內窺鏡屬于微創醫療器械,就像醫生的“眼睛”能夠有效地幫助醫生“看清“病灶。微創手術的普及與臨床診斷需求推動內窺鏡進入快速發展時期。據Markets and Markets報告顯示,2019年全球內窺鏡的市場容量約為256億美金,將以6.6%的復合年增長率增長,到2024年將達到352億美金。根據中國醫療器械行業協會數據,2018年,我國內窺鏡市場容量達到278億元,內窺鏡配套器械市場規模更大,達500億元。
內窺鏡是一類精密的光學儀器,不論是硬鏡和軟鏡,它們的生產工藝都需要選擇特有的密封技術來實現,不論是內窺鏡中鏡片之間、鏡片和外管之間、金屬材料之間都需要非常高的固定和密封要求。而隨著小型化內窺鏡的出現,對于內窺鏡廠家制造工藝的考驗是“更上一層樓”。對3D打印技術而言,顯著的優勢是比傳統工藝更易于駕馭產品的復雜性。面對小型化的復雜內窺鏡組件制造需求,3D打印有哪些可能的應用切入點?本期,與網友一起通過國內外科研機構、內窺鏡制造商、3D打印企業所開展的應用探索,來感受其中蘊含的潛能。
成就小而復雜的組件
“最小”內窺鏡
在不引起組織創傷的情況下,小型內窺鏡探頭是對小腔或脆弱器官進行成像時所必需的設備。但當前的制造方法限制了高度小型化的探針成像性能,從而限制了小型內窺鏡探頭的廣泛應用。澳大利亞阿德萊德大學醫學院、光學先進傳感研究所和德國斯圖加特大學應用光學研究所(ITO)和SCoPE研究中心的研究人員,通過雙光子光刻微型3D打印技術開發了一種新型超薄探針裝置,在單模光纖上(比人類發絲還細)直接創建側面自由形微光學器件。研究人員稱,這是迄今報道的最小自由形式三維成像探頭,帶有保護性塑料外殼的整個內窺鏡直徑為0.457毫米。
當前的探針制造技術在制造高度小型化探針時存在球面像差、低分辨率或淺焦深的問題。在光學設計中,需要權衡高分辨率(大數值孔徑,NA),從而導致光束發散迅速,聚焦深度較小,而分辨率差(NA較小),無法實現較大的聚焦深度 。在光學相干斷層掃描成像中,因為內窺鏡和血管內探針部署在透明的導管鞘內,既保護動物或患者在探針旋轉進行掃描時免受創傷,又防止在多個動物之間重復使用時的交叉污染。
在光學上,這種透明鞘相當于負柱面透鏡,并引起散光。散光增加了小型化探針的橫向分辨率的衰減。因此,對這些非色差的校正對于用微型探頭在所希望的聚焦深度上獲得盡可能好的分辨率是至關重要的,而當前的微光學制造方法缺乏減輕這些非色差的能力。研究人員開發了一種超薄單片光學相干斷層掃描內窺鏡,通過使用雙光子聚合3D打印技術將125微米直徑的微光學器件直接印刷到光纖上,克服了這些限制。
在研發過程中,研究人員將一根450微米長度的無芯光纖拼接到一根20厘米長的單模光纖上,在光束到達3D打印自由曲面微光學器件之前對其進行擴展。為了實現這一段無芯光纖的拼接,他們首先將一段較長的無芯光纖拼接到單模光纖上,然后使用自動玻璃處理器和直列式切割刀將其切割到450±5微米。雙光子光刻3D打印技術起到的作用是,將光束整形微光學器件直接打印到無芯光纖的遠端。
3D打印微光學器件的自由曲面通過全內反射改變光束的方向,并聚焦光束。光纖組件固定在外徑為0.36毫米的薄壁扭矩線圈內,扭矩線圈允許旋轉和線性運動從成像探頭的近端精確地傳遞到遠端,從而實現3D掃描。3D打印的微型成像探頭在導管鞘內自由旋轉,導管鞘保持靜止,并在3D掃描期間保護生物體組織。
促進內窺鏡細微化
深圳開立生物醫療科技股份有限公司自2002年成立以來一直致力于醫療設備的研發和制造,產品涵蓋超聲診斷系統、電子內鏡系統和體外診斷系列三大產品線。開立醫療推出的HD550系列高清內窺鏡產品,產品性能與外資差距逐漸縮小,在醫院端獲得良好反饋。填補了國產高清內窺鏡的空白,有望更進一步加快國產高端內窺鏡產品發展。開立醫療重視技術創新,其中也包括通過3D打印技術進行產品設計創新。
開立醫療研發了一種可在一定程度上減小外形尺寸的內窺鏡頭端部,使內窺鏡頭端部進一步微細化,從而解決內窺鏡頭端部尺寸大的技術問題。內窺鏡頭端部包括頭端座、成像模組和圖像傳感模組。圖像傳感器模組由傳感器芯片組件和電子元器件構成。傳感器芯片組件和所述電子元器件通過立體封裝的方式封裝為一體。這種內窺鏡頭端座上設置有安裝孔,成像模組正式設置在安裝孔內,而圖像傳感模組對應安裝孔連接在頭端座的后端。
在這一內窺鏡頭端部組建的應用中,3D打印技術的作用是對芯片組件進行立體封裝。立體封裝結構具有內部流道介質,用于電信號的傳輸,滿足高密度、高性能、低成本的要求,并克服了現有技術中存在的互連金線長、空間利用率小、工藝要求高或成本高的缺點。在開立醫療開展的工作中,傳感器芯片組件和電子元器件采用了立體封裝,取消了外部連接結構,形成立體式電路連接結構,解決了二維電子元器件需要足夠的面板空間以設置所需電子元器件的問題。并且不需要在傳感器芯片組件外沿周圍設置保護邊沿,從而能夠消除T型結構中電子元器件對空間的占用。
這種立體封裝帶來的優勢是,可相應地減小圖像傳感模組的整體外部尺寸,從而進一步減小內窺鏡頭端部的外形尺寸,使得內窺鏡的微細化成為可能,繼而有效改善受測者的臨床體驗。
復雜微型一體化組件
開立醫療在3D打印領域的一家戰略合作伙伴為摩方材料。在精密醫療內窺鏡制造領域,內窺鏡的結構越來越趨向體積微型化,鏡體的直徑小到1毫米以內,傳統的加工方式很難達到如此高要求。精細復雜的結構設計,導致傳統工藝的高昂的研發和加工成本,生產過程中常面臨諸多棘手難題。而摩方材料的微納3D打印技術能夠實現復雜部件的一體成型生產。
對于壁厚小于0.15毫米的精密內窺鏡端部座,CNC和開模注塑等傳統加工方式成型都比較困難,尤其對于一些深寬比大的薄壁件。內窺鏡端部座中的圓管壁厚是70微米,管徑1mm,高度為4mm,精度要求±10~25微米,CNC和開模注塑,很難加工出這樣逼近極限的結構。摩方微納3打印設備則能夠實現這類微型薄壁組件的整體結構一次成型,無需組裝。
殼體小型化
奧林巴斯是日本乃至世界精密、光學技術的代表企業之一,事業領域包括醫療、生命科技、影像設備等。在 20 世紀 60 年代末,奧林巴斯就已經預見了內鏡在外科手術中的應用。1979年,公司收購了德國硬鏡制造商 Winter & Ibe GmbH,將醫學領域的業務從軟鏡拓展到軟鏡、硬鏡和手術耗材。在中國市場上,軟鏡市場幾乎被奧林巴斯、富士膠片和賓得三家日企巨頭壟斷,其市場份額超過95%,硬鏡市場中奧林巴斯也占據了第一梯隊。
奧林巴斯也開展了內窺鏡領域的3D打印應用研究。在一項研究中,奧林巴斯開發了一種超聲波內窺鏡,并提出了超聲波振子組件的制造方法。
已知超聲波振子的類別有凸起型、線陣型、徑向型等超聲波光束的收發方向不同的多個類型。其中,就凸起型的超聲波振子而言,多個壓電元件沿著曲面排列,它們分別將超聲波光束朝向曲面的徑向射出。而在以往的超聲波內窺鏡中,在將超聲波振子組裝于殼體時,在中繼基板和收容部之間形成了空隙,而空隙的存在難以使殼體小型化。奧林巴斯希望提供能夠使收容超聲波振子的殼體小型化的超聲波內窺鏡。
在這項應用研究中,3D打印技術被用于制造殼體。奧林巴斯開發的超聲波振子組件包括:超聲波振子、線纜、中繼基板以及殼體。殼體的作用是保持超聲波振子。在進行制造時,首先通過具有絕緣性的樹脂及3D打印技術成形殼體的一部分,然后在利用該3D打印技術在超聲波振子、中繼基板、線纜一側進一步成形3D打印殼體。
根據奧林巴斯,這一研發工作起到能夠使收容超聲波振子的殼體小型化的效果。
微細圓管直接打印
上海交通大學開發了一種單光纖內窺鏡掃描探頭,該探頭包括:準直鏡、單纖維光纖、永久磁鐵、微細圓管、驅動線圈和支柱,準直鏡固定在單纖維光纖的一端部。其中微細圓管通過3D打印機直接打印而成,這一3D打印微細圓管表面上有傾斜式凹槽。
這一研究以微機電系統加工技術為基礎,通過3D打印機直接形成帶有傾斜凹槽的微細圓管,這樣就可以利用纏繞方式在微細圓管表面形成具有任意傾角的驅動線圈結構,即可以沿著凹槽的方向直接繞驅動線圈,使得驅動線圈非常穩定的固定在微細圓管的表面上。
Review
通過以上應用研究可以發現,3D打印的應用都離不開“微、小” 這一概念。在內窺鏡體積微型化的發展趨勢下,實現小而復雜的內窺鏡組件中所體現出來的優勢,為3D打印技術帶來了應用空間。
目前3D打印微型內窺鏡組件的應用多處于研發和原型制造階段,內窺鏡屬于一種進入到人體內中使用的三類醫療器械,因此制造內鏡組件所用的3D打印材料、工藝均需跨越滿足三類醫療器械注冊審批需求這道門檻,方能實現產業化應用。業界對于這一過程中所需投入的研發資金和時間仍需要報以足夠的耐心。
責任編輯:tzh
-
電子元器件
+關注
關注
133文章
3354瀏覽量
105863 -
醫療器械
+關注
關注
19文章
830瀏覽量
51515 -
醫療設備
+關注
關注
12文章
956瀏覽量
66908 -
內窺鏡
+關注
關注
1文章
80瀏覽量
17964 -
3D打印
+關注
關注
26文章
3556瀏覽量
109303
發布評論請先 登錄
相關推薦
3D打印技術,推動手板打樣從概念到成品的高效轉化
有源晶振在3D打印機應用方案
DMD芯片在3D打印中的創新應用
3D打印技術應用的未來
新質生產力探索| AICG浪潮下的3D打印與3D掃描技術
尼龍材料3D打印加工服務小批量3D打印模型制作
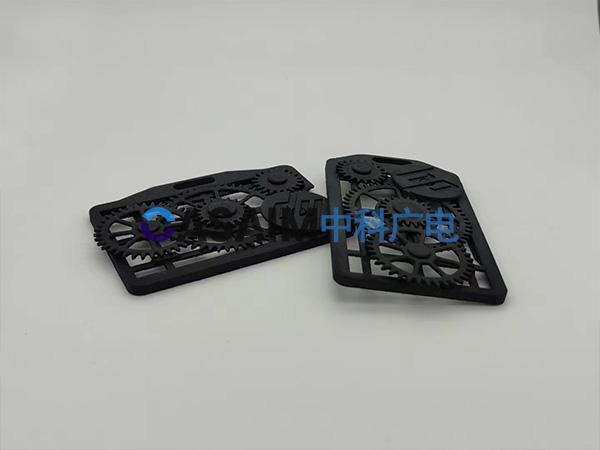
評論