摘要
本文提出了一種用于實(shí)現(xiàn)貫穿芯片互連的包含溝槽和空腔的微機(jī)械晶片的減薄方法。通過研磨和拋光成功地使晶圓變薄,直至達(dá)到之前通過深度反應(yīng)離子蝕刻蝕刻的空腔。研究了腐蝕結(jié)構(gòu)損壞的可能原因。研究了空腔中顆粒的捕獲,并制定了清潔程序來解決這一問題。到目前為止所取得的結(jié)果允許進(jìn)一步加工薄晶圓,通過電鍍銅形成晶圓互連。通過替代清潔程序,可進(jìn)一步改善減薄表面的質(zhì)量。
介紹
高密度三維(3D)集成是通過將2D集成電路擴(kuò)展到垂直方向來實(shí)現(xiàn)的。因此,它可以在體積減小的情況下提高密度,并大大縮短互連時(shí)間,從而顯著提高高速、低功耗的性能。通過芯片互連是實(shí)現(xiàn)高密度三維集成、RF(射頻)MEMS(微機(jī)電系統(tǒng))結(jié)構(gòu)和微傳感器封裝的重要方面。減薄晶片是實(shí)現(xiàn)高密度、密集互連的重要步驟。具體而言,使用微機(jī)械結(jié)構(gòu)(如深溝槽、通孔或空腔)細(xì)化晶圓,以獲得定義明確且可控的通孔,是一個(gè)具有挑戰(zhàn)性的步驟。
本文研究了微機(jī)械結(jié)構(gòu)硅片的機(jī)械減薄。其目的是構(gòu)建完整的三維結(jié)構(gòu),包括芯片互連。在對(duì)正面的通孔溝槽進(jìn)行深度干法蝕刻后,通過研磨和化學(xué)機(jī)械拋光從背面進(jìn)行晶圓減薄。晶圓變薄后,采用電鍍銅形成貫穿芯片互連。還研究了減薄過程中空腔結(jié)構(gòu)的行為。
結(jié)果和討論
硅的深度干法蝕刻的最大深度在很大程度上取決于等離子體的配置和功率以及對(duì)掩模層的蝕刻選擇性、掩模層厚度和開口。晶圓手柄是晶圓減薄的一個(gè)重要方面,尤其是當(dāng)晶圓減薄至100μm或更小時(shí)。晶圓的機(jī)械強(qiáng)度降低,難以處理。為了克服這一問題,采用了一種支撐或手柄,將晶片粘合或粘合到待減薄的晶片上。硅晶片或玻璃晶片都可以用作支撐晶片。但是,應(yīng)考慮粘接過程中出現(xiàn)的熱問題。為了避免上述問題,必須考慮熱膨脹的兼容性。我們已經(jīng)成功地將通過蠟連接到另一個(gè)硅片或薄玻璃片的硅片減薄至30μm。另一種方法,已經(jīng)給出了成功的結(jié)果,并且不會(huì)受到上述熱問題的影響,就是將水粘合到平板玻璃基板上。
當(dāng)研磨到達(dá)孔或溝槽時(shí),孔或溝槽區(qū)域可作為磨粒的捕集中心。顆粒的另一個(gè)來源也來自研磨過程中的硅本身和破碎結(jié)構(gòu)的小塊。此外,化學(xué)機(jī)械拋光過程還產(chǎn)生非常小(例如:0.3μm)且始終帶電的顆粒。因此,必須解決研磨和拋光后去除此類顆粒的問題。我們已經(jīng)測試了各種清潔程序。一種常用的方法是超聲波攪拌,然后進(jìn)行RCA清洗。
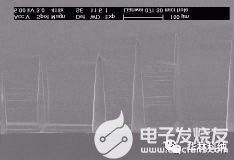
圖2:ICP下深度反應(yīng)離子蝕刻后溝槽和孔洞的橫截面。
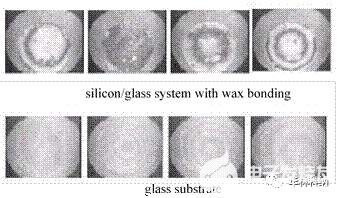
圖3:冷卻循環(huán)期間硅/玻璃(上部)和玻璃基板(下部)的表面平整度
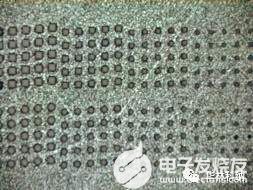
圖8:研磨和化學(xué)機(jī)械拋光后晶圓背面的光學(xué)顯微照片
結(jié)論
總之,我們通過研磨和拋光到30-80μm,研究了微機(jī)械晶片的減薄過程。對(duì)不同長寬比和形狀的深蝕結(jié)構(gòu)進(jìn)行了測試。該結(jié)構(gòu)可在該過程中存活至臨界最終厚度,該厚度取決于幾何因素以及研磨和拋光參數(shù)。討論了深孔和溝槽區(qū)域可能出現(xiàn)的厚度變化,并對(duì)邊緣損傷進(jìn)行了分析。仍然需要對(duì)清潔程序進(jìn)行進(jìn)一步研究,以避免在孔或溝槽中捕獲顆粒。
審核編輯:符乾江
-
半導(dǎo)體
+關(guān)注
關(guān)注
334文章
27363瀏覽量
218713 -
晶圓
+關(guān)注
關(guān)注
52文章
4912瀏覽量
127988
發(fā)布評(píng)論請(qǐng)先 登錄
相關(guān)推薦
晶圓為什么要減薄
晶圓背面涂敷工藝對(duì)晶圓的影響
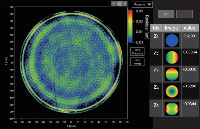
晶圓的TTV,BOW,WARP,TIR是什么?
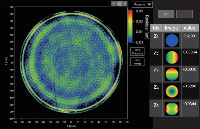
改善晶圓出刀TTV異常的加工方法有哪些?
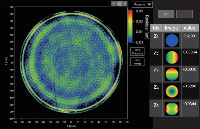
芯豐精密第二臺(tái)12寸超精密晶圓減薄機(jī)成功交付
硅晶圓的制備流程
晶盛機(jī)電減薄機(jī)實(shí)現(xiàn)12英寸30μm超薄晶圓穩(wěn)定加工
碳化硅晶圓和硅晶圓的區(qū)別是什么
用于薄晶圓加工的臨時(shí)鍵合膠
芯碁微裝推出WA 8晶圓對(duì)準(zhǔn)機(jī)與WB 8晶圓鍵合機(jī)助力半導(dǎo)體加工
晶圓鍵合及后續(xù)工藝流程
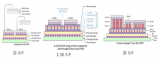
評(píng)論