如今,電池供電的電機驅動解決方案通常可以使用非常低的工作電壓提供數百瓦的功率。在這類應用中,若要確保整體系統的能效和可靠性,就必定要正確管理流經電子設備驅動電機的電流。事實上,電機電流可能超過數十安培,導致逆變器內部的功率耗散增加。逆變器元器件的功率越大溫度就越高,如果超過允許的最大額定值,性能就會下降甚至突然發生中斷。熱性能的優化,結合緊湊的外形尺寸,是逆變器設計階段的一個關鍵方面;如果處理不當,可能會產生隱患。這個問題的解決方法之一是生產通過現場驗證持續完善的原型。但是,電氣評估和熱學評估過去是完全分開的,電熱耦合效應在設計期間從未得到解決。這往往導致需要多次迭代和漫長的上市時間。當前有一種更有效的替代方法,通過利用現代仿真技術來優化電機控制系統的電熱性能。Cadence? Celsius? Thermal Solver 是一款用于系統分析的業界領先電熱協同仿真軟件,只需短短幾分鐘就能從電氣和熱學的角度對設計性能進行全面和準確的評估。領先的工業電機控制集成電路制造商 STMicroelectronics 使用 Celsius? 對其 EVALSTDRIVE101 評估板進行了微調。最終獲得一個適用于三相無刷電機的逆變器,能夠驅動高達 15 Arms 的電流,供最終應用設計人員參考使用。在本文中,我們將借此機會介紹 STMicroelectronics 所采用的工作流程,其能將 EVALSTDRIVE101 投入量產,同時減少熱優化所需的工作量。
EVALSTDRIVE101
EVALSTDRIVE101 以 STDRIVE101 為基礎,后者是一款 75 V 三重半橋柵極驅動器,通過四通道扁平無引腳 (QFN) 4x4 mm 封裝提供保護,非常適合電池供電型解決方案,其六個 STL110N10F7 功率 MOSFET 排列成三個半橋。Celsius? 極大地簡化了 EVALSTDRIVE101 的優化過程,在短時間內便實現了緊湊且可靠的設計。正如下文所討論,仿真結果被用來對元器件的放置進行迭代調整,完善平面和印制線的形狀,修改層厚度,增加或刪除過孔,從而獲得可生產版本的逆變器。經優化的 EVALSTDRIVE101 布局由四個寬度為 11.4 cm,高度為 9 cm 的 2 oz 銅層組成,使用 36 V 電池電壓可向負載提供高達 15 Arms 的電流。從熱學角度來看,EVALSTDRIVE101 最關鍵的部分是功率級區域,主要包括功率 MOSFET、分流電阻器、陶瓷旁路電容器、大容量電解電容器和連接器。這部分的布局被大幅縮減,只占總體板尺寸的一半,即 50 cm2。在此方面,我們特別留意了 MOSFET 的放置和布線,因為在逆變器運行期間,這些元器件造成了大部分的功率損耗。頂層所有 MOSFET 漏極端子的銅面積都被最大化,并在可能的情況下復制到其他層并放大,以改善熱量向板底面的傳遞。這樣一來,電路板的頂面和底面都能通過自然對流和輻射有效地加快熱量的耗散。不同層之間的電氣和熱連接是由直徑 0.5 mm 的過孔提供,這有利于空氣流動和改善冷卻。在 MOSFET 裸焊盤的正下方有一個過孔網格,但其直徑被縮小到 0.3 mm,以防止焊膏在孔中發生回流。
估算功率損耗

圖 1:仿真的頂層電流密度。(圖片來源:STMicroelectronics)

圖 2:仿真的頂層穩態溫度。(圖片來源:STMicroelectronics)
EVALSTDRIVE101 的熱優化從估算逆變器在運行期間的功率耗散開始,這是熱仿真器的輸入之一。逆變器的損耗可分為兩部分:由電路板印制線內的焦耳效應引起的損耗,以及由電子元器件引起的損耗。雖然 Celsius? 可以直接通過導入布局數據,精確地確定電流密度和電路板損耗,但因電子元器件而造成的損耗仍須通過計算才能獲得。盡管電路仿真器可以提供非常精確的結果,但我們決定使用簡化的公式來獲得合理但存在一定近似的功率損耗估算值。事實上,制造商可能無法提供元器件的電氣模型,而且由于缺乏建模數據,可能很難或無法從頭開始實現模型,而提供的公式卻只需要規格書中的基本信息。如果不考慮次級現象,逆變器的功率耗散以分流電阻器 Psh 和 MOSFET 的內部損耗為主。這些損耗分別表示為傳導損耗 Pcond、開關損耗 Psw 和二極管壓降損耗 Pdt:

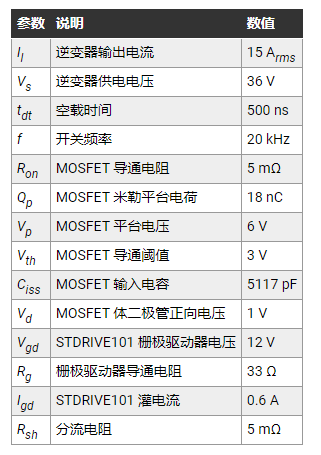
每個 MOSFET 估算的功率耗散為 1.303 W,每個分流電阻器為 0.281 W。
熱仿真
Celsius? 允許設計人員進行仿真,包括對系統進行電氣分析,顯示印制線和過孔中的電流密度以及電壓降。這些仿真要求設計人員使用系統的電路模型來定義感興趣的電流回路。EVALSTDRIVE101 的每個半橋采用的模型如圖 3 所示。它包括兩個放置在輸出與電源連接器之間的恒流發生器,以及三個將 MOSFET 和分流電阻器旁通的短接電路。這兩個電流回路有效地擬合了整個電源軌和地平面的實際平均電流,而輸出路徑電流則略微偏大,這是評估設計穩健性的一個便捷工作條件。圖 4 和圖 1 分別顯示了電流為 15 Arms 的 EVALSTDRIVE101 的電壓降和電流密度。相對于接地基準的電壓降突顯了經過特別優化的布局,該布局沒有瓶頸,并且在 U、V 和 W 分別擁有良好平衡的 28 mV、25 mV 和 23 mV 輸出。輸出 U 顯示了最高電壓降,而輸出 W 由于距離電源連接器的路徑長度較短,是三者中最低的一個。電流在各個路徑上分布良好,平均密度低于針對電源印制線尺寸推薦的值 15 A/mm2。在靠近 MOSFET、分流電阻器和連接器的位置,有一些突出顯示的紅色區域。這些區域代表由于元器件的端子小于底層的電源印制線而產生的更高電流密度。但是,最大電流密度仍舊遠低于在現實中可能造成可靠性問題的 50 A/mm2 限值。

圖 3:電流回路建模。(圖片來源:STMicroelectronics)
設計人員可利用仿真器來設置和運行穩態或瞬態仿真。前者為各層和元器件提供單一的二維溫度圖,后者則以更長的仿真時間為代價,提供每個仿真時刻的即時升溫曲線圖。穩態仿真所需的設置可以應用于瞬態仿真,但還需要定義元器件的功率耗散函數。瞬態仿真適合針對具有多個非同時激活的電源的系統定義不同的工作狀態,以及評估達到穩態溫度所需的時間。

圖 4:仿真的內層電壓降。(圖片來源:STMicroelectronics)
EVALSTDRIVE101 仿真是在 28℃ 的環境溫度下進行的,以傳熱系數為邊界條件,并為器件使用雙電阻器熱模型。這些模型被用來取代 Delphi 等詳細熱模型,因為它們可以直接在元器件的規格書中獲取,但也略微犧牲了仿真精度。圖 4 提供了 EVALSTDRIVE101 的穩態仿真結果,圖 5 提供了瞬態仿真結果。瞬態仿真中使用了階躍功率函數,在零時間點啟用所有 MOSEFT 和分流電阻器。仿真結果表明,U 型半橋區域是電路板上最熱的地方。Q1 MOSFET(高壓側)的溫度為 94.06 °C,其次是 Q4 MOSFET(低壓側)、R24 和 R23 分流電阻器,溫度分別為 93.99 °C、85.34 °C 和 85.58 °C。

圖 5:仿真的 U 型半橋元器件升溫。(圖片來源:STMicroelectronics)
熱特征化設置
在生產之后對 EVALSTDRIVE101 的熱性能進行了實驗性特征化。為便于實現,我們沒有使用連接到制動試驗臺的電機,而是考慮了一個如圖 6 所示的等效測試平臺。EVALSTDRIVE101 與一塊控制板相連,以產生必要的驅動信號,并被放置在一個有機玻璃箱內,在獲得對流形式的系統冷卻的同時,避免了意外的氣流。玻璃箱上方放置了一臺熱成像相機(Nippon Avionics 生產的 TVS-200 型),它通過箱蓋中的一個孔對電路板進行取景。一個三相負載被連接到電路板的輸出端,系統的供電電壓為 36 V。該負載由三個按星形配置連接的線圈組成,用于模擬電機。每個線圈的飽和電流為 30 A,電感為 300 μH,寄生電阻僅為 25 mΩ。低寄生電阻大大減少了線圈內部的焦耳熱效應,有利于在電路板與負載之間實現無損電力傳輸。通過控制板施加適當的正弦電壓,在線圈內產生了三個 15 Arms 的正弦電流。利用這種方法,功率級在非常接近最終的電機驅動應用的工作條件下工作,而且還有一個優勢,不需要控制回路。

圖 6:熱特征化設置。(圖片來源:STMicroelectronics)
測量功率損耗
功率級上每個器件的功率耗散數據的精度,當然是影響仿真結果質量的因素之一。這個數據是對 MOSFET 和分流電阻器使用簡化公式獲得的,因此引入了近似。在電路板上進行測量,以評估量化耗散功率的誤差。電路板功率損耗 Ploss 的測量方法是,輸入功率 Pin 與在三個輸出端提供給負載的功率 PUout、PVout 和 PWout 的差值。測量使用了示波器(Teledyne LeCroy 的 HDO6104-MS 型號),并對波形應用了適當的數學函數:首先,計算電壓和電流的逐點乘積,然后對整數個正弦周期的功率求平均值。下表顯示了在環境溫度下,以及當功率級達到穩態條件時的熱狀態下得到的測量結果。此外還提供了之前通過公式估算的電路板的總體耗散功率值。
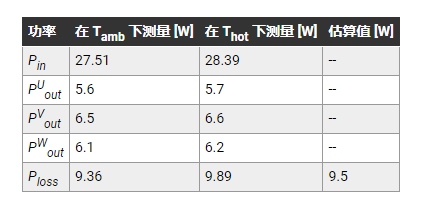
結果顯示,測量值與估算值之間高度吻合,與引入的近似是一致的。該公式相對室溫下的測量結果高估了 1.5%,與熱狀態下的數據相比,大約低估了 3.9%。這一結果符合與 MOSFET 導通電阻和分流電阻器相關的變異性,因為計算中使用的是標稱值。不出所料,由于線圈和 MOSFET 的電阻隨溫度的升高而增大,所有高溫下的功率值都要比室溫下的高。該數據還顯示了在三個輸出端測量的功率之間的差異。這種影響是由于三相負載的不平衡造成的,因為各線圈的 L 值和 R 值略有不同。但是,這種影響起到的作用微乎其微,因為觀察到的偏差低于測量值與估計值之間的偏差。
溫度結果
負載中正弦電流的產生和熱成像相機對熱圖像的采集是同時啟動的。熱成像相機先前被配置為每 15 秒采集一次熱圖像,并在每次采集中包括元器件 Q1、Q4 和 R23 的三個溫度標記。該系統持續保持活動狀態,直至大約 25 分鐘后達到穩態條件。測試結束時,箱內檢測到的環境溫度約為 28℃。圖 7 顯示了從溫度標記推導出的電路板的加熱瞬態,圖 8 顯示了電路板上的最終溫度。測量結果顯示,Q1 MOSFET 是整個電路板上最熱的元器件,溫度為 93.8°C,而 Q4 MOSFET 和 R23 電阻器分別達到了 91.7°C 和 82.6°C。如前所述,Celsius? 仿真得到的 Q1 MOSFET 溫度為 94.06°C,Q4 MOSFET 溫度為 93.99°C,R23 溫度為 85.58°C,與測量結果高度吻合。直接比較圖 5 和圖 7 可以輕松發現,加熱瞬態的時間常數方面也有同樣的一致性。

圖 7:測量的 U 型半橋元器件升溫。(圖片來源:STMicroelectronics)

圖 8:測量的頂層穩態溫度。(圖片來源:STMicroelectronics)
結語
STMicroelectronics 最近發布了 EVALSTDRIVE101 評估板,其設計利用了 Cadence? Celsius? Thermal Solver。該電路板面向的是電池供電應用所需的高功率和低電壓三相無刷電機控制。它包括一個 50 cm2 的緊湊型功率級,可以向電機提供超過 15 Arms 的電流,而不需要散熱器或額外的冷卻。利用熱仿真器內嵌的各種仿真功能,不僅可以預測電路板的溫度曲線及其功率級元器件上的熱點,還可以詳細說明沿著電源印制線的電壓降和電流密度,而這些信息要是通過實驗測量來獲取,可能會非常棘手,甚至根本不可能做到。從設計早期到簽核,利用仿真輸出可以快速優化電路板布局,調整放置并糾正布局中的弱點。使用紅外相機進行的熱特征化表明,仿真的和測量的穩態溫度以及瞬態溫度曲線之間存在良好的一致性,從而證明了該電路板的出色性能,以及熱仿真器在幫助設計人員減少設計裕量和實現快速上市方面的有效性。
-
電機控制
+關注
關注
3537文章
1886瀏覽量
269017 -
逆變器
+關注
關注
286文章
4737瀏覽量
207269 -
仿真器
+關注
關注
14文章
1019瀏覽量
83839 -
電池
+關注
關注
84文章
10644瀏覽量
130480
發布評論請先 登錄
相關推薦
大功率電池供電設備逆變器板如何助力熱優化
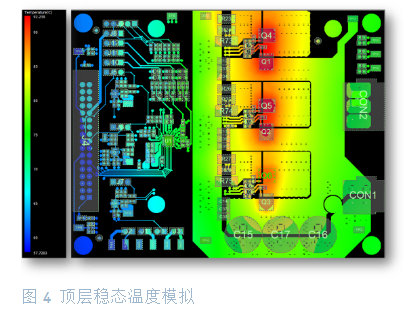
評論