本文簡單介紹了純電動汽車高壓線束及生產工藝,并對高壓線束成本構成及物料成本構成進行了詳細分析。研究了高壓系統架構優化、高壓線束布置優化、高壓線束物料優化、平臺化及標準化設計的降成本方法,對高壓線束成本優化意義重大。以下為正文。
引言
目前國內新能源汽車市場競爭越發激烈,隨著國產特斯拉的降價和大眾的電動車型加入,后續競爭會更加白熱化。汽車企業只有憑借高品質、高價值的產品和領先的技術,才能在激烈的新能源汽車市場中占有一席之地。各大車企在技術不斷創新的同時,也在重點關注零部件成本優化,提高產品力和提升企業競爭力。高壓線束是純電動汽車中高價值的零部件,也是成本優化的主要零件。
高壓線束簡介及生產工藝
高壓線束將高壓系統上各個部件相連,作為高壓電源傳輸的媒介,是電動汽車上動力輸出的主要載體,主要用于傳輸電能及屏蔽外界信號干擾。高壓線束具有高電壓、大電流、防護等級高及抗電磁干擾等特點,是純電動汽車高壓系統的神經網絡,是整車性能和安全的關鍵零部件。純電動汽車高壓線束一般分為動力電池高壓線束、電機控制器高壓線束、快充插座線束、慢充插座線束、空調系統線束及充電高壓線束,其中充電高壓線束是指連接高壓配電盒到車載充電機、空調壓縮機和動力電池包加熱器之間的線束。
高壓線束主要由高壓連接器、高壓線纜、包覆物(膠帶、熱縮管、波紋管、耐磨自卷管等)、護板等組成。高壓線束生產工藝流程主要有裁線、附件預裝、端子壓接/ 超聲波焊接、屏蔽壓接、線束總裝及電檢。
高壓線束成本構成分析 高壓線束成本由物料成本、加工費、包裝運輸費及利管費構成,高壓線束物料成本主要由線束技術方案決定,其中加工費包含了人工成本、動力費、設備折舊費及低值易耗品等費用。以下為某車型高壓線束成本構成比率圖(見圖1)及高壓線束物料成本構成比率圖(見圖2),高壓線束物料成本占線束總成本比率約73.8%。需要不斷通過優化設計及優化生產工藝等方法,降低高壓線束成本。
圖1高壓線束成本構成占比
圖2高壓線束物料成本構成占比 高壓線束成本優化研究 汽車行業企業降成本主要有三類方法,規模類、供應商協作類和技術類降成本,其中技術類降成本是降低成本最有效且可持續的方法。目前技術降成本的方法主要有以下三種:成本標桿法、管理技術法和技術手段法。 一般情況下技術手段法包括減少冗余功能、國產化率提升及規格統一平臺化等方法。在純電動汽車高壓線束降成本活動中,此次主要研究用技術手段法從以下幾個方面來進行高壓線束成本優化。
01高壓系統架構優化
在純電動汽車上,高壓零部件有動力電池、三合一(電機控制器+ 驅動電機+ 差減)、PDU(高壓配電盒)、ECP(電動壓縮機)、二合一(IPS=OBC+DC-DC)、HVH( 電池采暖)、PTC(乘員采暖)、慢充座(ACInlet)、快充座(DC Inlet)及高壓線束等,這些部件組成了整車的高壓系統。純電動汽車高壓系統架構優化的好,可大幅減少接插件的使用數量和冗余的高壓線束。以某項目高壓系統架構優化為例,優化前高壓線束系統架構中PDU 僅作為電源分配功能模塊存在,沒有整車功能性能相關模塊,詳見圖3。
圖3優化前高壓系統架構圖
PDU 的獨立,使得高壓線束系統中轉接數量增加。HVH和PTC 兩個功能相近,使得高壓線束回路數量增加。快慢充插座布置在左右后側圍,距離用電器接口(電池快充接口在前部,充電機慢充接口在前艙)太遠,使高壓線束長度偏長。經過研究分析,實現功能的電器元件為僅用于連接功能的銅排和電源保護功能的熔斷器,與其他用電器集成難度小。PDU 與IPU 集成可以取消一個高壓配電盒總成,同時可以節省掉一套電機控制器線束(約1.5m 的50mm2 導線和兩對φ8mm 端子接插件),可帶來的降成本效益明顯。HVH 和PTC 兩個功能相近,這兩個功能合并,高壓線束可以減少一個回路(約1.5m的3mm2 導線和兩對片寬2.8mm 端子接插件),高壓系統架構優化后如圖4 所示。
圖4優化后高壓系統架構圖
通過此高壓系統架構優化,減少了4 個高壓連接器和兩根高壓線束,高壓線束能降成本約730 元。
02高壓線束布置優化
高壓線束布置需要根據車型進行不斷的優化,優化后可以減少高壓線纜的使用等,進一步降低成本。以某車型快慢充口布局優化為例,優化前快慢充口均布置在左右后側圍,快慢充線束長度過長,其中慢充線束長度約4.5m,快充線束長度約4m,造成快慢充高壓線束成本高。優化后將充電口布置在左右翼子板處,靠近充電機和電池包布置,減少高壓線束長度。優化前后布置圖如圖5、6 所示,通過此高壓線束布置優化能降低成本約260元。
圖5優化前快慢充口布置位置圖
圖6優化后快慢充口布置位置圖
03高壓線束物料優化
高壓線束成本構成中,物料成本占比最高,對目前的現狀進行分析,目前高壓線束物料優化方向主要為充電插座一體式設計、高壓連接器國產化、高壓線纜線徑優化及物料一對多可選優化。
03.1充電插座一體化設計優化
充電插座優化前為分體式設計,成本較高,優化前分體式充電插座如圖7 所示,含快充充電插座和慢充充電插座。通過充電插座按照平臺化方案進行開發設計,對所有項目的充電插座主體結構進行固化,以最大限度降低開發成本,優化后一體式充電插座詳見圖8 所示。通過此優化可減少一套法蘭模具從而使高壓線束總成成本下降約8 元。
圖7優化前分體式充電插座
圖8優化后一體式充電插座
03.2高壓連接器國產化近年來高壓連接器行業發展迅速,涌現出了一批優秀的國內高壓連接器品牌供應商。優化前主要利用TE 等外資品牌的高壓連接器,通過高壓連接器國產化不斷優化,用國產品牌如Luxshare、Ebusbar 等進行國產化替代,對高壓連接器降成本意義重大,如下表1 所示為高壓連接器國產化示范案例。 表1高壓連接器國產化示范案例
03.3高壓線纜線徑優化
通過對法規的解讀、對標及統計云端大數據等措施,來優化高壓線纜線徑。針對具體的高壓線纜,往往可以通過截面、溫度要求、柔韌性以及屏蔽效果的優化來量體裁衣,避免過度尺寸和過度的組件。以快充高壓線纜為例,優化前線纜線徑為70mm2,優化后為50mm2,均能滿足實際充電需求。
03.4物料一對多可選優化
高壓線束物料一對多可以充分調動tier1 供應商的積極性以及運用tier 1 供應商自己的供應鏈優勢,選擇成本最優方案進行供貨。以物料成本中占比較高的高壓線纜為例,目前主要規格高壓線纜按照一對多思路按照高壓線纜標準進行開發,每一種規格線束廠有多個規格可選,其中各回路具體應用導線情況,需要根據整車實際負載情況確認。通過不斷的優化設計,目前很多物料可以實現一對多可選,以下表2 僅為部分物料一對多示例。
表2物料一對多示例 04平臺化及標準化設計從整車線束原理和原材料等方面進行平臺化和標準化設計,可以大幅度縮短整車線束設計階段開發周期,減少重復驗證試驗,降低線束成本。通過線束物料的不斷平臺化和標準化,減少了物料的種類,提高單一物料的數量可起到規模化效應,對于物料降低成本意義重大。經過研究與分析,通過二級物料(連接器、電纜、輔料等)的平臺化及標準化方案可大幅降低高壓線束物料成本。以下為高壓插件平臺化示例,在滿足同等電性能的情況下,電池包鋁合金面板上的開孔尺寸能同時安裝不同品牌(TE、Luxshare)的板端連接器,詳見圖9、10、11。此平臺化設計,通用性強。
圖9電池包鋁合金面板上的開孔尺寸
圖10TE 品牌HVP2P800 板端
圖11Luxshare 品牌 HVP2P800 板端 總結與展望 純電動汽車高壓線束由于具有大電壓、大電流、大線徑導線數量多等特點,高壓線束面臨著布線、安全、屏蔽、重量及成本等挑戰。高壓線束作為高價值的純電動汽車的零部件,通過研究不斷的成本優化,可為整車降成本做貢獻。降成本工作是一個不斷優化持續的活動,后續還需不斷優化,從而使整車成本降至最低,向客戶提供更有競爭力的產品。
審核編輯 :李倩
-
神經網絡
+關注
關注
42文章
4771瀏覽量
100767 -
電機控制器
+關注
關注
20文章
525瀏覽量
32066 -
線束
+關注
關注
7文章
976瀏覽量
25989
發布評論請先 登錄
相關推薦
Aigtek汽車ATX-6256高壓線束測試儀新能源汽車測試
ATX-6000系列高壓線束測試系統
高壓線性方案
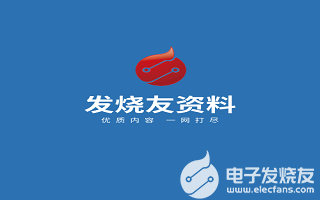
純電動汽車高壓線束成本優化
新能源汽車高壓線束的多方案對比
新能源汽車的高壓線束設計方案
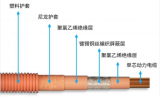
純電動汽車高壓線束成本優化策略探討
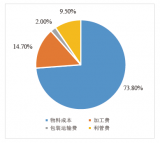
汽車高壓線束如何應對電磁干擾
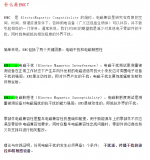
新能源汽車高壓線束設計方案分享
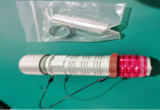
評論