純電動汽車由于動力電池和電驅系統取代傳統燃油和發動機,整個系統電壓從傳統12V升高到300V以上系統電壓等級,高壓母線充電及放電電流達到200A以上。因此在設計整個高壓電氣架構時,不僅要考慮整車成本、驅動性能和充電時間要求,還需要考慮整個高壓系統安全,確保駕乘人員的安全。
文章基于目前典型純電動汽車高壓電氣架構,提出了一種全新高壓架構設計方案。
01純電動汽車高壓電氣架構功能要求
純電動汽車高壓部件包括電池、電驅、電力電子及充電部件。如圖1所示,電池是整個高壓系統的能源,為電驅及電力電子部件提供能量。充電系統包括慢充和快充,為電池提供能量。合理的高壓部件方案及集成設計,可以優化整個高壓系統的導線、繼電器、熔斷絲及接插件數量。另外,整個高壓架構需滿足高壓安全要求,高壓互鎖、主被動放電、絕緣監測、預充電、繼電器監測和線路保護等功能,合理的設計可滿足安全的需求并實現成本的最優。
02高壓電氣架構設計
2.1 高壓架構設計輸入
高壓架構設計要求包括整車性能及系統安全要求,整車性能包括加速、續航里程、充電時間、低壓用電功耗及熱系統用電功耗等。根據整車性能相關需求,通過計算仿真確定高壓動力電池電壓范圍,額定輸出電壓,電池總能量,電機功率,慢充及快充功率,DC /DC、PTC、ACCM、Heater等高壓部件功率。表1是根據整車性能要求仿真的直流母線瞬態電流信息,供導線及熔斷絲選型設計。
2.2 典型純電動汽車高壓電氣架構分析
圖2是產品車A高壓拓撲圖,整個高壓系統通過HPDM模塊實現高壓能量的分配,各模塊相對獨立,無集成設計。優點:滿足系統安全要求,由于各模塊獨立設計,可實現獨立控制和診斷。缺點:系統成本高,各模塊需要獨立高壓線束連接及熔斷絲保護;增加整車布置空間及整車質量。
2.3 高壓架構方案設計
1) 高壓零部件整體設計策略。為保證整個系統成本及空間的最優,采用電池集成BDU、電機控制器和電機集成、DC /DC、OBC及PDU集成的整體設計方案。如圖3所示,這種方案實現了零部件高度集成、空間布置及成本最優化。
2) 驅動系統設計策略。驅動系統采用電機和電機控制器集成的設計策略,省去獨立的三相線束。前期進行了驅動單元直接從電池出線的方案研究。由于功能安全要求,驅動單元直接從電池出線,IPE需增加一路熔斷絲保護,最終從成本、熔斷絲失效風險和電池包開蓋維修風險等因素綜合考慮采用Option1。DU接口分析如表2所示。
3) 充電系統設計策略。充電系統設計快慢充功能,由于IPE集成OBC,慢充接口直接連接IPE;快充連接電池,通過BDU內部繼電器給電池模組充電。
4) 電池設計策略。電池內部集成BDU,主正負繼電器和快充繼電器并聯實現驅動和快充切換。基于成本和安全綜合考慮,采用低壓MSD代替傳統高壓MSD的方案。
對比圖2產品車A高壓拓撲圖,該方案優點是采用了電驅及IPE的集成設計方案,高壓零部件成本降低,另外節省了高壓導線及接插件數量,降低了整車布置空間及整車質量。
2.4 高壓架構系統安全設計
1) 放電及絕緣監測設計策略。通過電機控制器加電機主動放電實現5S系統電壓從300V降低到60V以下,保證人員觸電安全;整個高壓系統設計有主被動絕緣監測功能,實現上電和下電時的系統絕緣監測,確保絕緣失效時的故障報警及系統斷電保護。
2) 預充設計策略。BDU內部設計有預充回路,在200~300ms時間內預充整個高壓回路到正常高壓值,確保系統上電安全。
3) 高壓線路保護策略。每個高壓線路設計有線路保護功能,通過熔斷絲保護,確保線路過流斷開。
4) 高壓母線紋波及UCG設計要求。通過軟件仿真分析整個直流母線上不同頻域的電壓紋波,確保所有高壓部件工作正常。另外通過軟件分析非受控再生制動下的最高反向電動勢電壓,確保直流母線零部件及電機控制器交流側不受影響。
03結論
本文首先通過分析純電動汽車高壓架構功能要求,對比目前典型純電動汽車高壓電氣架構。通過高壓架構方案設計和高壓架構系統安全設計兩方面,提出了一種全新高壓架構設計方案,通過集成化的設計方案和最優的拓撲設計結構,實現成本最優并滿足系統安全要求。研究表明,此方案滿足系統功能和安全要求,空間布置簡單且質量降低,系統成本低,可實現平臺化推廣。
審核編輯 :李倩
-
動力電池
+關注
關注
113文章
4535瀏覽量
77670 -
架構
+關注
關注
1文章
514瀏覽量
25478 -
電驅系統
+關注
關注
0文章
113瀏覽量
2392
發布評論請先 登錄
相關推薦
混合動力汽車電動汽車中高壓電流感應的挑戰及解決辦法
新能源電動汽車高壓線束技術規范
優化電動汽車的結構性能
如何解決混合動力汽車/電動汽車中的高壓電流感應設計難題
電動汽車高壓電氣系統安全設計原理及概括
解決混合動力汽車/電動汽車的高壓電流感應設計難題
純電動汽車高壓線束成本優化
使用了高壓電池的電動汽車安全性如何?

高壓電氣系統驗證
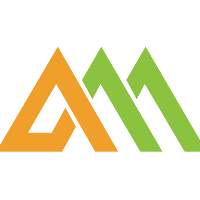
評論