隨著4680產(chǎn)業(yè)落地。供應(yīng)鏈內(nèi)收益材料包括高鎳正極、硅基負(fù)極、新型鋰鹽、復(fù)合集流體、設(shè)備及電池殼體,其中 PET 復(fù)合銅箔及硅基負(fù)極或?qū)⒊蔀闉樽钪饕隽俊?/p>
◆ 復(fù)合銅箔
鋰電銅箔根據(jù)組成材料的不同可分為傳統(tǒng)銅箔與復(fù)合銅箔。
傳統(tǒng)銅箔:由99.5%的純銅組成,根據(jù)厚度可分為極薄銅箔(≤6μm)、超薄銅箔(6-12μm)、薄銅箔(12-18μm)、常規(guī)銅箔(18-70μm)、厚銅箔(≥70μm)等,其特點(diǎn)為單位面積重量較重、金屬銅材使用量高、導(dǎo)熱性能高。
◆ 鋰電銅箔技術(shù)趨勢(shì)
PET 復(fù)合銅膜在鋰電行業(yè)的大批量應(yīng)用是必然的
例如,目前同樣級(jí)別的6-8微米的PET銅箔大部分會(huì)替代目前6-8微米的傳統(tǒng)銅箔,但是無(wú)法代替更薄的傳統(tǒng)銅箔。取代邏輯主要是由 PET 復(fù)合銅膜的四個(gè)先進(jìn)性所決定的:高安全、高比容、長(zhǎng)壽命、高兼容。6-8μm傳統(tǒng)銅箔極板在遭遇外力碰撞時(shí)容易造成燃燒、爆炸等安全隱患,研制更加安全的新式動(dòng)力電池材料已成為未來(lái)發(fā)展的趨勢(shì)。
◆ 性能特點(diǎn)
①高安全:消費(fèi)端對(duì)鋰電池的最大顧慮也是也是其不夠安全,電池自燃是由于發(fā)熱失控導(dǎo)致的內(nèi)短路。PET復(fù)合銅膜對(duì)這一問題的解決方法就是高分子不容易斷裂,即便斷裂,1微米的鍍銅的強(qiáng)度無(wú)法達(dá)到刺穿隔膜的標(biāo)準(zhǔn),可以實(shí)現(xiàn)永不刺穿,把內(nèi)短路的風(fēng)險(xiǎn)完全規(guī)避掉。
②高比容。PET復(fù)合銅箔重量更輕,目前集流體占電池重量的比重是15%,PET 技術(shù)可以提升5%-10%的電芯能量密度,實(shí)現(xiàn)高比容。
③長(zhǎng)壽命。這主要是因?yàn)?PET 表面更為均勻。并且金融結(jié)晶體更容易熱脹冷縮,高分子材料的膨脹率更低,更容易空置,保持表面完整性,提升程度在5%。
④高兼容。即很多性能可以更高的去進(jìn)行匹配,比如鋁箔和銅箔都可以應(yīng)用 PET 技術(shù)
⑤成本更低:傳統(tǒng)銅箔約占鋰電池質(zhì)量的9%、成本的8%。銅箔變薄可使相同電芯體積容納更多活性材料,6μm和4.5μm銅箔相比8μm銅箔能量密度分別提升5%和9%;此外銅箔越薄,電池成本越低、受銅價(jià)影響越??;傳統(tǒng)銅箔的銅原材料成本占比約80%,原材料環(huán)節(jié)難以降本;而PET銅箔原材料成本占比約31%。受產(chǎn)業(yè)化初期影響設(shè)備成本占比高達(dá)50%,PET銅箔生產(chǎn)通過規(guī)模效應(yīng)降低成本的空間更大,主要降本路徑為通過提高生產(chǎn)效率與良率攤薄單位固定成本。
◆成本結(jié)構(gòu)
銅箔占電池成本比重
迫于成本壓力開發(fā)新材料。動(dòng)力鋰電池整體朝著高能量密度的方向發(fā)展,但高鎳三元材料較傳統(tǒng)的 6 系三元材料和 5 系三元材料的成本有所上升,由此帶來(lái)了原材料的成本壓力,性能與成本的兼顧成為了亟需解決的問題。
鋰電銅箔是鋰電池最重要的原材料之一,充當(dāng)負(fù)極活性物質(zhì)載體的同時(shí)又充當(dāng)負(fù)極電子流的收集和傳輸體。目前主流的銅箔產(chǎn)品約占動(dòng)力電池總質(zhì)量的 14%,更薄的銅箔可以為電池帶來(lái)更高的能量密度,但同時(shí)也會(huì)帶來(lái)更高的成本。部分企業(yè)為解決這一難題, 在銅箔產(chǎn)品中引入高分子材料,通過材料創(chuàng)新降低銅箔的重量與成本,從而進(jìn)一步改善電池的性能與成本的兼顧問題。
使用PET銅箔可大幅降低銅箔原材料成本。傳統(tǒng)銅箔由純銅制備,銅成本占銅箔總成本約80%,而PET銅箔是在PET基膜表面進(jìn)行鍍銅,成本由PET價(jià)格和銅價(jià)共同決定,益于PET材料的低成本,PET銅箔能為電池帶來(lái)更更低的材料成本。截至2023年4月10日,銅價(jià)約為6.9萬(wàn)元/噸,PET材料價(jià)格約為2.6萬(wàn)元/噸,經(jīng)我們測(cè)算,6.5μm的PET銅箔較目前主流的6μm銅箔可降低62.42%的原材料成本,較目前最為先進(jìn)的4.5μm銅箔可降低51.68%的原材料成本。
◆銅箔產(chǎn)業(yè)鏈
上游原材料及設(shè)備廠商:設(shè)備廠商包括磁控濺射設(shè)備廠商和電鍍?cè)O(shè)備廠商;
銅箔制造:根據(jù)鋰電銅箔工藝可分為電解銅箔以及PET銅箔,其中電解銅箔為市場(chǎng)主流工藝,PET銅箔為新工藝;
下游鋰電池廠商:主要包括動(dòng)力電池廠商、3C消費(fèi)電池廠商以及儲(chǔ)能電池廠商等。
◆設(shè)備廠商
傳統(tǒng)銅箔多采用電解法制備,PET銅箔工藝核心為真空鍍膜與離子置換
傳統(tǒng)銅箔目前多采用連續(xù)電解法制備。鋰電池發(fā)展初期多采用壓延銅箔,但壓延銅箔生產(chǎn)工藝復(fù)雜、成本高,且全球產(chǎn)能極度集中于少數(shù)幾家公司;電解銅箔由于生產(chǎn)設(shè)備和工藝簡(jiǎn)單、容易操作,且產(chǎn)品性能良好,逐漸成為目前最普遍的銅箔生產(chǎn)方式。電解銅箔是在直流電流作用下,銅離子在連續(xù)轉(zhuǎn)動(dòng)的陰極輥表面還原沉積形成很薄的連續(xù)的銅層繼而連續(xù)剝離形成的,其主要生產(chǎn)流程包括溶銅、生箔沉積、后處理及分切。
PET銅箔制造工藝核心為真空磁控濺射、銅堆積層和清洗抗氧化保護(hù)。PET銅箔生產(chǎn)工藝以高真空設(shè)備磁控濺射在基膜上金屬化,再以離子置換機(jī)進(jìn)行金屬置換使金屬層增厚,具體工藝流程包括真空濺射鍍銅(非金屬材料金屬化)、液體電鍍(銅層增厚沉積)、成品材料配切。
復(fù)合銅箔產(chǎn)業(yè)化的核心壁壘為工藝與設(shè)備——真空磁控濺射
真空磁控濺射是制備薄膜的主要技術(shù)之一,下游應(yīng)用廣泛。
磁控濺射鍍膜是通過電場(chǎng)和磁場(chǎng)的作用,工作氣體產(chǎn)生輝光放電,離子轟擊靶材濺射出材料粒子形成薄膜,目的是在塑料薄膜表面制作一層金屬層、使非金屬材料金屬化,具有鍍膜穩(wěn)定性好、重復(fù)性高、均勻度好、適合大面積鍍膜、膜層致密、結(jié)合力好、工藝靈活度高等優(yōu)點(diǎn),主要應(yīng)用下游包括消費(fèi)電子、汽車、光學(xué)和玻璃等行業(yè)。
◆ 市場(chǎng)容量
預(yù)計(jì)2025年P(guān)ET銅箔磁控與鍍銅設(shè)備市場(chǎng)空間總計(jì)約80億元
預(yù)計(jì)2025年P(guān)ET銅箔真空磁控濺射設(shè)備市場(chǎng)空間約33.4億元,鍍銅設(shè)備市場(chǎng)空間約46.5億元。相較于傳統(tǒng)鋰電銅箔,PET復(fù)合銅箔帶來(lái)真空磁控濺射設(shè)備和鍍銅設(shè)備需求,基于以下假設(shè)測(cè)算:
1)假設(shè)2025年中國(guó)/全球新能源汽車滲透率33%/21%,據(jù)SPIR預(yù)測(cè),2022-2025年儲(chǔ)能電池需求分別為56GWh、79GWh、108GWh、168GWh;
2)假設(shè)PET銅箔滲透率2025年提升至21.7%;
3)假設(shè)2021年單GWh磁控濺射設(shè)備價(jià)值量為3000萬(wàn),單GWh鍍銅設(shè)備價(jià)值量為3750萬(wàn)。隨著設(shè)備技術(shù)迭代及規(guī)模效應(yīng),2022至2025年單GWh磁控濺射設(shè)備價(jià)值量分別為2900萬(wàn)、2800萬(wàn)、2700萬(wàn)以及2500萬(wàn),單GWh鍍銅設(shè)備價(jià)值量分別為3600萬(wàn)、3500萬(wàn)、3400萬(wàn)及3300萬(wàn)。
-
新能源汽車
+關(guān)注
關(guān)注
141文章
10557瀏覽量
99619 -
銅箔
+關(guān)注
關(guān)注
5文章
220瀏覽量
16331 -
圓柱電池
+關(guān)注
關(guān)注
0文章
181瀏覽量
9859
原文標(biāo)題:PET銅箔增量!受益于4680圓柱電池產(chǎn)業(yè)落地
文章出處:【微信號(hào):深圳市賽姆烯金科技有限公司,微信公眾號(hào):深圳市賽姆烯金科技有限公司】歡迎添加關(guān)注!文章轉(zhuǎn)載請(qǐng)注明出處。
發(fā)布評(píng)論請(qǐng)先 登錄
相關(guān)推薦
圓柱電池自動(dòng)分選機(jī):提升電池生產(chǎn)效率與品質(zhì)的關(guān)鍵設(shè)備
比克動(dòng)力:全球圓柱鋰電池行業(yè)領(lǐng)軍者
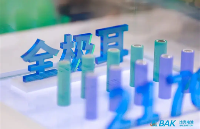
比克動(dòng)力以先進(jìn)大圓柱產(chǎn)品布局多領(lǐng)域應(yīng)用
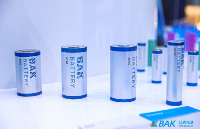
億緯鋰能圓柱電池產(chǎn)能再獲提升
比克動(dòng)力:競(jìng)速“大圓柱”賽道,全極耳工藝實(shí)現(xiàn)性能再升級(jí)
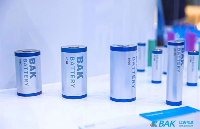
大圓柱電池產(chǎn)業(yè)加速分化,特斯拉押注全干法4680動(dòng)力
比斯特自動(dòng)化 氣動(dòng)科技賦能圓柱電池生產(chǎn):高效點(diǎn)焊機(jī)引領(lǐng)產(chǎn)業(yè)升級(jí)
特斯拉里程碑達(dá)成:第1億顆4680電池震撼問世
RFID技術(shù)賦能4680大圓柱電池生產(chǎn)溯源
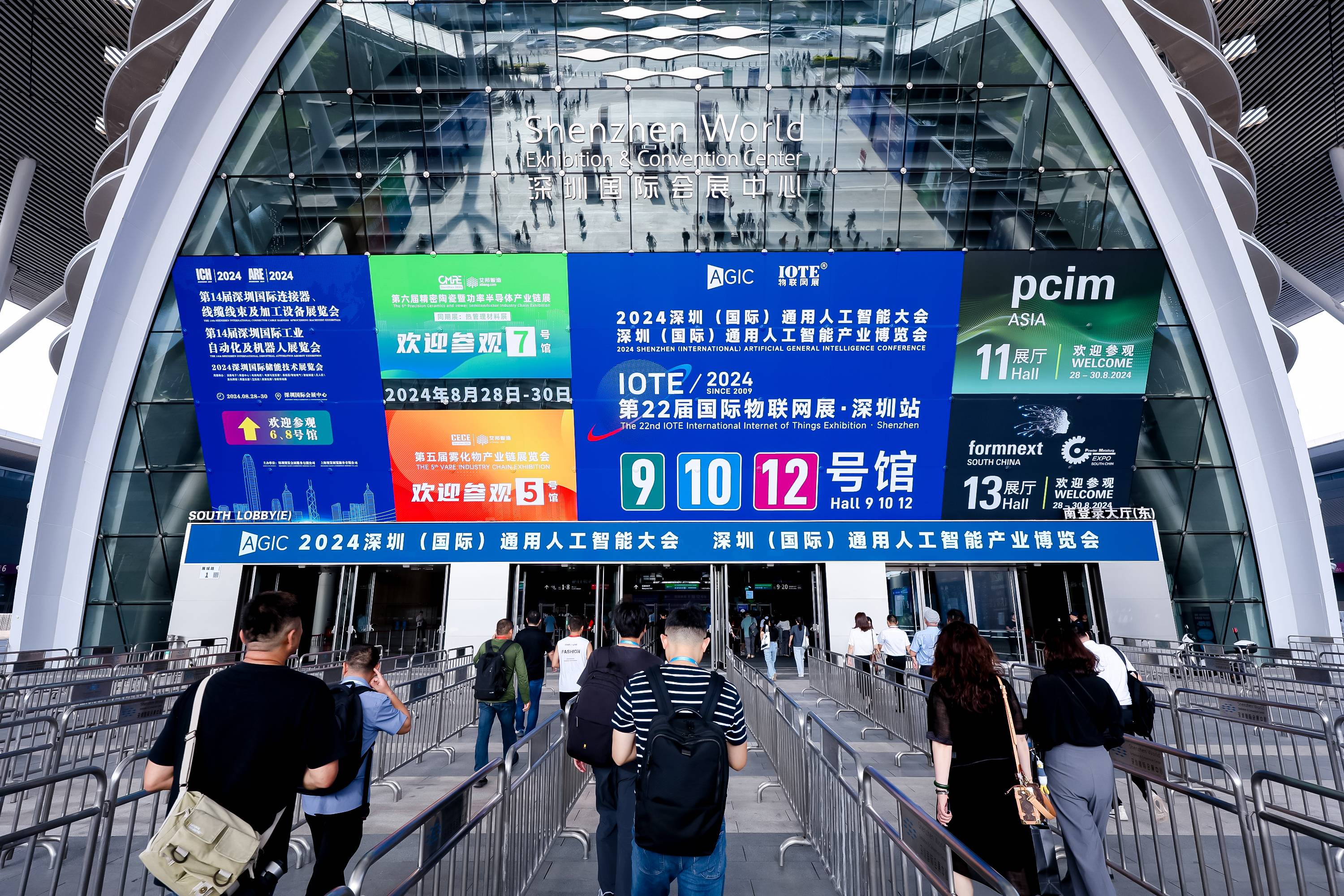
特斯拉4680電池產(chǎn)量環(huán)比增長(zhǎng)50%,成本持續(xù)優(yōu)化
圓柱電池測(cè)試設(shè)備:如何確保電池性能卓越
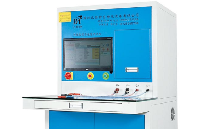
什么是小圓柱軟包電池?小圓柱軟包電池的優(yōu)缺點(diǎn)?
圓柱電池和方形電池的差異
圓柱電池是固態(tài)電池嗎?
Cybertruck的4680電池系統(tǒng)設(shè)計(jì)迭代
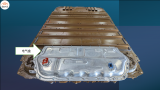
評(píng)論