4月2日,據外媒報道,作為“CustoMat_3D”研究項目的一部分,EDAG集團與八家合作伙伴聯手開發出一種可應用于汽車的鋁合金。這種合金的強度更高,而且斷裂伸長率更大。后者非常重要,特別是在發生碰撞的情況下。
新研究強調,目前,AM型鋁合金不能滿足汽車行業的高要求,如碰撞試驗性能。并且,EDAG認為,現下的工藝設計只考慮到高強度非延展性材料參數。
過去三年,EDAG著眼于整個過程鏈,包括粉末制造、仿真和部件開發。萊布尼茨材料工程研究所(Leibniz Institute for Materials Engineering)和全球特種材料公司Kymera International,負責合金定義和粉末制造。弗勞恩霍夫應用高分子研究所(Fraunhofer IAPT)、GE Additive和FKM Sintertechnik GmbH,負責粉末基激光束焊接(LBM)的加工和工藝開發。Fraunhofer ITWM和MAGMA Giessereitechnologie GmbH,對焊接材料的快速冷卻過程進行了模擬研究。梅賽德斯-奔馳和EDAG Engineering GmbH公司負責性能演示,并得到工程軟件供應商 Altair Engineering公司的支持。通過綜合方法,實現增材量產。這種合金可用于制造重量顯著減輕的汽車零部件。
在實驗室階段,研究人員起初對各類合金進行了測試。通過不同的激光束焊接系統,有可能成功找到最有前途的合金。這種合金的特別之處在于其功能多樣性:通過一種合金提供多種性能。利用下游加熱處理方式,可以靈活實現這些性能。根據傳遞的材料值,生成材料卡片,并使用Altair Opti OptiStruct軟件進行結構優化,以減少等功率部件的重量。其中特殊之處在于,可以考慮對增材生產工藝和組件對齊的要求。
選擇汽車不同部位的零件,不論是動態承重車輪載體,還是傳動箱區域對剛度要求較高的復雜構件,都有可能實現有效減重。有些可減重超過預期值30%。基于增材生產工藝,該零件可通過負載級模型,適應相關車輛的要求。
此外,研究人員利用最新開發的材料,對激光沉積焊接和粘接技術等混合工藝,進行了研究。在模擬過程中,通過宏觀模擬零件中的代表性元素,引導粉末的微觀過程。利用這種方式,可以顯著縮短計算時間。因此,能使殘余應力和延遲在生產前可視并最小化。
新開發的CustAlloy?品牌合金,將在幾個月后正式上市。由于應用廣泛,而且受益于防腐處理和粘接技術,這種合金符合汽車工業的許多其他要求,可以進行大規模生產。新合金的生產過程和模擬測試方法,為專家提供了有利工具,幫助減少汽車重量,并且在大規模生產過程中使用3D打印技術。
3D打印站在“上風口”的典型應用
3D打印的冷卻劑分配器的任務是有效地消散快速充電過程和負載循環期間產生的熱量。根據產生的熱量,各個電池模塊由集成的閥門控制器通過各種冷卻回路主動控制,并根據需要進行冷卻。借助西門子的Siemens CFD拓撲優化軟件,與傳統設計方法相比,冷卻劑分配器將壓力損失減少了22%。
3D打印冷卻劑分配器
由于產品性能獲得的明顯提升,這款冷卻劑分配器如同GE所規模生產的噴油嘴一樣,面臨著產業化生產的需求。將惠普的工業級HP Jet Fusion 5200 3D打印設備集成到西門子的數字企業解決方案中,可以比以前更快,更經濟,更可持續地生產這種冷卻劑分配器。而基于高達30萬件的規模化生產概念證明了在批量生產中通過3D打印制造零部件的經濟可行性。
很多時候,企業無法實現從1到n的產業化發展,是因為陷入了下風口的僵局。而想要從“下風口”轉移到“上風口”是充滿挑戰的,僅僅從對公司實力的要求上看,這兩個風口對公司實力和人才水平的要求差距很大。
就專注于研發設備與材料的3D打印領域廠家來說,很難依靠自身的實力引領其用戶從“下風口”轉移到“上風口”。而依靠用戶自身對3D打印的了解,更難下定轉型的決心,這其中除了像GE, 西門子這樣產業鏈健全的應用型企業可以主動實現制造轉型之外,在還會觸及到動一發而牽全身的供應鏈的重新改造,技術的挑戰、原有固定資產的投入或歸零、人才的重新培訓需求,各種“大山”使得當前的3D打印應用從下風口轉移到上風口的路途舉步維艱。
在這方面,EDAG做了很好的示范,EDAG是一家在汽車制造商背后的全力以赴、專門致力于開發3D打印汽車技術的工程公司。EDAG不僅探索如何創建通過傳統制造工藝難以實現的零件設計實現從0到1的創新開發工作,還積極的探索從1到n的產業化發展路徑。就在2019年漢諾威工業博覽會期間,西門子與EDAG還宣布了加強合作的計劃。一個典型的產品是“Next Gen Space frame 2.0”智能模塊化系統。這是EDAG和西門子以及Constellium,Fraunhofer IAPT,Concept Laser和BLM共同完成的輕質鋁合金結構。
“Next Generation Space Frame 2.0”智能模塊化系統結合了仿生力學設計和增材制造節點以及高強度,吸收能量的鋁合金擠壓型材。該概念提供極其靈活的制造解決方案,使其能夠支持越來越多的交通產品,同時仍考慮經濟因素。
EDAG工程公司在生產過程領域提供的專業知識為合作做出了重大貢獻。已經創建了量身定制的未來工廠概念,使得為增材制造開發的組件也能夠以更大批量生產并轉移到實際的批量生產中。
另一個經典的案例是EDAG工程發起的一個3D打印輕量化汽車引擎蓋鉸鏈的設計與制造項目-LightHinge+ 。在這個輕量化鉸鏈的設計與制造過程中,EDAG 公司與其合作伙伴一起,通過拓撲優化設計、仿真分析、3D打印技術設計與制造了一個3D打印汽車引擎蓋鉸鏈,鉸鏈在實現輕量化的同時,兼顧到了汽車制造業對安全穩定性的需求。通過仿真分析,項目組對該鉸鏈的3D打印預期進行了有效控制。
汽車輕量化是實現汽車節能減排的重要途徑,已成為汽車發展的潮流。3D打印技術在制造復雜輕量化結構零件方面,給予了設計師更廣闊的設計空間。而EDAG正與其合作伙伴一起在引領3D打印應用于汽車輕量化的新技術潮流。
責任編輯:gt
-
汽車電子
+關注
關注
3027文章
7990瀏覽量
167420 -
分配器
+關注
關注
0文章
194瀏覽量
25785 -
3D打印
+關注
關注
26文章
3556瀏覽量
109299
發布評論請先 登錄
相關推薦
有源晶振在3D打印機應用方案
3D打印技術應用的未來
物聯網行業中的模具定制方案_3D打印技術分享
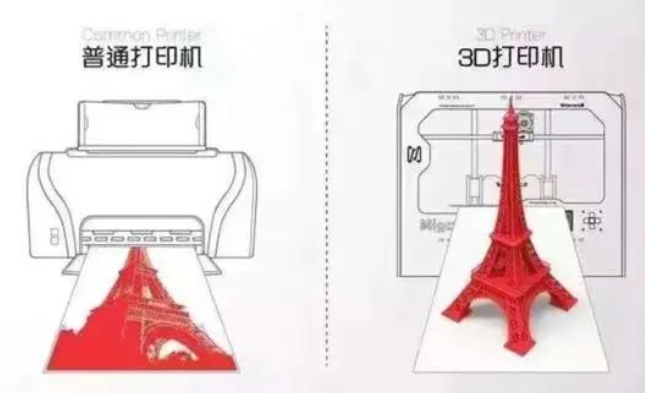
應用在3D打印機的BD系列金屬連接器
維愛普3D打印設備工字電感磁芯:驅動創新與高效的科技核心
3D打印汽車零部件建模設計3D打印服務
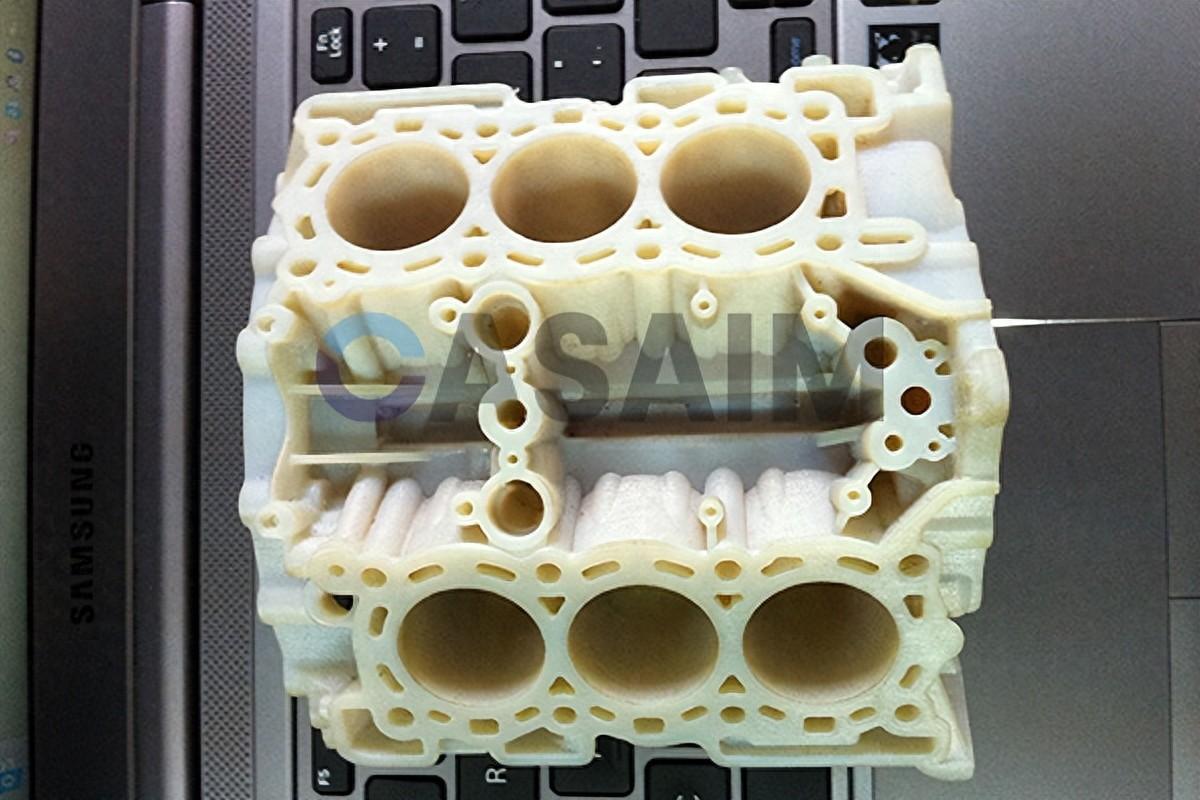
評論