電機采用編織繞組技術,減少了原材料用量,所需焊點也比發夾式繞組少得多。此外,電機采用的冷卻技術讓冷卻液與銅直接接觸。
冷卻液直觸、編織繞組技術以及其他創新技術的應用使系統功率凈增加50%。
ZF表示,其模塊化電驅系統將于2025年投入生產線。
采埃孚表示,即將在2025年投入生產的新一代電驅系統結構更加緊湊,能提供更大的能量密度,且適應性更強,這對新一代純電汽車的制造商有極大吸引力。該集團最近展示了新模塊化概念系統的關鍵細節,其工作電壓可設置為400V或800V。在近期的一場數字研討會上,公司高管告訴全球媒體,這款可定制系統囊括了電機、逆變器、變速箱和軟件,能夠幫助OEM縮短開發時間。
高管們表示,該系統可以滿足80%的現有OEM用例。
電氣系統產品經理Markus Schwabe指出,“采埃孚已經準備好應對當前和未來的挑戰”。作為傳統變速箱的大型供應商,采埃孚一直在增加對電氣化的投資。2019年,它開始為奔馳EQS SUV提供整個動力總成。Schewabe表示,“盡管我們站在系統的角度,并擁有強大的技術,但我們也深知每一個組件是多么重要。”他補充道,采埃孚工程師們專注于提升以下四個方面的性能:成本、里程、扭矩和功率密度。新系統的設計需要盡可能滿足“即裝即用”。采埃孚預測,新系統可以直接滿足80%的客戶需求,其余只需簡單定制就可適應任何應用需求。Schwabe還表示,采埃孚預計,對800V系統的需求將迅速超過400V系統。電驅動技術開發負責人Otmar Scharrer說,其電驅系統的緊湊性和各個部件的內部接口設計,使得調整相當輕松;此外,這些設計還具有非常高的結構剛度,極大提升了NVH性能。
新技術的一大關鍵點在于,對400V和800V系統不同需求的處理是由控制芯片和帶有獨立電源開關的逆變器進行的。采埃孚斷言,與目前的電源模塊相比,這種結構可以有效減少部件數量。Sharrer說:“我們可以更快、更精確地服務于不同的市場要求。”據悉,系統軸功率最低為100 kW(134馬力),最高可達300 kW(402馬力)。
編制繞組的優勢
采埃孚工程師介紹,新一代電機的編織繞組技術在提高系統功率密度中起到了重要作用。電機產品系列負責人Roland Hintringer說,“發夾式繞組是當今最先進的技術,在五到七年前推出,需要數百個激光焊點。”而采埃孚電機上的線圈只需一步就可編織成型,耗時少,占用空間也更小,其繞組端部尺寸為15毫米,而發夾式為28毫米;并且編織繞組只需要24個焊點,還可以減少10%的原材料用量。
采埃孚的工程師們非常注重冷卻,冷卻技術可以極大提升功率。除了在電機外殼采用水冷技術外,他們還將冷卻油泵送到定子周圍和編織繞組內部的縫隙中。Hintringer解釋道,“冷卻油流經定子并在溫度最高的部位與銅直接接觸”,這使峰值性能提高85%,功率提高50%,所需稀土用量只占目前技術所需稀土量的1%。
高功率密度
采埃孚通過使用兩個行星齒輪組改進了以前的偏置齒輪箱。
為車輪提供動力的是新一代同軸減速箱,它應用了采埃孚的關于行星齒輪的專業技術,其中使用兩個行星齒輪以實現所需的減速比和50/50的功率分配。車橋驅動工程產品線負責人Robert Peter表示,這款減速箱還具備完全的差速器功能;與2011年以來常見的平行軸解決方案相比,新一代變速箱所占空間減少了25%,功率密度更高,重量減少了10%,傳動損耗降低了20%,并且其NVH性能與平行軸相當,甚至更好。
Peter說:“我們的變速箱技術幫助我們解決了提升NVH性能和降低重量之間的矛盾。”
這種DC-DC轉換器是為燃料電池而設計的。效率達到99.6%。
工程師們還說,新的逆變器設計能夠更充分地與動力總成的其他部分融合。他們預測,在2030年前,比硅性能更出色的碳化硅芯片驅動的裝置將占據約60%的市場份額。除了逆變器之外,采埃孚還在制造一種用于燃料電池的高壓DC-DC轉換器,該轉換器的效率高達99.6%,并且控制整個系統的軟件設計得很靈活,可以根據不同的驅動特性進行調整。
審核編輯:劉清
-
OEM
+關注
關注
4文章
402瀏覽量
50405 -
逆變器
+關注
關注
286文章
4738瀏覽量
207279 -
電氣系統
+關注
關注
1文章
365瀏覽量
24278 -
電驅系統
+關注
關注
0文章
114瀏覽量
2428
原文標題:采埃孚推出全套電驅系統,幫助OEM縮短開發時間
文章出處:【微信號:SAEINTL,微信公眾號:SAE International】歡迎添加關注!文章轉載請注明出處。
發布評論請先 登錄
相關推薦
英飛凌與采埃孚合作優化自動駕駛軟件
采埃孚富士康展望2029年營收翻倍,沈陽新廠加速布局
恩智浦和采埃孚合作開發基于SiC的電動汽車牽引逆變器解決方案
電驅失效類型和風險分析,如何從測試端提升電驅可靠性?
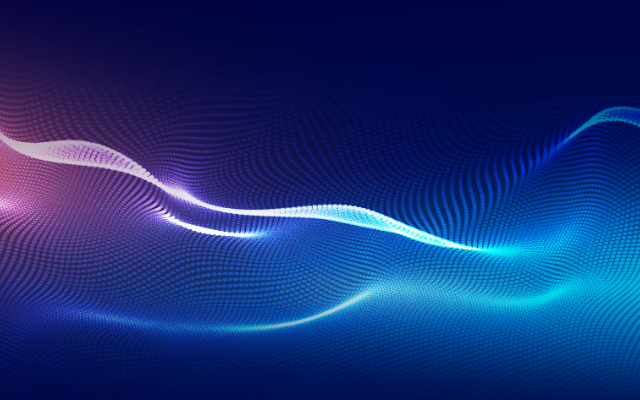
恩智浦與采埃孚攜手推動電動汽車行業創新:SiC牽引逆變器解決方案亮相
電驅逆變器模塊連續工作測溫系統的開發步驟和過程
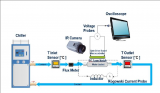
評論