1.壓合凹陷
異?,F象:
產品表面出現凹陷的現象。
原因分析:
1、銅箔品質異常。
2、無塵室潔凈度不夠。
3、p/p未封邊。
4、銅箔絲、p/p粉塵、砂紙顆粒、頭發、牛皮紙屑等異物造成。
5、鋼板上異物。
6、鋼板刮傷。
處理流程:
處理步驟與參數:
1、 將異常填寫于壓合課后處理質檢統計表
2、 單pcs報廢或作整片報廢處理。作整片報廢處理則進行3b-1的步驟。
3a-1.決定單pcs報廢繼續送下制程。
3a-2.在異常的pcs上打報廢戳記并剪角標記在工單上注明異常原因及數量按正常流程轉下制程。
3b-1.作整片報廢處理。
3b-2.檢驗人員將板子交課內賬目管理員,由賬目管理員負責按MRB流程將異常板送至MRB。
檢查單位:
壓合檢修站
檢查項目:
是否有凹陷現象
2.織紋顯露
異?,F象:
外層蝕刻后在PP的地方有織紋顯露。
原因分析:
1、壓機程序設定不當。
2、物料(PP)異常。
3、迭板結構設計異常。
處理流程:
處理步驟與參數:
1、 將異常填寫于壓合課檢驗日報表。
2、 單pcs報廢或作整片報廢處理。
決定單pcs報廢處理則進行3a-1的步驟。
作整片報廢處理則進行3b-1的步驟。
3a-1.決定單pcs報廢繼續送下制程。
3a-2.在異常的pcs上打報廢戳記并剪角標記在工單上注明異常原因及數量按正常流程轉下制程。
3b-1.作整片報廢處理。
3b-2.檢驗人員將板子交課內賬目管理員,由賬目管理員負責按MRB流程將異常板送至MRB。
檢查單位:
外層檢驗、終檢。
檢查項目:
是否有織紋顯露。
3.壓合皺折
異?,F象:
產品銅面出現皺折現象。
原因分析:
1、 銅箔本身皺折。
2、作業方法不對,造成皺折。
3、壓合程序不當。
4、內層線路設計不當。
5、迭板夾頭不平整。
6、鉚釘用錯。
7、鉚合板厚計算錯誤。
8、板面設計時空曠區太大填膠不足及流膠口設計異常流膠不均。
9、壓機停電造成失壓。
處理流程:
處理步驟與參數:
1、 將異常填寫于壓合課后處理質檢統計表。
2、 單pcs報廢或作整片報廢處理。
決定單pcs報廢處理則進行3a-1的步驟。
作整片報廢處理則進行3b-1的步驟。
3a-1.決定單pcs報廢繼續送下制程。
3a-2.在異常的pcs上打報廢戳記并剪角標記在工單上注明異常原因及數量按正常流程轉下制程。
3b-1.作整片報廢處理。
3b-2.檢驗人員將板子交課內賬目管理員,由賬目管理員負責按MRB流程將異常板送至MRB。
檢查單位:
壓合檢修站。
檢查項目:
是否有壓合皺折。
4.壓合偏移
異常現象:
在壓合前或壓合后發生內層偏移。
原因分析:
1、鉚釘開花不良。
2、內層板漲縮不一致。
3、壓機平整度異常。
4、組合偏移。
5、壓合偏移。
6、內層曝偏。
處理流程:
處理步驟與參數:
1、 將異常填寫于壓合課X-Ray鉆靶機生產日報表。
2、 繼續送下制程或作報廢處理。
決定繼續送下制程處理則進行3a-1的步驟。
作報廢處理則進行3b-1的步驟。
3a-1.決定繼續送下制程。
3a-2.剪角標記并在工單上注明異常及數量按正常流程轉下制程。
3b-1.作報廢處理。
3b-2.檢驗人員將板子交課內賬目管理員,由賬目管理員負責按MRB流程將異常板送至MRB。
檢查單位:
壓合檢修站。
檢查項目:
是否有壓合偏移。
5.靶孔不良
異常現象:
打靶后發現靶孔不良。
原因分析:
1、鉆頭磨損不一致。
2、重復鉆。
3、壓合偏移。
4、內層靶孔制作不良。
5、鉆靶偏、鉆針過小或過大。
6、鉆靶機精度異常。
7、鉆靶精度異常。
8、壓合漲縮異常。
9、鉆靶機機臺故障。
處理流程:
處理步驟與參數:
1、 將異常填寫于壓合課X-Ray鉆靶機生產日報表。
2、 繼續送下制程或重工處理。
決定繼續送下制程處理則進行3a-1的步驟。
作重工處理則進行3b-1的步驟。
3a-1.決定繼續送下制程。
3a-2.剪角標記并在工單上注明異常及數量按正常流程轉下程。
4a-1.異常板未超過10pnl,補膠后按正常作業步驟重鉆。
4a-2.剪角標記并在工單上注明異常及數量按正常流程轉下制程。
4b-1.異常板超過10pnl,PCB和埋鉆板需打中間短靶制作;HDI轉MASK板應重新補打CCD。
4b-2.異常板將不良靶孔撈破,提DRB管制。
檢查單位:
壓合檢修站。
檢查項目:
是否有靶孔不良。
6.撈邊尺寸不足
異?,F象:
在壓合撈邊,磨邊時,成型后的尺寸異常。
原因分析:
1、成型撈邊參數設定有誤。
2、磨邊參數設定有誤。
3、pin針未固定好。
4、人員操作失誤。
處理流程:
處理步驟與參數:
1、 將異常填寫于壓合課后處理質檢統計表。
2、 繼續送下制程或作報廢處理。
決定繼續送下制程處理則進行3a-1的步驟。
作報廢處理則進行3b-1的步驟。
3a-1.決定繼續送下制程。
3a-2.剪角標記并在工單上注明異常及數量按正常流程轉下制程。
3b-1.作報廢處理。
3b-2.檢驗人員將板子交課內賬目管理員,由賬目管理員負責按MRB流程將異常板送至MRB。
檢查單位:
壓合檢修站。
檢查項目:
是否有尺寸異常。
7.棕化刮傷
異常現象:
產品表面出現凹陷的現象。
原因分析:
1、滾輪刮傷。
2、人員未按照Handling作業規范進行作業。
3、治具板邊沿刮傷板面。
處理流程:
處理步驟與參數:
1、 將異常填寫于壓合課水平棕化線生產日報表。
2、 送棕化線重工或作報廢處理:
決定重工處理則進行4a-1的步驟。
作報廢處理則進行4b-1的步驟。
4a-1.按照棕化線正常生產程序生產,并記錄壓合課水平棕化線重工生產日報表(32123001-02)。
4a-2.用油性筆在板邊劃線作標記轉下制程。
4b-1.作報廢處理。
4b-2.檢驗人員將板子交課內賬目管理員,由賬目管理員負責按MRB流程將異常板送至MRB。
3、 重工辦法:
3-1.內層銅厚為0.5 OZ的板子不允許重工作業。
3-2.內層銅厚為1OZ允許重工一次,重工時100%依工單確認其阻抗線寬和面銅厚度,重工后內層銅厚不得低于1.0mil。
3-3.內層銅厚為2OZ允許重工一次,重工時100%依工單確認其阻抗線寬和面銅厚度,重工后內層銅厚不得低于2.4mil。
3-4.SAMPLE板重工前100%依工單確認其阻抗線寬和面銅厚度。
注:銅厚量測五個點,線寬量測稀疏區,密集區及阻抗線三個點(若重工面次為大銅面則只記錄銅厚;若重工面次為線路面則量測板內DUMMY銅區之銅厚及線寬記錄)。
檢查單位:
壓合檢修站。
檢查項目:
是否有棕化刮傷。
8.棕化不良
異?,F象:
經過棕化后的板面露銅或顏色不均。
原因分析:
1、內層板嚴重氧化。
2、酸性清潔槽清潔能力不夠。
3、棕化線生產溫度、濃度異常。
4、微蝕不足或微蝕過度。
5、棕化線停電造成棕化處理時間異常。
處理流程:
處理步驟與參數:
1、 將異常填寫于壓合課水平棕化線生產日報表。
2、 送棕化線重工或作報廢處理:
決定重工處理則進行4a-1的步驟。
作報廢處理則進行4b-1的步驟。
4a-1.按照棕化線正常生產程序生產,并記錄壓合課水平棕化線重工生產日報表(32123001-02)。
4a-2.用油性筆在板邊劃線作標記轉下制程。
4b-1.作報廢處理。
4b-2.檢驗人員將板子交課內賬目管理員,由賬目管理員負責按MRB流程將異常板送至MRB。
3、 重工辦法:
3-1.內層銅厚為0.5 OZ的板子不允許重工作業。
3-2.內層銅厚為1OZ允許重工一次,重工時100%依工單確認其阻抗線寬和面銅厚度,重工后內層銅厚不得低于1.0mil。
3-3.內層銅厚為2OZ允許重工一次,重工時100%依工單確認其阻抗線寬和面銅厚度,重工后內層銅厚不得低于2.4mil。
3-4.SAMPLE板重工前100%依工單確認其阻抗線寬和面銅厚度。
注:銅厚量測五個點,線寬量測稀疏區,密集區及阻抗線三個點(若重工面次為大銅面則只記錄銅厚;若重工面次為線路面則量測板內DUMMY銅區之銅厚及線寬記錄)。
檢查單位:
壓合自主檢查。
檢查項目:
是否有棕化不良現象。
9.裁板歪斜
異?,F象:
裁板后發現裁板裁偏。
原因分析:
1、人員作業不小心。
2、預迭時板與板之間的間距太少。
處理流程:
處理步驟與參數:
1、 將異常填寫于壓合課成型機生產日報表。
2、 繼續送下制程或作報廢處理。
決定繼續送下制程處理則進行3a-1的步驟。
作報廢處理則進行3b-1的步驟。
3a-1.決定繼續送下制程。
3a-2.剪角標記并在工單上注明異常及數量按正常流程轉下制程。
3b-1.作報廢處理。
3b-2.檢驗人員將板子交課內賬目管理員,由賬目管理員負責按MRB流程將異常板送至MRB。
檢查單位:
壓合檢修站。
檢查項目:
是否有裁板歪斜現象。
10.板厚偏厚
異?,F象:
壓合后發現板厚超出規格。
原因分析:
1、壓合程序用錯。
2、Tg達不到要求。
3、多放p/p。
4、p/p型號用錯。
處理流程:
處理步驟與參數:
1、 將異常填寫于壓合課板厚記錄表。
2、 報廢處理
作報廢處理則進行如下的步驟。
**3、**檢驗人員將板子交課內賬目管理員,由賬目管理員負責按MRB流程將異常板送至MRB。
檢查單位:
壓合檢修站。
檢查項目:
是否有板厚偏厚現象。
11.板內異物
異?,F象:
在壓合后板內有異物。
原因分析:
1、棕化后使用的墊紙受污染。
2、內層板面有未去處的殘膜。
3、推車烤漆掉入板內。
4、p/p上有異物。
5、無塵室的潔凈度不夠。
6、棕化水洗槽噴壓不足造成板面不潔。
處理流程:
處理步驟與參數:
1、 將異常填寫于壓合課檢驗日報表。
2、 繼續送下制程或作報廢處理。
決定繼續送下制程處理則進行3a-1的步驟。
作報廢處理則進行3b-1的步驟。
3a-1.決定繼續送下制程。
3a-2.作標記并在工單上注明異常及數量按
正常流程轉下制程。
3b-1.作報廢處理。
檢驗人員將板子交課內賬目管理員,由賬目管理員負責按MRB流程將異常板送至MRB。
3b-2.作標記并在工單上注明異常及數量按
正常流程轉下制程。
注:缺點不在線路下但長度超過200mil則作報廢處理。
檢查單位:
最終檢查課。
檢查項目:
是否有板內異物。
12.板厚偏薄
異常現象:
壓合后發現板厚超出規格。
原因分析:
1、壓合程序用錯。
2、Tg達不到要求。
3、少放p/p。
4、p/p型號用錯。
處理流程:
處理步驟與參數:
1、 將異常填寫于壓合課板厚記錄表。
2、 作報廢處理。
作報廢處理則進行如下的步驟。
**3、**檢驗人員將板子交課內賬目管理員,由賬目管理員負責按MRB流程將異常板送至MRB。
檢查單位:
壓合檢驗站。
檢查項目:
是否有板厚偏薄現象。
13.爆板
異?,F象:
在做信賴度測試發現層與層之間產生分層。
原因分析:
1、棕化線生產條件不符,造成露銅。
2、棕化烘干溫度不夠造成板面不干。
3、鋼板表面未烘干。
4、p/p表面不干。
5、壓機真空度異常。
6、Tg值異常。
7、壓機停電造成失壓。
處理流程:
處理步驟與參數:
1、 將異常填寫于熱應力試驗切片檢驗報表。
2、 作報廢處理:
作報廢處理則進行如下的步驟。
**3、**檢驗人員將板子交課內賬目管理員,由賬目管理員負責按MRB流程將異常板送至MRB。
檢查單位:
外層檢驗站、信賴度測試。
檢查項目:
是否有爆板現象。
14.毛邊
異常現象:
成型后或磨邊后發現板邊有毛邊。
原因分析:
1、成型機銑刀鈍化。
2、磨邊刀不鋒利。
3、磨邊刀具高度調整不當。
4、迭板片數太多。
處理流程:
處理步驟與參數:
1、 將異常填寫于壓合課后處理質檢統計表。
2、 繼續送下制程或作報廢處理。
決定繼續送下制程處理則進行3a-1的步驟。
作報廢處理則進行3b-1的步驟。
3a-1.決定繼續送下制程。
3a-2.用正常作業流程重新進行撈邊或磨邊,然后用1000目砂紙打磨后作剪角標記并在工單上注明異常及數量按正常流程轉下制程。
3b-1.作報廢處理。
3b-2.報廢面積小于50%則在異常處打上報 廢戳記轉下制程;報廢面積大于50%則整片送MRB處理。
檢查單位:
壓合檢修站。
檢查項目:
是否有毛邊現象。
15.白點
異?,F象:
在外層蝕刻后發現有白角白邊的現象。
原因分析:
1、壓機程序設定不當。
2、物料(PP)異常。
處理流程:
處理步驟與參數:
1、 將異常填寫于壓合課檢驗日報表。
2、 繼續送下制程或作報廢處理。
決定繼續送下制程處理則進行3a-1的步驟。
作報廢處理則進行3b-1的步驟。
3a-1.決定繼續送下制程。
3a-2.作標記并在工單上注明異常及數量按正常流程轉下制程。
3b-1.報告課長級以上主管。
3b-2.作報廢處理:賬目負責人按MRB流程將異常板送至MRB。
注:在成型區內如不在線路下則視同不在成型區內處理。
檢查單位:
外層檢修站、最終檢查課。
檢查項目:
是否有白點現象。
16.撈邊撈入成型區內
異?,F象:
在成型撈邊時撈入成型區內。
原因分析:
1、人員作業不小心。
2、撈邊程序用錯。
3、pin針未固定好。
處理流程:
處理步驟與參數:
1、 將異常填寫于壓合課后處理質檢統計表。
2、 繼續送下制程或作報廢處理。
決定繼續送下制程處理則進行3a-1的步驟。
作報廢處理則進行3b-1的步驟。
3a-1.決定繼續送下制程。
3a-2.剪角作標記并在工單上注明異常及數量按正常流程轉下制程。
3b-1.作單PCS報廢續流程處理。
3b-2.報廢面積小于50%則在異常處打上報廢戳記轉下制程;報廢面積大于50%則整片送MRB處理。
檢查單位:
壓合檢修站。
檢查項目:
是否有撈入成型區內。
17.壓合氣泡
異?,F象:
外層蝕刻后發現層與層之間有氣泡。
原因分析:
1、壓機程序不當。
2、棕化后板面未干。
3、鋼板表面未烘干。
4、P/P表面不干、P/P揮發分含量異常。
5、壓機真空度異常。
6、設計異常氣體不易排出。
7、壓機停電造成失壓。
處理流程:
處理步驟與參數:
1、 將異常填寫于壓合課后處理質檢統計表。
2、 作報廢處理。
作報廢處理則進行如下的步驟。
3、 由負責人按MRB流程將異常板送至MRB。
檢查單位:
壓合、外層檢驗站、最終檢查課。
檢查項目:
是否有氣泡。
18.板彎板翹
異常現象:
在壓合后發現板彎板翹的現象。
原因分析:
1、下熱壓后沒有及時進行冷壓。
2、p/p經緯方向搞錯。
3、工程壓合結構設計部合理。
處理流程:
處理步驟與參數:
1、 將異常填寫于壓合課后處理質檢統計表。
2、 作重工或作報廢處理。
決定重工送下制程處理則進行2a-1的步驟。
作報廢處理則進行2b-1的步驟。
2a-1.分析異常原因。
2a-2.使用板彎板翹壓機程序重壓
2a-3.按正常流程轉下制程。
2b-1.分析異常原因。
2b-2.作報廢處理:
檢驗人員將板子交課內賬目管理員,由賬目管理員負責按MRB流程將異常板送至MRB。
檢查單位:
板翹測量。
檢查項目:
是否有板彎板翹的現象。
19.板面刮傷
異常現象:
壓合后發現板面刮傷。
原因分析:
1、剪床的托料未開。
2、磨邊線滾輪刮傷。
3、成型機上下料刮傷。
4、人員未按照Handling作業規范作業。
5、鋼板上異物。
6、設備異常造成卡扳。
處理流程:
處理步驟與參數:
1、 將異常填寫于壓合課后處理質檢統計表。
2、 繼續送下制程或作報廢處理。
決定繼續送下制程處理則進行3a-1的步驟。
作報廢處理則進行3b-1的步驟。
3a-1.決定繼續送下制程。
3a-2.剪角作標記并在工單上注明異常及數量按正常流程轉下制程。
3b-1.作單PCS報廢續流程處理。
3b-2.報廢面積小于50%則在異常處打上報廢戳記轉下制程;報廢面積大于50%則整片送MRB處理。
檢查單位:
壓合檢修站。
檢查項目:
是否有板面刮傷。
20.面銅不均
異?,F象:
減銅后發現板面面銅不均OUT SPEC異常。
原因分析:
1、藥水濃度異常。
2、噴嘴堵塞異常。
3、壓力異常。
4、線速異常。
處理流程:
處理步驟與參數:
1、 將異常填寫于壓合薄銅線生產日報表。
2、 繼續送下制程或作報廢處理。
決定繼續送下制程處理則進行3a-1的步驟。
作報廢處理則進行3b-1的步驟。
3a-1.決定繼續送下制程。
3a-2.剪角作標記并在工單上注明異常及數量按正常流程轉下制程。
3b-1.作單PCS報廢續流程處理。
3b-2.依 MRB流程將異常板整片送MRB報廢處理。
檢查單位:
壓合檢修站。
檢查項目:
是否有面銅不均。
-
CCD
+關注
關注
32文章
882瀏覽量
142336 -
PCB板
+關注
關注
27文章
1448瀏覽量
51734 -
HDI
+關注
關注
6文章
200瀏覽量
21316 -
PCS
+關注
關注
1文章
142瀏覽量
14689
發布評論請先 登錄
相關推薦
關于RK3568-ANDROID11-BOARD_HAVE_DONGLE報錯的原因及其解決辦法
電腦開機啟動時提示(顯示)NTLDR文件丟失解決辦法及原因分
壓敏電阻燒壞的原因后果及解決辦法
音箱沒聲音的原因和解決辦法
內存條兼容異常問題的原因及其解決辦法
空氣開關跳閘常見原因、解決辦法和卸下步驟
PCBA加工焊點拉尖產生的原因及解決辦法
電感嘯叫的原因和解決辦法
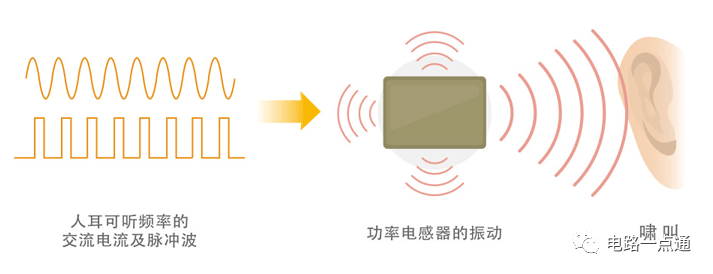
評論