在數字化、智能化不斷發展的今天,車燈功能的不斷增加以及外形所需的開口尺寸的不斷縮小,均對led光源提出了不同挑戰。這些新挑戰促使LED光源朝著高亮度,微型化,集成化三個維度發展。
下面我們就來分別介紹這3個LED光源的發展方向。
高亮度
鑒于車燈變薄的趨勢,也需要led光源體積扁平化,因為車燈開口越小,勢必導致光損耗越大,繼而使整個體系光學效率越高,若要保證大燈的照明性能不變,則需要光源的大小也應進一步扁平化和高亮度化。
下圖說明了車燈高度和led光源尺寸的一個線性對應關系,例如,要設計12mm透鏡高度的車燈,來實現光學擴展量為3°的像素高度,led芯片的高度尺寸必須控制在0.68mm以內,否則整個光學系統的效率會大大降低。
圖1:遠近光透鏡高度和led光源尺寸之間的線性對應關系。
即便CCC/ECE/SAE允許遠近光照明僅滿足最低法規值,但是對大多數車廠而言,需要考慮的是最終用戶的要求,一般而言,600lm下的近光,甚至達到法規要求,對最終用戶造成偏暗的影響。也就是滿足用戶需求的LED近光目前最少要有800 lm~1000 lm的路面照明。即假定光學模組的光學效率為40%至55%,則近光led光源的光通量應至少為1500 lm至2000 lm。再假定大燈內有一到三個近光透鏡模組,則每個LED透鏡模組的光源光輸出為500 lm到2000 lm的光源。因此,通過以上簡單的數學計算,對于通常發光面積為~1 mm2的大功率LED顆粒,亮度水平要達到150 Mcd/m2到500 Mcd/m2的亮度,才能達到光輸出分別為500 lm和2000 lm。
當前主流的LED制程技術可以實現200 Mcd/m2左右的亮度水平。為了達到更高的性能水平,則需要Led供應商們開發下一代高亮度led芯片
圖2為假設為12 mm高的薄透鏡大燈的示例。它由兩個近光透鏡模組和兩個遠光透鏡模組組成。
若使用單芯led的高度是0.68 mm時,當具有2°以下的光學擴展度像元高度時,根據圖1的函數關系,遠光透鏡模組的高度值將會大于它的光學擴展量的約束。結合光學零件和玻璃透鏡光的損耗,進一步的光學模擬可以計算出模組的光學效率是38%,這種效率是很低的。
圖3:左:近光光學模擬。右:遠光光學模擬
若要led芯片超出200 Mcd/m2的亮度,則需重新優化LED芯片結構和整個光學系統,以期獲得更高的能量密度。在led芯片領域,最大限度地避免led效率降低是核心。
如今led芯片電流密度通常在3 A/mm2附近,如果想要實現200 Mcd/m2能量密度,led芯片電流密度應該增加到5-8A/mm2,所以有必要對led外延區進行重新規劃,增加外延區電流密度及電遷移的同時盡量降低熒光粉抑制。現若要達到500 Mcd/m2的能量密度,我們預計在電流密度為8 A/mm2的情況下,led 的結點處需要>30%的光電轉換效率。所以,有必要對車燈的散熱系統進行優化。正如圖4所顯示的那樣,LED芯片會在較大電流密度時獲益于優化車燈散熱系統。結溫由110°C下降到85°C,電流可望下降接近1 A。這種下降對于提高效率,延長led壽命都是非常有益的。
圖4:在不同結溫下 LED光通量和輸入電流的關系
圖4為不同led結溫下光輸出與電流的關系曲線。LED芯片的發光面積為1mm2。虛線表示為1570 lm的極限值,相當于500 Mcd/m2(假設遠場中的朗伯輻射模式和整個發光面積的亮度均勻)。
微型化
還有新的車燈功能如矩陣ADB,要求每顆led芯片都能單獨供電和控制,成百上千顆的led芯片集成在一塊led板上,這導致ADB模組的尺寸越來越大,同時系統的光學效率和散熱問題也成了主要問題。自適應ADB的功能整合進一步推動了led光源的微型化。
目前基于單顆LED陣列的ADB矩陣模組已經上市多年。然而,這些模塊通常需要設計前置光學系統,這些前置光學系統加深了透鏡模塊的深度(見圖5左)。如果使用尺寸更小,更微型化,更高亮度的led陣列,可以避免額外的前置光學系統,降低模組的深度。
圖5:左:使用準直透鏡的矩陣模組的光學系統。右圖:緊密排列LED陣列直接成像的光學系統。
現有汽車級別微型化led陣列制作方法為:首先在平板上制作led芯片陣列并通過充填/側涂硅基密封劑從而實現光學隔離。此法存在著很多弊端。一、填充層的不透明性隨著填充厚度的增加而降低因此很難降低led芯片之間的雜散光,造成矩陣分區像素之間的對比度低。另外,打造3行以上led陣列也面臨著制造、成本等諸多挑戰。針對光學性能及成本問題,需要開發新的led芯片結構,從而實現緊密排列、最小串光和可陣列配置的微型化led芯片(如圖6顯示的微型化led示意圖)
圖6:微型化led的示意圖。
圖7展示的是一個矩陣大燈的實物示例,使用13個間距很近的LUXEON Neo Exact LED,每相鄰2顆的間距只有50μm。矩陣模組采用直徑40mm圓透鏡,透鏡中心可通過光學模擬達到最大對比度1:200像素分區亮點。為了使得遠光光型分布更加均勻,彌補像素之間由于縫隙形成暗區的問題,需要優化透鏡設計,使得像素分區之間更加平滑。如果使用硅基密封劑涂覆同樣的LED陣列,像素對比度僅為1:60。
圖7:使用13顆緊密排列的LUXEON Neo Exact LED的矩陣系統,led陣列發光間隙只有50μm。左上:系統前視圖,右上:電路板圖紙,左下:所有LED亮起的模擬光型,右下:每秒LED熄滅的模擬光型。
集成化
還有新的全數字車燈技術,比如道路投影,分辨率更高,甚至提高到了上萬像素的規模,需要led的制程工藝提升到小于50μm x 50μm的micro級別,而每一個led芯片的光學控制都是相互獨立的,led芯片之間的縫隙最小。此時需要采用經過CMOS集成、單個led顆粒可自主控制的電路相互連接,這樣才能在公路上成像圖案由更高一級協議進行控制。
綜合這些新型數字大燈技術方案對研發顛覆性創新micro-led系統帶來要求,要求高分辨率與微型光學設計同步。
功能集成化的最終應用就是分辨率更高的數字前大燈。若LED陣列具有足夠的分辨率及尺寸精度,單個數字大燈可生成多種光型。功包含高分辨率ADB、AFS功能、與導航或攝像系統相關聯的隨動轉向、近光截止線的自適應調節功能,車道標線、障礙物和標志高亮顯示等。micro-LED的需求都可以從這些應用中派生出來。
在ADB系統中,要求在水平方向上至少有+/-12°的發光角度。要為圖案建立足夠清晰的截止線,起碼要有1:250對比度。對遠光進行ADB分區以具有更低分辨率為目的,對一個0.085°的亮點在50m遠處是一個寬7.5厘米,長4米的一個矩形亮斑,我們由此可依此推斷對應ADB功能所需分辨率。例如對于車道投影,假定縱橫比為1:3的led陣列板我們就能直接算出要達到清晰車道投影所需的最小19000像素。一個通常的遠光需要在250 m內產生至少1 lx照度的光(相當于65000 cd)。通過光學公式換算,照度=光通量/立體角的關系,我們可以計算出每芯片所需的光通量為0.14 lm/芯。假設ADB系統33%的光學效率,每顆LED芯片需要提供0.43 lm/芯。如果使用90 Mcd/m2的合理光源亮度,我們可以估算micro-led陣列的單科發光面積為40μm x 40μm。
如果需要led陣列的體系結構以滿足市場ADB的需求,存在許多技術難點。首先,要創建一個約20000個密集像素的micro-LED陣列,很明顯micro-led陣列必須由單塊或幾個大的子塊組裝而成,而每顆micro-led是一個芯片分區。每顆芯片的尋址必須通過CMOS驅動來完成(見圖8)。
圖8: led 芯片和 CMOS 集成 (原理圖)
對led芯片和CMOS的集成,一個主要挑戰是對比度和整體效率。當單顆micro-led芯片的尺寸為40μm 時,在每顆芯片之間幾乎沒有空間來隔離串光。如果Micro-led之間的間距留10μm,這樣將使led的發光面積減小到30μm x 30μm,與-40μm x 40μm的發光面積相比,面積減小了40%以上。面積縮小而要達到同樣的光輸出需要相應增加電流密度,從而降低整體光學效率10%。micro-led內的光電躍遷和邊緣的非輻射重組將進一步抑制效率,解決的方法是使led發光面積增大,但這反而使led和系統的成本大幅增加。因此這是一對相互沖突的計劃。不管怎么說,以上這些困難都是led廠商必須要解決的問題,隨著技術的發展,這些問題都可以克服。
LED光源的總結和展望
總之,新造型、新功能不斷促進led技術進步的同時,LED新技術正迅速地促進汽車大燈新造型與新功能的運用。增加led亮度水平可達到超薄且高性能前照燈設計。
Led微型化可明顯縮小ADB矩陣大燈體積。micro-LED的進一步發展將使汽車前照燈的功能集成化與所需的緊湊性完美結合。再說micro-LED也有先天的優點,那就是只有在必要的時候才會發光,也就是說對于數字大燈而言,該技術比DMD具有明顯的效率優勢。
而從長遠看,完全一體化封裝micro-led工藝會比分立LED陣列明顯節約成本。所以micro-LED陣列必將成為智能數碼前照燈中效果最好和性價比最好的方案。據悉,上萬像素的數字化大燈已經完成了樣品試制,預計2年后將裝配成新車上市。
-
led
+關注
關注
242文章
23277瀏覽量
660896 -
光源
+關注
關注
3文章
704瀏覽量
67781 -
車燈
+關注
關注
1文章
205瀏覽量
16574
發布評論請先 登錄
相關推薦
AI網絡發展的四大核心技術支柱
iLight混合點光源 激光與LED技術的結合
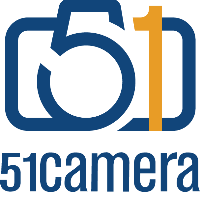
新項目LED車燈設計問題
晶能光電攜全系列車規級LED光源產品參加展會
從ECU到“燈光域”,車燈創新倒逼上游EE架構升級
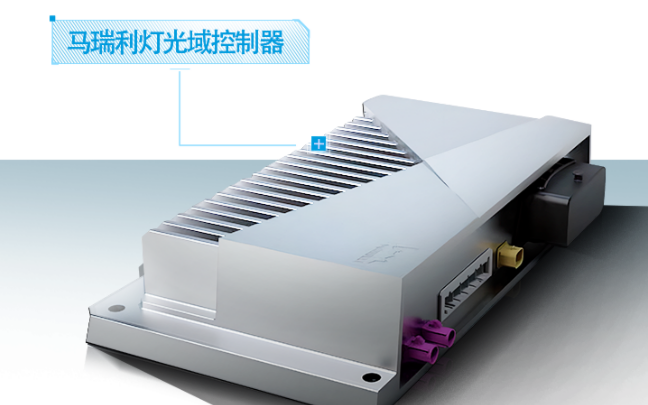
評論