在新能源汽車終端市場中,隨著SiC材料價格下降,碳化硅(SiC)的需求快速增長,來自于車載充電、驅動逆變和DC-DC轉換。隨著400V切換到800V,使用硅基IGBT開始向SiC MOSFET轉變,一方面提高功率密度,另一方面提高了驅動效率。
電動汽車和充電站需高電壓和惡劣環境下工作,SiC器件是目前主要方向。盡管制造和封裝成本高,但價格已開始用得起來,目前推動供應合作伙伴關系和新SiC工廠成了全球的潮流。SiC晶圓技術升級,需20%新工藝工具和80%改進工具,改進目標是提高功率器件的生產速度,促使車企合作直接晶圓工廠以加速模塊生產。
新的晶圓工藝工具包括高溫外延生長(>1,500°C)、熱離子注入、快速熱處理(RTP)和更快的脈沖原子層沉積。用于SiC 材料的晶圓研磨、CMP、拋光墊和漿料也在發生重大改進,包括剝離劑和清潔化學品在內的新材料可滿足設備和可持續性需求。從封裝端來看,帶有分立元件的高功率印刷電路板正在被集成電路+集成封裝(芯片級封裝CSP)所取代,以實現更小、更可靠的設計。
在模塊的設計中, SiC 模塊是主要研發方向,GaN 器件的潛力也在嘗試。到 2030 年,全球將生產 3000 萬輛新能源汽車,將推動功率半導體市場,其中約 50% 的硅器件、35% 的碳化硅器件和 12% 的氮化鎵器件將用于電動汽車。
SiC 模塊是從 400V 向 800V 核心器件。盡管仍需應對晶圓晶體缺陷、器件封裝和模塊集成、供應鏈變化等挑戰,但很多市場預測對于SiC寄予厚望,預計到 2027 年,功率半導體市場將達到 $6.3B,其中 70% 用于汽車應用。僅 SiC 晶圓產量方面,2022 ——2027 年年均增長率為 14%。
● SiC的玩家:IDM、代工企業和設計公司
在芯片制造層面,Wolfspeed、意法半導體、安森美、羅姆、英飛凌和博世等是關鍵參與者。碳化硅晶圓,正開始從 150mm切換到200mm,但生長、切片和制備過程,還有優化的空間。
IDM 和加工企業,都在努力降低 SiC 晶格的缺陷率,開發 SiC 專用工具平臺,例如高溫離子注入、在 1,500°C 以上運行的外延沉積爐,以及改進的 CMP 漿料、拋光墊和清潔化學品加工非常堅硬的材料。
400V體系下,硅、SiC 和 GaN 的開關器件都可以用,SiC比 GaN 功率水平更高。GaN具有比SiC更高的電子遷移率,但其成熟度較低。GaN 在制造高頻器件方面具備潛力。
許多 SiC 芯片制造商已將其150毫米硅生產線改為生產SiC芯片。在成熟、完全折舊的硅工廠中加工碳化硅的資本投資大約為 3000 萬美元,回報巨大。新的碳化硅晶圓廠正在快速建設中,無晶圓廠公司也在爭奪產能。
盡管 SiC 芯片的成本約為硅芯片的三倍,但最終的系統成本低于,主要是SiC 芯片能夠以高效率運行,減少了磁性元件和無源元件的體積,從而抵消了成本的增加。SiC 器件特別適用于汽車領域,能夠在惡劣環境下以更高的溫度提供高功率密度,實現非常低的開關損耗和超低的 RDSon(源極和漏極之間的電阻),小的 RDSon 直接可以讓 MOSFET降低功耗。
SiC器件的性能取決于 SiC 材料的質量,晶體質量一直是業內關注的主要問題,因為晶體中仍然存在一些缺陷。這些缺陷需要進行設計和調整,通常需要調整和驗證外延。這使得碳化硅在制造業中的實施方式還不是精益的。在電氣方面,功率器件可能對寄生電感、火花和其他挑戰非常敏感,不斷應對這些參數的變化。隨著碳化硅、氮化鎵和砷化鎵等化合物半導體變得更加主流且增長速度更快,參數良率問題將會得到改善。
● SiC產能和協作方式
垂直整合與晶圓協作在碳化硅開始慢慢形成,100mm和150mm尺寸的六方晶圓(4H和6H)主導市場。最大的SiC器件制造商正逐步轉向更大的200mm晶圓。英飛凌從多個供應商采購晶圓,瑞薩電子則簽署了10年協議,支付20億美元定金以獲得150mm裸露和外延SiC晶圓供應,并與三菱合作在日本新建SiC工廠。SOITEC和意法半導體正在研究單晶上的多晶SiC方法,以減少浪費并提高散熱性。
SiC的缺陷水平,需要數據共享,200mm晶圓的生長也需要更大的種子和更長的時間,隨著時間的推移,SiC晶圓生長的成本可能會降低,生產率有望提高約20%。
到 2030 年的需求和產能預估,日本、韓國、中國、馬來西亞、德國、奧地利和美國的全球晶圓和晶圓廠產能相當可觀,SiC是不是會產能過剩,這確實是個現實的問題!
小結:半導體行業正在邁向 1 萬億美元的市場,半導體技術界對下一代電源效率和性能的需求,是給出了明確的答案的。
-
集成電路
+關注
關注
5388文章
11547瀏覽量
361834 -
功率半導體
+關注
關注
22文章
1156瀏覽量
42977 -
晶圓工藝
+關注
關注
0文章
6瀏覽量
5819
原文標題:芝能智芯|功率半導體迎來碳化硅時代
文章出處:【微信號:QCDZSJ,微信公眾號:汽車電子設計】歡迎添加關注!文章轉載請注明出處。
發布評論請先 登錄
相關推薦
碳化硅在半導體產業中的發展
碳化硅功率器件的工作原理和應用
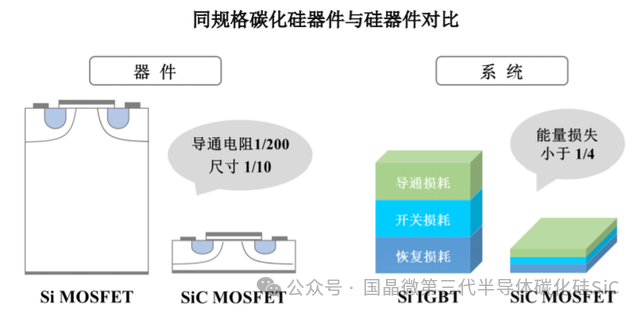
碳化硅壓敏電阻 - 氧化鋅 MOV
半導體碳化硅(SiC)行業研究
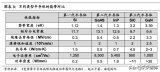
評論