電驅動橋是從傳統車橋衍變而來,它是汽車的傳動系統,起著承受負載、降低轉速、增大轉矩、保證左右車輪差速以及制動等功能。通過合理的選型和充分的驗證,可實現產品的緊湊化、輕量化、高效率和高壽命。
電驅動橋的種類
按電動機在整車中的布置形式可將電驅動橋分為電動機直聯式、平行軸式和同軸式。
1)直聯式結構是采用電動機取代燃油車的發動機和變速器,所采用的電驅動橋是從傳統燃油車的驅動橋上通過加大齒輪速比以及提升齒輪性能衍變而來,起初應用于微型乘用車、物流車等領域,現主要集中應用于輕型貨車、中型貨車等以上車型。
2)平行軸式結構是采用電動機進一步取代燃油車的發動機、變速器和傳動軸,將電動機集成為電驅動橋的一個子零件并與電驅動橋的輸出半軸呈平行布置,其減速器采用兩級傳動,系統集成度高,能量損耗小,目前廣泛應用于物流車、微型乘用車、輕型客車及皮卡上。從近年市場上的反饋來看,該電驅動橋已經完美地滿足了整車廠和客戶使用需求,大大加快了汽車的電動化進程。
3)同軸式結構是在平行軸式電驅動橋基礎上,將電動機與電驅動的輸出半軸做同軸布置,使得產品的集成度更優,是電驅動橋的發展方向。
電驅動橋的耐久試驗
1.電動機直聯式電驅動橋的耐久試驗
電動機直聯式電驅動橋是從傳統燃油驅動橋衍變而來,因而可參考QC/T 533-2020《汽車驅動橋臺架試驗方法》、QC/T 534-2020《汽車驅動橋臺架試驗評價指標》進行耐久試驗。標準中對強化系數K的取值只模糊定義1.0~2.2,然而實際應用中,電驅動橋的電動機轉矩普遍偏小,電驅動橋急加速和沖擊工況多,因此在耐久試驗(見圖4)中,應以電動機最大輸出轉矩乘以強化系數K的值作為試驗轉矩,且試驗轉矩與車橋速比的乘積應盡量接近以車橋附著力計算的輸出轉矩值。
通過對已經量產的幾款電動機直聯式電驅動橋的數據統計,試驗時將電動機轉矩的強化系數設為1.3~1.8是比較合理的。
為滿足整車能量回收功能,對電動機直聯式電驅動橋應增加反拖試驗要求,QC/T 533-2020中明確了在規定試驗轉矩下輸出端壽命不低于2萬次。該標準對試驗轉矩和轉速的表述不全,參照整車能量回收策略和實際量產的幾款產品數據統計,可按以下方式進行極限工況下的反拖試驗:試驗臺架在驅動橋輪端提供整車最高車速下的輸入轉速,在主減速器法蘭端施加該轉速下的最大功率點轉矩進行試驗;當輪端運轉次數達到5萬次時,拆解出主從動齒輪,觀察主從動齒輪表面有無拉毛、燒傷或者其他異常磨損的現象。
2.平行軸/同軸式電驅動橋的耐久試驗
針對平行軸/同軸式電驅動橋,目前行業內還未有針對性的試驗檢測指導性文件,大多數業內人員均是參考QC/T 533-2020《汽車驅動橋臺架試驗方法》、QC/T 534-2020《汽車驅動橋臺架試驗評價指標》及QC/T 1022-2015《純電動乘用車用減速器總成技術條件》進行耐久試驗,其臺架結構形式可參考圖5所示臺架。
然而單純以QC/T533-2020中表述的輸出端試驗次數最低10萬次來評判電驅動橋的壽命顯然過低,并且試驗工況太過單一;而以QC/T 1022-2015中的輸出端試驗次數約1300萬次來評判電驅動橋的壽命又太過苛刻,系統地完成所規定工況的疲勞試驗要將近一個多月,這勢必帶來巨額的試驗成本。因此,從縮短試驗成本的角度出發,研究和推行一種經濟可靠的電驅動橋耐久試驗方法和評價體系顯得十分迫切。
通過分析對比幾款已量產的平行軸式電驅動橋快速臺架耐久試驗、整車耐久路試及量產售后反饋,形成表1的統計數據。
表1 平行軸式電驅動橋相關參數
根據該統計結果,可以制定表2的兩種較經濟可靠的電驅動橋耐久試驗標準供選用。
表2 平行軸式電驅動橋試驗參考工況
結語
對電動機直聯式電驅動橋的耐久試驗和反拖試驗,應強化輸入轉矩和輸入轉速,使之盡量符合整車極限使用工況,避免驗證缺失和相關售后故障。
對平行軸式或同軸式電驅動橋的耐久試驗,應結合試驗成本、整車耐久路試和保修里程這些考核目的,來選擇最合適的試驗方案。從成本上考慮,推薦只進行高扭工況下的正轉正驅試驗,輸出端壽命不低于50萬次為宜;其次推薦進行高扭下的正轉正驅、高扭下的正轉反驅、高扭下的反轉正驅、高速下的正轉正驅試驗,綜合輸出端壽命100萬次為宜。
責任編輯:彭菁
-
電動機
+關注
關注
75文章
4121瀏覽量
96745 -
減速器
+關注
關注
7文章
397瀏覽量
23349
原文標題:淺析電驅動橋耐久試驗方法
文章出處:【微信號:EDC電驅未來,微信公眾號:EDC電驅未來】歡迎添加關注!文章轉載請注明出處。
發布評論請先 登錄
相關推薦
針對奧迪e-tron的電控部分進行詳細講解
半橋式與全橋式的優缺點
實現隔離式半橋柵極驅動器的設計基礎
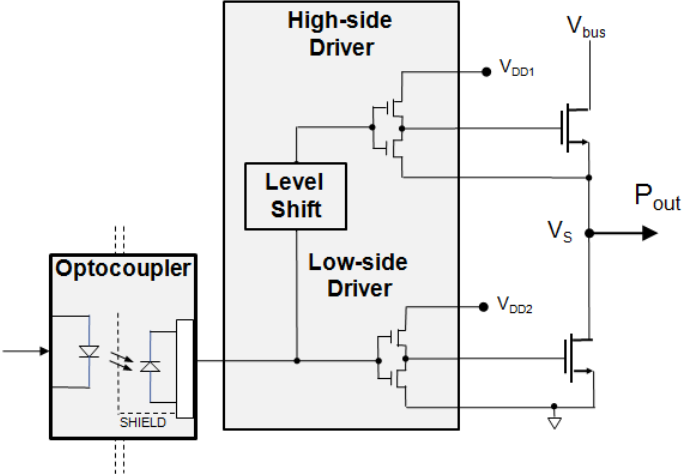
評論