汽車發展趨勢為線束開發帶來新的挑戰
摘要:
新技術的迅速引入以及汽車初創公司的蜂擁而入,導致線束開發面臨諸多挑戰。OEM 和初創公司都必須考慮它們集成到車輛中的技術特性數量和復雜度,因為它們對線束重量、線束直徑和成本都有直接的影響。電氣化、自動駕駛和駕駛員輔助、人工智能和連接功能,都會給線束帶來額外的負擔。
新技術的發展永無止境,當它們與現代車輛相結合,便會導致一種可稱為 “內容困境” 的現象。內容困境代表車輛制造商試圖整合到車輛中的技術內容與線束所需的重量、成本和封裝空間之間的沖突。
推動內容困境的最新技術趨勢示例包括(圖 1):
1
電氣化
2
自動駕駛
3
人工智能
4
互聯車輛
電動汽車領域的關鍵客戶競爭因素在于里程。車輛一次充電能夠行駛的里程越遠越好。車輛質量在決定車輛的行駛里程方面起著關鍵作用,因此,最大限度減小電動汽車的重量,對于能否面向市場推出具有競爭力的成功車輛至關重要。然而,新型車輛技術需要額外的電線和其他電子部件,從而增加了車輛的重量。與內燃機動力系相比,單單引入電動動力系統便增加了約 30% 的車身重量。
自動駕駛需要增加大量硬件冗余和故障安全機制,以防出現可能意外禁用自動駕駛系統的單點故障。系統冗余至關重要,因為如果駕駛員沒有注意到或主動參與駕駛和轉向過程,意外故障可能會導致車輛碰撞。但是,這些安全冗余也會大幅增加線束的重量和成本。
車輛中的人工智能能夠支持面部識別、計算機視覺和其他機器學習算法,通過處理和“學習”傳入的數據來幫助實現個性化的用戶體驗和車輛設置。這需要在整個車輛中包含無數的攝像頭和其他硬件。這些攝像頭往往通過同軸電纜或高速數據電纜連接到電子控制單元,與傳統的汽車布線相比,這些電纜更粗、更重且更昂貴。
最后一點但同樣重要的是,車輛作為物聯網和車聯網的一部分,逐漸變得高度互聯,從而將車輛轉變為我們在家和在工作中的互聯生活之間的無縫接口。將屏幕和顯示器集成到幾乎任何可以想象到的內表面,表明車輛作為娛樂、通信和生產力的樞紐,正在扮演著越來越重要的角色。
所有這些技術都必須連接到一起,導致線束的重量、直徑和成本不斷增加(圖 2)。一些現代車輛包含近 40 種不同的線束,由大約 700 個連接器和 3000 多根導線構成。如果拆開并拼接為一條連續的直線,這些電線的長度將會超過 2.5 英里(4 公里),重量約為 132 磅 (60 公斤)。此外,還可能有 70 多種專用電纜,如同軸電纜、高速數據電纜和 USB 電纜等。在老式汽車里,這一數字約為 10 種。
那么,今天的汽車制造商應如何化解內容困境呢?通過引入各種方法,幫助開發團隊減少增加的內容和技術給線束所需的重量、成本和封裝空間造成的影響。
一種解決方案是開發可減輕線束重量的技術。超小直徑布線 (0.13mm2) 就是一個很好的例子。不幸的是,行業至今仍難以為所有現有的端子開發出足夠數量的能夠壓接到如此小的布線直徑的端子替代物。當前市場上的可用產品無法支持大規模遷移到超小直徑布線。
鋁布線也面臨同樣的境況。對于小直徑布線而言,純鋁太脆,因此并非可行的選擇。端子供應商已紛紛著手開發適合其端子規格的最佳鋁合金。這導致市場上出現了各種合金,而且多數情況下,它們與其他供應商的端子互不兼容。反過來,這意味著車輛只有采用一家供應商的連接器,才能做到在整車上使用鋁,而這無異于癡人說夢。
另外,改用鋁布線需要壓縮鋁芯,以減小線束尺寸和重量。由于材料特性,鋁線直徑必須增加至不小于某個尺寸,才能保持與銅布線相同的導電性。在整車甚至在車輛的某個部分改用直徑更大的鋁線,將會導致線束尺寸大幅增加,并且需要更多的封裝空間。
找到特種電纜的替代品將會進一步降低線束重量和成本,并縮小線束直徑。未來的攝像頭和顯示器數量有增無減,因此開發通過標準化布線傳輸視頻和攝像頭信號的方法至關重要。或者,尋找方法將這些信號多路復用到一根共用的特種電纜上,并將多個設備接入這些電纜,也能產生同樣的效果,即降低線束重量和成本,并縮小線束直徑。
另一種方法是,使用Capital等先進的軟件解決方案,它們可支持權衡研究,優化模塊位置和識別任何可組合的模塊,以節省重量、成本,并縮小線束尺寸(圖 3)。這種方法能夠比較和分析布局對線束重量、成本和直徑的影響,因而可支持工程師選擇最優的系統架構。
圖3Capital 可利用成本、重量和線束尺寸指標進行權衡研究,從而優化線束設計.
汽車初創公司的涌現
在過去 10 到 15 年間,汽車行業在第二種趨勢的推動下悄然發生了一場革命,即汽車初創公司的激增。如今參與市場角逐的不僅僅是福特、大眾或豐田等老牌傳統 OEM 了。自 2003 年特斯拉成立以來,越來越多的電動車初創公司不斷涌入市場。隨之而來的還有它們獨有的一系列挑戰。
電動車領域的初創公司面臨獨特的挑戰,例如:
1
緊迫的上市時間
2
缺乏基礎設施
3
自下而上的設計
4
持續的變化
縮短產品上市時間會導致所謂的時間困境。老牌 OEM 開發新車型的周期約為 4 到 5 年。相比之下,大多數電動車初創公司往往將目標設定為在短得多的時間內發布車輛,有時甚至不到老牌 OEM 時間預算的一半。令這一困境雪上加霜的是,電動車初創制造商需要從頭開發,沒
有任何先前的車輛計劃可以繼承。上市時間短促導致迭代周期或開發階段也很緊張。
縮短迭代周期和開發階段本身并無大礙,但加上線束開發所需的較長交貨期,便會出現問題。從設計發布到產品交付,線束交貨期通常約為 23-26 周。交貨期的差異取決于項目在開發周期中執行的變更數量和進度。為了滿足下一個開發階段的截止期限,必須將線束凍結(此時數據/設計已經發布,必須通過正式的變更管理流程才能更新),導致兩個開發階段間只有極少甚至沒有任何時間來檢查或實施學到的經驗教訓。當下一次凍結來臨時,車輛測試往往甚至還沒開始。一旦下一個構建階段開始,這可能導致大量的返工工作,或在短時間內提出大量變更請求,以便在下一次凍結之前,盡快將變更實施到線束設計中。兩種替代方案都有可能導致線束質量下降,并在功能驗證期間導致不必要的延遲。
Capital 數字化流程
圖4:自動數據傳輸通過簡化領域之間的交互來減少線束設計中的錯誤。
縮短工程和制造階段的交貨期可令所有工程團隊獲益。更長的交貨期讓團隊有更多的時間來查找問題,確定適當的布線變更,并在設計中實施這些變更,以用于下一個驗證階段。那么如何才能縮短此交貨期?通過消除手動步驟,并自動將信息從一個步驟逐級傳遞到另一個步驟(圖4)。這將大幅減少錯誤,并降低核實工作結果的必要性。目標是在車輛制造商和供應商的工具鏈之間建立無縫的集成。
缺乏基礎設施
致力開發新型車輛的初創公司還必須應對缺乏業務和工程基礎設施的問題。初創公司的早期階段沒有適當的流程。具體而言,在布線開發方面,沒有任何有助于收集、組織和驗證線束設計所需電氣數據的設備傳輸數據庫。初創廠商也沒有經認證的連接器、端子、密封和其他附件的元件庫。在 OEM,這類基礎設施由來已久,并且經過了長期測試。而在初創公司,所有這一切都必須重起爐灶,在資源和時間有限的情況下需要投入大量的時間和精力。
隨著越來越多的初創公司進入市場,采用集成的設備傳輸數據庫和元件庫的開發工具將為布線團隊帶來長遠的優勢。它們無需通過 Excel 工作表收集繁瑣的數據,也無需通過容易出現人為錯誤的過程,將數據手動傳輸到邏輯原理圖中。線束開發工具將會簡化和自動執行該過程,從早期設計階段開始,減少錯誤并提高整體線束質量。
這類數據庫還可以運行自動報告,以獲得開路電路、缺少的負載等信息。實施元件庫后,將會大幅減少為尋找端子、密封或配對連接器的零件號而進行零件研究的需求。由于操作員的失誤或關于端視圖定義的錯誤信息而引起的連接器管腳錯誤是最常見的錯誤之一。元件庫將會提供每個零件號的端視圖,從而消除在為空腔指定管腳號時的猜測,并預防這類錯誤的出現。
設計差異
通常情況下,成熟的 OEM 采用自上而下的方法進行系統設計。在自上而下的方法中,系統被分解為子系統,這些子系統再進一步細分為部件。然后對每個部件進行定制設計,以支持特定的車輛特性并遵循特定的要求,例如,使用核準供應商提供的有限系列的連接器。
初創公司存在時間和預算限制,往往不允許采用自上而下的方法。相反,工程團隊會使用自下而上的車輛設計。工程團隊被指示使用最適合預期應用的現貨零件。之后,系統工程和布線團隊的任務是,嘗試將所有這些拼圖拼接到一起,構成車輛功能并建立連接。不幸的是,除非進行大筆投資,否則將無法更改或定制現貨零件。這通常會造成一些妥協,導致在線束中增加集成零件所需的布線。
此外,布線團隊無法獲得一些精選和核準的連接器系列,而是往往被迫采用各種類型的連接器,這些連接器可能缺乏 USCAR 認證、難以采購,或者質量和制造都不盡人意。理想的線束開發工具必須能夠支持自下而上的設計流程和多種連接器類型。
變更管理
在初始創建階段之后,布線工程師的大部分工作都與實施變更有關。希臘哲學家赫拉克利特斯說過:“一切都在變化,沒有什么是一成不變的”。這正是布線工程師的日常工作。線束設計和工程永遠存在變化。在初創公司,由于時間限制更為嚴格,所以普遍存在臨時流程和工程師新手。
幾乎每周都會有新的專家加入不同的部門,為團隊帶來新的見解。其中可能包括解決問題的更優方法,或者他們在以前的角色中所接觸或開發的新技術。這些新團隊成員很希望留下他們的印記,初創公司也亟需這樣的輸入。因此,這些想法可能會在很短的時間內得以實施,但卻很少考慮整體系統方面的影響。不僅如此,環境中僅僅部署很少的流程,變更規程仍處于起步階段。在這樣的環境中,變更很不統一,導致跟蹤最新的設計修訂難度極大。
相比之下,傳統 OEM 已經建立起高效、嚴謹的變更管理流程。這些流程經過多年的項目優化,具有很高的組織支持率。而在創業公司則不然。無論凍結日期或當前項目階段如何,總會持續產生變更請求。
此外,并非所有供應商都是從項目開始便確定不變,這也導致了反復出現的設計變更需求。某些零件的采購可能需要很長時間。作為權宜之計,工程師采用估算數據來滿足前幾個線束凍結日期的要求。完成供應商采購后,實際要求經常與工程師的假設不符,要讓零件正常工作便需要變更單。某些情況下,供應商無法滿足計劃時間,甚至決定終止參與。這就意味著必須重新采購零件。新零件很少精確符合原始零件的電氣規格。這又會導致更多修改線束的變更請求。
因此,在項目早期制定一種結構化和規范化的變更管理方法極為重要。同樣,先進的線束開發工具組合可以提供優雅的解決方案。前面討論的集成設備傳輸數據庫可以強化某些變更控制機制。利用這些增強功能,該數據庫可立即提供必要的結構和自動變更管理(圖 5)。
圖5現代線束設計解決方案包含自動變更管理解決方案。
設備的發布工程師可以直接在數據庫中起草設備傳輸并提交以供批準。獲得批準后,變更將在邏輯原理圖中自動更新。這便消除了從 Excel 文件手動更新原理圖這一極易出錯的過程。它還可以防止發布工程師對從其硬盤上找到的過時的本地副本執行更改,以及覆蓋自上次更新以來對設備傳輸所做的更改。最后,對于每組已發布的邏輯原理圖,將會在每個版本中實施自動生成的變更請求清單,從而將每項變更鏈回到特定的線束修訂,以供將來參考。
全新的挑戰需要全新的解決方案
新技術的迅速引入以及汽車初創公司的蜂擁而入,導致線束開發面臨諸多挑戰。OEM 和初創公司都必須考慮它們集成到車輛中的技術特性數量和復雜度,因為它們對線束重量、線束直徑和成本都有直接的影響。電氣化、自動駕駛和駕駛員輔助、人工智能和連接功能,都會給線束帶來額外的負擔。這些功能需要在車輛中引入數十個新傳感器,而且所有傳感器必須連接到線束,有時甚至需要使用特殊布線。
初創汽車公司在爭分奪秒地將產品推向市場時,面臨著更多的壓力。初創公司缺乏傳統設計的基礎以及為獲得最佳性能而定制設計零件所需的資源。沒有這些資源,這些公司的工程師必須采用自下而上的設計方法,這種情況下,需要調整現貨零件以滿足功能要求。初創公司還缺乏成熟的變更管理和跟蹤程序。雖然成熟的 OEM 擁有更成型的變更管理流程,但它們往往依賴于手動數據輸入和團隊之間的溝通。這會導致數據交換不僅低效,而且極易出錯。
現代線束設計和工程工具為汽車創新帶來的問題提供了優雅的解決方案。將Capital等工具與高水平的自動化、高級指標和分析功能相結合,工程師可以進行權衡研究,以優化材料、元件布局和布線,實現線束重量、成本和直徑的最小化。接下來,現代設計工具可以自動執行工程團隊之間甚至制造商和供應商之間的數據轉換。最后,創新的線束設計軟件套件具有集成的變更管理工具,可確保所有團隊使用最新數據。通過采用這些解決方案,老牌汽車 OEM 和初創公司都能更好地應對新汽車領域的挑戰。
審核編輯 :李倩
-
電動汽車
+關注
關注
156文章
12158瀏覽量
231962 -
線束
+關注
關注
7文章
982瀏覽量
26052 -
自動駕駛
+關注
關注
784文章
13910瀏覽量
166761
發布評論請先 登錄
相關推薦
變阻器的未來發展趨勢和前景如何?是否有替代品出現?
國產8位單片機在國內的應用情況及發展趨勢!
連接器和線束的關系
新能源汽車使用鋁芯高壓線束的應用分析
應用DMAIC降低汽車線束開線工序質量損失
未來線束的發展趨勢之一——小線徑鋁導線的應用
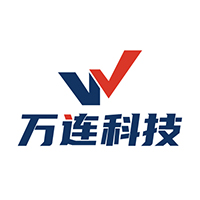
評論