在各大行業陸續復工復產的當下,在上海,不少制造企業通過打造智能工廠、數字化車間,有效提高了生產效率,率先“破疫”。
不擔心“因人斷產”
位于浦東川沙的開能健康科技集團股份有限公司生產車間,現場作業的工人并不多。這是一家生產凈水機的企業,產品遠銷全球90多個國家。“這幾天,國內外訂單不斷,已經排到4月份了。”開能健康副董事長瞿亞明說。
其實,現在企業還有30%的員工因疫情未返崗,逆勢接單的底氣源自“智能工廠”。兩座立體智能倉庫與生產車間直接連通,當ERP系統將訂單信息發至生產車間,MES數字化制造系統即刻啟動,倉庫內的生產物料通過智能導軌被精準轉運至生產車間的全自動生產線。24小時值守的機器人按照工程師設定的程序,完成玻璃鋼桶、控制閥體等的生產和裝配。記者看到,當產品完成生產并組裝后,又會被自動轉運至倉庫的成品區。
一眼望去,全自動生產線上空無一人。
“僅僅控制閥就由100多個零部件組成,以往全靠手工裝配,對裝配工人要求極高。”瞿亞明說。過去,一旦某一環節人員缺位,將影響整個產線運轉。現在,關鍵零部件實現自動化生產,讓企業面對疫情時,再不用擔心“因人斷產”。以往一條產線需要至少15個人全員到位,現在只要操機工程師在崗,機器就能運轉起來。
由于引入生產智能系統,開能的每個單品都有了數據支撐,可以實現全生命周期的質量追溯,產品不良率降低50%,整體運營成本降低30%以上。
交付訂單持續增加
位于閔行區的上海發電機廠,借助數字化工廠建設打下的基礎,成功實現防疫、復工兩不誤。就拿此次復工首日來說,工廠技術部260名員工實際到崗人數不足三成。技術部負責人告訴記者,在復工前就制訂預案,讓居家辦公的員工借助于協同設計平臺、產品生命周期管理系統、檔案系統等數字化技術平臺,足不出戶完成數據查詢、三維設計、二維出圖、設計變更等工作,與在廠內或外地的同事協同辦公。數字化工廠讓復工實現“全員上崗”,保證了技術工作進度不受影響。
以發電機鐵芯壓裝為例,以往6個人圍成一圈的手工作業,如今兩套鐵芯自動壓裝機器人系統同時工作,兩名操作者只需通過按鍵啟動設備進行疊裝,期間做一些暫停檢視工作。
傳統離散制造的特點是手加工、機加工并存,人是保證生產進行的決定性要素。基于汽輪發電機制造行業的特殊性,停工會給企業和上下游經濟造成巨大損失。得益于上發廠近兩年添置的機器人自動疊裝系統、線圈端部自動成型機等一大批智能設備,員工群體作業的現狀得到改觀。目前正處于疫情防控的關鍵期,但上發廠交付訂單持續增加,正是得益于智能制造。
近期新上榜“燈塔工廠”的寶鋼股份上海寶山基地,也在應對疫情中展現獨特優勢:依托自身數字化積淀,利用基于大數據和人工智能的遠程運維技術,寶鋼將寶山基地的冷軋熱鍍鋅智能車間變成了一座24小時運轉,卻不需多人值守的“黑燈工廠”,實現疫情防控和穩定生產的有效平衡。
智能制造是自救良藥
疫情是行業之危,數字化轉型是企業之機。在市經信委智能制造推進處處長韓大東看來,全球制造業的發展不會因為任何區域性的停工而停滯不前。面對這樣的情況,加快數字化轉型,實現智能制造才是企業自救的良藥。
作為最早探索智能制造的地區,上海的智能制造已形成價值鏈相對高端、產業鏈較為完整、創新鏈協同較強、“資源鏈”相對集聚的綜合優勢。智能制造應用方面,已初步建成14個國家級智能工廠、80個市級智能工廠;系統集成方面,集聚了一大批智能制造系統集成企業,2019年全市智能制造及機器人系統集成突破400億元,規模和能級位居國內第一梯隊。
根據計劃,到2021年,上海將培育10家10億元規模、1至2家100億元規模的智能制造系統解決方案供應商,打造10家智能制造標桿工廠、100家示范性智能工廠,推動1000家規模以上制造業企業實施智能化轉型。
-
數字化
+關注
關注
8文章
8775瀏覽量
61888 -
智能制造
+關注
關注
48文章
5574瀏覽量
76391 -
智能工廠
+關注
關注
3文章
1003瀏覽量
42443
發布評論請先 登錄
相關推薦
如何快速實現工廠向數字化轉型
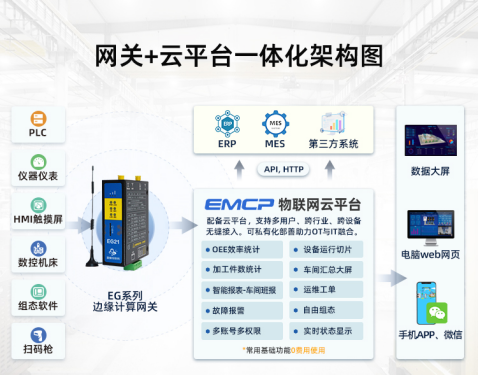
比亞迪榮登2024凱度BrandZ中國全球化品牌50強榜單 獲谷歌“披荊斬棘全球化品牌”獎
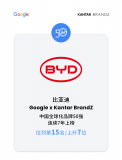
評論