經(jīng)過氧化、光刻、刻蝕、沉積等工藝,晶圓表面會(huì)形成各種半導(dǎo)體元件。半導(dǎo)體制造商會(huì)讓晶圓表面布滿晶體管和電容(Capacitor);而代工廠或CPU制造商則會(huì)讓晶圓底部排列鰭式場(chǎng)效電晶體(FinFET)等三維晶體管。
▲ 圖1: 電子元器件區(qū)域與金屬布線區(qū)域
單獨(dú)的元器件若不經(jīng)連接,則起不了任何作用。如果不把電子線路板上的元器件焊接起來,它們就無法工作。同樣地,晶圓上的晶體管若沒有相互連接起來,也起不了任何作用。只有把晶體管與外部電源連接起來,它們才能各司其職,正常執(zhí)行把已處理過的數(shù)據(jù)傳輸?shù)较乱粋€(gè)環(huán)節(jié)等各種工作。可見,晶圓上的元器件與電源以及其他元器件之間的連接是必要的。更何況,半導(dǎo)體本身就是一個(gè)“集成電路”,各個(gè)元器件之間需要通過電能來“交流”信息。根據(jù)半導(dǎo)體電路圖連接電路的過程,就是本篇要講的“金屬布線”工藝。
相同的元器件,用不同的方式連接,也能形成不同的半導(dǎo)體(CPU、GPU等)。可以說,金屬布線是賦予半導(dǎo)體工藝“目的”的一個(gè)過程。
本篇要講的金屬布線工藝,與前面提到的光刻、刻蝕、沉積等獨(dú)立的工藝不同。在半導(dǎo)體制程中,光刻、刻蝕等工藝,其實(shí)是為了金屬布線才進(jìn)行的。在金屬布線過程中,會(huì)采用很多與之前的電子元器件層性質(zhì)不同的配線材料(金屬)。 換言之,不像刻蝕工藝有專門的“刻蝕設(shè)備”,金屬布線環(huán)節(jié)沒有其專門的“設(shè)備”,而是要綜合使用各個(gè)工藝環(huán)節(jié)的設(shè)備:如移除殘余材料時(shí),使用刻蝕設(shè)備;添加新材料時(shí),使用沉積設(shè)備;每道工藝之間,則通過光刻設(shè)備進(jìn)行光刻。
導(dǎo)線與元器件的連接:接觸孔
連接電子線路板時(shí),要先用電線連接電子線路板上的各個(gè)電子元器件后,再進(jìn)行焊接。但半導(dǎo)體制程需要從下往上一層一層堆疊。因此,要先做好元器件層后,在其上層生成接觸孔(Contact,連接元器件與導(dǎo)線),然后再進(jìn)行金屬布線。
▲ 圖3:生成接觸孔時(shí),鎢(W)的作用與金屬阻擋層的作用
或許有些讀者會(huì)好奇:為什么不跳過“接觸孔”,直接把金屬與元器件連接起來?這還要從半導(dǎo)體的微細(xì)化說起。衡量溝槽填充程度的溝槽填充(Gap fill)能力。若使用鋁等配線材料,一旦穿孔稍深一些,就算“沉積”得再好,也無法把溝槽完全填充好,從而容易生產(chǎn)出一些中間有空隙的不良導(dǎo)線。也就是說,如果想實(shí)現(xiàn)較深的金屬布線(即元器件層與金屬布線層的距離較遠(yuǎn)時(shí)),就需要用鎢(W)等溝槽填充能力優(yōu)秀的配線材料進(jìn)行沉積,提前把溝槽填充好。或者,生成接觸孔后再進(jìn)行高溫處理。如果采用鋁等熔點(diǎn)較低的配線材料,需要先用鎢形成接合面后,再連接鋁導(dǎo)線。
在尺度只有頭發(fā)直徑數(shù)千分之一的微觀世界里,很多問題是我們難以想象的。為解決這些問題,我們必須比較各種對(duì)策,不斷尋找最優(yōu)的方案。前邊提到的鎢配線似乎只有優(yōu)點(diǎn),其實(shí)不然。作為半導(dǎo)體配線材料,鎢遠(yuǎn)不如銅或鋁。鎢的電阻大,如果用它來充當(dāng)所有配線材料,將大幅提高半導(dǎo)體的功耗。
金屬阻擋層:減少金屬與金屬之間的電阻
元器件與接觸孔之間需要能起到阻擋作用的金屬層(金屬或金屬化合物)——金屬阻擋層(Barrier metal)。連接不同性質(zhì)的物質(zhì)時(shí),接合面的電阻會(huì)變大,令半導(dǎo)體的功耗大幅提高。因此,在半導(dǎo)體制程中,有效連接金屬與非金屬材料的難度相當(dāng)大。形成金屬阻擋層的目的,便是實(shí)現(xiàn)非金屬材料與金屬材料間的“自然”過渡。要形成金屬阻擋層,我們要先在硅表面涂敷鈦(Ti)或鈷(Co)等材料,使其與硅發(fā)生反應(yīng)生成硅化物接觸結(jié)構(gòu)(Contact Silicide)。這一過程被稱為硅化工藝(Silicidation) 。
此外,金屬阻擋層還可以在各工藝中保護(hù)元器件不受損。例如,鋁與硅(Si,晶圓的主要成分)相遇時(shí)會(huì)發(fā)生反應(yīng),導(dǎo)致接合面被破壞。因此,如果想在元器件層的近處排布鋁線,就必須在硅與鋁接合面之間形成鈦化合物等阻擋層,防止接合面被破壞。
▲ 圖4:采用鋁材料進(jìn)行金屬布線時(shí),金屬阻擋層的作用
如果以銅取代鋁作為配線材料,金屬阻擋層的作用就更多了。銅的反應(yīng)能力比鋁還強(qiáng),可以與比硅更穩(wěn)定的二氧化硅(SiO2)發(fā)生反應(yīng)。如果銅擴(kuò)散到二氧化硅里,銅粒子就會(huì)滲入到氧化膜中,造成漏電現(xiàn)象。為防止這種情況的發(fā)生,要用鉭(Ta)在銅與元器件層接合面形成阻擋層。
導(dǎo)線:元器件與元器件之間的電線
生成接觸孔后,下一步就是連接導(dǎo)線。在半導(dǎo)體制程中,連接導(dǎo)線的過程與一般電線的生產(chǎn)過程非常相似,即先制作線的外皮。在一般的電路連接中,直接采用成品電線即可。但在半導(dǎo)體制程中,需要先“制作電線”。
▲ 圖5:反應(yīng)性離子刻蝕(RIE)與鑲嵌(Damascene)工藝的比較
電線的制作過程因配線材料而異。如果沉積鋁配線,可采用在前幾篇文章講述過的刻蝕和沉積工藝制作:先在整張晶圓表面涂敷金屬膜,再在涂敷光刻膠后進(jìn)行曝光,然后移除殘余的鋁材料,最后在鋁周圍添加各種絕緣材料。 然而,采用銅作為配線材料時(shí),金屬與電介質(zhì)層的沉積順序要反過來:即先沉積電介質(zhì)層,再通過光刻工藝刻蝕電介質(zhì)層,接著形成銅籽晶層(Seed Layer),在電介質(zhì)層之間加入銅,最后去除殘余銅。
有些讀者可能會(huì)好奇:只是調(diào)換了沉積順序,為什么這么重要?如前所述,采用銅布線,就必須涂敷銅籽晶層,為此又新加入了沉積和電鍍(Electroplating,以鋁作為配線材料時(shí)不需要電鍍過程)等工藝。日后,為攻克鋁配線帶來的技術(shù)難題,除用銅(Cu)來做線材外,我們還需要研發(fā)出更多新的工藝。
其實(shí),早在100年前,人類就知道銅的導(dǎo)電性要優(yōu)于鋁。那么,當(dāng)時(shí)為什么沒有把銅用作配線材料?因?yàn)椋瑥陌雽?dǎo)體制造商的角度來看,要以更低廉的成本令導(dǎo)線用于更多的晶體管,半導(dǎo)體制造工藝也需要同步發(fā)展,而當(dāng)時(shí)的工藝并無法解決銅配材帶來的新問題。
金屬布線越往上越厚。在半導(dǎo)體元器件中,頻繁交流龐大數(shù)據(jù)的元器件之間當(dāng)然要近一些,反之則可以遠(yuǎn)些。排列較遠(yuǎn)的元器件之間,可以通過上層較厚的金屬布線來進(jìn)行連接。 不難看出,位于上層的較厚金屬導(dǎo)線無需高難度技術(shù)做支撐。半導(dǎo)體制造商在過去制作的有一定厚度的鋁導(dǎo)線到如今也可以直接放到上層。也就是說,上層布線無需采用尖端技術(shù),只要沿用以往的工藝即可。這也是半導(dǎo)體制造商節(jié)省投資并縮短工藝學(xué)習(xí)時(shí)間的一個(gè)有效方法。
技術(shù)的組合
上述技術(shù)并非各自獨(dú)立存在,而是根據(jù)各半導(dǎo)體制造商的不同目的,形成各種不同組合,從而生產(chǎn)出廠商希望制造的多種半導(dǎo)體。例如,與SK海力士等芯片制造商不同,臺(tái)積電(TSMC)、英特爾等邏輯半導(dǎo)體制造商對(duì)晶體管的電流控制能力要求比較高。
為此,邏輯半導(dǎo)體制造商采用了FinFET等三維晶體管,實(shí)現(xiàn)了三維結(jié)構(gòu)的電流,以增加電流通道的面積。在三維晶體管上生成接觸孔,當(dāng)然要比在DRAM等平面晶體管上難度更大。圖6形象地揭示了這兩種情況,左圖是在平面電流通道生成接觸孔,較容易;右圖是在三維晶體管上生成接觸孔,較難。
▲ 圖6:在邏輯半導(dǎo)體的FinFET生成接觸孔,要遠(yuǎn)比在DRAM的平面晶體管生成接觸孔難。
導(dǎo)線的金屬阻擋層也一樣,英特爾在其7納米工藝中,為解決銅的電遷移現(xiàn)象,試圖用鈷配線代替銅,卻兜了好幾年的圈子。2022年,英特爾在4納米工藝中又重新回到原點(diǎn),采用銅配線,試圖通過用鉭(Ta)和鈷金屬層包裹銅線來攻克技術(shù)難關(guān)。英特爾將此稱為“強(qiáng)化銅(Enhanced Cu)”。
隨著半導(dǎo)體的日益微細(xì)化,這種新的挑戰(zhàn)將不斷出現(xiàn)。對(duì)英特爾等CPU制造商來說,元器件的高速運(yùn)行至關(guān)重要。正是由于CPU制造商非常重視元器件的速率,連抗電遷移性能出色的銅配線也遇到了瓶頸。英特爾的幾番周折正是為了解決銅配線帶來的技術(shù)難關(guān)。而像SK海力士等芯片制造商,雖然不存在電路運(yùn)行速率上的問題,但卻在堆疊電容維持電荷容量上遇到了難題。微細(xì)化給處于不同制造環(huán)境的制造商提出的技術(shù)難題各有不同。
審核編輯:劉清
-
DRAM
+關(guān)注
關(guān)注
40文章
2337瀏覽量
184712 -
晶圓
+關(guān)注
關(guān)注
52文章
5049瀏覽量
128840 -
晶體管
+關(guān)注
關(guān)注
77文章
9882瀏覽量
139875 -
FinFET
+關(guān)注
關(guān)注
12文章
253瀏覽量
90726
原文標(biāo)題:金屬布線—為半導(dǎo)體注入生命的連接
文章出處:【微信號(hào):半導(dǎo)體封裝工程師之家,微信公眾號(hào):半導(dǎo)體封裝工程師之家】歡迎添加關(guān)注!文章轉(zhuǎn)載請(qǐng)注明出處。
發(fā)布評(píng)論請(qǐng)先 登錄
相關(guān)推薦
有關(guān)半導(dǎo)體工藝的問題
半導(dǎo)體工藝講座
6英寸半導(dǎo)體工藝代工服務(wù)
半導(dǎo)體工藝幾種工藝制程介紹
《炬豐科技-半導(dǎo)體工藝》硅納米柱與金屬輔助化學(xué)蝕刻的比較
《炬豐科技-半導(dǎo)體工藝》超大規(guī)模集成電路制造技術(shù)簡介
半導(dǎo)體工藝之金屬布線工藝介紹
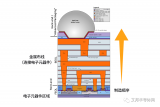
半導(dǎo)體工藝之金屬互連工藝
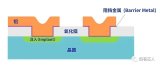
半導(dǎo)體前端工藝:金屬布線—為半導(dǎo)體注入生命的連接
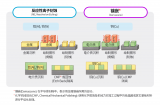
評(píng)論