作者:翟秀果,李毅拓,鄭 權丨河南森源重工有限公司
摘 要:
設計了一款新型純電動物流車用驅動電機,定子采用分裂繞組形式,電機在低速區域工作時繞組全部接入,電機在高速區域工作時繞組部分接入,以替代機械式兩檔變速箱,拓寬電機高效率工作區域。
解決電動汽車續航里程問題,一方面要從儲能電池入手,研制高儲能的電芯和電池管理系統,另一方面要從電驅系統方面入手,研制高效節能的電機和電控系統。本文主要研究電機的高效節能性,以一款200 kW永磁同步電機為例,探討分裂繞組定子和交直軸電感優化對電機高效率特性的貢獻。
永磁同步電機轉子上沒有銅耗,相對于異步電機效率較高,電動汽車廠家在電驅系統中越來越傾向于使用永磁同步電機。傳統電機定子繞組為固定匝數,因為電機感應電動勢和轉速成正比,所以永磁電機在高速時必須進行弱磁控制,以免感應電勢過高擊穿開關器件,即永磁電機在高速時有相當一部分電流是起到反向弱磁功能,并不提供轉矩,該部分弱磁電流在定子中同樣存在銅耗。
為了解決這一問題,部分廠商采用兩檔變速箱的結構,在車輛高速行駛時用切換齒輪的方法降低電機轉速,以此來降低電機的感應電動勢,但該結構增加了變速箱后電驅系統的體積和成本。本文采用分裂繞組的定子結構,從根本上解決永磁同步電機寬轉速運行的弱磁問題,電機定子繞組分段引出,在低速區域運行時繞組全部接入工作,保證電機恒轉矩輸出;在高速區域運行時繞組部分接入工作,定子磁鏈減小,所需弱磁電流降低,保證電機恒功率輸出。
1 動力匹配及電機性能
1.1 計算電機外特性曲線
本文所研究的永磁同步電機擬用作物流車的驅動電機,物流車相關動力需求參數如表1所示。
表1 電動物流車動力需求參數
物流車最大需求功率出現在滿載時的爬坡路段,根據最大爬坡功率計算式[4]:
(1)
計算爬坡路段所需驅動電機峰值功率Pr=150 kW,計算爬坡時電機轉速
3 650 r/min,再由公式:
(2)
計算電機恒轉矩段峰值轉矩T=392 N·m,取T=400 N·m。
電機低速段工作在恒轉矩區域,高速段工作在恒功率區域,繪制電機需求外特性曲線如圖1所示。
圖1 電動物流車需求電機外特性
1.2 計算電機參數
首先用解析法根據永磁同步電機所需功率和轉矩確定電機的大致尺寸,有經驗公式[3]:
(3)
式中:T為電機輸出轉矩;暫取電機輸出效率η=96%;電樞繞組系數kw=0.92,水冷電機電負荷A=50 kA/m,磁負荷B=0.8 T,根據車輛底盤安裝空間估算電機的有效長度le=0.15 m。
根據需求T=400 N·m,計算定子內徑Dsi=0.22 m。
取定子裂比0.66,定子外徑Dso=330 mm。
根據公式:
(4)
確定定子槽面積As,取槽滿率kp=0.7,定子槽數Ns=48,電流密度J=15 A/mm2。
進一步根據公式:
(5)
確定定子軛厚度hc和定子齒寬ωt尺寸,定子采用平行齒結構。
用相關數值在Maxwell軟件中進行2D建模,并進行電磁優化計算,得到電機基本參數,電機二維模型如圖2所示,具體電機參數如表2所示。
圖2 150 kW永磁同步電機1/2模型圖
表2 電機參數
計算得到電機輸出峰值狀態功率和轉矩,如圖3所示。圖3中,三角標志線為峰值轉矩,叉線為峰值功率,可以看出電機性能滿足車輛動力需求。
圖3 電機外特性曲線
進一步計算電機的電流曲線如圖4所示。圖4中,平滑曲線為定子相電流is曲線,三角線為交軸電流iq曲線,叉線為直軸電流-id曲線。計算電機的效率map如圖5所示。
圖4 電機電流曲線
圖5 電機效率map
從圖4可以看出,電機在低速恒轉矩區需要380 A的電流,隨著轉速升高,進入恒功率區域后電流先降再升,到達10 000 r/min之后,在高速區域電流逐漸超過了恒轉矩段電流。這是因為電流可以分解為兩部分,提供轉矩的交軸電流iq和弱磁電流-id,在低速區域,電機感應電動勢低,需要的弱磁電流較小,電流大部分用來提供轉矩輸出;中速段后進入恒功率區域,電機所需輸出轉矩降低而感應電動勢未超出額定電壓,電流呈現降低趨勢;高速段后電機感應電動勢超出額定電壓,且隨著轉速升高進一步升高,電機所需輸出轉矩仍然降低趨勢,需要越來越多的電流參與到弱磁分量中,以至于電流超過了低速區電流。
電驅系統的最大伏安容量定義為電機最大工作電壓點的電壓Us1和電機最大工作電流點的電流Is2的乘積,該Us1和Is2可以不同時出現,最大伏安容量決定著電驅系統的功率密度,也限制著功率元器件的選型。顯然,定子電流在高速段超過低速段,這不是電機工作的理想情況,會提高電驅系統的最大伏安容量,降低系統的功率密度;另外,高速時因為電機鐵耗越來越高,再加上不斷增大的銅耗會導致高速段效率嚴重下降,從圖5的電機效率map可以直觀地看出電機高效區域面積很小。
2 分裂繞組設計
2.1 設計原則
為了降低電驅系統的最大伏安容量,同時提高電機高效率區面積,擬將本電機的定子繞組設計為分裂繞組形式,將定子繞組分兩部分組成,兩部分同槽分布,低速區域兩部分串聯同時工作,高速時切掉部分繞組來降低電機的感應電動勢,分裂繞組電機拓撲結構如圖6所示。
圖6 分裂繞組拓撲結構
定子繞組分為N1和N2兩部分,兩段之間首尾串聯并做中間引出線,三相電機的三個尾端引出線接切換開關K1,三個中間引出線接切換開關K2。低速時K1接通,K2斷開,電機工作繞組N=N1+N2;高速時K1斷開,K2接通,電機工作繞組N=N1。當然,圖6為特殊的兩段式分裂結構,而分裂繞組的分段段數z不僅限于z=2,切換開關個數等于分段段數z,具體分段段數需依照電機的弱磁調速范圍而定,并同時考慮經濟性和可行性。
分裂繞組內部結構如圖7所示,以A相為例,每個六邊形為一個繞組元件,普通電機繞組的元件個數為Ns/m,即槽數除以相數,而分裂繞組的元件個數為z×Ns/m,本文中電機z=2即可滿足弱磁調速需求。圖7中繞組A1-X1段每個元件的匝數為N1,繞組A2-X2段每個元件的匝數為N2,兩段繞組的元件同槽分布。
圖7 分裂繞組內部結構
分裂繞組的設計原則如下:
1) 繞組分段段數z需要同時考慮經濟性和可行性,分段段數提升會導致切換開關個數增加,從而增加接線盒體積,不利于成本控制。
2) 繞組分裂匝數比λ=N1/(N1+N2),λ的選取需要同時考慮低速時輸出足夠大的轉矩和高速時足夠小的感應電動勢。
3) 分裂轉速點n的選取要根據分裂匝數比而定,并同時保證繞組分裂前感應電勢足夠小,繞組分裂后輸出轉矩足夠大。
4) 為了盡可能降低系統的最大伏安容量,繞組分裂前所有繞組串聯工作的電流is1和繞組分裂后僅部分繞組工作的電流is2要滿足關系is1≈is2。
5) 繞組分裂前的總匝數選取要考慮系統的安全電壓,即考慮切換開關的故障模式,在所有繞組串聯情況下,電機在最大轉速時的感應電動勢要小于控制器件的安全電壓。
2.2 設計結果與對比分析
根據以上設計原則,利用Maxwell 2D軟件對繞組匝數、分裂轉速點和轉子磁鋼尺寸進行參數化分析,計算得出分段段數z=2,分裂轉速n=6800r/min,元件匝數N1=4,N2=5,即轉速小于6800r/min時繞組工作匝數為9匝,轉速大于6800r/min時繞組工作匝數4匝。
對比分裂繞組電機和普通繞組電機的空載感應電動勢曲線如圖8所示。圖8中,實線為分裂繞組電機空載感應電動勢曲線,虛線為普通繞組電機感應電動勢曲線。可以看到,分裂轉速前電機感應電動勢斜率很大,分裂轉速后電機感應電動勢斜率較低,之后電機的空載感應電動勢遠低于普通電機。
圖8 空載感應電勢對比
分裂繞組電機的定子電流曲線如圖9和圖10所示,其中圖9為電流幅值曲線,圖10為電流相角曲線。對比圖4和圖9可以看出,高速時分裂繞組電機的電流得到有效抑制,最高速時電流不超過低速時的恒轉矩電流。
圖9 分裂繞組電機電流幅值曲線
圖10 分裂繞組電機電流相角曲線
對比普通電機和分裂繞組電機最大伏安特性曲線如圖11所示。可見,繞組采用分裂控制可以有效地降低整個系統的伏安容量,從而節省成本,提高系統的功率密度。
圖11 電機最大伏安容量對比
計算分裂繞組電機的輸出轉矩特性曲線,如圖12所示。圖12中,三角線為繞組分裂前轉矩曲線,虛線為繞組分裂后轉矩曲線,兩條曲線疊加之后的輪廓線可以完全覆蓋圖1的電動物流車需求轉矩曲線。進一步計算分裂繞組電機的效率map,如圖13所示。可見,該電機存在兩個高效率區域,對比圖5普通電機的效率map,發現高效區域面積幾乎增加了一倍。
圖12 分裂繞組電機輸出特性曲線
圖13 分裂繞組電機輸出效率map
3 實驗驗證
分裂繞組電機試驗樣機,分裂繞組電機接線盒內部引出線,兩段式分裂繞組共計9個引出頭,其中A、B、C端接控制器輸出,A1,B1,C1和A2,B2,C2分別接切換開關K1和K2。
將電機安裝在臺架上進行性能測試,電機通過減速器、傳動軸和后橋的差速器連接,后橋兩端各布置一個測功機,可以模擬車輛的具體運行狀態,電機和差速器的連接。
電機測試過程中對數據進行記錄,中控室操作界面如圖18所示。設定轉速后測功機測取轉矩值,本測試所用電機減速器變比3.07,后橋差速器減速比6.15,總計減速比18.8,界面中左右轉速和轉矩分別顯示的是兩個測功機的測量值,即代表實際車輛運行時輪轂的轉速和轉矩,兩邊轉矩之和除以減速比即為電機輸出轉矩。
圖17 分裂繞組電機與差速器連接
圖18 電機性能測試界面
根據測試數據繪制電機實際工作效率map如圖19所示。和仿真計算一致,該圖有兩個高效率區域,不過高速區的實測效率值要大于計算值。由于測試臺架的轉速限制,測試只能進行到12 000 r/min,根據效率分布趨勢來看,更高轉速時的實測效率值依然要大于計算值,可見,分裂繞組電機對于效率的提高是十分見效的。
圖19 分裂繞組電機實測效率map
將電機的效率值結合電動汽車具體蓄電池參數,用ADVISOR軟件計算續航里程,計算結果如圖20所示,分裂繞組電驅動系統對比普通電驅動系統的電動汽車續航里程整體提升了約30%。
圖20 電動汽車續航里程對比
4 結 語
本文以純電動物流車用驅動電機為應用對象,設計并制造了一臺分裂繞組永磁同步電機,通過仿真分析和實測得出以下結論:
1) 電機定子繞組采用分裂繞組形式可以額外增加電機的高效率區域,能有效地提高電驅系統的效率,從而延長電動車續航里程。
2) 電機定子繞組采用分裂繞組形式可以大幅降低電驅系統的最大伏安容量,從而減小體積、增加功率密度、降低成本。
3) 分裂繞組的設計既要考慮到電機低速大轉矩特性,又要保證電機高速時較低的感應電動勢,需要對分裂轉速點和繞組分裂前后匝數比進行優化計算。
4) 分裂繞組電機可以根據弱磁區間的范圍靈活地選取繞組分裂段數,以此來代替多檔式機械變速箱,提高電驅系統功率密度,并且以電切換代替機械切換,可以提高換擋靈敏度。
審核編輯:湯梓紅
-
電動汽車
+關注
關注
156文章
12087瀏覽量
231264 -
永磁同步電機
+關注
關注
28文章
873瀏覽量
49552 -
繞組
+關注
關注
2文章
522瀏覽量
19875 -
電驅系統
+關注
關注
0文章
113瀏覽量
2385
原文標題:電動汽車用分裂繞組永磁同步電機設計
文章出處:【微信號:EDC電驅未來,微信公眾號:EDC電驅未來】歡迎添加關注!文章轉載請注明出處。
發布評論請先 登錄
相關推薦
【TL6748 DSP申請】基于DSP的電動汽車永磁同步電機驅動器的設計
電動汽車電機電控技術解析
永磁同步電機原理、特點、應用詳解
電動汽車驅動電機的選配原則研究
電動汽車中電機和電控技術分析
電動汽車如何使用永磁同步電機弱磁控制的詳細資料免費下載
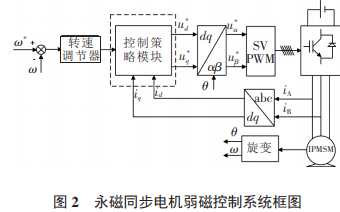
評論