浸錫是PCB行業內一種成熟的表面涂層,由于其具有高可靠性,在汽車行業備受信賴。在汽車市場,由于QFN(quad-flat no leads,即方形扁平無引腳)封裝的靈活外形、尺寸及可擴展性和散熱能力,而越來越受到人們的關注。
成功關鍵步驟之一是要有可潤濕的側翼,可提供與PCB上的可靠焊點連接,并能實現焊點和焊點質量的自動檢測。
QFN的底部通常是用電解錫覆蓋,有銅的側面會暴露于空氣中,需要額外處理才能實現側翼的可焊性。
如果沒有進行進一步處理,就會生成銅的氧化物抑制焊料的潤濕,所以在這種情況下只能形成二維焊點。
為了達到更佳的可靠性,業界正在研究提高QFN側翼潤濕性的解決方案,以形成三維焊點。
制造QFN的最后一步是分離步驟,可以是切割,也可以是沖壓。在這一步驟中,封裝側翼可能會被錫渣或模具殘留物污染,用標準的PCB預清洗系統無法去除黏在表面的這些污染物。
因此,必須使用專門調配的清洗劑和微蝕劑才能去除錫和模具殘留物,使引線框架材料中的銅合金平整。圖1展示了完成切割步驟后(a)經過清洗的銅合金表面。清洗過程包括預清洗和微蝕刻步驟(b)。最后一張圖是鍍錫后的側翼(c)。
圖1:QFN側翼的預處理和鍍錫過程:a)QFN分離后;b)清洗和微蝕刻之后;c)鍍錫后
在預清洗后,銅的表面看起來很平整;分離過程導致的劃痕和涂料殘留污物均已被去除。在浸錫鍍過程中,封裝側翼被浸錫覆蓋,形成密實的錫層,覆蓋了QFN側壁的全部焊盤。在鍍錫工藝之后,可以進行電鍍后期處理,防止錫層在后期的組裝過程中變色,形成疏水表面,保護表面免受蒸汽老化的影響。
為了確認錫層能夠改善焊料潤濕及形成三維焊點,將QFN試樣浸入液態焊料中進行測試,評估焊料對側面焊盤的表面覆蓋情況。試樣以45°的角度浸入焊料,停留5s。在150℃下對試樣進行8h、16h的熱預老化測試,然后在93℃下進行4h、8h的蒸汽老化測試。圖2為QFN側翼焊料潤濕的驗收標準。圖3展示了專門用于QFN鍍覆的浸錫工藝與應用在QFN上的PCB標準浸錫工藝的性能對比。
圖2:QFN側翼焊料潤濕的驗收標準
圖3:具有不同浸錫涂層的QFN側翼焊料潤濕效果
焊盤上焊料的覆蓋范圍至少要達到50%以上才是可接受的,低于50%可拒收。圖4是焊接后的側翼示例圖。圖中展示了在150°C下烘烤16h并在93°C下和93%相對濕度下存放8h后的焊接后的焊盤。
圖4:在150°C下烘烤16h的焊料潤濕示例圖(左)和93°C/93%相對濕度下存放8h的示例圖(右)
結果證實,與QFN采用的PCB浸錫工藝的焊接性能相比,為QFN側翼設計的浸錫工藝有明顯優勢。
在浸錫鍍層的老化過程中,金屬間化合物(intermetallic compound,簡稱IMC)的厚度增加,導致游離錫的含量降低;這一點對于錫表面的可焊性至關重要。
為了研究金屬間化合物在不同的基材合金下隨著時間推移而增長的情況,進行了存放測試。此測試需要將錫層鍍在EFTEC 64T和C194合金上。這兩種合金的成分如表1所示。
表1:合金的質量分數% 針對所有條件,沉積錫層的總厚度為1.5μm,并在150℃和93℃、93%相對濕度下進行熱老化和蒸汽老化測試。IMC和游離錫厚度的結果如圖5所示,厚度以μm為單位,其中淡藍色為游離錫,深藍色為IMC。
圖5:IMC和游離錫厚度的結果
結果表明,IMC的形成首先受溫度的影響。在150°C的儲存溫度下,IMC的增加隨時間線性增長。在150°C溫度下存放4h后,大約一半的錫厚度被IMC消耗。
在93°C的濕度老化過程中,IMC的形成速度較慢,在相同時間內,只有約40%的錫層轉化為IMC。這也表明,即使在150°C溫度下存放16h后,仍殘留了25%~32%的游離錫,可確保良好的可焊性。
合金材料對鍍層的影響很低,導致EFTEC 64T材料上的游離錫增加了約10%。
側翼的錫沉積層具有良好的可焊性,即使在加熱老化或蒸汽老化后也是如此,具體結果與IMC形成后是否剩余足夠多的游離錫相關。
檢查各個工藝步驟對QFN底部焊盤電解錫沉積的影響,未發現負面影響。晶須是浸錫沉積的已知風險,為了防止晶須的形成,加入了一種抗晶須添加劑,其沉積在錫沉積層的晶界上,可抑制錫晶須的形成。
審核編輯:劉清
-
pcb
+關注
關注
4319文章
23111瀏覽量
398284 -
qfn
+關注
關注
3文章
190瀏覽量
56204 -
IMC
+關注
關注
0文章
25瀏覽量
4598
原文標題:QFN可潤濕側翼連接的浸錫鍍層
文章出處:【微信號:actSMTC,微信公眾號:actSMTC】歡迎添加關注!文章轉載請注明出處。
發布評論請先 登錄
相關推薦
可目視確認焊接狀態的可潤濕側翼封裝
可潤濕側翼工藝怎么樣
可潤濕側翼 QFN 封裝對于汽車應用的價值所在
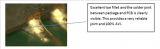
手工浸焊與機器浸錫的特點介紹
可潤濕側翼QFN封裝對于汽車應用的價值所在
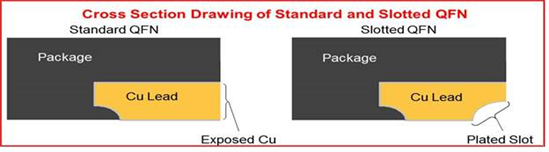
QFN側面為什么很難上錫,該如何解決?
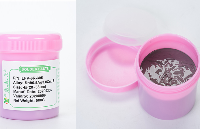
評論