目前有很多文章都在介紹工業4.0,智能傳感器在工廠環境中也日益普及(我和其他作者都寫過這些話題)。 雖然我們都注意到,在工廠、加工廠甚至一些新構建的自動化系統中,傳感器的使用明顯增加,但廣泛使用的傳感器也帶來一個重要變化,就是需要在這些舊款控制器內處理大量IO。 這些IO可能是數字IO或模擬IO。 這就需要構建存在尺寸和熱量限制的高密度IO模塊。 在本文中,我將重點介紹數字IO,在后續文章中再介紹模擬IO。
通常,PLC中的數字IO由分立式器件,例如電阻/電容或有獨立FET驅動組成。 為了盡可能減小控制器的尺寸,并且要求能夠處理2到4倍的通道數,這些都促使從分立式方案向集成式方案轉變。
我們可以用整篇文章來闡述分立式方法的缺點,尤其是每個模塊處理的通道數達到8個或以上的情況下,但只要說到高熱量/功耗、數量龐大的分立式組件(從尺寸和平均故障間隔時間(MTBF)角度),以及需要可靠的系統規格,就已足以說明分立式方法并不可行。
圖1顯示在構建高密度數字輸入(DI)和數字輸出(DO)模塊時面臨的技術挑戰。 在Di和DO系統中,都需要考慮尺寸和散熱問題。
數字輸入
大小
熱
支持所有輸入類型
類型 1、2、3、輸入
支持 24 V 和 48 V 輸入
穩健的操作規格
斷線檢測
數字輸出
支持不同類型的輸出驅動程序配置
大小
感性負載的集成消磁
熱量 - 驅動多個輸出時
驅動精度
診斷
對于數字輸入,還需注意它支持不同的輸入類型,包括1/2/3類型的輸入,以及在某些情況下,支持24V和48V輸入。 在所有情況下,可靠的工作特性非常重要,有時,斷路檢測也至關重要。
對于數字輸出,系統使用不同的FET配置來驅動負載。 驅動電流的精度通常是一個重要的考量因素。 在許多情況下,診斷也非常重要。
我們將探討集成解決方案如何幫助解決其中一些挑戰。
設計高通道密度數字輸入模塊
傳統的分立式設計使用電阻分壓器網絡將24V/48V信號轉換為微控制器可以使用的信號。 前端也可以使用分立式RC濾波器。 如果需要隔離,有時會使用外部光耦合器。
圖1顯示構建數字輸入電路的一種典型的離散方法。
圖1. 數字輸入和輸出模塊的考量因素。
這種類型的設計適合一定數量的數字輸入; 即每個板4到8個。 超過這個數字,這種設計很快會變得不實用。 這種分立式方案會帶來各種問題,包括:
高功耗和相關的板高溫點。
每個通道需要一個光耦合器。
部件過多會導致FIT率低,甚至需要更大的器件。
更重要的是,分立式設計方法意味著輸入電流隨輸入電壓呈線性增加。 假設采用一個2.2K?輸入電阻和24V V在。 當輸入為1,例如,在24V時,輸入電流為11mA,相當于功耗為264mW。 8通道模塊的功耗大于2W,32通道模塊的功耗大于8W。 參見下方的圖3:
DI 通道數 | 估計功耗 (W) |
8 | 2.1 |
16 | 4.2 |
32 | 8.4 |
64 | 16.9 |
單從散熱角度,這個分立式設計無法支持單個板上的多個通道。
集成式數字輸入設計的最大優勢之一在于顯著降低功耗,從而減少散熱。 大多數集成式數字輸入器件允許可配置的輸入電流限制,以顯著降低功耗。
當限流值設置為2.6mA時,功耗顯著降低,每個通道約為60mW。 8通道數字輸入模塊的額定值現在可以設置為低于0.5瓦,如下方的圖4所示:
DI 通道數 | 估計功耗(分立方法)(W) | 估計功耗(集成方法)(W) |
8 | 2.1 | 0.48 |
16 | 4.2 | 0.96 |
32 | 8.4 | 1.92 |
64 | 16.9 | 3.84 |
反對使用分立式邏輯設計的另一個原因是:有時DI模塊必須支持不同類型的輸入。 IEC公布的標準24V數字輸入規格分為1型、2型和3型。 1型和3型通常組合使用,因為其電流和閾值限值都非常相似。 2型具有6mA限流值,要更高一些。 采用分立式方法時,可能需要重新設計,因為大部分分立值都需要更新。
但是,集成式數字輸入產品通常支持所有這三種類型。 從本質看,1型和3型一般受到集成式數字輸入器件支持。 但是,為了滿足2型輸入最低6mA的電流要求,我們需要針對一個現場輸入并聯使用兩個通道。 而且只調節限流值電阻。 這需要進行電路板變更,但變更很小。
圖2 .采用分立式邏輯的傳統數字輸入設計。
例如,當前Maxim Integrated(現為ADI公司一部分)DI器件的限流值為3.5mA/通道。 所以,如圖所示,我們并聯使用兩個通道,如果系統必須接入2型輸入,則調節REFDI電阻和RIN電阻。 對于一些較新的部件,我們也可以使用引腳或通過軟件來選擇電流值。
要支持48V數字輸入信號(不是常見要求),需要使用類似流程,必須添加一個外部電阻來調節現場一端的電壓閾值。 設置此外部電阻的值,使得引腳的限流值* R +閾值滿足現場一端的電壓閾值規范(參見器件數據手冊)。
最后,由于數字輸入模塊與傳感器連接,因此設計必須符合可靠的工作特性要求。 當使用分立式方案時,必須仔細設計這些保護功能。 選擇集成式數字輸入器件時,確保根據行業規范確定以下各項:
寬輸入電壓范圍(例如,高達40V)。
能夠使用現場電源(7V至65V)。
能夠承受高ESD(±15kV ESD氣隙)和浪涌(一般為1KV)。
提供過電壓和過溫診斷也非常有用,以便MCU采取合適的操作。
設計高通道密度數字輸出模塊
典型的分立式數字輸出設計具有一個帶驅動電路的FET,由微控制器進行驅動。 可以使用不同的方法來配置FET,以驅動微控制器。
高端負載開關的定義是:它由外部使能信號控制,并連接或斷開電源與給定負載的連接。 與低端負載開關相比,高端開關為負載提供電流,而低端開關連接或斷開負載的接地連接,從負載獲取電流。 雖然它們都使用單個FET,但低端開關的問題在于:負載與接地之間可能短路。 高端開關保護負載,防止接地短路。 但是低端開關的實現成本更低。 有時,輸出驅動器也配置為推挽開關,需要兩個MOSFET。 參見下方的圖6:
集成式DO器件可以將多個DO通道集成到單個器件中。 由于高端、低端和推挽開關使用的FET配置不同,因此可使用不同的器件來實現每種類型的輸出驅動器。
圖3. 使用分立式邏輯構建的數字輸入模塊的預估功耗。
感性負載的內置消磁
集成式數字輸出器件的關鍵優勢之一是器件本身內置感性負載消磁功能。
感性負載是任何包含線圈的器件,在通電后,通常執行一些機械工作,例如電磁閥、電機和執行器。 電流引起的磁場可以移動繼電器或接觸器中的開關觸點,以操作電磁閥,或旋轉電機的軸。 大多數情況下,工程師使用高端開關來控制感性負載,挑戰在于,當開關打開,電流不再流入負載時,如何給電感放電。 不當放電導致的負面影響包括:繼電器觸點可能拉弧、很大的負電壓尖峰損壞敏感型IC,以及產生高頻噪聲或EMI,進而影響系統性能。
在分立式方案中,對感性負載進行放電的最常見解決方案就是使用續流二極管。 在本電路中,當開關閉合時,二極管被反向偏置且不導電。 當開關打開時,通過電感的負電源電壓會使二極管正向偏置,從而通過引導電流通過二極管的方式使存儲能量衰減,直至達到穩定狀態且電流為零。
對于許多應用,特別是工業行業中每個IO卡具有多個輸出通道的應用,該二極管通常尺寸很大,會導致成本和設計尺寸大幅增加。
現代數字輸出器件使用一種主動箝位電路在器件內實現這一功能。 例如,Maxim Integrated采用一項獲取專利的安全消磁(SafeDemag?)功能,允許數字輸出器件在不受電感限制的情況下安全關閉負載。
在選擇數字輸出器件時,需要考慮多個重要因素。 應仔細考慮數據手冊中的以下規格:
查看最大連續電流額定值,并確保在需要時可以并聯多個輸出,以獲得更高電流的驅動器。
確保輸出器件能驅動多個高電流通道(超過溫度范圍)。 參考數據手冊,確保導通電阻、電源電流和熱電阻值盡可能低。
輸出電流驅動精度規格也很重要。
圖4. 使用集成式DI芯片的數字輸入模塊的預估功率節省。
要從一些超出范圍的工作條件下恢復,診斷信息就非常重要。 首先,您希望獲取每個輸出通道的診斷信息。 其中包括溫度、過電流、開路和短路。 從整體(芯片)來看,重要診斷包括熱關斷、VDD欠壓和SPI診斷。 在集成式數字輸出器件中查找部分或所有這些診斷。
可編程數字輸入/輸出器件
通過在IC上集成DI和DO,就能構建可配置產品。 這是一個4通道產品示例,可以配置為輸入或輸出。
它有一個DIO內核,這意味著可以在高端或推挽模式下將單個通道配置為DI(1/3型或2型)或數字輸出。 DO上的限流值可以設置為130mA至1.2A。 內置消磁功能。 要在1/3型或2型數字輸入之間切換,我們只需設置一個引腳,無需使用外部電阻。
這些器件不僅易于配置,而且堅固耐用,可在工業環境中工作。 這意味著高ESD,提供高達60V的電源電壓保護和線路接地浪涌保護。
這是一個可能完全不同產品(可配置的DI/DO模塊)的示例,可通過集成式方法實現。
結論
在設計高密度數字輸入或輸出模塊時,明顯可以看出,當通道密度超過一定數量時,分立式方案毫無意義。 從散熱、可靠性和尺寸方面考慮,必須仔細考慮集成式器件選項。 在選擇集成式DI或DO器件時,必須注意一些重要的數據要點,包括可靠的工作特性、診斷、支持多種輸入-輸出配置。
審核編輯:郭婷
-
傳感器
+關注
關注
2551文章
51099瀏覽量
753572 -
驅動器
+關注
關注
52文章
8236瀏覽量
146365 -
電機
+關注
關注
142文章
9021瀏覽量
145492
發布評論請先 登錄
相關推薦
工業自動化逐步向工業無線的轉變發展
構建以軟件為中心的下一代自動化測試系統
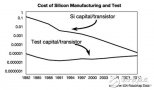
工業迎來數碼轉型 下一代智能機器會是什么模樣
自適應機器人助力下一代工業自動化
使用虹科port的GOAL中間件和RENESAS RZ/T2M推動實現下一代工廠自動化
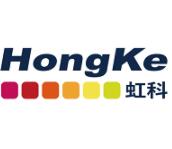
評論