控制外延層的摻雜類型和濃度對 SiC 功率器件的性能至關重要,它直接決定了后續器件的比導通電阻,阻斷電壓等重要的電學參數。
由Larkin等人發現的“競位外延”方法[1],可以有效地大范圍改變N型和P型的摻雜濃度,被廣泛應用在了實際生產中。我們這里分別以氮(N)和鋁(Al)作為N型和P型的摻雜元素來簡單說明它的原理。在外延生長過程中氮(N)原子和碳(C)原子競爭格點位置,如果想減少氮(N)原子的摻雜濃度,可以提高外延氣源中的碳(C)原子濃度;與之相反,降低外延氣源中的碳(C)原子濃度可以提高氮(N)原子的摻雜濃度。
而鋁(Al)原子是和硅(Si)原子競爭格點位置,如果想減少鋁(Al)原子的摻雜濃度,可以提高外延氣源中的硅(Si)原子濃度;與之相反,降低外延氣源中的硅(Si)原子濃度可以提高鋁(Al)原子的摻雜濃度。外延生長中,Si源的常用氣源是SiCl4或者SiH4;C源的常用氣源是CCl4或者C3H8,我們可以控制二者的流量比例來控制C/Si組分比例,進而有效地控制不同元素的摻雜濃度。
外延層的摻雜濃度除了與氣源中的C /Si組分比例有關以外,還和CVD工藝中的氣源流量、氣體壓強和生長溫度有關。我們以最常見的氮(N)摻雜為例來進一步說明。通過在CVD生長過程中引入氮氣(N2)能快速地實現氮(N)摻雜。圖1所示為外延溫度1550℃下,4H-SiC外延中的氮(N)摻雜濃度和氮氣(N2)流量的關系圖[2]。我們可以看到在固定的C/Si組分比例下,無論是Si面還是C面的摻雜濃度在四個數量級內都和氮氣(N2)流量成正比例關系。摻雜濃度涵蓋了器件中最常用e14—e18的摻雜范圍。
圖1. 4H-SiC氮(N)摻雜濃度與氮氣(N2)流量關系
U. Forsberg等人[3]也研究了CVD腔內氣體壓強和摻雜濃度的關系。外延溫度在1600℃,C/Si比例為3.5,氮氣流量為12ml/min條件下, N元素濃度和壓強的關系見圖2。無論4H-SiC的C面或Si面外延,摻雜濃度隨著壓強的升高而變大。
圖2. N元素摻雜濃度和氣體壓強的關系
摻雜濃度和生長溫度的關系更為復雜,這里還是以4H-SiC外延中氮(N)摻雜為例。在其他工藝參數保持不變的情況下,溫度的升高會增加Si面的摻雜濃度,但是同時會降低C面的摻雜濃度。伴隨著溫度的升高,因為襯底的N摻雜高于外延層,有可能襯底的N元素會擴散到外延層,改變了外延層和襯底的電學特性;同時溫度的升高也會提升外延速率,引起厚度橫向分布不均。所以溫度的設定要根據多種因素來考慮。
P型外延的摻雜使用的氣源為三甲基鋁(TMA: Al(CH3)3)。和N型摻雜類似,它的摻雜濃度也受到C/Si組分比,氣源流量,氣體壓強和工藝溫度的影響,這里不做具體說明。實際生產中,4H-SiC外延中常用的摻雜元素有:N型摻雜,氮(N)和磷(P); P型摻雜,鋁(Al),硼(B)和鎵(Ga)。在4H-SiC中,Si/C原子有兩種晶格格點,分別為六方格點和立方格點。由于格點效應,對于同種元素,替換不同格點處的原子的電離能也是不同的。這些元素具體的電離能和溶解度極限見表1。鎵(Ga)元素的電離能的理論計算值為329mev[4]。
氮(N) | 磷(P) | 鋁(Al) | 硼(B) | |
六方/立方 電離能(mev) | 61/126 | 60/120 | 198/201 | 280/280 |
溶解度極限(cm-3) | 2*1020 | 1*1021 | 1*1021 | 2*1019 |
表1. 4H-SiC中常見摻雜元素的電離能和溶解度極限
對于N型摻雜,氮(N)元素和P(磷)元素有著接近的電離能和溶解極限,都可以用作摻雜雜質。但是Rongjun Wang等人研究發現[5],磷 (P)元素的“競位外延”效應不明顯,它的摻雜濃度改變對C/Si組分的變化不敏感。比起氮(N)元素,P(磷)元素更難實現較高的摻雜濃度,所以目前大規模生產中主要使用氮(N)作為N型摻雜元素。 對于P型摻雜,理論上鋁(Al),硼(B)和鎵(Ga)元素都可以作為摻雜雜質。但是考慮到鎵(Ga)元素的329 mev電離能,一般不考慮該元素。鋁(Al)的電離能比硼(B)要小,同時考慮到B元素會在后續的高溫工藝中異常擴散散問題,所以鋁(Al)是P型摻雜最理想的摻雜元素。
圖3. 4H-SiC中N元素的電離率隨溫度的關系
圖4. 4H-SiC中Al元素的電離率隨溫度的關系
圖3和4分別給出了4H-SiC中N元素和Al元素的電離率隨溫度的變化關系。因為Al元素較高的電離能,它的電離率低于N元素,但是它們的電離率都隨著溫度的升高而變大。室溫下當摻雜濃度小于e16時候,N元素幾乎完全電離,這時候我們可以認為它的施主濃度等于載流子濃度。 綜上所述,外延層的摻雜濃度受C/Si組分比,氣源流量,氣體壓強和工藝溫度的多重影響,所以對外延工藝后的摻雜濃度的監控十分必要。二次離子質譜分析(SIMS)和擴散電阻探針技術(SRP),都可以用來測量外延摻雜濃度/載流子濃度隨深度的變化。
SIMS能測試的最小元素濃度為1014/cm3,設備的橫向空間分辨率為1微米量級,縱向的深度分辨率為10nm量級,適合測量外延層中摻雜濃度隨深度的變化。但是SIMS做為一種破壞性地測試方法,在濺射后會在樣品表面留下隕石坑的破壞,而無法重復或者進行其他測試。此外SIMS測試的是元素濃度分布,與該元素是否被電離無關。SiC中雜質元素的電離能普遍比較高,比如鋁(Al)在室溫下部分電離,所以SIMS濃度分布無法完全表征外延層的電學特性。下面介紹的SRP技術測試的就是電離后的雜質對電阻的影響,更能直接反應出外延摻雜的電學特性。
SRP的測試原理如圖5所示。待測試樣品通過小角度地機械研磨形成了一個斜面,兩個對齊的探針跨在x方向上做步進移動,并同時做電阻測試。假定X方向步進為 Δx ,則縱向的步進 Δz = sinα·Δx ,其中 α 為研磨角。通過不同的研磨角和步進相互匹配,則z軸的縱向深度精度可以得到納米級別。因為兩探針是做直接接觸的電阻測試,所以它的電阻測試范圍很廣,在100 Ω 到1011 Ω范圍[6]。
圖5. SRP測試原理
SRP技術的缺點是樣品制備的復雜性。首先要保證研磨表面有足夠的粗糙度,對注入的載流子有較高的復合速率,降低測試中注入載流子對電阻的影響;同時研磨的角度涉及縱向深度的表征,所以在研磨斜面后要進行準確的測試研磨角度。SEMILAB公司為了解決該問題推出了SRP-2100i設備,它內置了樣品的研磨角裝置和自動對齊樣品放置的視覺系統,提供了前所未有的自動化水平,使數據更易于獲取減少了對操作者的依賴。此外SRP-2100i還引入了PCIV技術來克服4H-SiC的高肖特基勢壘的問題。圖6為SRP-2100i測試4H-SiC外延層的曲線,可以看出該外延層是由兩部分組成:頂部大約為1.5um的高摻雜外延層,下部為10.498um的低摻雜外延層。如果使用了已知電阻率的4H-SiC校準樣品,經過校準后SRP-2100i也能自動計算出該樣品的電阻率隨深度變化的曲線。
圖6. SRP-2100i測試得到4H-SiC外延層電阻隨深度的變化曲線
因為SiC外延片成本很高,而且摻雜濃度受多個工藝參數的影響,所以實際生產中要求所有外延片進行摻雜濃度測試。而SIMS和SRP都是破壞性測試,無法滿足這種測試需求,現在工廠端使用的是電壓-電容法(C-V)測試技術。C-V技術的基本物理原理是:外延層的空間電荷區的寬度取決于外部的反向電壓,而該寬度又和它的電容成反比,通過測試該電容值和反向電壓值,就可以計算出外延層內的摻雜濃度。通過改變反向的電壓大小,就能計算出摻雜濃度隨深度的變化關系。 汞探針C-V(MCV)可以快速地和外延層形成肖特基接觸,而且也不會破壞外延層的表面,成為了檢測摻雜濃度的最快速有效的辦法。市場占有率最高的為SEMILAB公司MCV-530,圖7為該設備測試的外延片不同位置摻雜濃度隨深度分布,對于多點測試還可以生成Mapping圖來方便查看摻雜濃度在外延片上的橫向分布。
圖7. SEMILAB公司MCV-530測試的摻雜濃度分布圖
MCV測量中的汞殘留,可以通過多種清洗工藝將表面恢復到低于5x1010/cm2的水平,不會影響后續的器件工藝。但是為了避免該清洗工藝,并考慮到汞使用的安全問題,SEMILAB公司又開發出了一種電荷式非接觸式CV測量設備CnCV-230。它的測試原理圖見圖8(a),測試探頭主要有左側的電暈槍和右側的開爾文探頭組成。電暈槍精準的放置已知劑量的電荷到SiC外延層表面,形成空間耗盡層;表面電勢通過右側的非接觸開爾文探頭精確測量。非接觸的測試方法可以解決MCV汞殘留問題,CnCV和MCV的量測相關性見圖8(b),在E15-E18摻雜范圍內有非常好的一次線性關系。在不改變監控基準線情況下,兩種檢測技術可以在外延工廠內相互替代。
圖8. (a)SEMILAB公司CnCV-230測試原理圖 (b) SEMILAB公司MCV和CnCV量測相關性
原文標題:SiC外延工藝的摻雜以及監測
文章出處:【微信公眾號:旺材芯片】歡迎添加關注!文章轉載請注明出處。
審核編輯:湯梓紅
-
工藝
+關注
關注
4文章
593瀏覽量
28794 -
功率器件
+關注
關注
41文章
1770瀏覽量
90442 -
SiC
+關注
關注
29文章
2814瀏覽量
62650
原文標題:SiC外延工藝的摻雜以及監測
文章出處:【微信號:wc_ysj,微信公眾號:旺材芯片】歡迎添加關注!文章轉載請注明出處。
發布評論請先 登錄
相關推薦
淺析SiC功率器件SiC SBD
SiC功率器件SiC-MOSFET的特點
SiC MOSFET的器件演變與技術優勢
國產CVD設備在4H-SiC襯底上的同質外延實驗
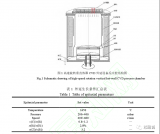
評論