導讀:隨著物聯網、大數據、人工智能等技術的發展,新一代信息技術與制造業正在深度融合,人們與物理世界的交互方式正在發生轉折性的變化。數字化轉型,正在成為企業的重要戰略,而數字孿生,則成為全新焦點。本文通過對數字孿生在工廠中的實際應用,為企業數字化轉型提供了一套落地可行的方法。
引言
工業企業的數字化轉型,需要面臨制造理念、組織方式和商業模式的多種變革。一個產品,從設計理念開始,經歷了制造、使用和報廢,跨越了時空,呈現出一個完整的生命周期。如果設想這種產品有一本履歷表,那么它將忠實地記錄了這個產品的各階段生命周期相關的數據。各種健康狀況和風險,都會一目了然,然而事實卻并非如此。對于制造商而言,各階段的數據通常呈現孤立、分散的特征,尤其是用戶對于產品使用過程中,基本就是黑匣子。數據的分裂,讓產品的各個階段,都成為一座座孤島而互不相連,數據失去了流動性,大大約束了人們的洞察力。
數字孿生,作為連接實體與數字空間的一種高保真、實時互動的可視化模型,隨著工業互聯網的發展,成為一種全新而有效的解決方案。工廠的設備,可以通過實時可視化的數字孿生,模擬機器在生產系統中的表現,通過虛實交互、數物融合和知識自動化,形成一線操作者和管理者的決策支撐系統,提供更加實時、高效、智能的服務[1]。
一、研究背景
企業數字化轉型,圍繞著數據驅動而來。而數據要真正產生的價值,需要靠企業知識體系來提供。因此,數字化轉型,首先需要面對的是企業知識的梳理。但是傳統的知識體系,往往呈現非常僵化的狀態。例如,工程圖檔往往是企業的重要知識資產,但很多制造企業都是采用傳統的圖紙檔案管理方式,以“底圖”或“藍圖”的形式,進行分類、分密級歸檔保存。而代表企業重要的知識體系,如工藝說明、操作手冊、工程文件等,已經隨著企業信息化應用的逐步發展,一般都是通過掃描后進行管理。
然而這些圖紙、電子文檔所保存的知識,都是靜態、分散和割裂的。顆粒度太大,缺乏語義的連接,無法實現相互之間的關聯,流動性很差。這種知識體系,只是被收藏起來,但卻無法高效重復使用。對于資深工程師而言,這只是一種儲存方式而已,因為信息查找而言,仍然非常低效;而對于經驗不足的員工而言,這些知識則像是被隱藏起來。
面臨數字化轉型,由于缺乏系統性的知識體系支撐,因此工業企業呈現出如下的困境:
1)工業場景復雜,存在海量多源異構的工業數據,多樣性、復雜性的工業數據,造成工業場景信息孤島化,數據利用價值低。
2)工業場景中,存在顯性知識與隱性知識,各種結構化、半結構化和非結構化知識,知識關聯性弱。
3)人工智能(AI)正在逐漸成為大數據分析的重要技術,但是傳統AI訓練,過度依賴人工開發算法。它無法關聯自然語言所對應的概念、屬性、關聯性等。
4)隨著工業數字化普及,海量的CAD、CAE文件以及數字化的各類文檔、說明書、操作手冊等,信息量暴增,給用戶決策帶來新的痛點。
5)工業知識專業性強,且涉及技術領域廣。零散化的知識晦澀難懂,工業術語解釋專業性強,經驗知識傳播、傳承困難。
而通過知識圖譜,可以將各種概念,通過編碼連接的方式,形成語義連接,將隱形的知識顯性化;而數字孿生技術,則可以在傳統靜態模型中,增加了實時運行數據的反饋,動態記錄,并且用可視化的方式進行展現。這將徹底改變原有的知識管理方式,激活沉默的知識資產,從而幫助人們重新認識、管理和控制機器世界。
二、構建數字孿生的方法論
構建機器數字孿生,不僅僅是信息組織和表現形式的圖形化,更在于構建過程中,是將企業的知識體系貫穿其中,信息上下游之間的背景鏈路清晰明了。而在構建數字孿生的過程中,可以采用“雙模數字孿生”的方式,就是將幾何模型和和機理模型相互嵌套。結合不同的設計、制造和運維的階段,知識體系嵌入其中,最終在使用的時候,就可以實現知識自動化。
01建立物理幾何模型,對應物理實體
構建物理幾何模型,首先是從零配件開始。例如,一臺煙草包裝機,有1.5萬個零件,需要一一建模,并且建立設備零部件庫。這些零部件庫的最小單位為零件級別,如螺絲、螺母。主要數據獲取方式,包括從CAD軟件、數據表以及現場測繪開始,構建實體等比的數字化模型。
02建立機理模型,對應運行軌跡
機理模型,就是要將幾何空間的零部件,跟控制系統的機器動作進行匹配。機器的真實運動軌跡,在幾何模型都有對應描述作。這其中,都是通過數據標簽,來標識零部件的狀態,并且跟控制邏輯相對應。例如,薄膜紙會剔除那些無法包裝的煙支和煙包。而煙支無法包裝的原因會有幾十種:薄膜褶皺、煙支重量不夠、圓周不夠圓、空投、漏氣、重量等。需要深入了解這些機理,然后將其做成模型和算法,并與幾何模型相對應。
03三類知識模型的構建
第一種是設計類。要設備的設計資料出發,運用數字孿生技術,全面刻畫設備的物理屬性,實現虛擬設備對物理設備的真實映射,最終完成對物理設備的完全鏡像。
第二類是制造知識模型的構建。運用數字孿生技術全面的刻畫設備與產品之間的屬性,實現虛擬設備與物理設備的數字模型真實映射。制造階段所涉及的知識按其特性可分為三類:
(1)基礎知識:為裝備制造企業核心數據,企業組織結構、崗位、工種、人員、存貨檔案、固資編碼、供應商等信息。
(2)生產管理知識:如生產計劃、產品指標、原材料清單、績效考核指標等。
(3)設備知識:如供應商、規格型號、操作說明、操作規程等。
第三類是運維知識模型的構建。基于設備服務知識模型,在采集的實時數據、歷史數據及領域知識等,共同實現設備的多維數字孿生模型構建。建立各種故障代碼、維修對策庫,并且提前通過虛擬模型,進行仿真驗證,從而實現對機器狀態檢測、故障預測以及維修策略建議等功能。
以上三種知識模型的建立,都離不開一套表達各種物品之間關系的知識圖譜,這是構建在行業規則之上的編碼體系,具有很強的支撐作用,能夠快速建立知識模型,并且用可視化的方式,將背后的知識體系表達出來。
三、數字孿生提升現場員工能力
在知識體系的基礎上,構建了高保真的數字孿生,就可以在現場,提高員工的判斷力,從而提升工廠的運營效率。
01化簡為繁,輕松看透機器的奧秘
機器作為工業生產的必備工具,可視化管理是工業數字化轉型必經階段。而數字孿生,則更勝一籌,不僅僅讓使用者對設備有形象具體的圖形理解,對設備現實的狀況及所有參數數據等信息一目了然,而且以非常體系化的方式,引導用戶輕松使用機器。
設備數字孿生,可以將一臺機器以3D的形式,展示設備整機、部套、零件之間的層次關系。用戶可以借助于導航樹,在煙機的不同零部件之間進行自由切換,深度了解。數字孿生會呈現出拆分動畫,逐級遞進,用戶可以直接與場景中的3D對象進行交互,用層層“爆炸圖”的方式,查看機械零件、子部件的詳細信息。
圖1:機械結構層層分解圖
設備的元器件、油路、氣路等,都是等比例建模,攜帶各種屬性信息。設備數字孿生,就像為操作者提供了一臺CT機,看到機器的各種結構和屬性,從而對機器有著深刻的了解。
02聰明機器傻瓜式操作:“虛擬專家”在線培訓
基于數字孿生技術創造出來的3D互動模擬的在線培訓系統,可以實現現實與虛擬仿真的統一。它突破了“分別翻看圖紙說明書“的傳統培訓模式的限制,而是直接“在線手把手”。各種不同的操作規范、說明手冊等,都被統一集成到一個界面上,每一步行動都有說明和提示。在大大縮短培訓周期的同時,豐富了培訓內容,并減少了現場實訓的成本損耗和危險性。以前一臺進口的高端煙草機械,即使是成熟的工人,完全掌握一臺機器,需要用兩三年。而現在生手工人,只需要3-6個月就可以完全上手,大大減少了對熟練工人的依賴性。
圖2:虛擬專家引導操作培訓
03提升設備運行效率,實現自適應
傳統設備管理工作中,設備監管、設備控制、設備維護、庫存管理等各個業務模塊之間數據不互通互聯,存在信息孤島。同時還存在設備管理效率較低、設備維護成本高等問題。而基于數字孿生的設備管理應用,能夠讓現場發生故障的時候,不僅僅是知其然,而且知其所以然。
例如機器如果發生停機故障,傳統方式需要統治維修人員,然后去現場排查,排查往往又需要半天時間,找到故障原因。機器非計劃停產,會給企業帶來很大的損失。但這種現象,在車間里非常普遍。
而通過機器數字孿生,就可以在車間的任何一臺人機界面上,直接就可以看到什么位置、何種部件、發生了何種故障。如圖3中所示意。
圖3:設備數字孿生自動完成故障報警及診斷
這種基于設備服務知識模型,能夠對設備狀態進行評估,準確預警,從而幫助優化設備檢測、維修計劃安排和人力資源分配,大大提高了設備的運行效率與可靠度。
這種應用,也可以在云平臺上,對多個系統實時遠程管理,并且可以細化到產線級、設備級、零部件級的運行狀態,了解設備故障問題嚴重程度、故障描述、處理方法等
而下一步,設備數字孿生將進一步推動智能機器的進化,實現自適應的機器控制。根據故障情況,可以直接反向去控制機器。
結束語
從圖紙到零件,從制造商到最終客戶,從決策者到管理者再到操作者,數字孿生的應用貫穿在整個設備的全生命周期之中。而知識作為指導人和機器學習及做事的指令集合和規則體系[4],為高保真、實時互動的數字孿生提供了核心支撐。通過數字孿生技術,實現工業知識模型化、模型軟件化、軟件云端協同化,推動業務流程與機器效率的提升,真正實現了知識自動化。
實際上,數字孿生的應用并不限于機器,往上它還有車間級、企業級和城市級。不同層次的數字孿生,對應不同的決策判斷,從而使得數字化轉型可以逐層切入。高保真、實時交互的數字化孿生,成為數字化轉型的重要支點。
審核編輯 :李倩
-
數字化
+關注
關注
8文章
8816瀏覽量
61983 -
工業互聯網
+關注
關注
28文章
4326瀏覽量
94185 -
數字孿生
+關注
關注
4文章
1341瀏覽量
12297
原文標題:數字孿生:企業數字化轉型的支點
文章出處:【微信號:IndustryIOT,微信公眾號:工業互聯網前線】歡迎添加關注!文章轉載請注明出處。
發布評論請先 登錄
相關推薦
數字孿生場景構建好處的詳細闡述
數字孿生:賦能多行業場景構建的創新應用
數字孿生技術實施中的挑戰
基于數字孿生的智慧城市
數字孿生場景構建行業應用和優勢
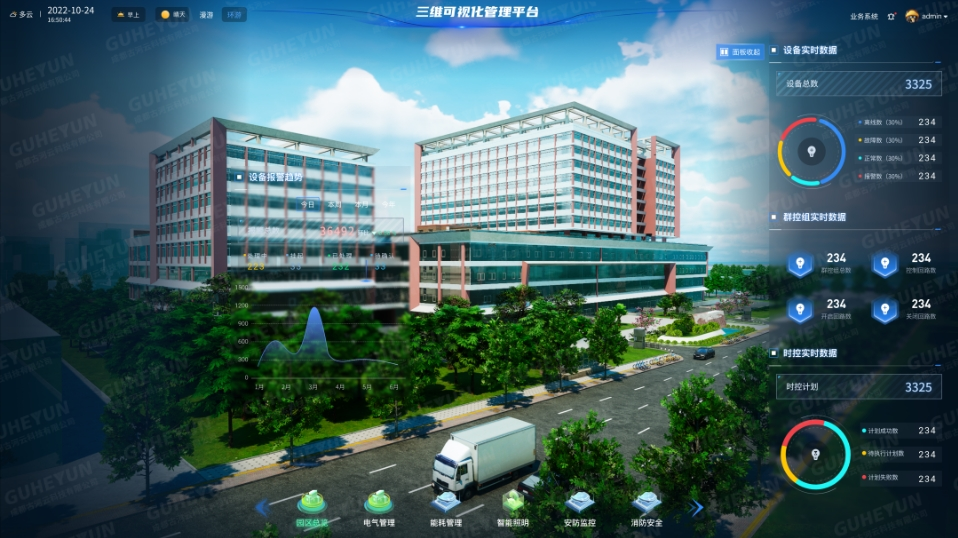
評論