引言
利用現有的超臨界二氧化碳進行蝕刻和干燥的工藝由兩階段工藝組成:在高壓干燥器外部利用溶劑對晶片進行蝕刻,然后移動到高壓干燥器,利用超臨界二氧化碳進行清洗和干燥。利用該工藝在本研究中進行了試驗,結果證實,無粘可蝕刻、清洗和干燥,但反復試驗結果證實,重現性差。這是因為外部蝕刻后移動到烘干機時,蝕刻用溶劑汽化,結構粘著的問題發生了。本研究旨在改善這一問題,不移動晶片,而是在高壓干燥器內利用超臨界二氧化碳,連續執行微電子啟示系統晶片的蝕刻、清洗和干燥工藝。此外,還想探討在執行連續工藝時,蝕刻工藝中使用的二氧化碳狀態(氣體、液體、超臨界狀態)的影響。利用氣體二氧化碳冷卻的情況下,可以無粘蝕、清洗和干燥,通過反復實驗確認了工藝的優化和再現性。另外,通過現有的第二階段,與這一淘汰過程相比,可以減少清洗用溶劑的量。利用液體二氧化碳進行蝕刻的情況下,液體二氧化碳和蝕刻用共溶劑(丙酮)之間發生了層分離,沒有形成完整的蝕刻。使用超臨界二氧化炭牛進行蝕刻7.5兆帕,40攝氏度)的情況下,可以無粘地進行蝕刻、清洗和干燥,與傳統的第二階段工藝相比,不僅節省了清洗用溶劑,還可以與使用氣體二氧化碳的連續工藝相比,縮短工藝時間。
介紹
微電子啟示系統(微機電系統,MEMS)技術利用在一個硅片上有微尺寸的數萬個結構(結構),實現了傳統半導體技術無法實現的超精細結構,并實現了現有半導體微體系結構。
但是,由于微電子啟示系統的超精細化、超高密度化,現有的濕半導體工藝在清洗過程中使用的超純、化學溶劑難以滲透,清洗效率下降,圖1等蝕刻、清洗過程中溶劑的表面張力和干燥過程中,清洗液從液體變為氣體,結構之間的毛細管力(毛細管)另外,現有的濕法半導體工藝技術中使用的昂貴的純化學溶劑會引起環境污染、廢水處理等環境問題。
為了彌補上述現有濕半導體工藝的缺點,開發了使用等離子體(血漿)激光(激光)氣溶膠(氣溶膠)和臭氧的干清洗技術,但如果單獨使用干清洗法,則不能進行完美的清洗,必須與現有的濕清洗工藝并行進行,缺點是破壞了半導體的結構。
由此產生的新的替代方法研究了利用超臨界流體的干法工藝技術,結果表明,美國洛斯阿拉莫斯國家實驗室(NAML此后,國內外進行了大量研究,開發了利用超臨界流體的微電子機械系統干法工藝技術,但僅限于對蝕刻、清潔、干燥工藝各角度的工藝和設備進行技術開發,還未達到商業化。在國內,對利用超臨界二氧化碳進行微電子機械系統干洗的研究進行了嘗試韓[10]的房間方法是:在與高壓干燥裝置分離的設備上用丙酮蝕刻微電子機械系統晶片后,將蝕刻晶片注入高壓干燥器內清洗和干了。清洗液使用甲醇,該清洗液在高壓干燥器內以液體二氧化碳取代,升溫制成超臨界二氧化碳后,在一定溫度下降低壓力的同時,慢慢推出船,完成了干燥過程。也就是說,用單獨的裝置進行蝕刻后,在高壓干燥器內進行清洗、干燥過程的第二階段工序。通過上述過程、MEMS晶片可以不粘地干燥,但從外部蝕刻后移動到烘干機中,丙酮會汽化,在清洗和干燥之前有可能發生晶片的粘著。這預計在實際商業化時,生產穩定性和自動化將面臨困難。
本研究試圖改進現有的由兩個階段(外部蝕刻后高壓干燥器中清洗、干燥)組成的工藝,在不移動晶片的情況下連續進行蝕刻、清洗、干燥,以解決這一問題。另外,想了解連續工藝執行時,在蝕刻工藝中使用的二氧化碳的物態(氣體、液體、超臨界狀態)的影響。
結果和考察
4-1。外部蝕刻現有兩階段工序
從外部可以確認,蝕刻后在烘干機內干燥的第二階段工序可以不粘地進行蝕刻、干燥,但總共8次
實驗結果表明,圖6(a)、(B)等沒有粘著的情況下,只能進行一次蝕刻、干燥的實驗,其余七次實驗中,圖6(c)、(D)等蝕刻、干燥后發生粘著,結構遭到破壞。
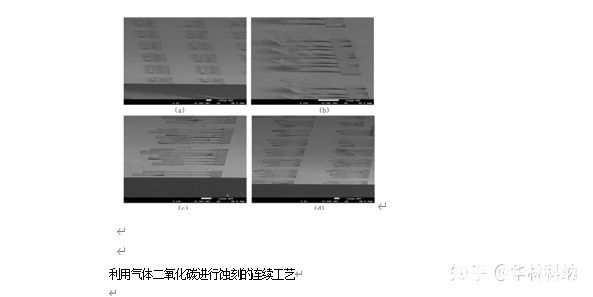
在沒有晶片移動的情況下,在干燥器內利用氣體二氧化碳進行蝕刻后,利用液體二氧化碳進行清洗后利用超臨界二氧化碳進行干燥的案例2連續工藝的情況下,如預期的那樣,可以在不粘著的情況下進行蝕刻、干燥。晶片邊緣的毀壞的結構物是在晶片切割過程中受損的情況106 .案例2的實驗后,掃描電鏡圖像出現在圖7上。
通過大量實驗,可以建立表5等優化工藝,共進行了14次實驗,確認了優化工藝的再現性。
另外,工藝的優化結果是,現有第二階段的蝕刻、干燥過程中使用了680毫升甲醇(烘干機體積的100%),連續過程中甲醇用量減少到150毫升(烘干機體積的22%)。
這是現有的第二階段蝕刻、干燥過程中,為了防止蝕刻后丙酮蒸發導致晶片結構的粘著,用甲醇填充干燥器內部,防止去除犧牲層的結構和晶片基板之間的粘著。
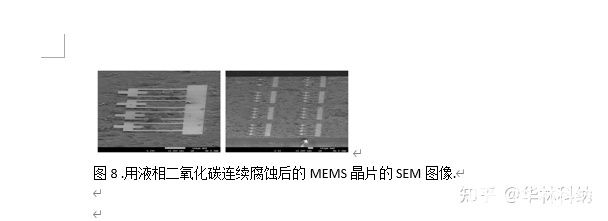
但是,在連續工藝中,在沒有晶片移動的情況下,在蝕刻、清潔工藝中,烘干機內部使用二氧化碳,使其處于高壓狀態(5.5兆帕),防止結構與晶片基板之間的粘著,從而減少甲醇的使用量。
4-3。利用液態二氧化碳進行蝕刻的連續工藝
在沒有晶片移動的情況下,在干燥器內利用液體二氧化碳進行蝕刻后利用液體二氧化碳進行清洗后利用超臨界二氧化碳進行干燥的案例3的連續工序,如圖8,完全沒有進行蝕刻,部分進行了。
這是二氧化碳本身非極性,與極性丙酮不能很好地混合在一起,導致層分離、MEMS晶片和丙酮之間沒有發生足夠的接觸,因此被認為沒有完全形成口感。
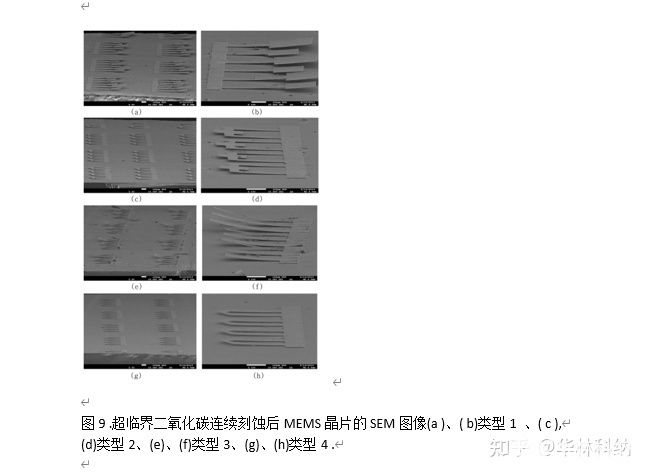
4-4。利用超臨界二氧化碳冷卻的連續工藝
在沒有晶片移動的情況下,在烘干機內使用超臨界二氧化碳的蝕刻、清潔和干燥案例4的連續工藝中,可以進行無粘蝕、干燥,如圖9,通過大量實驗,可以建立表7等優化工藝,并確認了優化工藝的再現性。
與使用氣體二氧化碳的連續工藝(案例2)一樣,與傳統的第二階段蝕刻、干燥工藝相比,甲醇的使用量可以減少530毫升(占槍早期體積的78%),所有工藝都使用超臨界離散化碳,因此烘干機始終保持在高溫狀態(35~40攝氏度),冷卻烘干機所需的攝氏35度至40度.
結論
為了改善現有超臨界二氧化碳的第二階段蝕刻、干燥工藝中蝕刻后晶片移動過程中出現的粘著問題,研究了利用超臨界二氧化碳的蝕刻、清洗、干燥連續工藝。
在本研究之前,使用現有超臨界二氧化碳進行了第二階段的蝕刻、干燥過程(案例1),結果是無粘蝕、干燥,但在總共8次實驗中,只有一次可以無粘干燥,這是由于晶片從外部蝕刻后進入干燥器的過程中丙酮蒸發所致,從而確認了晶片無移動的蝕刻、清潔、干燥連續過程的必要性。
本研究以蝕刻、清潔、干燥連續工藝為例,根據蝕刻、清潔工藝中使用的二氧化碳的狀態,分為3種情況(氣體、液體、超臨界狀態)進行。
使用氣體二氧化碳進行蝕刻后使用液體二氧化碳進行清洗的工藝(案例2)可以進行無粘性的蝕刻、清洗、干燥,通過大量實驗優化了工藝,在優化的工藝組份中共進行了14次實驗,確認了再現性,與傳統的第二階段蝕刻、干燥工藝相比,可以減少使用的甲醇量。使用液體二氧化碳的蝕刻、清潔工藝(案例3)的情況下,由于液體二氧化碳和蝕刻用共溶劑丙酮之間的層分離,沒有實現完全的蝕刻。通過這種方式,可以調整烘干機內晶片的安裝高度,或者代替液體二氧化碳,實現氣體或超臨界離散化。
確認了使用碳調節密度的必要性。
在蝕刻、清潔、干燥的所有工序中,使用超臨界二氧化碳的連續工序(案例4)可以進行無粘蝕、干燥,很多通過實驗優化工藝后,在優化的工藝條件下確認了再現性,與傳統的第二階段蝕刻、干燥工藝相比,可以減少使用甲醇的量,減少烘干機冷卻時所需的30~60分鐘,升溫時所需的20~50分鐘的工藝時間。
通過這一點,從蝕刻、干燥后晶片結構的粘著問題、使用的溶劑量、工藝時間方面確認了在蝕刻、清潔、干燥所有工藝中使用超臨界二氧化碳的工藝是有效的。
審核編輯:符乾江
-
微機電系統
+關注
關注
2文章
131瀏覽量
23799 -
二氧化碳
+關注
關注
0文章
154瀏覽量
16604
發布評論請先 登錄
相關推薦
基于51單片機的二氧化碳濃度檢測報警系統仿真
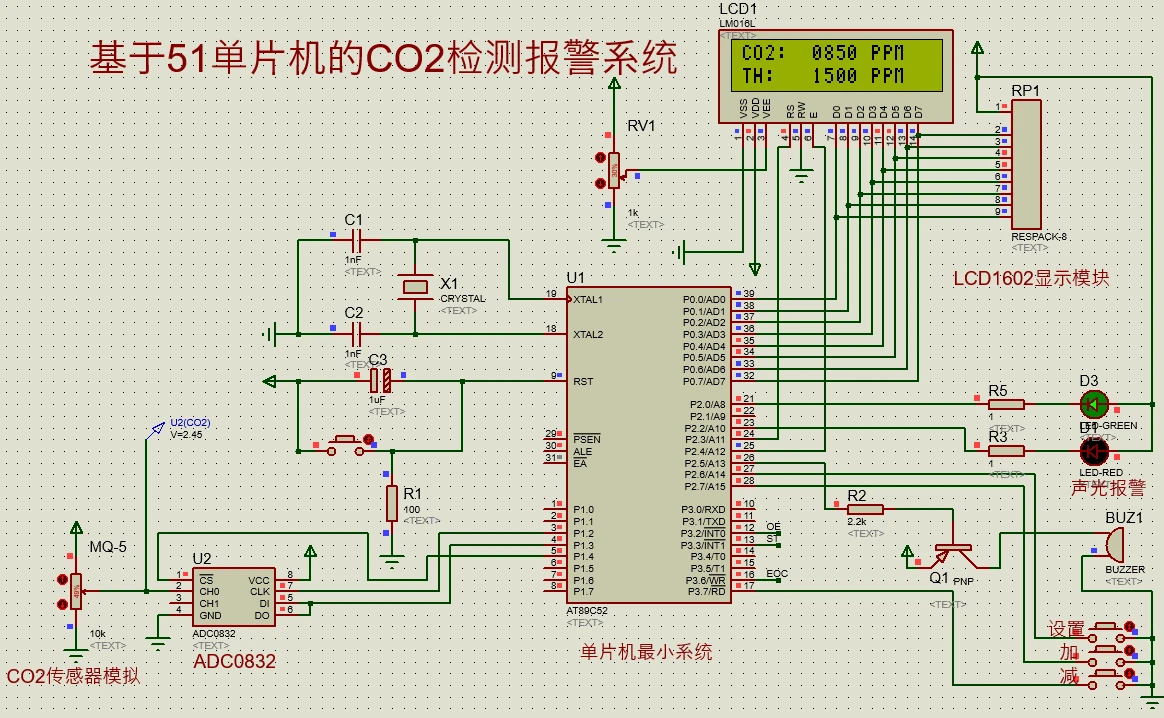
基于51單片機的二氧化碳濃度檢測調節系統仿真
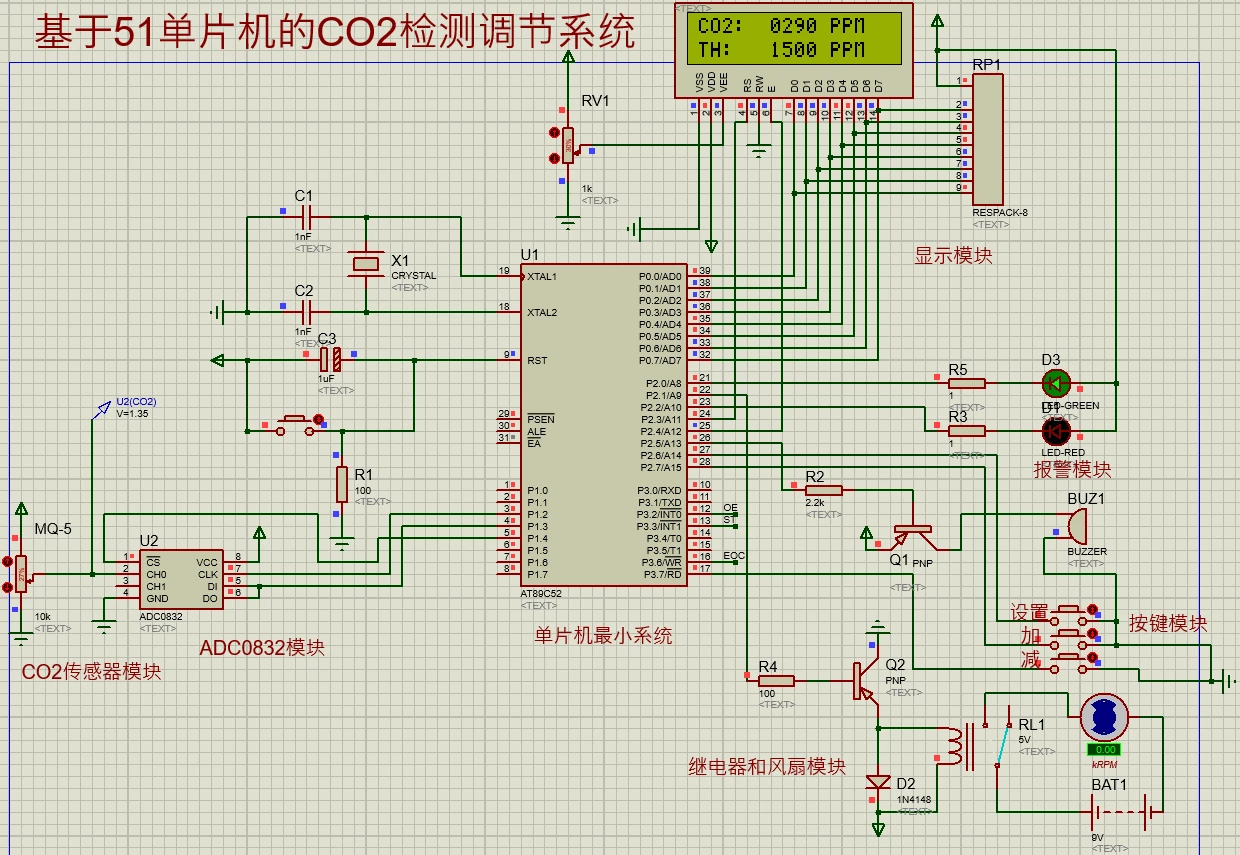
我國首座超臨界二氧化碳光熱發電機組項目圓滿驗收
二氧化碳氣體5g網絡監測面包棚
溫室大棚二氧化碳監測的優勢
二氧化碳儲能的原理 二氧化碳儲能的應用
壓縮空氣儲能和二氧化碳儲能的區別
尺寸雖小、潛力無限:Sensirion推出創新性微型二氧化碳傳感器
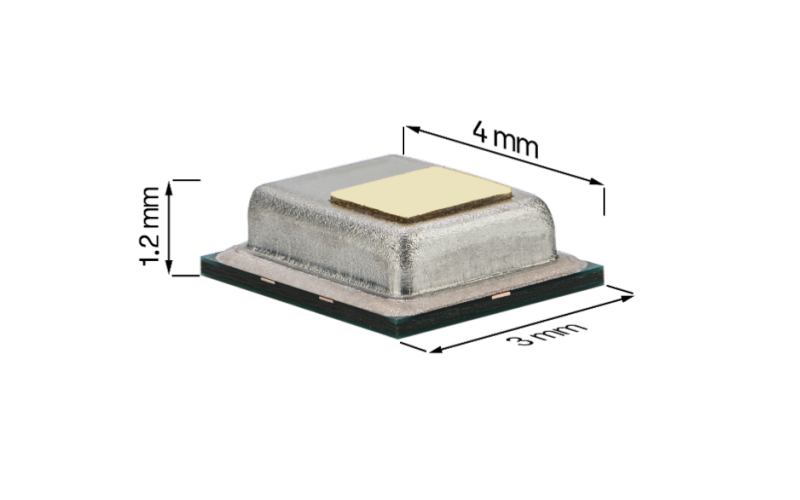
二氧化碳傳感器的分類及其原理
二氧化碳雪清洗技術在芯片制造中的關鍵突破
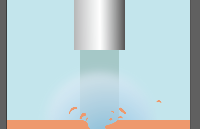
二氧化碳氣體保護焊怎么調電流電壓
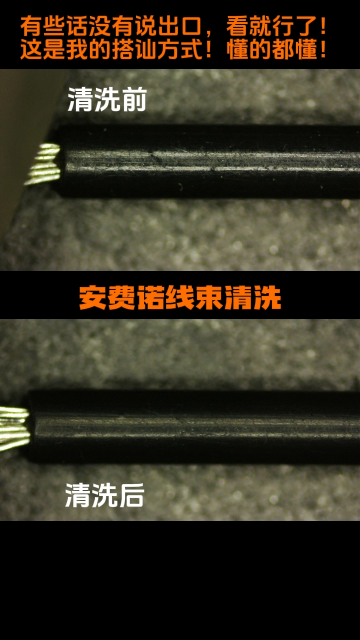
評論