軸承視覺檢測技術,軸承被稱為工業(yè)的“心臟”,是一種廣泛應用的精密基礎部件。
除基本型外,還有各種變型結(jié)構,如帶防塵蓋的、帶橡膠密封圈的、帶止動槽的等。基本型深溝球軸承主要由外圈、內(nèi)圈、鋼球、保持架、鉚釘組成。
以汽車為例,一輛汽車通常有約30種50余套軸承,分布在汽車底盤、變速箱、輪轂、剎車盤、發(fā)動機等位置,行駛中高速轉(zhuǎn)動的軸承有絕對的承上啟下的作用,容不得一點閃失,也關乎汽車的壽命和質(zhì)量。
目前我國軸承產(chǎn)業(yè)規(guī)模已居世界軸承總量第三位,然而,在成品軸承外觀檢測上,基本依賴于人工,在工業(yè)領域,質(zhì)檢要想擺脫人力就必須進行技術升級和轉(zhuǎn)型。
保證出廠軸承的良品率至關重要
軸承作為現(xiàn)代機械設備中的重要零部件,主要功能是支撐機械旋轉(zhuǎn)體,降低運動過程中的摩擦系數(shù),并保證其回轉(zhuǎn)精度。
在生產(chǎn)中,質(zhì)檢是重要的一環(huán)。通常情況下,質(zhì)檢員采用人工肉眼觀察、手指轉(zhuǎn)動軸承等質(zhì)檢方式挑出表面有油污、劃痕等缺陷的軸承。
但質(zhì)檢結(jié)果易受人為因素影響,檢驗標準難以保持一致,穩(wěn)定性差且易漏檢,始終不能做到良品率100%。
就汽車而言,汽車的動力、可靠性、安全性和舒適性都與其息息相關。
因此,保證出廠軸承的良品率至關重要。
軸承常見的表面缺陷一般有以下幾種:
1.麻點
零件表面呈分散或群集狀的細小坑點,呈黑色針孔狀凹坑,有一定深度,個別存在或密集分布。形成原因為金屬表面疲勞,在滾動接觸應力的循環(huán)作用下,金屬亞表面形成微觀裂紋,并逐漸發(fā)展成凹坑狀。
2.擦傷
零件表面因滑動摩擦而產(chǎn)生的金屬遷移現(xiàn)象,其形態(tài)特征為沿軸承零件的滑動方向,并具有一定的長度和深度的表面機械性損傷,這種缺陷多發(fā)生在軸承零件的工作面。
3.裂損
軸承零件金屬的連續(xù)性遭到破壞而產(chǎn)生的損傷,呈現(xiàn)線狀,方向不定有一定的長度和深度,有時肉眼不可見,磁化后有聚粉現(xiàn)象。
由于軸承表面缺陷形態(tài)各異,有些缺陷形態(tài)差別很大,很難找出這類缺陷的共同特點,造成識別上的困難。
有些缺陷目標的空間分布范圍由單一連通的空間區(qū)域組成,而有些缺陷目標則可能由多個子區(qū)域組成;有些缺陷目標具有相當大的形狀任意性和復雜性,并且不同類別的缺陷形狀有可能相當接近,從而使目標和特征之間失去一一對應關系。有些非缺陷,如油印與缺陷非常相似,可能被誤認成缺陷。
基于機器視覺技術軸承缺陷檢測應用
眾所周知,3C電子制造行業(yè)要求使用無塵車間生產(chǎn),為AI質(zhì)檢提供了良好的環(huán)境。然而,軸承零部件行業(yè)的生產(chǎn)環(huán)境卻要差很多,即使是號稱使用“無塵車間”的成品軸承生產(chǎn),其環(huán)境也只是相對干凈和無塵,卻無法與3C電子行業(yè)的無塵車間相提并論。
其次,軸承外觀檢測往往依賴于人,對工藝、要求的認知極大程度上依賴于行業(yè)經(jīng)驗的判斷,軸承缺陷種類繁多,如端面缺陷、外徑缺陷、內(nèi)徑磨削燒傷等,有些瑕疵普通人甚至很難用肉眼觀測得到。
這種情況下,對傳統(tǒng)的檢測方式無疑提出了很大的挑戰(zhàn)。
近幾年,機器視覺在軸承行業(yè)的發(fā)展突飛猛進,已經(jīng)實現(xiàn)的功能主要如下:
宏觀缺陷的檢測
1)滾動體的數(shù)量和位置識別與判定。
2)密封件的標識內(nèi)容、形狀、外觀的識別與判定。
3)套圈表面、滾子表面宏觀裂紋、磕碰等缺陷的識別與判定。
微觀缺陷的檢測
1)軸承零件半成品的尺寸形狀檢測與判定(精度±0.01mm)。可實現(xiàn)鍛件、車件、保持架、密封圈等主要尺寸精度在0.01mm以上的檢測。目前已經(jīng)穩(wěn)定實現(xiàn),并有不少實際應用。
2)軸承零件成品的尺寸形狀檢測與判定(精度±0.001mm)。由于成品零件尺寸形狀精度普遍達到0.001mm,通過單純的光學成像原理來檢測很難達到其精度等級。目前國內(nèi)有一些科創(chuàng)企業(yè)通過后處理算法的優(yōu)化,對檢測精度進行了大幅的提高。
3)軸承零件表面微觀裂紋、麻點、磕碰傷等缺陷的識別與判定。
機器視覺智能在線檢測,摒棄繁瑣低質(zhì)的人工肉眼檢測方式,提升并改進軸承品質(zhì)。
以精加工軸承內(nèi)環(huán)外環(huán)凹槽表面缺陷檢測為例:
根據(jù)軸承特性,視覺系統(tǒng)圖像采集的實際視野大小,寬度方向為10mm左右(軸承實際寬度為7mm左右),本案例采用2K的線掃相機,寬度方向能夠達到的最大分辨率為2048個像素。
相機像素精度=單方向視野范圍大小/相機單方向分辨率。
系統(tǒng)的相機像素精度為10mm/2048pix = 0.0048mm/pix,即每個像素的寬度為0.0048mm。我們規(guī)定缺陷直徑方向上最少有5個像素,所以能夠檢測到寬度0.024mm的缺陷。
采用4K線掃相機,能檢測寬度為0.012mm的缺陷;
采用8K線掃相機,能檢測寬度為0.006mm的缺陷;
本系統(tǒng)視覺組件:2K線掃工業(yè)相機,Schneider線掃工業(yè)鏡頭,鏡頭附加鏡,專用線掃光源,高精度旋轉(zhuǎn)平臺,工業(yè)內(nèi)窺鏡。
表面缺陷檢系統(tǒng)硬件:MV-VS078FC 1024х768面陣相機,M0814-MP 鏡頭,CCD條形光源,高精度旋轉(zhuǎn)平臺
工業(yè)線掃相機具體參數(shù)如下所示:
鏡頭選型
根據(jù)實際情況,圖像采集系統(tǒng)選擇 M0814-MP 鏡頭,該鏡頭結(jié)構設計較為緊湊,分辨率也較高,畸變小(小于 1.0%),非常適合需要高精度的檢測場合。此外,鏡頭上面設計有鎖緊螺母,用于在定好焦距和光圈后進行鏡頭鎖緊,防止圖像采集過程中由于震動而使焦距發(fā)生變化而影響圖像的采集效果。
光源選型
選擇的光源是LED 高角度條形光,型號為 LDR2-90SW,顏色為白色,耗電量為24V/4.2W,發(fā)光面積為100mm×80mm,厚為8mm。
精度分析
根據(jù)軸承特性,視覺系統(tǒng)圖像采集的實際視野大小,寬度方向為10mm左右(軸承實際寬度為7mm左右),長度方向為14本實驗采用1024х768面陣相機,長度方向能夠達到的最大分辨率為1024像素,寬度方向能夠達到的最大分辨率為768個像素。
滾動軸承內(nèi)圈缺陷檢測的 CCD 成像系統(tǒng)設計
為了能利用 CCD 面陣攝像機對軸承外圈表面成像 ,需要用機械設備支撐軸承軸部,使其能轉(zhuǎn)動。用面陣 CCD 攝像頭垂直于軸承外圈面(軸承的法線方向),光源對著軸承外圈面。
滾動軸承外圈缺陷的 CCD 成像系統(tǒng)設計
CCD 攝像機配合光源對軸承外圈滾道面進行了圖像采集,如果金屬表面存在缺陷,其形態(tài)、大小、程度會反映在圖像上,通過專門的圖像檢測軟件,發(fā)現(xiàn)缺陷并對其進行分類。
相機和光源的布置如下圖所示,相機光源布置在軸承外圈兩側(cè),來防止出現(xiàn)一側(cè)遮擋現(xiàn)象。
審核編輯 :李倩
-
機器視覺
+關注
關注
162文章
4389瀏覽量
120447 -
軸承
+關注
關注
4文章
2123瀏覽量
31247 -
檢測技術
+關注
關注
2文章
355瀏覽量
29094
原文標題:基于機器視覺技術軸承缺陷檢測應用
文章出處:【微信號:機器視覺沙龍,微信公眾號:機器視覺沙龍】歡迎添加關注!文章轉(zhuǎn)載請注明出處。
發(fā)布評論請先 登錄
相關推薦
機器視覺檢測應用場景:缺陷檢測、尺寸測量、引導定位、運動控制
視覺檢測是什么意思?機器視覺檢測的適用行業(yè)及場景有哪些?
機器視覺在焊接質(zhì)量檢測中的應用
機器視覺的四大類應用是什么?
深度學習在工業(yè)機器視覺檢測中的應用

機器視覺檢測技術在工業(yè)自動化中的應用
機器視覺尺寸檢測技術全解析!
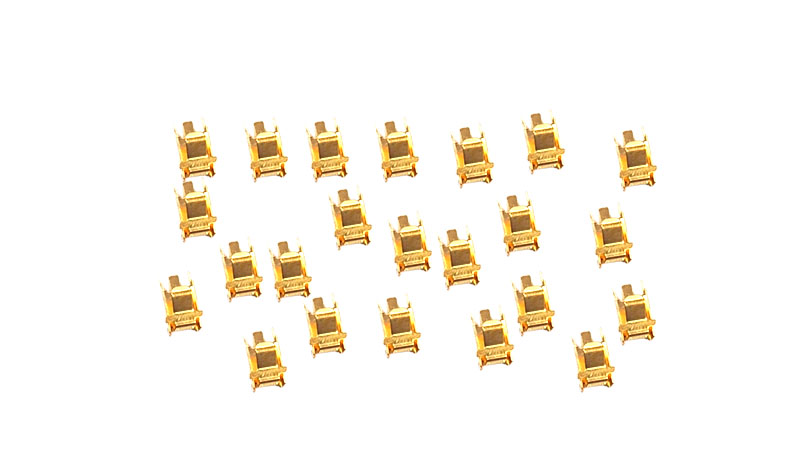
一目了然:機器視覺缺陷識別方法
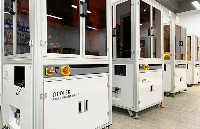
評論