近年來,隨著智能汽車相關技術的迅速發展,在過去的五十年間,工業機器人就已經被廣泛應用于車身制造車間,來更大的提升生產力。如今,市場經濟的蓬勃發展推動了生產需求的提升,工業機器人技術已無法滿足日益復雜的市場,因為機器人技術的高效僅僅展現在負責傳送汽車底盤的傳送系統上。對于許多汽車廠來說,效率低下的傳送系統業已成為提升性能的主要障礙。
傳統傳送技術存在的問題
事實上,在車間的日常運用中,汽車制造業所用的傳送技術還影響了產能和靈活性。現有的鏈條式傳送帶、輥道甚至滑板傳送帶都需要以定速、定節距運行。對于汽車裝配廠來說,這意味著整個傳送系統必須始終保持通電狀態并以相同的速度運行才能正常運轉。然而,傳統的傳送載體無法加速、減速,也無法根據工序步驟的完成情況精確定位特定的底盤。雖然某些傳統系統支持變“節距”或改變傳送器之間的距離,但在大多數情況下,即使距離改變,也難以兼容多種型號。
此外,傳統傳送帶采用復雜的機械設計,配有傳送鏈、傳送帶、輥輪和齒輪等,有時還需要使用數百種易磨損零部件。這些解決方案體量龐大、結構復雜,不僅難以調整,還需要頻繁維護并可能導致計劃外停機。但更重要的可能是,傳統的摩擦式傳送系統依靠的是旋轉電機技術。從本質上來說,旋轉電機會增加線性應用的慣性,并引入多個機械部件,這會影響速度和加速度的提升。
如何提高裝配傳送系統的性能?
目前,對于汽車制造商而言,提高車間裝配傳送系統的性能迫在眉睫。為了更好的適應市場需求,羅克韋爾自動化推出了獨立小車技術,能夠依托直線電機技術在實際生產中取得新進展,并推動性能效率的顯著提升。
這是為什么呢?首先,借助線性電機技術,汽車制造商可對傳送模塊進行端到端配置,產生可驅動傳送器的電磁力,讓載體以遠超傳統系統的速度移動。其次,直線電機沒有接觸件,也沒有易磨損零部件,能夠更大限度地減少了維護作業。不過,直線電機只是一方面,真正提高生產力、靈活性和可持續性的則是智能運動控制系統。例如,全球知名汽車自動化系統供應商 Kuka Systems 推出的 PULSE 載體傳送系統。該系統專為汽車車身裝配流水線而設計,采用的是 MagneMotion 的直線同步電機技術。
此外,利用嵌入式位置傳感器和控制軟件可對軌道上的每個載體進行單獨控制,并對加速度、減速度、移動速度和位置等參數進行編程。車身部分并不以固定的速度移動,而是可以隨著一道又一道工藝步驟快速向前穿過機器人工作站。
那么結果如何呢?與傳統的摩擦式傳送系統相比,這樣的“無節距”系統不僅更節能,速度也提升了 30%。而速度提升后,工業機器人和其他加工設備的價值也得到更充分地利用,并大大縮小了系統的整體占用空間(與傳統系統相比)。另外,這一系統的可配置程度極高,經過改造后可兼容多個型號,而其模塊化設計更是提高了擴展的成本效益。
羅克韋爾自動化獨立小車系統在車間運用中還具有如下優勢:
產量提高
機械部件和連桿數量有所減少。加速度提高 (>6g),速度亦有所提升 (>5m/s),且運動軌跡全面受控,產量得到提高
靈活性增強
每個移動的載體都支持獨立控制,可靈活調整機械節距,讓同一臺機器得以同時處理多種包裝/格式規格并全面控制產品的移動
包裝追蹤質量穩定
提供完整的追蹤軌跡。載體由軟件控制,用戶無需使用外部傳感器和復雜的追蹤解決方案,即可確切了解載體位置
靈活性正常運行時間得到延長
淘汰機械連桿和機械部件,僅留極少移動部件,這樣可以縮短整體停機時間、減少維護并降低能耗
占用空間明顯減小
借助獨立小車技術,可以在更小的空間內利用一種機器處理多種產品規格
小羅有話說
羅克韋爾自動化作為作為智能制造的引領者,未來將繼續專注于技術創新,利用自動化、數字化和智能化技術,為汽車行業打造更安全、環保、節能、高效的超級車間,提升企業的全球競爭力,推動汽車制造業的數字化和智能制造轉變。
審核編輯 :李倩
-
電機技術
+關注
關注
1文章
50瀏覽量
11144 -
運動控制
+關注
關注
4文章
585瀏覽量
32915 -
傳送帶
+關注
關注
0文章
22瀏覽量
8794
原文標題:獨立小車技術 | 車間的“智勝法寶”,下一代運動控制
文章出處:【微信號:羅克韋爾自動化,微信公眾號:羅克韋爾自動化】歡迎添加關注!文章轉載請注明出處。
發布評論請先 登錄
相關推薦
如何優化總線系統的性能
明達MR30 IO模塊助力汽車座椅裝配線升級

如何優化MEMS設計以提高性能
如何優化DCS系統的性能
如何提高GPU性能
如何提高云計算的性能和效率
提高系統的阻尼比對系統有何影響
能否建議通過內存映射提高aur性能?
美國硅谷站群服務器如何提高網站性能
挖掘機生產裝配線無線通訊應用
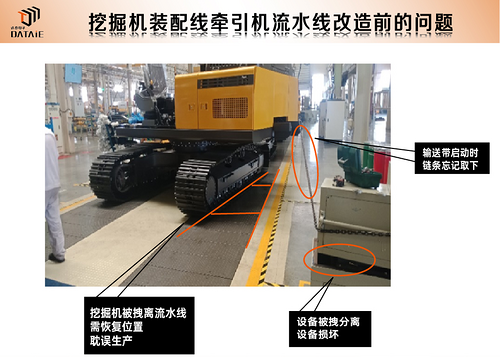
評論