業(yè)內獨創(chuàng)!WAYON維安內置絕緣封裝高壓MOSFET由代理KOYUELEC光與電子提供技術選型和方案應用
近年來,新一代電動汽車的進一步普及,促進了更高效、更小型、更輕量的電動系統(tǒng)的開發(fā)。同時,在電動汽車領域,為延長續(xù)航里程,車載電池的容量呈日益增加趨勢,隨著新能源汽車續(xù)航里程不斷提升,相應的電池容量日益提高,如特斯拉Modle S 2021款長續(xù)航升級版(719km)電池容量100kWh,與此同時,還要求縮短充電時間, Modle S 2021款快充時間1小時。為了解決這些問題,能夠實現高耐壓和低損耗的功率元器件被寄予厚望。
高功率、高效率就意味著需要更低導通電阻的MOSFET,目前TO-247封裝是高功率充電機、充電樁電源模塊應用中使用最多的封裝形式。但常規(guī)TO-247封裝框架和漏極直接相連,非絕緣特性使得應用的時候必須外部安裝絕緣片,復雜的生產過程容易造成外部絕緣片破裂,導致絕緣強度下降甚至短路,使得產品整體可靠性下降。
圖1 常規(guī)TO-247 封裝示意圖
圖2 充電機TO-247安裝示意圖
圖3 外部絕緣片破損示意圖
功率器件安裝到散熱器使用時,系統(tǒng)熱阻包括封裝芯片Rthj-c和散熱器到環(huán)境電阻Rth(h-a),結到環(huán)境總熱阻Rth(j-a) = Rth(j-c) + Rth(c-h) + Rth(h-a)。
圖4 MOSFET die 模型
圖5 TO247 MOSFET封裝結構
硅芯片通過預成型件連接到框架,整個結構封裝在樹脂中,由于樹脂的熱導率非常低,因此硅芯片散熱的首選路徑是熱導率較高的銅質背面,管芯內產生的功率會改變器件的溫度,并根據所涉及層的熱電容和電阻(從硅到封裝背面)使器件溫度升高,類似于圖4所示的熱模型。
維安創(chuàng)新的內置絕緣封裝可將陶瓷絕緣片封裝到內部,降低散熱器到環(huán)境電阻Rth(h-a),內部陶瓷絕緣材料緩沖了功率MOSFET封裝中硅片和銅框架的熱膨脹系數的差異,顯著減少相鄰層之間的熱失配,提高了功率循環(huán)耐受性,進而降低器件結溫給應用帶來諸多優(yōu)點。
圖6 常規(guī)封裝熱阻示意圖
圖7 常規(guī)TO-247封裝安裝示意圖
優(yōu)點一:熱阻低
采用恒功率模塊電路進行驗證測試,對比實測數據得出結論:相比外部絕緣片,內部絕緣結到散熱器熱阻更低,故而內置絕緣整體熱阻比普通封裝加外置絕緣片的系統(tǒng)熱阻低。
圖8 恒功率模塊電路驗證測試
圖9 TO-247 外部加絕緣片熱阻評估
圖10 TO-3P ISO內部絕緣封裝熱阻評估
圖9溫升數據 △T =40 ℃,P=28.86W,R=1.38℃/W;
圖10溫升數據 △T ℃=33.7 ℃,P=29W,R=1.16℃/W。
優(yōu)點二:溫升低
低熱阻也使得實際應用過程中器件溫升較低,如下150W LED電源驗證測試對比數據,在220VAC 輸入條件下內置絕緣產品WMC53N60F2表面溫度比常規(guī)TO-247 WMJ53N60F2低5.1℃,且低溫升還能提高器件的使用壽命。
圖11 溫升對比曲線
優(yōu)點三:高可靠性
簡化生產工藝,避免生產工藝導外部致絕緣片破裂導致的故障,提高可靠性。
圖12 內置絕緣封裝安裝示意圖
封裝的銅框架和半導體硅芯片熱膨脹系數差異較大,使用陶瓷絕緣片可以減低二者熱膨脹系數差異,提高功率循環(huán)的可靠性。
圖13熱膨脹系數差異
外部異常應力導致炸機,絕緣特征依然存在,即異常失效后仍有絕緣特征。
圖14 管體異常裂隙
常規(guī)TO-247的封裝安裝孔和框架的絕緣距離是3.7mm, 在某些要求較高的應用中,安全距離可能不滿足要求,內置絕緣封裝有更大的安規(guī)要求距離。 內置絕緣器件絕緣耐壓測試>2500VAC。
圖15 內置絕緣封裝安裝孔距
業(yè)內領先的深溝槽工藝與獨創(chuàng)的內絕緣封裝結合,使得SJMOSFET具有業(yè)內領先的超高功率密度,可大大提升電源的總體功率密度,節(jié)省空間。目前內置絕緣封裝產品主要面向高功率電源模塊,比如新能源汽車地面充電樁模塊電源,充電機高功率和電子負載類儀表儀器行業(yè)。
維安內置絕緣主推的物料
審核編輯:湯梓紅
-
電動汽車
+關注
關注
156文章
12154瀏覽量
231908 -
MOSFET
+關注
關注
147文章
7213瀏覽量
213840
發(fā)布評論請先 登錄
相關推薦
CCPAK1212封裝將再次提升Nexperia功率MOSFET的性能表現
安世半導體CCPAK1212封裝再次提升Nexperia功率MOSFET的性能表現
意法半導體高壓功率MOSFET研討會即將來襲
華盛昌萬用絕緣表在配電網運維中的具體應用
GB-311.1-1997高壓輸變電設備的絕緣配合
銳駿200V低壓和600V高壓MOS對于電機控制和電源管理
PEM羅式線圈在高壓絕緣放電測試瞬態(tài)變化上的應用
OC5818內置功率MOSFET的單片降壓型開關模式轉換器中文手冊
高壓開關柜設備需要做哪些絕緣預防性試驗
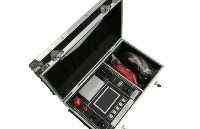
淺談煤礦高壓動力電纜絕緣故障系統(tǒng)的研究
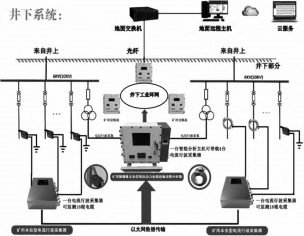
評論