形具有極高的穩態精度,同時又避免了一般的時域仿真工具從初始狀態到最終穩態的等待時間,使其仿真時間可以從每個仿真數十分鐘縮減至1-2秒。因此ScanTool特別適合動輒需要仿真成百上千種軟硬件設計組合的高自由度的電力電子系統的前期設計。一個圖像化的原理介紹見圖1。
一般而言,當人們設計一款基于IGBT芯片的功率模塊時,芯片的種類及并聯數量的選擇依據大多為芯片的結溫(或者說是最大結溫時能輸出的峰值功率)。此項目采用碳化硅芯片,單個面積小、適合多芯片并聯,但其價格較IGBT高出不少。另一方面,碳化硅屬于單極性器件,因此碳化硅芯片的并聯數量越多,其總導通損耗越低,并可因此提高電控的效率。所以,選擇芯片并聯數量時,除了最高結溫限制了最大輸出功率,還必須考慮它對于系統層面的優勢——如之前所提到過的,即必須考慮綜合的效率提升,尤其是如在NEDC、WLTC、CLTC等循環路況下的續航里程的提升,并結合財務回報模型進行綜合分析。一種簡化的財務模型可以包含使用碳化硅的模塊(較IGBT模塊)導致的成本差異、電池安裝成本減少,以及后續的充電使用成本減少。前兩者為初始投資支出(CAPEX),后者為運營支出(OPEX),最終可以折算出獲得財務回報的時間點。根據車型與用戶使用頻次,該盈虧平衡點可以在1-4年之間。由于該系統層面測算模型涉及到很多變量的假設,本文不再贅述。
?
經過一系列的系統分析,我們驗證了芯片并聯數量過多,不會對續航里程進一步提升有過多幫助,而只能提升該車的最大加速度;芯片數量過少,貌似模塊成本降低,但也可能失去效率/經濟優勢——尤其是考慮碳化硅芯片的正溫度系數后。
?
基于此結果,作者對選擇的芯片數量依據財務模型進行了優化,既能避免無謂的多安裝的芯片而導致的成本增加,也避免了芯片并聯數量過少而導致的經濟優勢不再。同時,臻驅碳化硅模塊也引入了平臺化設計的理念,即當客戶對于整車加速性有更高要求的時候(例如對于部分高端車型),模塊內部可以根據客戶需求而并聯更多的芯片,從而提高最大瞬時輸出功率,給整車用戶提供更大的推背體驗。
?
模塊本體設計
當芯片選型與并聯數量確定后,我們進入功率半導體模塊的本體設計階段,它一般包含電磁、熱、結構與可制造性等內容。需要注意的是,碳化硅的開關速度比硅基的IGBT高很多,所以,一些在IGBT模塊中通常并不嚴苛的指標,會在碳化硅模塊的設計中變得十分關鍵。這些指標包括了各并聯碳化硅芯片之間的開關時刻同步性、芯片的瞬態電流電壓應力的均衡性、功率鏈路對于門極的干擾等。其中,前兩個指標體現在模塊外特性上,它們會決定該模塊的極限電壓與電流輸出能力;功率鏈路對門極的干擾,是器件在開通關斷的瞬間,將電磁能量通過空間耦合到控制鏈路上,其造成的后果可能是導致門極瞬態電壓應力過大導致門極老化加快、壽命減少,嚴重的可導致功率的誤觸發,造成模塊及系統的損壞。
?
此外,在臻驅之前的碳化硅功率模塊的設計項目中,發現碳化硅模塊中較為明顯的振蕩現象,它是由功率模塊的漏感與碳化硅芯片的結電容構成的LC諧振,通常其頻率在數十兆赫茲。該振蕩會影響到電控系統的電磁兼容表現,并降低碳化硅模塊的效率優勢,甚至在某些極限工況下,此諧振會進一步惡化,使電壓電流幅值超越器件的安全工作區域(SOA)。為了解決這個問題,臻驅開發了一系列設計輔助工具,并基于此優化了模塊本體設計,最終將該問題基本解決。圖2是兩個輸出波形的對比。可以看出,在相同的工況下,優化后的模塊設計不再有明顯的振蕩現象。
最終,臻驅設計的碳化硅功率模塊經過多次迭代,將模塊內部多芯片之間的瞬態應力不平衡度降低到了10%以下。根據團隊內部進行的競品對標評估,認為僅此性能就已經做到了業內的頂尖水平。同時,功率鏈路對于門極的電壓毛刺干擾也大大減小;模塊開關時刻的高頻振蕩問題也得到了較好的解決。
?
碳化硅模塊性能對標測試
功率模塊的測試包含性能與可靠性測試,而性能測試可以分為用于導通損耗評估的靜態測試與用于開關損耗評估的動態測試。后者通常的實現方法是一種稱為“雙脈沖測試”的方法,它需要對于被測器件施加不同的電壓、電流、器件溫度,甚至不同的門極驅動電阻,以進行全面測試評估。一個完整的測試DoE表格(Design?of?Experiment)可包含數千個工作點。考慮到接著還需要進行大量的測試數據的后處理工作,功率器件的動態測試顯然是一個費時費力的任務。因此,很多情況下,用戶不得不選擇降低測試點密度,即刪減DoE表格的長度來縮短測試時間。
?
臻驅科技開發出了一套高精度、高測試速度的功率模塊動態測試標定平臺,它基本可以做到“一鍵”完成數千個工作點的全自動測試,并自動化后做數據的后處理,并半自動地生成標準化的模塊測試報告。使用者所需要做的,只是對測試前期硬件進行配置、生成科學的DoE表格,以及對最終的測試報告添加主觀評估的內容。對一個有3000多個測試點的模塊標定任務,相較于一般的手動/半手動測試系統,該自動化標定平臺可以將工作從2個月壓縮到2天,且包含了數據后處理及報告生成。圖3介紹了該測試平臺的核心功能。
?
本項目中,動態性能的參考對象為一知名的IGBT功率模塊。測試結果顯示,臻驅開發的碳化硅功率模塊在動態性能上全面超越了參考的IGBT功率模塊,這包括了開通損耗、關斷損耗及體二極管的反向恢復損耗。同時,碳化硅模塊在極端溫度下也沒有出現明顯的振蕩。
?
碳化硅電控的效率對標測試
接著,基于碳化硅功率模塊及其配套的門極驅動被裝入了電機控制器,并匹配一永磁電機進行效率圖的標定,其結果用于與基于IGBT功率模塊的電控的對標。電控及驅動電機測試系統見圖4。
IGBT電控與碳化硅電控的實測效率圖與關鍵參數對比分別見圖5與表2??梢钥吹剑捎昧颂蓟韫β誓K的電控無論是在最高效率、最低效率,還是高效區都有了顯著的提升。尤其是在低扭矩的輕載情況下,碳化硅的效率優勢極為明顯。這主要是得益于單極性功率器件在輕載時的導通損耗低,及全區域的開關損耗低的特性。
?
?
碳化硅電控的效率仿真驗證
此外,我們也將雙脈沖測試的數據導入了系統評估工具ScanTool,對效率圖進行了仿真計算。需要指出的是,由于碳化硅器件有較明顯的正溫度系數特性(即損耗隨著溫度升高而增加),ScanTool中設置了溫度迭代功能,即根據前一次仿真結果的器件結溫計算該器件在此結溫下的損耗,再進行結溫復算,直至前后兩次計算結果的溫度偏差小于1度??梢韵胂蟮氖?,當芯片并聯數量過少的時候,由于結溫升高會引起器件的損耗增加;反之,芯片并聯數量較多時,單個器件的損耗較低,使其工作結溫也較低,在此較低的結溫下,碳化硅芯片的損耗將進一步減少。可見,具備溫度-損耗的迭代功能的ScanTool是保證建模精度的一個關鍵。
仿真的結果顯示在圖6及表3。對照圖5和表2的實測結果,我們可以看到,分析工具與實測結果是十分吻合的。兩者之間的剩余差異主要體現在低速區,在這個區域內的電控輸出功率很低,因此電控內的殘余損耗顯得明顯,如銅排與母線電容上的損耗等。此外,脈寬調制的方案、測試設備的精度也是可能的原因,但這些較小的差異不影響接下去的系統級續航里程分析。
?
?
碳化硅電控的最大輸出能力分析
?
碳化硅模塊內部的芯片并聯數量越多,其電控的輸出能力越大。在這項分析中,我們假設碳化硅與IGBT允許工作在相同的最高結溫下即150℃。ScanTool的仿真結果顯示,當模塊采用6芯片并聯時,最大輸出功率增加12.4%;當采用8芯片并聯時,功率增加31%。
?
在實驗中,由于動力總成臺架的能力限制,我們使用了電感作為負載來測試最大輸出能力。相較于采用真實電機負載,這個妥協的方案用于評估碳化硅模塊測試是可以接受的,原因是碳化硅芯片雙向導通的特點使得其損耗對于負載的功率因數的大小并不敏感。
圖9展示了碳化硅電控輸出達到了600?Arms,且已達到了測試設備的最大能力。需要指出的是,在電控應用場景中,我們保持了10kHz的開關頻率,而此時碳化硅模塊的開關損耗的百分比仍是較低的(約20%)。因此,通過升級軟件的控制頻率和驅動電路的功率能力,可以顯著提升電控的開關頻率而不導致明顯的功率降額。在高開關頻率下,負載的基波頻率也可以顯著提升,即將電控用于如高速空壓機、航天等應用場景。
?
碳化硅電控帶來的系統優勢評估
此處的系統評估指的主要是整車層面的續航里程。為此,臻驅科技已開發了一套整車基于指定路譜的計算工具:使用者選定一款車型,并指定路況模板后,該工具將輸出對應于動力總成(電機+電控)的扭矩與轉速指令,并根據ScanTool計算或實際標定得出的碳化硅電控及電機的效率圖,計算出整車的續航里程。
此處我們選擇了一款低風阻的轎車車型,并匹配如圖5所示的IGBT/SiC電控及其對應驅動電機實測效率,置于CLTC-P(China?Light-duty?Vehicle Test Cycle – passenger car, 中國輕型汽車行駛工況-乘用車)路譜下進行仿真分析,整車系統能耗對比見圖11。較原來搭載的IGBT電控方案,搭載了臻驅碳化硅電控的整車能耗降低4.4%,即搭載相同電池容量情況下,續航里程可增加4.4%!這個令人振奮的結果,證明了碳化硅技術在新能源車主驅應用中的顯著優勢。用戶可根據此結果,進一步進行整車經濟性方面的分析。
?
項目總結
本文介紹了臻驅科技對于碳化硅功率模塊及電控的開發、測試及系統評估。實測結果證明,該碳化硅功率模塊工作穩定,并相較于IGBT模塊在損耗方面有明顯降低;所對應的碳化硅電控,相較于IGBT電控,無論在最大輸出功率還是續航里程上都有顯著的優勢。此項目也側面證明了,碳化硅技術應用于新能源車的主驅是大勢所趨。
?
?
本文所開發的碳化硅功率模塊與某主流IGBT功率模塊在功率端子部分兼容,而門極位置經過了優化改動,其目的是優化模塊內部的電氣性能。本文所開發的碳化硅電控與IGBT電控的功能完全兼容而性能優勢明顯,并可在臻驅科技現有的電控自動化產線上實現批量生產。
?
臻驅科技自主研發了一套自動化產線(見圖12),其規劃產能為每年15萬臺,組裝線自動化率約85%,測試線自動化率為100%。工廠通過了TUEV(德國技術監督協會的)的IATF16949質量體系認證。
?
臨近尾聲,作者對碳化硅電控的心得討論如下:
總體而言,碳化硅電控適用于續航里程長、風阻小的高端車型,并對整車使用頻次較高的用戶有更高經濟價值。
?
更多信息:https://www.rohm.com.cn/products/sic-power-devices
?
?
Introduction
碳化硅功率半導體近年來在能源轉換應用中正在成為一個熱門的話題:由于材料屬性,使得它具有比硅基半導體器件更高的最大結溫、更小的損耗,以及更小的材料熱阻系數等。
?
因此,很多人宣稱,當碳化硅功率器件應用于能源轉換后,變頻器系統將有更高的功率密度、更小的體積、更高的允許工作溫度,以及更低的損耗,從而給應用系統帶來更大優勢。
?
臻驅科技計劃將碳化硅芯片封裝至功率模塊,并應用于新能源車的電機驅動器中(以下簡稱“電控”),用于取代其現有的硅基IGBT功率模塊(峰值功率約為150?kW)。
?
進行開發之前,應用者需要進行評估,哪些碳化硅的特性能給主驅應用帶來最大的價值。例如,對于此類DC-AC的拓撲結構,碳化硅技術的導入對于電控體積的減小并沒有顯著的作用,因為電控的體積主要取決于其各子部件的封裝技術而功率模塊只占其中很小的百分比;另一些人宣稱可以利用碳化硅更高工作結溫的優勢,少安裝芯片數量并使其工作在高溫,從而降低成本。也許,此特性適用于如地下鉆探等環境溫度很高的應用,但對于新能源車而言,是否有必要將結溫推高而犧牲效率(注:碳化硅在高溫下的損耗會顯著增加),以及是否因為節省了芯片數量就能節省系統成本,是需要被質疑的。
?

在臻驅看來,碳化硅技術應用于主驅電控的主要系統優勢,是在于效率的提升,以及峰值輸出功率的增加。前者可以提升續航里程或減少電池安裝數量,后者可以給整車帶來更大的百公里加速度。臻驅第一款開發的是750V的碳化硅模塊,針對A級及以上的乘用車型;第二款是1200V碳化硅模塊,應用于800V系統的乘用車或商用車。在臻驅開發的碳化硅模塊中,臻驅采用的是羅姆最新的第四代750V及1200V芯片,以1200V芯片為例,其綜合性能較上一代產品有顯著提升,見表1。
?
本文介紹了該項目的研發過程:包含系統性能評估(top-down flow),用于選擇芯片并聯數量;碳化硅模塊的本體設計,包括封裝形式、電磁、熱、結構、可制造性等;模塊性能測試,對標某知名IGBT功率模塊;根據模塊的標定結果迭代系統性能評估,包括最大輸出功率、高效區并輔以臺架實測結果,并展開其對續航里程影響的分析。基于以上結果,本文最后將總結一下關于碳化硅模塊應用于主驅設計的方法論。
?
系統分析
根據羅姆提供的第四代SiC芯片規格書,作者將其相關參數導入至臻驅的系統分析工具——ScanTool中。ScanTool是一種時域-頻域混合的穩態仿真工具,主要用于電力電子系統的前期方案設計,可用于計算系統在不同軟硬件配置下的功率、效率、輸出波形失真、母線電容的電壓紋波及電流應力等。ScanTool的計算原理是將時域激勵波形轉成頻域的頻譜,同時將負載用頻域矩陣的形式表述,兩者相乘從而獲得頻域的響應,再對該頻域響應逆變換成時域波形。通過此種方式,該工具的輸出波形具有極高的穩態精度,同時又避免了一般的時域仿真工具從初始狀態到最終穩態的等待時間,使其仿真時間可以從每個仿真數十分鐘縮減至1-2秒。因此ScanTool特別適合動輒需要仿真成百上千種軟硬件設計組合的高自由度的電力電子系統的前期設計。一個圖像化的原理介紹見圖1。
?
經過一系列的系統分析,我們驗證了芯片并聯數量過多,不會對續航里程進一步提升有過多幫助,而只能提升該車的最大加速度;芯片數量過少,貌似模塊成本降低,但也可能失去效率/經濟優勢——尤其是考慮碳化硅芯片的正溫度系數后。
?
基于此結果,作者對選擇的芯片數量依據財務模型進行了優化,既能避免無謂的多安裝的芯片而導致的成本增加,也避免了芯片并聯數量過少而導致的經濟優勢不再。同時,臻驅碳化硅模塊也引入了平臺化設計的理念,即當客戶對于整車加速性有更高要求的時候(例如對于部分高端車型),模塊內部可以根據客戶需求而并聯更多的芯片,從而提高最大瞬時輸出功率,給整車用戶提供更大的推背體驗。
?
模塊本體設計
當芯片選型與并聯數量確定后,我們進入功率半導體模塊的本體設計階段,它一般包含電磁、熱、結構與可制造性等內容。需要注意的是,碳化硅的開關速度比硅基的IGBT高很多,所以,一些在IGBT模塊中通常并不嚴苛的指標,會在碳化硅模塊的設計中變得十分關鍵。這些指標包括了各并聯碳化硅芯片之間的開關時刻同步性、芯片的瞬態電流電壓應力的均衡性、功率鏈路對于門極的干擾等。其中,前兩個指標體現在模塊外特性上,它們會決定該模塊的極限電壓與電流輸出能力;功率鏈路對門極的干擾,是器件在開通關斷的瞬間,將電磁能量通過空間耦合到控制鏈路上,其造成的后果可能是導致門極瞬態電壓應力過大導致門極老化加快、壽命減少,嚴重的可導致功率的誤觸發,造成模塊及系統的損壞。
?
此外,在臻驅之前的碳化硅功率模塊的設計項目中,發現碳化硅模塊中較為明顯的振蕩現象,它是由功率模塊的漏感與碳化硅芯片的結電容構成的LC諧振,通常其頻率在數十兆赫茲。該振蕩會影響到電控系統的電磁兼容表現,并降低碳化硅模塊的效率優勢,甚至在某些極限工況下,此諧振會進一步惡化,使電壓電流幅值超越器件的安全工作區域(SOA)。為了解決這個問題,臻驅開發了一系列設計輔助工具,并基于此優化了模塊本體設計,最終將該問題基本解決。圖2是兩個輸出波形的對比。可以看出,在相同的工況下,優化后的模塊設計不再有明顯的振蕩現象。
?
碳化硅模塊性能對標測試
功率模塊的測試包含性能與可靠性測試,而性能測試可以分為用于導通損耗評估的靜態測試與用于開關損耗評估的動態測試。后者通常的實現方法是一種稱為“雙脈沖測試”的方法,它需要對于被測器件施加不同的電壓、電流、器件溫度,甚至不同的門極驅動電阻,以進行全面測試評估。一個完整的測試DoE表格(Design?of?Experiment)可包含數千個工作點。考慮到接著還需要進行大量的測試數據的后處理工作,功率器件的動態測試顯然是一個費時費力的任務。因此,很多情況下,用戶不得不選擇降低測試點密度,即刪減DoE表格的長度來縮短測試時間。
?
臻驅科技開發出了一套高精度、高測試速度的功率模塊動態測試標定平臺,它基本可以做到“一鍵”完成數千個工作點的全自動測試,并自動化后做數據的后處理,并半自動地生成標準化的模塊測試報告。使用者所需要做的,只是對測試前期硬件進行配置、生成科學的DoE表格,以及對最終的測試報告添加主觀評估的內容。對一個有3000多個測試點的模塊標定任務,相較于一般的手動/半手動測試系統,該自動化標定平臺可以將工作從2個月壓縮到2天,且包含了數據后處理及報告生成。圖3介紹了該測試平臺的核心功能。
本項目中,動態性能的參考對象為一知名的IGBT功率模塊。測試結果顯示,臻驅開發的碳化硅功率模塊在動態性能上全面超越了參考的IGBT功率模塊,這包括了開通損耗、關斷損耗及體二極管的反向恢復損耗。同時,碳化硅模塊在極端溫度下也沒有出現明顯的振蕩。
?
碳化硅電控的效率對標測試
接著,基于碳化硅功率模塊及其配套的門極驅動被裝入了電機控制器,并匹配一永磁電機進行效率圖的標定,其結果用于與基于IGBT功率模塊的電控的對標。電控及驅動電機測試系統見圖4。
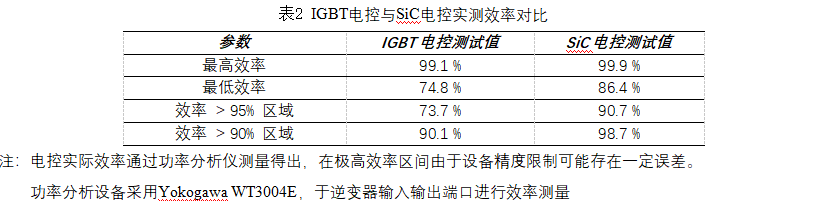
?
碳化硅電控的效率仿真驗證
此外,我們也將雙脈沖測試的數據導入了系統評估工具ScanTool,對效率圖進行了仿真計算。需要指出的是,由于碳化硅器件有較明顯的正溫度系數特性(即損耗隨著溫度升高而增加),ScanTool中設置了溫度迭代功能,即根據前一次仿真結果的器件結溫計算該器件在此結溫下的損耗,再進行結溫復算,直至前后兩次計算結果的溫度偏差小于1度??梢韵胂蟮氖?,當芯片并聯數量過少的時候,由于結溫升高會引起器件的損耗增加;反之,芯片并聯數量較多時,單個器件的損耗較低,使其工作結溫也較低,在此較低的結溫下,碳化硅芯片的損耗將進一步減少。可見,具備溫度-損耗的迭代功能的ScanTool是保證建模精度的一個關鍵。

?
碳化硅電控的最大輸出能力分析
?
碳化硅模塊內部的芯片并聯數量越多,其電控的輸出能力越大。在這項分析中,我們假設碳化硅與IGBT允許工作在相同的最高結溫下即150℃。ScanTool的仿真結果顯示,當模塊采用6芯片并聯時,最大輸出功率增加12.4%;當采用8芯片并聯時,功率增加31%。
?
在實驗中,由于動力總成臺架的能力限制,我們使用了電感作為負載來測試最大輸出能力。相較于采用真實電機負載,這個妥協的方案用于評估碳化硅模塊測試是可以接受的,原因是碳化硅芯片雙向導通的特點使得其損耗對于負載的功率因數的大小并不敏感。
圖9展示了碳化硅電控輸出達到了600?Arms,且已達到了測試設備的最大能力。需要指出的是,在電控應用場景中,我們保持了10kHz的開關頻率,而此時碳化硅模塊的開關損耗的百分比仍是較低的(約20%)。因此,通過升級軟件的控制頻率和驅動電路的功率能力,可以顯著提升電控的開關頻率而不導致明顯的功率降額。在高開關頻率下,負載的基波頻率也可以顯著提升,即將電控用于如高速空壓機、航天等應用場景。
?
碳化硅電控帶來的系統優勢評估
此處的系統評估指的主要是整車層面的續航里程。為此,臻驅科技已開發了一套整車基于指定路譜的計算工具:使用者選定一款車型,并指定路況模板后,該工具將輸出對應于動力總成(電機+電控)的扭矩與轉速指令,并根據ScanTool計算或實際標定得出的碳化硅電控及電機的效率圖,計算出整車的續航里程。
此處我們選擇了一款低風阻的轎車車型,并匹配如圖5所示的IGBT/SiC電控及其對應驅動電機實測效率,置于CLTC-P(China?Light-duty?Vehicle Test Cycle – passenger car, 中國輕型汽車行駛工況-乘用車)路譜下進行仿真分析,整車系統能耗對比見圖11。較原來搭載的IGBT電控方案,搭載了臻驅碳化硅電控的整車能耗降低4.4%,即搭載相同電池容量情況下,續航里程可增加4.4%!這個令人振奮的結果,證明了碳化硅技術在新能源車主驅應用中的顯著優勢。用戶可根據此結果,進一步進行整車經濟性方面的分析。
?
項目總結
本文介紹了臻驅科技對于碳化硅功率模塊及電控的開發、測試及系統評估。實測結果證明,該碳化硅功率模塊工作穩定,并相較于IGBT模塊在損耗方面有明顯降低;所對應的碳化硅電控,相較于IGBT電控,無論在最大輸出功率還是續航里程上都有顯著的優勢。此項目也側面證明了,碳化硅技術應用于新能源車的主驅是大勢所趨。
?
?
本文所開發的碳化硅功率模塊與某主流IGBT功率模塊在功率端子部分兼容,而門極位置經過了優化改動,其目的是優化模塊內部的電氣性能。本文所開發的碳化硅電控與IGBT電控的功能完全兼容而性能優勢明顯,并可在臻驅科技現有的電控自動化產線上實現批量生產。
?
臻驅科技自主研發了一套自動化產線(見圖12),其規劃產能為每年15萬臺,組裝線自動化率約85%,測試線自動化率為100%。工廠通過了TUEV(德國技術監督協會的)的IATF16949質量體系認證。
?
臨近尾聲,作者對碳化硅電控的心得討論如下:
- 碳化硅用于電控的主要優勢在于效率,而更高效率帶來的經濟優勢在于電池安裝成本及充電成本的降低;
- 碳化硅模塊設計時,其芯片并聯數量需要一定過設計以實現最佳經濟性;更多的芯片并聯會降低經濟性,但可幫助整車實現更大的加速度;
- 碳化硅模塊本體設計難點在于電磁部分,需要開發出精確的建模和設計輔助工具;
- 碳化硅技術用于小風阻車型時續航里程可增加4%以上。
總體而言,碳化硅電控適用于續航里程長、風阻小的高端車型,并對整車使用頻次較高的用戶有更高經濟價值。
?
更多信息:https://www.rohm.com.cn/products/sic-power-devices
?
評論