使用化學機械拋光(CMP)方法對碳化硅晶片進行了超精密拋光試驗,探究了滴液速率、拋光頭轉 速、拋光壓力、拋光時長及晶片吸附方式等工藝參數對晶片表面粗糙度的影響,并對工藝參數進行了優化,最終 得到了表面粗糙度低于0.1 nm的原子級光滑碳化硅晶片。
0 引言
與傳統半導體相比,單晶碳化硅作為新型半導體 材料,具有禁帶寬度大(3.3 eV)、擊穿電場高(0.8~ 3.0 MV/cm)、熱導率高(3.0~4.9 W·cm-1K-1)、飽 和電子漂移速率高(2.0×107 cm/s)等突出優點,可 滿足在高頻高功率電子器件方面的需求,傳統半導 體無法代替。因此,單晶碳化硅在電子元器件的應 用成為未來發展的必然趨勢,而碳化硅晶片的生長 技術又是器件制作的前提,如何將碳化硅晶錠制作 成符合要求的碳化硅晶片就成為了關鍵環節。
單晶碳化硅具有超高硬度,其莫氏硬度高達 9.5,加工難度十分巨大。碳化硅具有極其穩定的化 學性質,在常溫下不與任何已知的強酸或強堿等化 學試劑發生反應,且碳化硅的壓縮強度遠大于其彎 曲強度,材料具有較大的硬脆性,導致碳化硅加工難度巨大。目前國際上部分發達國家已具有成熟的 碳化硅單晶襯底的制備技術,其中美國碳化硅單晶 襯底技術最為成熟,壟斷了國際上80%的市場,而國 內則處于起步狀態,距離國際頂尖水準還有較大差 距,因此打破國際技術壟斷,制備超光滑的碳化硅襯底晶片,具有十分重要的意義。
為得到表面超光滑的碳化硅襯底晶片,用改造 后的設備對碳化硅晶片進行了超精密拋光試驗,得 到了表面粗糙度低于0.1 nm的超光滑碳化硅襯底晶 片,并探討了晶片的粘貼方式、拋光壓力、拋光時 長等參數對晶片表面粗糙度的影響。
1 碳化硅晶片超精密拋光試驗
碳化硅單晶襯底的制作需要經過切割、研磨、 拋光等一系列工藝,最終得到超光滑的碳化硅襯底晶片。其中,拋光又分為粗拋和精拋:粗拋的目的 是將襯底表面粗糙度加工至納米級別;精拋是碳化 硅襯底晶片制作的最后一步工藝,其直接關系到加 工之后的襯底能否投入生產。精拋的目的是進一步 改善碳化硅襯底的表面質量,得到超光滑表面質量 的晶片,通常要求表面粗糙度低于0.2 nm以下。
獲得超光滑表面碳化硅晶片的拋光方式中,包 括電化學拋光(ECMP)、摩擦化學拋光(TCP)、化 學機械拋光(CMP)等,其中化學機械拋光將化學 拋光技術和機械拋光技術相結合,是當前國際上公 認,可實現全局平坦化和超光滑無損傷納米級表面 的加工方式。試驗中使用自主研發的設備對碳化硅晶片進 行CMP,如圖1所示。拋光盤使用質地較硬的鑄鐵 材質,具有良好面形,表面粘貼的拋光布使用無紡 布,拋光頭下面帶有真空吸附功能,通過調節真空 吸附壓力可以將陶瓷盤牢牢吸附住,此外,設備還 具有滴液調節及攪拌功能,可以根據需求對拋光液 的進給速率進行調節和攪拌。
拋光液采用粒徑在100~300 nm范圍內的SiO2磨粒 作為拋光介質,使用KMnO4作為催化劑和氧化劑, 同時加入KOH溶液用來調節拋光液的PH值使其呈堿 性,其反應原理如圖2所示,拋光液中SiC與氫氧基進 行化學反應,在氧化劑及催化劑作用下,SiC表面生 成SiO2改質層,在磨粒機械作用下去除。
拋光時間設定為6~12 h不等,拋光壓力設定為 200~260 N,拋光盤轉速設為固定值30 r/min,拋 光頭轉速設定為35~50 r/min,通過改變不同工藝 參數,對經過粗拋工藝后的碳化硅晶片進行了化學 機械拋光,并對拋光后的碳化硅晶片進行了測試分 析,拋光前碳化硅晶片表面粗糙度為3.2 nm,如圖3 所示。
2 試驗結果與討論
2.1 拋光液進給速率對晶片表面粗糙度的影響
研究拋光液進給速率對晶片表面粗糙度的影響規律,工藝參數為:拋光盤轉速30 r/min,設定拋光 頭轉速50 r/min,拋光壓力設定為200 N,拋光時長 設定為6 h,拋光液進給速率分別設定為1.8 mL/min、 2.6 mL/min、3.4 mL/min、4.2 mL/min,觀察CMP后 晶片表面質量,在原子力顯微鏡(AFM)下觀測到 的晶片表面粗糙度如圖4所示。
在其他條件不變的情況下,隨著拋光液進給速 率的增加,晶片的表面表面粗糙度隨之減小,這是 由于拋光液較少時CMP中主要是機械拋光起作用, 隨著拋光液增加,化學作用逐漸凸顯,晶片表面質 量得到改善。
2.2 拋光頭轉速對晶片表面粗糙度的影響
設定拋光盤轉速為30 r/min保持不變,設定拋光 壓力為200 N,滴液速率為4.2 mL/min,拋光時長定 為10 h,改變拋光頭轉速,測量拋光后的晶片表面粗糙度,其結果如圖5所示。
對測量結果進行了擬合,其擬合曲線如圖6所 示,從圖中可以看出,在保持其他條件不變的情況 下,隨著拋光頭轉速的增加,碳化硅晶片表面粗糙 度逐漸減小,從0.12 nm下降到0.095 nm,這是由于 拋光頭轉速增加會加劇拋光液中的磨粒運動,從而 與晶片表面的接觸更充分,但過快的轉速容易導致 晶片出現崩邊現象,當轉速增加到50 r/min時,晶片 表面粗糙度可以達到0.1 nm以下,最低為0.096 nm。
2.3 拋光壓力對晶片表面粗糙度的影響
同樣將拋光盤轉速固定為30 r/min,拋光頭轉速 定為50 r/min,滴液速率為4.2 mL/min,拋光時長定 為10 h,改變拋光頭壓力,對碳化硅晶片進行化學機 械拋光,測量拋光后晶片表面粗糙度,測量結果如圖7所示。
拋光頭壓力對晶片表面粗糙度影響擬合曲線如 圖8所示。隨著拋光頭壓力逐漸增加,拋光后晶片 表面粗糙度也隨之增加,由于隨著壓力的增加,晶 片與上下拋光盤之間的摩擦力會不斷增大,拋光時 產生的損傷層也逐步增大,導致晶片表面粗糙度增 加,可得出,拋光壓力保持在200 N時,拋光后晶片 表面質量最好,但過低的拋光壓力會降低晶片的材 料去除效率,增加成本,因此將拋光壓力定為200 N 最優。
2.4 拋光時長對晶片表面粗糙度的影響
將拋光盤轉速固定在30 r/min,拋光頭轉速固定 為50 r/min,拋光壓力保持200 N不變,滴液速率為 4.2 mL/min,研究了不同拋光時長對晶片表面粗糙度 的影響,經過CMP工藝后晶片表面粗糙度AFM圖如 圖9所示。
拋光時長對晶片表面粗糙度的擬合曲線如圖10 所示。由圖可見,當拋光時長為6 h時,晶片表面粗 糙度最大,隨著拋光時間的加長,晶片表面粗糙度 明顯下降,當拋光時長大于8 h時,表面粗糙度下降趨于穩定,化學作用和機械作用接近均衡,當拋光時 長增加到12 h時,晶片表面粗糙度最低達到0.083 nm。
2.5 晶片粘貼方式對晶片表面粗糙度的影響
除了上述拋光參數的研究之外,還分析了晶片 的吸附方式對其表面粗糙度的影響,固定其他條件 不變,即大盤轉速30 r/min、拋光頭轉速50 r/min, 拋光壓力200 N,滴液速率為4.2 mL/min,將碳化 硅晶片分別以水霧吸附及上蠟粘貼吸附的方式進行 CMP,拋光時長6.5 h,測得拋光后晶片表面粗糙度 AFM圖如圖11所示。
從圖中可以看出,其他條件不變的情況下,上 蠟粘貼吸附進行拋光和水霧吸附進行拋光后碳化硅 晶片的粗糙度差別不大,說明兩種吸附方式的不同 對晶片表面粗糙度影響不大,但水霧吸附方式所使 用的吸附墊成本較高,且壽命短,事后清理較為麻 煩,因此建議使用上蠟粘貼吸附方式。
3 結論
本文中對碳化硅襯底晶片進行了超精密化學 拋光工藝,分析了拋光頭轉速、拋光壓力及拋光時 長對碳化硅晶片表面粗糙度的影響,結果顯示,拋光頭轉速的增加和拋光壓力的減小有利于改善晶片 表面粗糙度,增大拋光時長可以進一步改善晶片質 量,最終確定了工藝中的最優參數,即:拋光液進 給速率為4.2 mL/min、拋光盤轉速為30 r/min、拋光 頭轉速為50 r/min、拋光盤壓力為200 N、拋光時長 為12 h時,碳化硅晶片表面質量最好,其粗糙度最好 可達0.083 nm。
來源:電子工藝技術第44卷第2期
作者:甘琨,劉彥利,史健瑋,胡北辰
(中國電子科技集團公司第二研究所)
審核編輯:湯梓紅
-
半導體
+關注
關注
334文章
27578瀏覽量
220513 -
工藝
+關注
關注
4文章
597瀏覽量
28845 -
CMP
+關注
關注
6文章
151瀏覽量
26061 -
晶片
+關注
關注
1文章
403瀏覽量
31513 -
碳化硅
+關注
關注
25文章
2789瀏覽量
49146
原文標題:【半導光電】碳化硅晶片的超精密拋光工藝
文章出處:【微信號:今日光電,微信公眾號:今日光電】歡迎添加關注!文章轉載請注明出處。
發布評論請先 登錄
相關推薦
碳化硅壓敏電阻 - 氧化鋅 MOV
碳化硅的歷史與應用介紹
碳化硅深層的特性
碳化硅半導體器件有哪些?
碳化硅基板——三代半導體的領軍者
請教碳化硅刻蝕工藝
淺談硅IGBT與碳化硅MOSFET驅動的區別
圖騰柱無橋PFC中混合碳化硅分立器件的應用
碳化硅單晶襯底加工技術現狀及發展趨勢
切割工藝參數對6英寸N型碳化硅晶片的影響
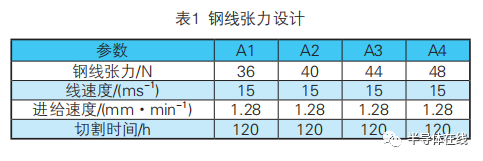
評論