電子發燒友網報道(文/程文智) 在新能源汽車的BOM成本中,電池組的成本是最高的,其次就是電驅動系統的成本了,電驅動系統的成本包括電機與電控,電控部分包含了以功率半導體為主的逆變器成本。
那么作為新能源汽車中第二重要的部件,它的需求是什么,產業現狀如何,關鍵技術有哪些,有什么發展趨勢呢?
我國車用驅動電機技術需求
在不久前的一個汽車論壇上,來自上海電驅動有限公司的車輛事業集團首席技術官張舟云談到了國內驅動電機技術的主要有六大需求。
一是低速時高轉矩、高速時恒功率,具有寬調速范圍。也就是說車輛起步的時候能夠有高轉矩,高速運行時能夠進行恒功率輸出,電機的調速范圍能達到1:3到1:4以上;
二是高效率,即采用稀土永磁和電磁設計優化,使驅動電機最高效率可以達到97%以上,電機超過85%的高效率區達到85%以上;
三是高密度、小型輕量化、集成化。即采用液冷結構、高電磁負荷、高性能磁鋼、高轉速等技術,實現電機小型輕量化和高密度化,并要求實現電傳動系統集成、電力電子集成;
四是可靠性、耐久性、免維護、可回收。由于車用電機處于振動大、沖擊大、灰塵多、溫度變化大的環境下運行,這就必然要求電機系統具有耐沖擊、長壽命、免維護,以及可回收利用。
五是低振動噪聲、電磁兼容與低成本。電動汽車NVH(振動噪聲)和EMC/EMI技術是整車研發水平的重要衡量指標,電機成本的高低是決定電動汽車能否產業化的重要因素。這也是電機電控系統供應商的挑戰所在,既要保證產品的低成本,還需要持續保持產品的性能不降低,還要持續投入新技術的研發。
六是智能化、自診斷與高安全性。這要求電機在運行過程中能夠實現狀態檢測、自我診斷與故障預警及分即處理能力,還要具備高功能安全等級。
我國電驅動系統產業現狀
在張舟云看來,驅動電機方面,我國驅動電機在功率密度、最高效率、峰值轉速、繞組制造工藝、冷卻散熱技術等方面與國外相當;多家驅動電機企業產能達到數十萬套級以上,部分產品批量出口歐美,比如精進電機就有些產品出口到了歐美國家。
在電力電子方面,五年前確實跟國際廠商之間有不少差距,但在最近五年,我國的車用電力電子控制器產品發展迅速,已經很接近國際廠商的水準了。我國的自主IGBT芯片、雙面冷卻IGBT模塊封裝、高功率密度電機控制器水平接近國外同類產品;碳化硅器件、全碳化硅控制器已經開始研發,自主封裝碳化硅模塊實現了量產。據比亞迪半導體有限公司芯片研發總監吳海平介紹,比亞迪在去年就推出了第三代SiC MOSFET模塊,采用了超聲波焊接和納米銀燒結技術,該產品已經在比亞迪最新的漢上得到是使用。其第四代SiC+雙面散熱型的SiC產品也正在研發當中。
目前Tesla的Model3也使用了SiC逆變器,張舟云認為現在的SiC逆變器價格還是偏貴的,但隨著越來越多的車企使用,價格應該會降下來。他預計未來兩三年會有越來越多的車企采用SiC產品。
在產業鏈方面,我國建立了電動汽車電驅動系統全產業鏈技術創新戰略聯盟,在關鍵材料和關鍵器件方面形成了自主的技術與產品,實現國產化替代和批量應用。
電驅動系統集成是發展趨勢
在新能源技術應用過程中,驅動電機、電機控制器和減速器深度集成的電驅動一體化總成是新能源汽車領域的主要技術方向。目前,國外以博世、大陸汽車、麥格納、吉凱恩、博格華納、采埃孚等為代表的電驅動系統集成商推出了電驅動一體化總程產品。我國起步與國外基本同步,比如上海電驅動、精進電動、巨一、匯川、比亞迪、上汽變速器等均推出了三合一電驅動總成系統,最高轉速達到13000~16000rpm,長安逸動EV460、比亞迪元EV360、廣汽Aion S已批量上市,精進電動的三合一電驅動總成實現出口。
集成化帶來的優勢是十分明顯的,不僅能夠減小系統體積與質量,提升整車布置便利性,增加車內乘坐空間;系統間的能量損耗也有望進一步降低,整體效率大幅提升;而且由于殼體、連接件的省略,系統成本與價格將會顯著下降;此外,也有利于模塊化標準供貨,縮短研發周期與匹配周期。
當然,集成化也是有一些弊端的,比如前期研發與匹配費用將會增加;NVH、可靠性、散熱等技術指標挑戰難度提升,對研發能力要求更高;而標準化供貨也意味著定制化空間有限,車企需要做出更多妥協。
不過,整體來看,集成化電驅動/電控系統是利大于弊的,已經成為了新能源汽車技術發展趨勢。
目前,電驅動系統的集成以三合一技術路線為主流,即將電機、電控(逆變器)與減速器集成為電驅橋,常見于插電混動和純電動車上。電控系統的集成則傾向多合一模塊,通常將變壓器、車載充電機、加熱器、功率分流模塊等進行集成,甚至會將VCU(整車控制器)、MCU等包含在內。國內的北汽新能源、長安新能源、中車時代等開發了多種形式的多合一總成,其中北汽EMD(E-Motion Drive)3.0動力總成系統為代表的純電多合一動力總成已經搭載在EU5系列車型上了。
隨著未來純電動車型的進一步滲透,集成化新能源模塊的應用將愈加廣泛。尤其是三合一的電驅動,由于其體積小、重量輕、成本低等核心優勢,在合資車企和自主品牌未來的純電平臺車型上均將成為標配。
比如在2020年北京國際車展上,精進電動展示了其全新一代的三合一電驅動總成(EDM)實現了高度的集成化和輕量化,各個子總成也都達到了國際領先的技術水準。精進電動在電機和減速器上都采用了公司獨到的“無泵油水復合冷卻”技術,不但實現了高強度的冷卻,也避免了油泵帶來的效率損耗;結合高效電機和減速器的設計,該總成達到了行業突出的連續功率水平。
華為則展示了其多合一電驅動系統DriveONE,據華為展臺技術人員介紹,這是業內首款超融合動力域解決方案,該系統通過電機、MCU、PDU、OBC、DCDC、減速器、BCU七大部件的高度集成,不僅實現了機械部件和功率部件的深度融合,還將智能化帶入到電驅動系統中,實現了端云協同與控制歸一。
廣汽新能源則發布了高性能兩擋雙電機“四合一”集成電驅,實現了雙電機、控制器和兩擋減速器深度集成。據介紹,接下來埃安系列車型將搭載該項新技術,屆時百公里加速用時縮短至2秒區間,刷新“中國最快的車”的加速記錄。
電驅動系統關鍵創新技術
具體來說,電驅動系統的關鍵技術包括驅動電機、電力電子器件、高速減變速器等。
在高密度驅動電機方面,大眾、沃爾沃、克萊斯勒等驅動電機最高轉速在不斷提升,最高達到了16000rpm,Tesla的Model 3電機達到了17900rpm。從繞組結構上看,發卡式繞組/扁導線繞組成為了明確的技術方向之一,目前通用、豐田和本田等企業在此類電機方面有投入,扁導線電機的電機功率密度可達到3.8~4.6kW/L。此外由于稀土材料的稀缺性,業內企業普遍在追求不用稀土或者少用稀土的電機產品。
在高密度電機控制器方面,芯片雙面焊接和系統級封裝是當前國外電機控制器主流封裝形式,比如電裝、博世、大陸等集成控制器功率密度已經達到了16~25kW/L。在雙電機插電式混動和高功率乘用車應用領域,直流電壓正呈現出從250V~450V提升到500V~800V的提升趨勢中。
在電力電子器件方面,除了現在常用的IGBT和MOSFET功率器件外,最近最受關注的莫過于SiC器件在汽車上的使用。SiC器件的高溫、高效和高頻特性是實現電機控制器功率密度和效率持續提升的關鍵要素。目前豐田、日立和電產推出了全SiC PCU。豐田帶載SiC PCU載工況下較IGBT PCU損耗降低了30%。Tesla采用標準的SiC器件并聯方式,研制的大電流全SiC電機控制器已經在整車上開始使用了。據張舟云透露,我國中科院電工所、比亞迪、中車和精進電動等也研制了SiC電機控制器樣機。其中,電工所的控制器功率密度達到了37.1kW/L@85℃。
在高速減速器方面,博格華納、吉凱恩、麥格納等開發出了14000~18000rpm的高速減速器。我國上汽變速器、重慶青山、比亞迪等自主減速器產品級最高轉速在12000~14000rpm之間,其中有廠商正在開發16000rpm減速器產品。好消息是,我國正持續在軸承、齒輪等配套關鍵零部件方面加快開發,并強化電機和減速器的深度集成。
張舟云分享說,電驅動系統的關鍵創新技術還包括NVH性能的提升和EMC/EMI的優化。
結語
總的來說,電驅動一體化總成是新能源汽車的發展方向,我們還需要再深度耦合集成設計、高速減速器,以及軸承、齒輪等關鍵零部件開發方面持續投入,研發出更多技術創新,性能優異,又成本可控的產品。因為汽車產業其實對成本要求也是很高,企業如何在既保證低成本的情況下,制造出客戶性能要求的產品來至關重要。
經過這些年的發展,其實我國的電驅動系統產業鏈已經取得了長足發展,國產化替代比例在逐漸上升中。
聲明:本文由電子發燒友原創,如需轉載和入群交流,請添加微信elecfans999,投稿爆料采訪需求,請發郵箱huangjingjing@elecfans.com。
-
新能源
+關注
關注
26文章
5560瀏覽量
107704 -
電機驅動
+關注
關注
60文章
1219瀏覽量
86843 -
SiC
+關注
關注
29文章
2853瀏覽量
62773
發布評論請先 登錄
相關推薦
電力驅動測試系統的技術原理和應用
飛凌嵌入式受邀亮相TI嵌入式技術創新發展研討會
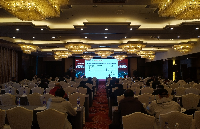
SCADA系統的 7 大最新發展趨勢!
匯川技術持續推動產業創新和低碳轉型升級
廣電計量聯合舉辦半導體技術創新發展論壇,標準引領創“芯”發展
安全,高效,靈活擴展的新能源汽車動力系統測試解決方案 | Vector與CSM助力核心技術創新,提升終端用戶體驗
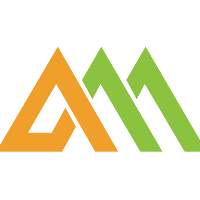
評論