在電源與充電樁等高功率應用中,通常需要專用驅動器來驅動最后一級的功率晶體管。這是因為大多數微控制器輸出并沒有針對功率晶體管的驅動進行優化,如足夠的驅動電流和驅動保護功能等,而且直接用微控制器來驅動,會導致功耗過大等弊端。
首先,在功率晶體管開關過程中,柵極電容充放電會在輸出端產生較高的電壓與電流,高電壓與高電流同時存在時,會造成相當大的開關損耗,降低電源效率。因此,在控制器和晶體管之間引入驅動器,可以有效放大控制器的驅動信號,從而更快地對功率管柵極電容進行充放電,來縮短功率管在柵極的上電時間,降低晶體管損耗,提高開關效率。其次,更大的電流可以提高開關頻率,開關頻率提高以后,可以使用更小的磁性器件,以降低成本,減小產品體積。
為什么要用隔離驅動?
給功率管增加驅動的方式有兩種,一種是非隔離驅動,一種是隔離驅動。傳統電路里面經常見到非隔離驅動,在高壓應用中一般采用半橋非隔離驅動,該驅動有高低兩個通道,低側是一個簡單的緩沖器,通常與控制輸入有相同的接地點;高側則除了緩沖器,還包含高電壓電平轉換器。
非隔離驅動有很多局限性。首先,非隔離驅動模塊整體都在同一硅片上,因此耐壓無法超出硅工藝極限,大多數非隔離驅動器的工作電壓都不超過700伏。其次,當高側功率管關閉而低側功率管打開時,由于寄生電感效應,兩管之間的電壓可能會出現負壓,而非隔離驅動耐負壓能力較弱,所以如果采用非隔離驅動,應特別注意兩管間電路設計。第三,非隔離驅動中需要用到高電壓電平轉換器,高電平轉換到低電平時會帶來噪聲,為了濾除這些噪聲,電平轉換器中通常加入濾波器,這會增加傳播延遲,而低側驅動器就需要額外增加傳輸延遲,以匹配高側驅動器,這就既增加了成本,又使得延遲很長。第四,非隔離驅動與控制芯片共地,不夠靈活,無法滿足現在許多復雜的拓撲電路要求,例如在三相PFC三電平拓撲中,要求多個輸出能夠轉換至控制公共端電平以上或以下,所以這種場景無法使用非隔離驅動。
相比非隔離驅動,隔離驅動就有很多優勢,這里以數字隔離驅動來做說明。在數字隔離驅動器內部,有兩塊或更多的硅片,硅片之間通過絕緣材料隔離,而控制信號通過電容型或電磁型方式穿過隔離層來傳遞,從而讓輸入與輸出處于不同硅片上,這種隔離方式能繞過硅工藝極限,可以滿足高耐壓需求,隔離驅動可以承受10kV以上的浪涌電壓。此外,兩個輸出驅動之間,也有絕緣材料建構的隔離帶,所以與非隔離驅動要求與控制信號共地不同,隔離輸出接地點選擇更靈活,可以匹配不同電路拓撲需要。
數字隔離驅動器的優勢
光耦隔離是傳統的隔離方式,但與數字隔離相比,光耦隔離在性能和面積上都不占優勢。
首先,光耦隔離方案傳輸延遲較大,通常在百納秒以上。在光耦隔離方案中,LED將柵極驅動信號轉換為光信號,再通過光電二極管等光敏電路轉換為待測電信號,根據結構設計的不同,常見的光耦傳播延遲在幾百納秒甚至微秒級。高速光耦通過優化內部寄生參數、增加LED驅動強度等設計,可在幾十納秒時間內接通和斷開,但成本會上升很多。
常規光耦方案的傳播延遲甚至不如非隔離驅動。在半橋非隔離驅動中,因為增加添加了速度較慢的高電壓電平轉換器,以及去毛刺和濾波電路,常見延遲時間可達到100納秒,因為低側要與高側匹配,所以要在低側添加一個單獨的延遲時鐘,整個系統傳播延遲在100納秒左右。
數字隔離驅動通過上百兆高頻載波編解碼,開關只需幾納秒甚至更短的時間。但由于內部邏輯延遲和去毛刺濾波設計,所以延遲到幾十納秒。以納芯微NSi6602為例,隔離驅動傳輸延遲典型值是在25納秒,最高值不超過35納秒。
其次,光耦方案脈寬失真較大。因為光電檢測器中的LED開啟和關閉時間并不總是對稱,且溫度越高不對稱越嚴重,所以光耦脈寬失真比較嚴重,光耦方案脈寬失真范圍從幾十納秒到幾百納秒。
數字隔離驅動的脈寬失真主要由振蕩器計時精度、隔離層傳輸特性和接收端檢測電路造成。NSi6602可將脈寬失真控制在6納秒以內,在脈寬失真這項參數上,數字隔離驅動也是大幅領先。
其他在設計中要注意的參數
除了傳播延遲和脈寬失真。在半橋拓撲中,如果使用單通道隔離驅動器,需要注意上下兩通道的延時匹配,如果采用了不同批次的器件,很容易帶來延時匹配問題,另外,兩個單通道隔離驅動在工作時結溫可能也會有差異,溫度差也會導致信號傳輸延時。對NSi6602這種高集成的雙通道半橋數字隔離驅動而言,就不太需要考慮延時匹配問題,這是因為在封裝時,納芯微都會選擇同一批次而且在晶圓上位置最接近的一對接收器,這樣制造差異影響最小,而一對接收器封裝在同一個芯片中,也能減少溫度差異對延時的影響。NSi6602可將上下通道的延時匹配這個指標控制在5納秒以內。
共模瞬態抗干擾度(CMTI)也是一個需要注意的指標。特別是如果驅動后級接的是碳化硅功率管,這是因為碳化硅功率管寄生電容更小,所以電壓瞬態變化值更大,同樣一個系統,如果從MOS功率管改為碳化硅功率管,其瞬態電壓比時間(dV/dt)的峰值會是MOS管的2到3倍,所以需要更高的CMTI指標。NSi6602的CMTI達到±150kV/μs,驅動碳化硅功率管毫無壓力。
隨著開關電源的小型化和智能化,在5G通信、數據中心、充電樁和車載電源中,工程師越來越多選擇隔離驅動以增強電源性能。
由于歷史原因,通信系統直流供電一般采用-48V輸入,即備電電池的正端接地。在過去,通信設備內部通常采用升降壓式(Buck-Boost)非隔離拓撲來實現輸入負壓到輸出正壓的轉換。但伴隨5G的到來,基站部署數量增加,基站設備小型化要求也越來越高,這就需要在電源部分進一步提高功率密度,采用隔離驅動會帶來很多好處。
非隔離驅動需要與控制芯片共地,所以非隔離驅動中,控制芯片地只能取在-48V,這就使得控制芯片易受到來自-48V電平的浪涌或雷擊等影響。而采用隔離驅動,則可以把控制芯片與驅動接到不同的接地點,控制芯片可以接在PGND(即設備地),所以不易受雷擊與浪涌影響,抗干擾能力強。而且,控制芯片接到設備地也使得其與上位機通信更加方便,不需要再加總線隔離芯片,輸出采樣也不用隔離,電源性能更穩定,采樣保護更及時。
在數據中心交流轉直流(AC-DC)電源中,也可以通過加入NSi6602隔離半橋驅動來改善電源性能,在流行的整流橋加升壓PFC與LLC架構中,還可以通過增加隔離半橋驅動的方式,將有橋PFC改為無橋PFC,從而減少二極管使用數量,并提高電源效率。
在新能源汽車充電樁中的直流轉交流電源通常采用三相交流供電,由于該設備須人員操作,所以在安全標準上要求極高,需要在操作人員可使用的接口與任何高壓電路之間提供增強隔離,以滿足系統對安全的要求,防止瞬時過壓、浪涌過壓和爬電等造成的安全隱患。這時候,隔離驅動就是最好的選擇。
事實上,充電樁直流輸出高達800V,而非隔離驅動最高耐壓只有700V,無法滿足充電樁應用的基本要求。而變壓器隔離驅動效率低、器件多、面積大。以NSi6602為代表的數字隔離驅動則具有高集成特性,成本更低,而且滿足加強絕緣要求,在可承受耐壓條件下,可工作十年以上。
基于隔離半橋驅動的240W高效率同步整流電源方案
如下圖所示,是一款可用于通信系統的48V輸入、12V輸出240W的隔離半橋同步整流電源方案,其開關頻率為200KHz,最高效率可達95%
此電源方案的半橋功率管驅動部分與副邊同步整流功率管驅動部分采用了納芯微高集成度、高可靠性隔離半橋驅動芯片NSi6602,輸出反饋控制部分采用了納芯微高精度隔離誤差放大器NSi3190。此方案支持輸入電壓范圍36V-60V,輸出電壓12V,電流20A,開關頻率200KHz,原副邊的輔助供電電路采用Fly-buck拓撲,本電源具備UVLOOVPOCPOTP等多種保護功能。功能框圖如下:
圖 240W同步整流電源功能框圖
更多關于此方案的詳細資料和數據,請參考納芯微官網。
總結
在5G通信、數據中心、充電樁和車載電源等應用中,無論是與非隔離驅動,還是與光耦隔離驅動相比,數字隔離驅動在傳播時延、可靠性和尺寸等方面都具有明顯的優勢,由于集成度高,成本優勢也很明顯,特別適合當前開關電源設計智能化、小型化的趨勢。
-
驅動器
+關注
關注
52文章
8236瀏覽量
146355 -
整流電源
+關注
關注
0文章
31瀏覽量
9849 -
充電樁
+關注
關注
147文章
2283瀏覽量
85026 -
數字隔離
+關注
關注
20文章
117瀏覽量
79884 -
光耦隔離
+關注
關注
7文章
39瀏覽量
14520 -
隔離驅動
+關注
關注
2文章
93瀏覽量
5691
發布評論請先 登錄
相關推薦
英飛凌推出新型EiceDRIVER? Power全橋變壓器驅動器系列,適用于結構緊湊、經濟高效的柵極驅動器電源
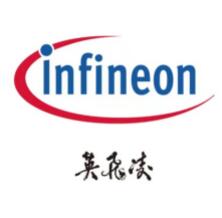
電隔離柵極驅動器選型指南
WBG 器件給柵極驅動器電源帶來的挑戰
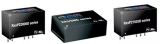
在電機驅動器的UCC23513光兼容隔離式柵極驅動器中實現分立式 DESAT
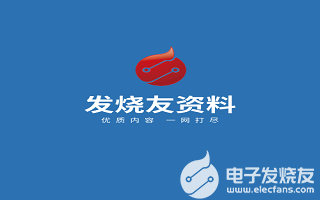
PMP40970.1-多輸出隔離式驅動器偏置電源 PCB layout 設計
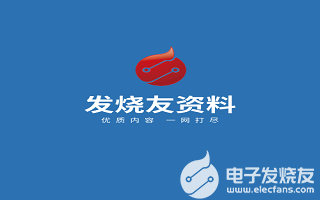
評論