貼片機的實裝動作都是通過我們編寫的程序實現的,而貼片程序編制的好壞,將直接影響生產線(即設備)能力的發揮。那么作為編程人員,為了使貼片程序能最大限度的發揮出設備的貼裝性能,需要掌握哪些技巧呢? 本篇我們就以接受過松下 CSE 診斷咨詢服務的一家客戶(以下簡稱 X 工廠)的實際案例,來說明貼裝程序優化的思路和方法。生產觀察、課題抽出我們在 X 工廠選擇產量大、生產周期長,且具有代表性的機種作為分析和改善的對象。首先,了解代表機種生產的線體配置和貼片 Cycle Time(生產節拍)的情況(如圖 1)。從收集到的數據中我們可以計算出線平衡為:42/60.5*100%=69%;CM602-1 的 CPH 為 48,853 點/小時,CM602-2 的 CPH 為 21,967 點/小時。
圖 1:改善前 X 工廠機器配置、機種 Cycle Time 和 CPH 信息
通過我們在現場的連續貼裝觀察,發現了以下問題點:料架的排列分布不合理導致吸嘴的同吸率不高,一次元件吸著存在兩次識別的情況,基板 Mark 點識別順序不合理。
同時,通過編程電腦對程序進行了診斷,也發現了其他的一些問題點:無源元件沒有開啟無極性判別功能,編輯元件只設置單個型號吸嘴,用量大的元件沒有進行元件拆分。
根據以上觀察發現的問題點,松下 CSE 人員與 X 工廠的編程人員進行了溝通,發現他們對于設備的機構和動作行程不明確,在編寫時,對于程序的手動優化無清晰的概念,以及對于如常規元件可添加的吸嘴型號無標準,工廠對于程序優化的結果也無明確的要求。
課題分析、改善提案
針對以上問題點,接下來我們逐一進行分析并提出相應的改善提案:課題一:料架分布不合理,導致吸嘴的同吸率不高
分析:CM602 設備 12 吸嘴的間距為 10.5mm,8 吸嘴的間距為 21mm,Double Feeder 上 L/R 的間距也為 10.5mm,所以當料架設置合理并符合同吸要求時,機器就會同時吸著,從而減少移動和吸料時間。以8 頭為例(如圖 2),吸嘴頭首先吸完 A-D 站的 6 顆料,接著再吸 E-H 站的 6 顆料。當設置不合理時,編程人員未手動設置空料站時,就會增加 Head 移動的時間(如圖 3),吸嘴頭首先會吸取中間料架的料,最終再吸取兩邊剩余的料,這樣就會增加 Head 移動時間,并導致貼裝時間延長。同樣在 12 吸嘴頭時,也要對料盤相應的設置來提高同吸率(如圖 4)。另外在料站位置擺放時盡量靠近 7 至 20 站,這個位置距離相機最近,減少頭部行程。
改善提案:對編程人員進行設備機構的教育訓練,掌握與編程相關的設備知識。如設備貼裝頭之間的間距,料架與料架的間距,減少貼裝頭移動距離的方法,同吸時相鄰元件是否有厚度差要求等。在接受培訓后要在程式編寫規定中添加高速機 CHIP 元件的同吸率要求(如同吸率 85%以上),以保證優化的效果。(程式同吸率在 PT 編程電腦中的解析工具進行查看)
課題二:一次元件吸著存在兩次識別
分析:CHIP 元件設置的 REF 值不一致,存在反射和透射認識兩種方式,導致兩次識別(如圖 5)。
改善提案:制定元件 REF 值識別模式參考表,編程人員需熟練掌握不同 REF 值的識別方式,優化時可合理擺放料架位置,統一把相同識別方式的元件放在同一 Table 或是設置元件分開吸取,減少兩次識別時燈光切換和識別的時間(如圖 6)。
課題三:基板 Mark 點識別順序不合理
分析:編程人員不清楚基板 Camera 移動軌跡會造成貼片時間上的損耗。目前的設置是識別相機在識別 Mark 時,先識別右下角,后識別左上角,再返回至第一 Mark 附件貼裝。我們知道生產中每塊基板貼裝完畢后,Table1&3 的基板相機都是移動并停留在第一 Mark 的位置,而移動到第一識別位置的時候,也是基板傳入的時間。而我們根據第一點的貼裝位置更改識別順序,就可以減少 Head 頭移動的距離縮短時間(如圖 7)。
改善提案:對不同基板需實際觀察 Mark 識別的順序與貼裝是否合理,特別是大基板生產時,要選擇合理基板識別順序,減少無效移動時間。
課題四:無源元件沒有開啟無極性判別功能
分析:對于無極性元件,在程式編輯時,需開啟此功能(如圖8)。在貼裝過程中,可減少或避免 Head 角度旋轉的時間。
改善提案:編程人員在元件庫編寫時對于無源元件需開啟此功能,并確認元件庫中所有無源元件,同時在程式編寫規定中添加此要求。
課題五:編輯元件時只設置單個型號吸嘴
分析:元件在選用吸嘴時可同時配置高速機貼裝的吸嘴和泛用機貼裝的吸嘴,并且可添加符合元
件吸著、貼裝要求的多個型號吸嘴。這樣可減少程序優化時間和優化平衡。
提案:建立起符合廠內元件要求的吸嘴添加標準文件,在編程時可按照此要求對元件添加生產用吸嘴(如圖 9)。同時用于吸著、貼裝元件的吸嘴需經過實際生產確認,要在保證品質的情況下才可考慮生產性。
課題六:用量大的元件沒有進行拆分
分析:貼片時,元件逐個吸取,導致貼片時間長。對用量大元件進行多盤設定,并設置在同一 Table的相鄰幾站,提高同吸率,并且在結工單,料盤不夠時,無需移動站位,機器會自動到有料的一站吸取。
提案:在程序編輯時,對用量大,優化時會產生瓶頸的,或同吸率低的情況下,設置多料盤(如圖 10)。設置的數量可根據程序提示,也可自行修改。同時對于多料盤設置的要求需在程式編寫規定中制定。(如多料盤設置最多可設置三盤,需同一 Table 相鄰幾站等)
以上就是針對 X 工廠程序優化方面發現的問題點提出的改善提案。同時在程序優化時對另外的幾個方面也需要考慮:
1. 貼裝的元件厚度要從低到高,可減少貼裝時元件上下移動的時間。
2. 對于同吸率高的 Table 可設置在后側,因為當固定邊在前側時,后側的Y 軸移動距離比前側長,通過同吸來彌補 Y 軸的移動時間。
設置貼裝(turn)來回數時盡量一致。優化時 Table2&4 可以設置多一個來回,因為 Table1&3 要對基板 Mark 做識別(可視為一個來回)。
總結改善成果
通過對程序的重新優化,Cycle Time 從 60.5s 提升到了 54s(如圖 11),Cycle Time 提升了 10.7%,線平衡達到了:41/54*100%=76%;CM602-1 的 CPH 為 54,831 點/小時,CM602-2 的 CPH 為 21,867 點/小時。
再通過優化前后對比(如圖 12),一條生產線每月可為 X 工廠增加 45,864 元的收益,效果非常明顯。
在給 X 工廠帶來直接收益的同時,也建立起了程序優化的標準。編程人員根據這個標準對工廠內所有的程序進行重新優化,降低了貼片程序的 Loss 率,從而提高了生產線的效率。
備注:工廠在判別程序是否為最優化時,通常用線平衡、CPH 以及單點貼裝時間。單點的貼裝時間的計算方式為:Mark 點識別完畢后元件開始貼裝到最后一點貼裝完畢的時間/貼裝點數。對計算出的單點貼裝時間與標準指標進行比對,判定程序優化的程度,并可確認是否有再優化的空間。
審核編輯 :李倩
-
貼裝
+關注
關注
0文章
91瀏覽量
16893 -
編程
+關注
關注
88文章
3637瀏覽量
93924
原文標題:【干貨】松下CM602生產線效率與效益提升改善報告(2023精華版),你值得擁有!
文章出處:【微信號:SMT頂級人脈圈,微信公眾號:SMT頂級人脈圈】歡迎添加關注!文章轉載請注明出處。
發布評論請先 登錄
相關推薦
如何選擇SMT生產線
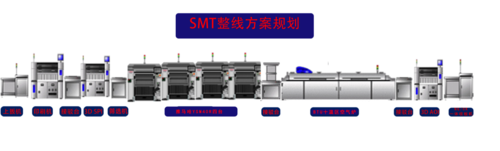
回流焊生產線布局規劃
特斯拉將暫停上海工廠部分生產線以煥新Model Y
LP-SCADA系統應用效益
SMT生產線布局設計技巧
SMT生產線的維護與保養
效率 智能 品質:在線測徑儀為產線注入活力!
初創公司借助NVIDIA Metropolis和Jetson提高生產線效率
生產線自動化革新:視覺上下料技術的精準應用與效率飛躍
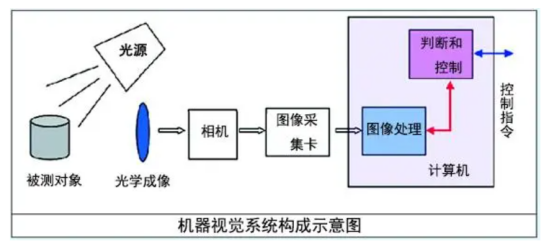
評論