本文討論了Pre-Switch的CleanWave評估系統,該系統演示了Pre-Switch技術如何使設計人員在200kW EV逆變器中以100 kHz的頻率實現99.1%的效率,從而將EV范圍提高多達12%。
讓我們從討論傳動系統和傳動系統損失開始。顯然,要擴大電動汽車的行駛里程,就需要同時提高電動機效率和逆變器效率。直到約50 mph時,動力傳動系統的損耗才是大多數EV損耗的主要控制點,此時風阻逐漸占據主導地位。但是,傳動系統損耗在EV的所有損耗中占最大份額,因此至關重要的是,我們要同時解決逆變器和電動機的問題。如果我們可以將電動機制造商和逆變器制造商放到同一房間,直接談論系統級傳動系統的效率,我們就可以實現EV范圍的顯著改善。
盡管電機制造商可以引用高效率數字,但這通常隱藏了一個問題。車輛制造時提供了很大的扭矩來加速行駛-遠遠超過了巡航所需的大部分時間。當以低扭矩水平巡航時,提供高效的電動機和逆變器具有挑戰性。思考它的另一種方法是速度。當電動機遠未達到峰值效率時,車輛的絕大部分運轉將以低于60 mph的速度進行-達到最大扭矩的3-5%。
如今,在開關損耗和更高的電機效率之間進行了權衡。電動機動力傳動系統的損耗隨開關頻率的增加而降低,但逆變器損耗卻增加。盡管碳化硅通過減少逆變器損耗幫助實現了這一目標,但它并沒有真正改變平衡。因此,盡管可以通過以更快的開關頻率運行來降低電機損耗,但大多數逆變器制造商仍以約10 kHz的頻率運行其碳化硅FET。可悲的是,解決方案不只是簡單地以較高的開關頻率進行開關。更快的開關速度會帶來更高的開關損耗,從而降低逆變器效率。同樣,如果您想嘗試更快地切換并保持較高的逆變器開關頻率,則需要添加更多的MOSFET來降低傳導損耗,以補償不斷增加的開關損耗。這導致逆變器成本,尺寸和重量增加。另一個問題是,如果處理不當,SiC的晶體管邊緣速度更快會導致電機性能下降和滾珠軸承損壞。是的,您可以制造堅固的電機,但這不可避免地要花錢。由于所有這些原因,開關速度已長時間保持在5-15 kHz。
Pre-Switch通過將AI嵌入到FPGA中來解決這一挑戰,該FPGA用于精確控制輔助諧振晶體管的時序,如圖1所示為S1和S2。其結果是實際上消除了主要碳化硅工作中的所有開關損耗晶體管(Q1和Q2)。(對于硅IGBT,我們可以消除大約70-80%的損耗,但是本文將主要關注SiC)。獨特地,我們的AI消除了在環境,輸入電壓和負載條件不斷變化的整個范圍內的開關損耗。
圖1:開關將AI嵌入到FPGA中,該FPGA精確控制輔助諧振晶體管S1和S2的時序
在每個開關周期,調整輔助諧振晶體管S1和S2的時序,以確保Q1和Q2的開關損耗實際上為零。在開關之間放置電容器時,預開關可減少SiC快速瞬態邊沿速度帶來的系統級問題,并且可以對其進行編程以滿足應用需求。此外,在每個開關周期中,Pre-Switch會基于對每個開關如何以及何時進行轉換的全面了解來計算,調整并最小化死區時間。這簡化了控制。最后,由于Pre-Switch逐周期控制所有內容,因此增強了系統級保護,并最大程度地減少了故障響應時間。系統級別的錯誤從內置的通信端口傳回主機。
為了演示該過程,讓我們看一下GIF(圖2),它顯示了20個不同的開關周期。在初始加電時以及隨后的前三個開關周期中,該算法開始學習過程,但輸出為系統可能處于任何狀況而準備的諧振電流。然后在第4個在切換周期中,該算法會進行首次AI預測的校正,以實現優化的軟切換。在這種情況下,請注意電感諧振電流(綠色)的大幅降低和優化。展望未來,對于每個隨后的開關周期,該算法將獨立調整諧振電感器電流,以確保其短暫地在負載電流之上擺動(以藍色顯示)。所有調整都足夠快,以確保在任何PWM輸入下都能進行精確的軟切換,并可用于與DC-AC逆變器一起創建完美的正弦波。該系統還可以反向無縫運行。
圖2:開關周期顯示了加電,算法學習過程以及正在進行的更正以優化軟開關
那么,我們如何消除開關損耗呢?圖3比較了使用傳統“硬”開關技術(3a)和“預開關”架構(3b)的“開通”開關損耗。在3a中,我們看到一個800V輸入:一個開關已經打開,電壓相應下降,電流上升。波形之間的重疊(藍色和品紅色)是開關損耗。該圖還顯示了所消耗的總能量(在這種情況下為2.5 mJ)。在切換前解決方案(3b)中,轉換速度變慢,以確保電壓和電流波形不重疊,從而實際上消除了開關損耗。
圖3:使用“硬”開關技術(a)與預開關架構(b)比較導通開關損耗
考慮到相同的關斷損耗曲線圖(圖4),重疊實際上很小,顯示出開關損耗大大降低,并且所消耗的能量很小– 0.013 mJ,而硬開關方法僅為1.25 mJ。另外,dV / dT也降低了。
盡管由于驅動預切換解決方案所需的開銷(例如,給FPGA供電)會產生一些較小的能量損耗,但它們的影響很小,尤其是在考慮到同時運行三個開關的系統級損耗時尤其如此。我們計算出,軟開關預開關解決方案所節省的能源至少為94%。
圖4:關閉損耗比較
隨著開關損耗的消除,出現了新的設計自由度。圖5使用來自Wolfspeed CAB450M12XM3電源模塊的數據,并顯示了流經其設備的電流量。硬開關紅線表明,隨著模塊開關速度的加快,必須減少電流量。與“切換前”軟開關綠色曲線相比,我們發現,在開關頻率增加的情況下,實際上可以流經同一器件的電流量并沒有減少。因此,可以將系統速度提高到100 kHz,而不是以10 kHz的速度運行。這意味著逆變器效率更高,可以使用更小的晶體管,并且可以使輸出具有更少的電流紋波,這使得冷卻器更高效,冷卻成本更低。還,減少了振鈴和過沖,并最大程度地減少了軸承損壞的問題。但關鍵是,系統可以在預切換曲線上的任何位置運行,從而提供了極大的設計靈活性。
圖5:預切換提供了設計靈活性
預切換的好處
大多數設計人員都在看我們的強制諧振電路,并錯誤地認為,在工作半橋的中點處串聯增加的小半橋比原始的半橋解決方案昂貴。畢竟還有更多零件,對嗎?好吧,現實情況是,在強制諧振電路中增加的總芯片面積明顯小于通過消除工作晶體管中的開關損耗而節省的成本。讓我進一步解釋。強制諧振開關通常僅占據工作半橋的裸片面積的25-33%,因為它們僅在占空比上明顯小于工作開關才能工作。(例如:在10kHz時為開關周期的0.5%,在100kHz時為開關周期的5%)。進一步,諧振開關只需要主開關的一半的隔離電壓。現在,讓我們考慮一下在主要的SiC半橋中節省的成本。開關損耗的減少使主開關的裸片面積減小了33-50%,而輔助開關的電壓是其兩倍。然后,在電動機或輸出濾波器中節省了10倍的較高開關頻率-天氣,從而節省了大量系統資源。最后,可節省大量系統級的冷卻,減輕重量,節省dV / dt并提高安全性。然后,在電動機或輸出濾波器中節省了10倍的較高開關頻率-天氣,從而節省了大量系統資源。最后,可節省大量系統級的冷卻,減輕重量,節省dV / dt并提高安全性。然后,在電動機或輸出濾波器中節省了10倍的較高開關頻率-天氣,從而節省了大量系統資源。最后,可節省大量系統級的冷卻,減輕重量,節省dV / dt并提高安全性。
考慮電動機的好處時,硬開關逆變器總是會通過最小化開關頻率以保持較高的逆變器效率而受到損害。結果是大量的輸出紋波被電動機濾除。與發送到電動機的純正弦波的每一個偏差都是浪費的能量,這種能量以在電動機內部發生的感應加熱器的形式表現出來。很明顯,這些熱量需要消散,這是另一項成本。開關頻率提高10到20倍后,Pre-Switch的CleanWave近乎完美的正弦波輸出可帶來更高的電機效率并減少電機所需的冷卻。
這一點的重要性如圖6所示。現在,逆變器的損耗不再增加,而是在整個開關頻率范圍內得到了有效減小。電動機損耗隨著頻率的增加而減少,最終結果是節省了大量的系統級電源。回到關于轉矩和最大電動機效率的討論,當采用Pre-Switch進行100 kHz或更快的開關速度時,電動機效率在低轉矩和中低RPM時得到了最明顯的改善,這是大多數驅動的地方。這就是我們將EV范圍提高5-12%的方式。
圖6:減少的總傳動系統損失導致EV范圍增加了5-12%
結論與評價體系
總之,通過消除開關損耗,預開關可以在100 kHz或更高頻率下大幅提高逆變器和電機的效率。結果是預期的EV范圍增加了約5-12%;通過減少晶體管的數量以及減少冷卻需求,這可以實現成本更低的系統。當然,通過提高電機效率,可以減小電池尺寸,這是一個巨大的好處,可以節省成本。預切換還通過降低dV / dT解決了電機難題,并節省了導致軸承性能下降的差分共模噪聲。最后,由于Pre-Switch會逐周期進行調整,因此系統能夠對系統中任何位置的故障做出快速反應,從而提供卓越的安全性和保護功能。
CleanWave評估系統(現已交付給全球主要客戶)是一個200 kW的三相電源塊,運行于100 kHz。它可以在5至100 kHz的任何開關頻率下運行。效率為99%。
編輯:hfy
-
FPGA
+關注
關注
1630文章
21769瀏覽量
604648 -
AI
+關注
關注
87文章
31262瀏覽量
269627 -
開關損耗
+關注
關注
1文章
63瀏覽量
13508
發布評論請先 登錄
相關推薦
AI模型部署邊緣設備的奇妙之旅:如何實現手寫數字識別
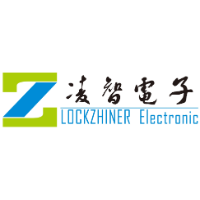
索尼和本田將在新EV中引入AI智駕功能
MCU如何實現AI功能
risc-v多核芯片在AI方面的應用
AI正通過智能家居幫助我們入眠
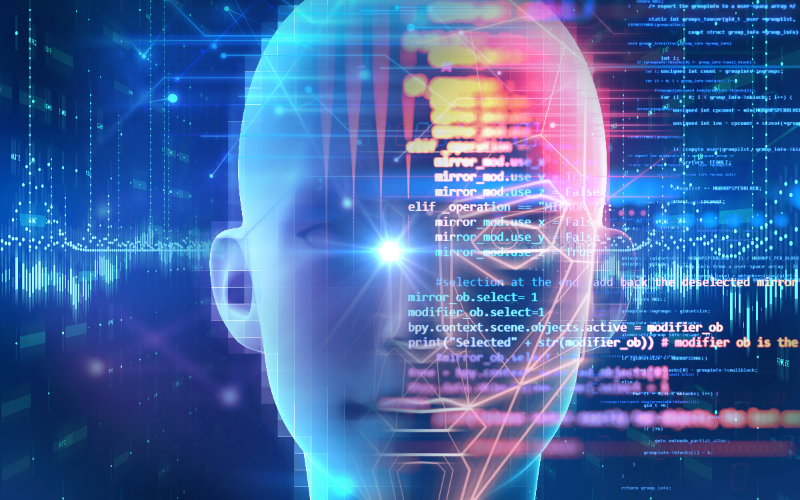
開發者手機 AI - 目標識別 demo
M12 17芯插座的公差范圍是多少
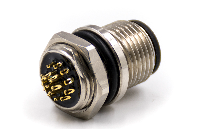
支持I2C和多達12個通道的電源序列發生器TPS38700數據表
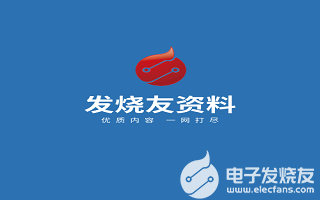
NanoEdge AI的技術原理、應用場景及優勢
嵌入式系統發展前景?
NVIDIA Jetson為嵌入式計算領域探索AI可能
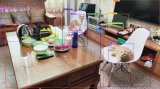
評論