1 前言
根據《2020年新能源汽車推廣補貼方案及產品技術要求》,純電動載貨車補貼要求單位載質量能量消耗量(Ekg)不大于0.29 W·h/km·kg,動力電池系統能量密度不低于125 W·h/kg,純電動續駛里程不低于80 km。根據近幾年補貼要求中Ekg加嚴趨勢,如圖1。結合現有新能源技術發展水平預測為滿足2021—2022年補貼要求,Ekg設定目標不大于0.27 W·h/km·kg。
圖1單位載質量能量消耗量(Ekg)變化趨勢
計算公式如式(1):
式中,E表示電能消耗率,按照電動汽車GB/T 18386—2017《電動汽車能量消耗率和續駛里程試驗方法》[1]在等速法下測量獲得的;M表示附加質量。按照GB/T 18386檢測試驗中的附加質量規定執行。
降低Ekg的值可以通過降低E值或提高M值來實現,即降低電能消耗率或者提高載質量(或降低整備質量)。
提升電驅動效率是降低電能消耗率的路徑之一,目前電機和電機控制器的綜合效率可提升的空間已經非常有限,但電驅動系統效率的提升仍有一定發展空間。目前,輕型載貨車主流電驅動系統路線主要有3種:電機直驅、電機加減速器和電驅橋方案。電機直驅方案特點是傳動效率較高、故障率低、扭矩需求大,因此電機成本高。電機加減速器方案中電機的扭矩低,但是傳動效率則不如直驅的高。電驅橋方案具有傳動效率高、質量低和成本低的特點。電驅橋方案幾乎適用于2.5~18 t的純電動載貨車型。
本文主要研究電動輕型載貨車匹配電驅橋方案及仿真分析。
2 電驅橋參數匹配
2.1 整車基本參數及技術指標
目標車型M-EB基于M-2019款做改款優化,采用電驅橋方案取代電機直驅方案。M-2019基礎車Ekg為0.29 W·h/km·kg,M-EB改款產品整車整備質量降為2 800 kg,Ekg設計目標不大于0.27 W·h/km·kg,并滿足動力性和經濟性要求。具體整車基本參數、主要技術指標需求與參考標準分別見表1、表2。
表1 整車基本參數
表2 主要技術指標需求與參考標準
2.2 驅動電機匹配設計
車輛動力性是衡量汽車性能的一項重要指標,主要由3方面的指標來評價:最高車速、最大爬坡度和加速性能[3]。
根據汽車理論,汽車的功率平衡關系方程式(2):
式中,Pv為車輛功率,kw,ηt為傳動效率,m為整備質量;f為滾動阻力系數;i為道路坡度;Cd為風阻系數;A為迎風面積;δ為旋轉質量換算系數;ua為車速。
最高車速對應車輛功率需求計算公式(3):
式中,umax為車輛最高車速,90 km/h。
最大爬坡度對應車輛功率需求計算公式(4):
式中,αm為爬坡角度。
加速時間采用恒功率加速計算的方法,根據推導出的加速過程所需功率P3[4],即式(5):
式中,tm為加速時間,取16 s;δ為旋轉質量換算系數,取1.15。
利用上述公式,可得到各動力性指標對應的車輛功率需求,具體見表3。
表3驅動電機參數需求分析
由車輛功率平衡關系可知,電機的峰值功率必須同時滿足整車動力性指標功率需求,則峰值功率至少為93.4 kW,額定功率至少47.8 kW。
結合輕型載貨車的場景特點及提高應對惡劣工況的能力,取過載系數為1.2,即額定功率不小于57.4 kW,峰值功率不小于112.1 kW。結合體系資源成熟度及競品同類車型產品配置信息,最終選定驅動電機功率參數:額定功率65.0 kW,峰值功率120.0 kW。
驅動電機較大的恒功率區可以改善車輛的動力性,在兼顧低速爬坡能力的同時提高最高車速。額定功率相同的電機額定轉速越高,體積越小。普通高速電機的轉速一般為10 000~15 000 r/min,最高轉速初步設定為12 000 r/min,如式(6)。
式(6)中:β為恒功率系數,一般取2~3,取3;nmax為最高轉速;ne為額定轉速。則ne取4 000 r/min。
由公式(7)計算峰值轉矩為286.5 N·m,額定轉矩為155.2 N·m。
目前市場上的電動汽車主要采用的是永磁同步電機和交流異步電機。永磁同步電機在瞬態有較高的效率(95%左右),同時有著更高的功率密度,因此適用于頻繁起停的工況;而感應電動機更適合在高速工況條件下使用[5]。
2.3 電驅橋傳動比的設計
電驅橋的傳動比要同時滿足車輛最高車速、最大爬坡度以及對加速時間的要求[6]。
傳動比的上限,由電動機最高轉速和最高行駛速度確定,見公式(8)。
傳動比的下限,由電動機最高轉速對應的輸出轉矩滿足最高車速的要求,式(9)和電機峰值轉矩滿足最大爬坡的要求,式(10)共同確定。根據以上確定傳動比取值范圍
由于傳動比越大,同噸級后橋的傳動齒輪半徑越大,后橋重量越大,且通過性越差。結合資源情況,初步選定傳動比為16.19。當滿足最大爬坡度要求,峰值轉矩需求計算如公式(11):
由式(11)得Tm=283.0 N·m,峰值轉矩為286.5 N·m滿足要求;但是考慮到輕型載貨車惡劣的工況適應能力,預留20%的后備轉矩,即峰值轉矩設定不小于340.0 N·m。
最終結合輕型載貨車實際使用工況、車輛結構、體系資源成熟度及上述性能需求參數,初步選定驅動電機參數如表4。
表4 驅動電機參數
2.4 動力電池匹配設計
純電動汽車行駛完全依賴動力電池的能量,基礎車型為81.14 kW·h磷酸鐵鋰電池,其具有比能量高,大功率充放電以及長循環壽命等特性。按照設計要求,動力電池需滿足車輛40 km/h等速續駛里程250 km以上。由式(12)可計算電量需求:
不考慮低壓電器損耗,EB不小于72.8 kW·h。基礎車型電量為81.14 kW·h,滿足現有車型續駛里程和功率需求,故動力電池可直接借用,具體參數如表5。
表5 動力電池參數
3 仿真分析
3.1 系統建模
AVL CRUISE軟件是用于研究車輛動力性、燃油經濟性、排放性能與制動性能的高級仿真分析工具。基于CRUISE平臺,參照整車參數以及選定的電驅橋系統和動力電池,建立整車模型。整車模型完成后,建立部件模塊之間機械連接與數據信號之間電氣連接[7]。最終純電動輕型載貨車整車系統仿真模型如圖2所示。
圖2純電動輕型載貨車系統仿真模型
3.2 仿真分析
3.2.1 電驅橋傳動比的仿真分析
首先通過CRUISE模型分別仿真運算,分析不同電驅橋傳動比取值下車輛模型的動力性和經濟性,確定最優傳動比。根據驅動電機參數及電驅橋傳動比的選取計算公式,確定取值范圍并間隔取值,進行仿真分析,具體結果如表6。
表6不同傳動比仿真結果
根據藍牌輕型載貨車高速最高限速要求為100 km/h,故傳動比大于16.19的變速器不適合目標車型實際使用需求;結合行業競爭產品功性能指標和輕型載貨車場景工況特征,輕型載貨車應滿足最大爬坡度大于30%的要求,故i不小于14.70。通過仿真數據結果分析,傳動比越小,車輛40 km/h等速工況下電能消耗率越小,越有利于Ekg目標的達成。且傳動比取值14.50~15.00時,車輛0~80 km/h加速性能最優。結合現有體系資源、成本和性能需求,故最終選定電驅橋的最優傳動比為14.70。
3.2.2 經濟性仿真分析
仿真數據40 km/h等速能耗為222.9 W·h/km,詳見表7。
表7 40 km/h等速工況能耗仿真數據
仿真數據C-WTVC工況能耗為323.5 W·h/km,詳見表8。
表8 C-WTVC工況能耗仿真數據
經計算Ekg為0.263 W·h/km·kg,均滿足目標車型經濟性設計要求,見表9。
表9經濟性仿真結果
3.2.3 動力性仿真分析
最高車速:在電機轉速11 407 r/min時,車輛達到最高車速110 km/h,如表10。
表10最高車速仿真數據
最大爬坡度:最大爬坡度為30.2%,在電機恒轉矩區間獲得;10 km/h和50 km/h最大爬坡度分別為29.86%和15.17%,見圖3。
圖3爬坡度仿真數據
加速性能:0~80 km/h加速時間為12.7 s,見圖4。
圖4加速性能仿真數據
根據以上動力性仿真結果,目標車型電驅橋系統滿足動力性設計要求,見表11。
表11 動力性仿真結果
4 結束語
根據仿真結果,該電驅橋系統能夠滿足GB/T 18386—2017規定的Ekg不大于0.27 W·h/km·kg的設計目標;滿足GB/T 18385—2005規定的動力性設計指標。且相比M-2019車型電驅動系統能夠降低物料(BOM)成本2 000元左右,降低質量100 kg左右,驅動效率提升4%。并且動力性相比電機直驅方案提升6%以上。
以上數據結論是基于現有開發經驗和數據結論進行參數匹配及仿真模擬,和實車測試數據會有一定差異,未來需要進行樣車試制,進一步試驗驗證分析。雖然集成式的電驅橋方案能夠縮減尺寸、降低質量、降低成本和降低車輛的復雜度,但其中的挑戰也很大,如選擇高速電機的電驅橋系統可能會引發一系列系統問題:像電機轉速提高會帶來NVH的挑戰;跨零部件開發協同難度增加;電氣系統跟機械系統之間的關系、邊界條件、安全、冷卻、壽命和可靠性問題,都需要試驗驗證及系統化解決[8]。
責任編輯:彭菁
-
電動汽車
+關注
關注
156文章
12117瀏覽量
231582 -
控制器
+關注
關注
112文章
16396瀏覽量
178511 -
電機
+關注
關注
142文章
9038瀏覽量
145737
原文標題:純電動輕型載貨車電驅橋參數匹配及仿真分析
文章出處:【微信號:EDC電驅未來,微信公眾號:EDC電驅未來】歡迎添加關注!文章轉載請注明出處。
發布評論請先 登錄
相關推薦
基于MASTA軟件的輕型電驅橋減速器齒輪的優化設計
電動助力轉向系統控制器的設計方案
輕型電動車低功耗控制器設計
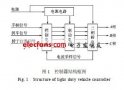
輕型載貨汽車的電動助力轉向系統的控制器研究設計
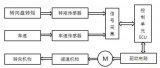
什么是匹配電阻,匹配電阻的作用是怎樣的
純電動載貨車動力性和經濟型參數設計
輕型電驅橋嘯叫優化分析
純電動汽車動力系統選型匹配與仿真
商用車中央集成式電驅橋結構及原理
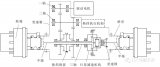
電動輕型載貨車匹配電驅橋方案及仿真分析
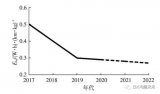
評論