#案例1
產線控制圖異常偵測與優化
線上控制圖是工廠用來偵測產品規格是否在可接受范圍內的工具,當產品規格超出標準控制限之外 ,工廠需要立即檢測產線上的制程狀況,并且采取緊急措施將產品的報廢量降到最低。
在應用材料(Applied Materials)公司,某客戶在 CIS產品上的線上控制圖發生了兩周內偵測值超過控制線標準,導致設備需要停止生產,并做相關清潔工作的情況。然而,每一次的清潔流程都將造成工廠高成本的支出,如何降低此種問題發生的頻率呢?
首先,工程師團隊使用應用材料公司的光訊號偵測系統來收集數據。然后,利用 JMP軟件的 Box Plot(箱線圖), Line Plot(線圖), Distribution Plot(分布圖), Graph Plot(繪圖)等多種功能對數據做初步檢視,找出異常數據點及離群值。
探索完原始數據的分布趨勢后,利用 JMP軟件的ANOVA功能來分析所有產品之間有無差異性。接著,使用 JMP軟件的 Sample Power Test決定采取樣品數量是否足夠采信再使用 JMP的 Equivalent Test, Comparison Test判別兩兩產品之間的差異性。
在確定了差異性顯著后,工程師團隊使用 JMP的 Fit Y by X功能得出回歸模型,將過往產品收集的原始數據利用此模型重新評估。
最終實驗結果顯示,應用材料公司的光訊號偵測系統能有效地幫助線上控制圖的數據維持在目標上,并且延長清潔設備的周期時間,降低了工廠成本及產品報廢數量。
#案例2
改進量測重復性與再現性GRR
任何有效的數據分析都離不開數據質量的保障,數據一般情況下是測量的結果,而在高精度的半導體高科技制造業更是如此,其特別強調測量數據本身的質量和相應的測量系統分析,高質量的數據是精細化質量管理的前提條件。
在應用材料公司,工程師想要改進擴散器(Diffuser)孔徑尺寸的針規(Pin Gauge)測量能力。那么,該如何優化此項目呢?
工程師團隊決定采用JMP平臺進行分析。
首先,使用 C&E Diagram 列出測量誤差的潛在根本原因,并利用 DOE 樣本量和功效計算所需的測量分辨率 (10%)。
在找到合適的因子之后,使用 Bias and Linearity 確保 GRR 評估前測量精度的標準化程序實施。
隨后,工程師分別對操作員和零件使用單因子方差分析來識別操作員之間的變異并確定尺寸范圍內零件的選擇,進一步闡述了GRR標準P/T比(Precision to Tolerance)而非P/TV比(Precision to Total Variance)的原因。
接著,使用 GRR 雙向方差分析來檢測由于過程均勻性而不是由于測量設備的可重復性引起的零件對操作員交互作用。進行Design Choice survey,檢測接受者在閱讀測量標準作業流程SOP前后對關鍵測量因素的差異,以提高量測工具的再現性。
最后,使用SPC Chart監測GRR的穩定性,計算GRR P/V比的制程長期標準偏差,確定制程合理分組,從而成功改進項目。
審核編輯:劉清
-
鋰電池
+關注
關注
260文章
8108瀏覽量
170134 -
JMP
+關注
關注
1文章
17瀏覽量
12601 -
CIS
+關注
關注
3文章
194瀏覽量
29617 -
SPC
+關注
關注
1文章
55瀏覽量
12155
原文標題:案例學習 | 基于JMP軟件偵測產線控制異常及改進GRR
文章出處:【微信號:半導體封裝工程師之家,微信公眾號:半導體封裝工程師之家】歡迎添加關注!文章轉載請注明出處。
發布評論請先 登錄
相關推薦
分布式 IO 模塊助力沖壓機械臂產線實現智能控制
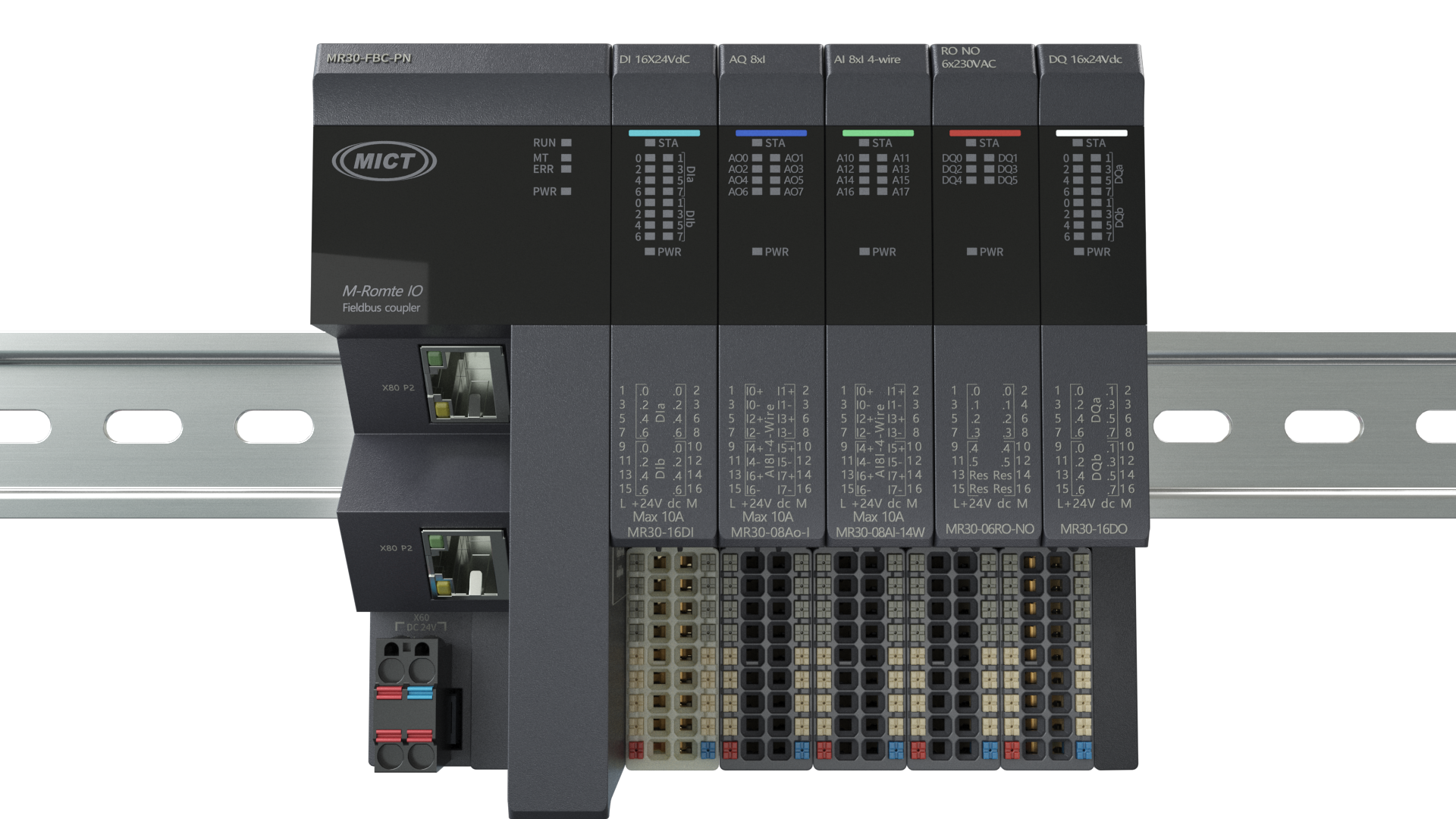
SMT產線固定讀碼器的應用效果
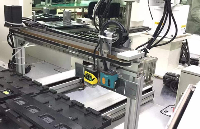
上揚軟件攜手合作伙伴打造智能化生產制造產線
重型工程機械產線潤滑系統遠程監控物聯網解決方案
產線AGV和倉儲AGV到底有什么不同?
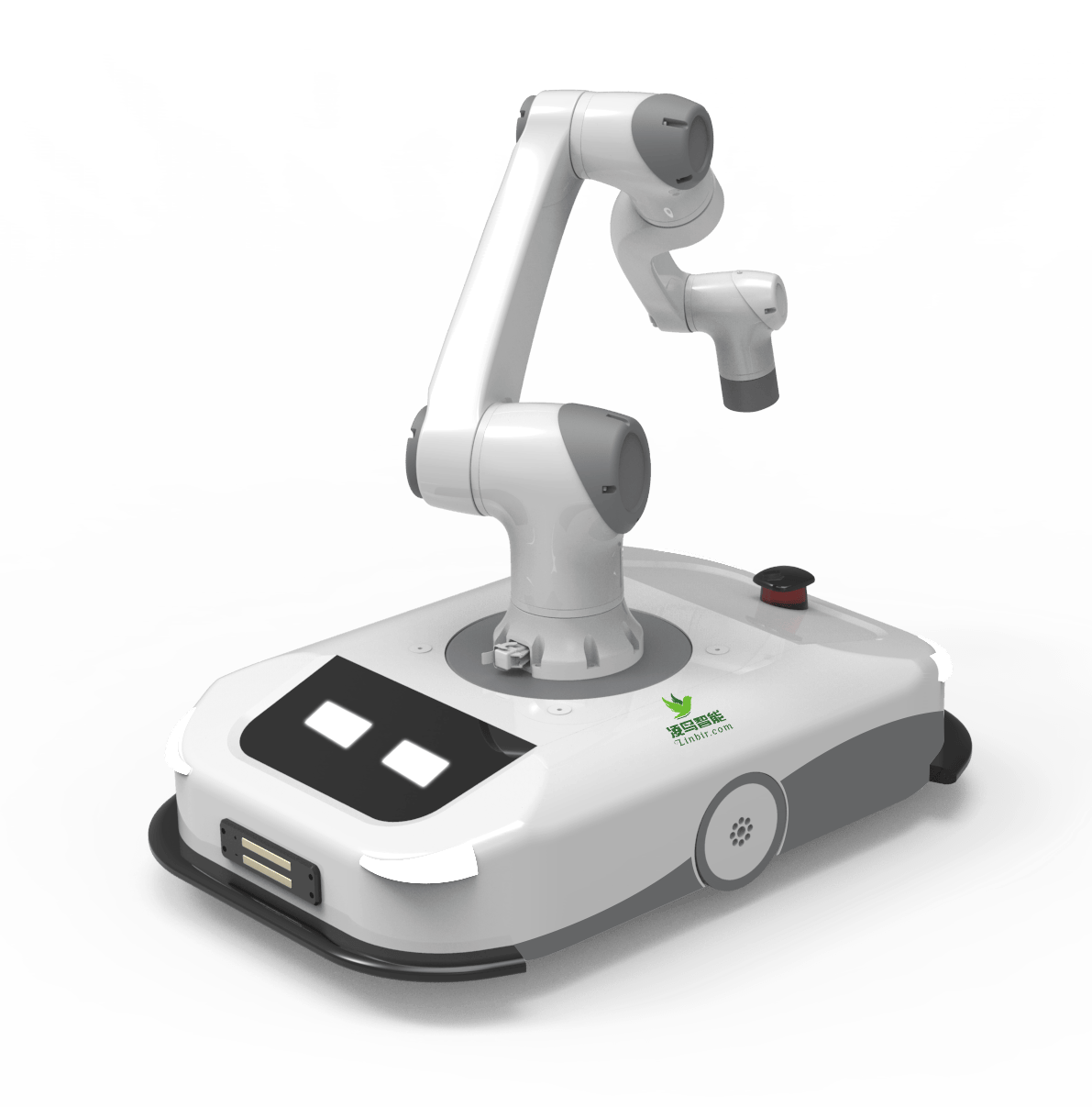
可重構柔性裝配產線:AI邊緣控制技術的嶄新探索
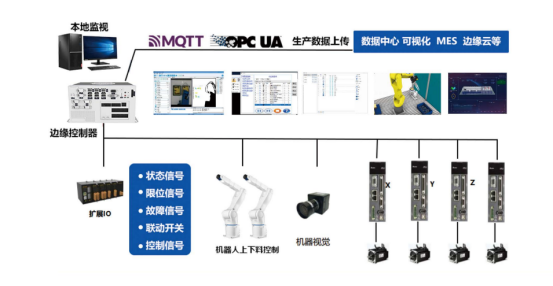
可重構柔性裝配產線整體解決方案,智能化生產轉型的引領者
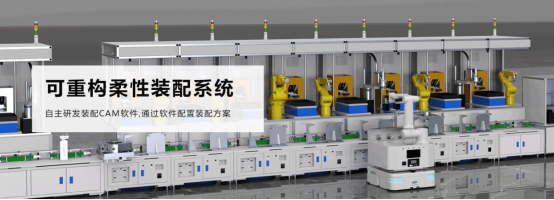
CClinkie轉Profinet 在包裝機產線應用
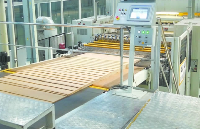
評論