該客戶是一家具有全球網絡的國內知名食品加工集團公司,在國內外設立多個生產基地,擁有超過5000名員工,同時也是首家零缺陷通過美國FDA在中國全國性審核活動的食品加工企業。
受工廠地理位置影響,其頂層3樓原料倉夏天溫度居高,不適宜工作人員長期在原料倉待命。當生產車間發出物料配送任務時,工作人員從獲取任務信息到抵達3樓取貨,整個流程耗時需約20分鐘。
且樓層與樓層間物料轉運使用的為老式貨梯,容納空間十分狹窄(一板貨物),一旦托盤放置不當,貨物則難以取出。缺少對貨梯出入庫的有效管理,多樓層間的出入庫搬運任務經常發生沖突,導致配料不及時,大大降低了生產效率。
為深化生產管理系統建設、滿足技術升級的行業需求,該客戶將己方工廠的物流無人化升級提上日程,采用未來機器人柔性物流無人化解決方案,最終實現集團產品競爭力的提升。
項目需求
客戶現場總計3個樓層,其中一樓為卸貨區,二樓為生產車間,三樓為原料倉。運送物料為空瓶包材,載具以川字托盤為主,部分采用田字托盤。無人叉車AGV將原料從一樓月臺搬運到三樓原料倉進行入庫存儲,待二樓產線發出配料需求時,無人叉車AGV將三樓原料倉的原料轉運到二樓產線,二樓共有5條生產線。
方案/產品
小型前移式無人叉車
明眸環境監控系統
通過客戶現場倉庫管理系統WMS和未來機器人WCS無縫對接,實際數據流精準快速交付。此項目涉及到的系統包括:明眸庫位監測系統WCS、電梯對接系統、手持終端系統等,實現了人、貨、車、設備的全方位管控。
方案概述· 遵循原有作業流程
(1)原材料入庫:從一樓月臺到三樓原料倉
當原材料從一樓月臺卸貨貼碼后,倉庫管理系統發布指令,視生產實際情況為兩臺貨梯分配任務:若是閑時,則使用兩臺貨梯將原料從一樓轉運到三樓原料倉入庫;若產線處于生產忙時,則分配一臺貨梯用于三樓原料倉到二樓產線的物料轉運。
當一樓的貨物進入電梯后,三樓的無人叉車AGV將自動前往三樓電梯口等待。若此時系統未發出任何出庫指令,則兩臺無人叉車AGV協同完成入庫任務。
方案亮點:?往期在客戶現場,人工叉車將貨物搬運入貨梯的情況下,貨物擺放不當的情況時有發生,導致貨物難以從貨梯中快速取出。如今,無人叉車AGV在不進入電梯的情況下,通過車頭+叉臂端搭載的多個傳感器,可自動檢測托盤位置、判斷貨物傾斜情況。
?無人叉車AGV可自適應調整位姿以叉取貨物,防止貨物由于擺放位置不標準,出貨梯途中摩擦到貨梯部件甚至發生貨物倒塌的情況。
?無人叉車AGV配備車載掃碼裝置(RFID),掃碼獲取貨物信息后,自動將貨物搬運至系統指定庫位。
(2)產線配料:從三樓原料倉到二樓產線緩存區
當產線有配料需求時,系統下達原料出庫任務給三樓的無人叉車AGV,與二樓產線的無人叉車AGV進行協作,將原料轉運到對應的線庫緩存區。整個流程由之前的20分鐘縮短到10分鐘,有效節約時間成本,提高生產效率。
方案亮點:?針對二樓的5條產線,未來機器人分別設立了對應的5個線庫緩存區。每個緩存區設有10個庫位,在未來機器人明眸庫位監測系統的管理下,實現智能化、可視化、高效的庫位利用。 ?在明眸庫位監測系統的監控下,線庫緩存區的庫位情況可實時上傳到倉庫管理系統中,若線庫中的一列貨物被取走,則中控系統調度三樓原料倉的無人叉車AGV進行原料出庫,保證緩存區原料充足,靈活適應不同產線的生產原料消耗情況,保證每條產線生產順暢。
(3)庫存管理:三樓原料倉
在生產閑時,倉庫管理系統下達任務,指示3樓原料倉無人叉車AGV整理庫位。
方案亮點:
?通過未來機器人深度學習視覺感知技術,識別容量不滿的托盤,并將其歸置到指定區域、統計剩余庫容數量,為未被占用的托盤騰出庫位空間,釋放庫容壓力、增加庫容量,有利于客戶進行庫容管理。
原文標題:標桿案例:無人叉車在多樓層物料轉運中進行協作,助力知名食品加工企業實現智能化生產管理
文章出處:【微信公眾號:機器人在線訂閱號】歡迎添加關注!文章轉載請注明出處。
責任編輯:haq
-
監控系統
+關注
關注
21文章
3939瀏覽量
175955 -
電動叉車
+關注
關注
5文章
37瀏覽量
8514
原文標題:標桿案例:無人叉車在多樓層物料轉運中進行協作,助力知名食品加工企業實現智能化生產管理
文章出處:【微信號:im_robotic,微信公眾號:機器人在線訂閱號】歡迎添加關注!文章轉載請注明出處。
發布評論請先 登錄
相關推薦
MES 生產管理系統:企業成本控制與質量提升的強大助力
rfid工業讀寫方案,賦能產線高效生產管理
中小企業是否需要引入生產管理MES系統
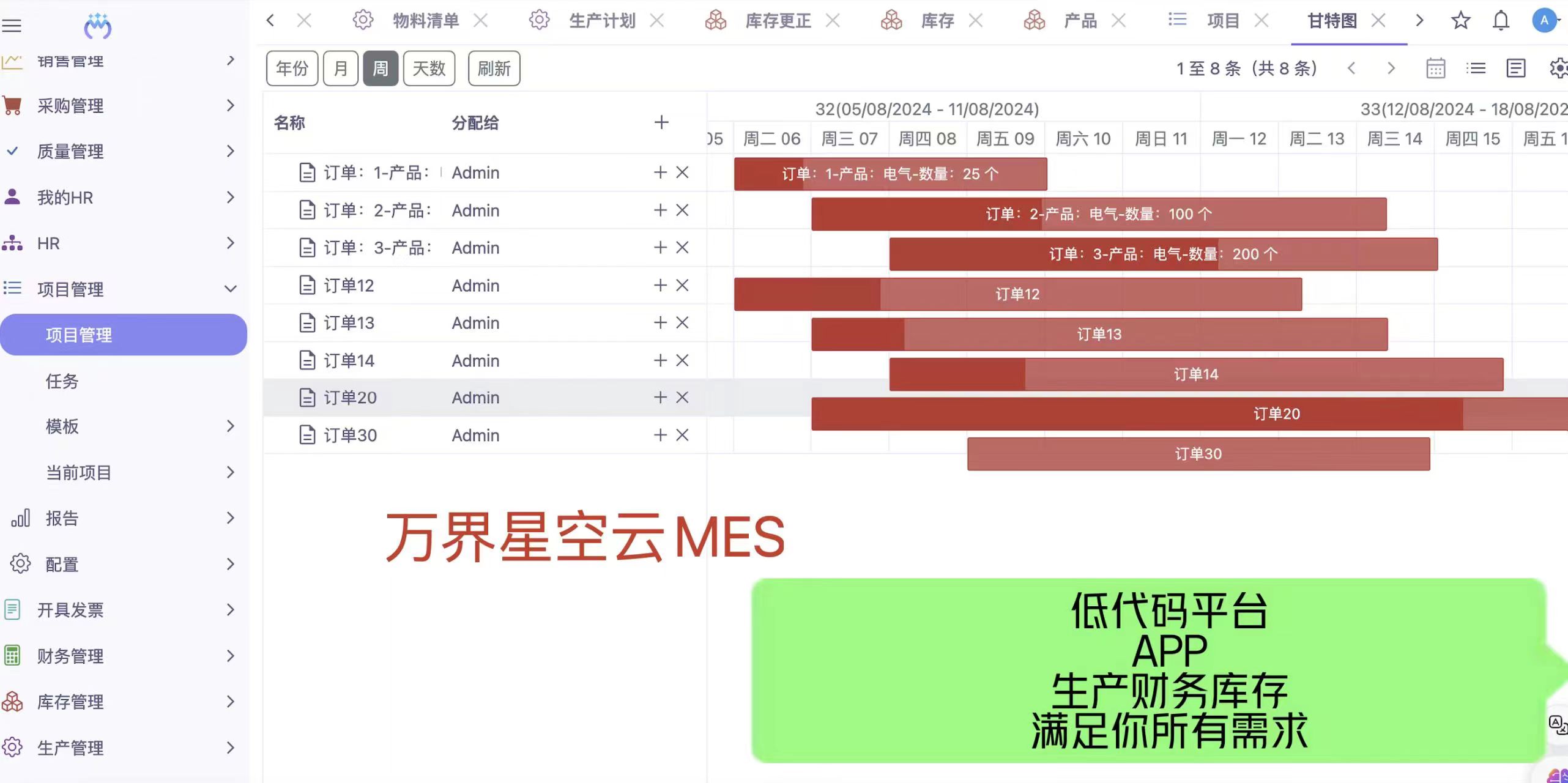
數字化生產管理物聯網系統解決方案
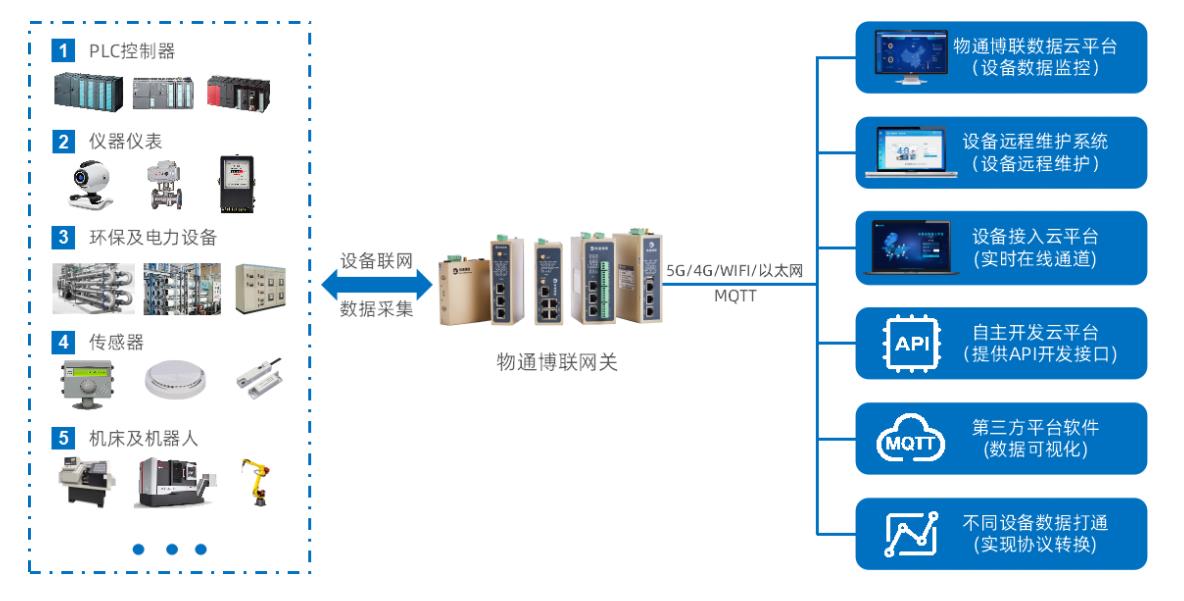
評論