導讀
機載武器是提升國家軍事力量的重要武器裝備,其生產過程中必須考慮其制造精度和生產效率。針對未來產品型號多樣化、批量小、周期短等發展趨勢,總裝產線需快速調整以滿足訂單交付的需求。本研究開展了基于數字孿生的總裝產線模型構建和仿真研究,突破了生產線建模,數字孿生模型仿真規則、虛實產線數據互聯和雙向交互規則等技術。最終, 解決了總裝產線設計定型周期長,產線布局合理性論證困難,訂單變化引起的生產計劃改變,資源利用率不足等問題,為目前的總裝產線建設起到正面、積極的推動作用。
01
引言
機載武器有利于我國在軍事戰爭中獲得絕對空中優勢,壓制空中火力來提高我國國防力量,提升國際地位發揮著至關重要的作用,必須保證其生產的高效性,可靠性。實現機載武器生產的數字化、自動化、智能化, 極大提升軍工企業的產線設計和生產并行的能力,從而使產品定型周期縮短,生產成本降低,提升資源利用率。隨著機載武器產品的迭代升級,產線需快速調整來滿足訂單需求。傳統的生產模式是機載武器研發定型后開始設計產線,經多輪口頭討論,驗證產線設計方案后,才正式建設產線。產線建設過程中才會發現問題,每次優化、升級產線需進行拆裝、重組,耗費較多時間和金錢, 這樣就會導致產品生產周期過長,喪失企業競爭優勢, 甚至在重要戰爭中延誤戰機。雖然現有的生產線已經擁有了相對完整的體系架構及完備的功能,且可以實現自動化生產及智能化管理,但缺少相應的仿真分析機制, 不能做到自主決策,及時發現問題。
隨著數字孿生技術的快速發展,可以明顯看出:任何事物都可能有數字孿生。數字孿生技術已廣泛投入應用到產品研發設計、工業制造等領域,它所具備的高度保真、實時反映、快速判斷和深度分析等特點,將大力促進中國數字產業化和制造產業數字化的發展,積極推動數字經濟和實體企業的融合發展。基于實體設備及產品,數字孿生對整個生產線進行系統描述,通過將實體以數字化形式展現在虛擬的信息空間中,對實體設備及產品在真實環境中的形狀、位置、功能信息等加以建模仿真,重構物理實體的關鍵要素,從而達成虛擬信息空間和物理真實環境之間的互聯互通。本文針對機載武器未來產品型號多樣化、批量小、周期短等發展趨勢和總裝產線快速調整以滿足訂單交付的需求,開展研究。
02
構建產線數字孿生模型
產線資源的數字化管理與描述是實現生產線設計, 迭代與優化的關鍵。產線仿真模型通過數字孿生技術構建,并構建實際生產中的各要素互相關聯、全流程的虛實交互,形成仿真模型和實際生產中裝配設備、測試設備之間的數據相互聯通和實時交互,實現生產線、單元和設備由真實空間到虛擬空間多維度、多粒度的自動映射,以及生產過程中的模型構建、離線和在線仿真,最終用來指導設計和迭代優化產線方案?;跀底謱\生構建的產線模型框架如圖1 所示。
對實際生產來說,不同生產設備實體需執行不同命令完成不同裝配工藝,最終完成產品總裝;但對于產線仿真,其忽視了生產裝配動作,同種類型的裝配、測試設備具有類似屬性信息,且可實現相同功能。也就是說每一類孿生模型都是對實現同種功能的物理實體設備的抽象化表述。產線仿真層面,構建數字孿生模型的目的是建立一套可重復使用,且具有通用性的數字模型,任何孿生模型都是某一類裝配設備或測試設備在虛擬空間的具象化體現?;跀底謱\生的總裝產線模型將具有相似生產行為的設備進行分類分析,將實體設備的幾何信息、屬性信息、仿真規則和裝配信息等在實際生產過程用到的各類參數抽象化,從而構建總裝產線的數字孿生模型(Twin Logical Model,TLM)。因此,總裝產線仿真的數字孿生模型:TLM = { 幾何信息,屬性信息,仿真規則,裝配信息}。
03
構建基于數字孿生驅動的產線仿真規則
虛擬空間中,實體設備的孿生模型根據自身幾何信息、屬性信息和裝配信息,以產線仿真規則為基礎驅動產線運轉,從而實現產線設計方案的預驗證及實際生產線仿真分析。因此,定義數字孿生模型的仿真規則,通過規定模型間的生產信息傳遞方法,即同步運行機制和互斥優先機制,利用信號通道將仿真計算所產生的信號傳給有關模型,進而使基于數字孿生的產線模型具備正常運轉的能力,保證邏輯仿真的正確映射。
3.1 生產信息傳遞方法
裝配工序相鄰仿真模型間連接的信息通道,在虛擬空間中是有向連接的。相連的孿生模型間借助信息通道建立前驅和后繼關系,基于此通道來完成數據的實時交互。前驅對象為當前模型中完成前一道裝配工序的模型, 后繼對象為當前模型中完成后一道裝配工序的模型。當仿真模型的運行狀態改變時,會自動切換狀態,并將這一變化以信號的形式傳送到信息通道,其前驅對象和后繼對象獲取信息通道中的狀態信號后做出響應,并觸發生產動作來改變其狀態。以此類推,整個仿真模型的信息傳遞工作就完成了。數字孿生模型間生產信息傳遞方法如圖2 所示。
因生產節拍、設備臺套數、人員配置和物流配送等會產生相應的差異,另外,各個生產過程中的生產資源數量也不一樣,因此所有仿真模型間的信息交互會出現兩類不同的情況,分別是一對一交互模式(單一模型連接),一對多交互模式(單一模型和多個模型同時連接)。一對一交互模式下通過同步運行機制實現狀態切換,而一對多交互模式下,狀態轉換則通過互斥優先機制進行。
3.2 同步運行機制
數字孿生模型在一對一交互模式下,模型運行狀態切換與仿真規則、相連模型傳輸的狀態信號有關。兩個相連的孿生模型,前驅生產對象只需關注能否發出物料, 不用關注后繼對象;后繼生產對象同樣只需關注能否接收物料并進行加工,無需關注前驅對象。仿真過程中, 如果前驅對象沒有傳入狀態信號,那么后驅對象則無法解析信號;另外,如果后繼對象沒有完成前一個信號解析時,前驅對象則沒有辦法完成下一個信號的傳入,也就是在一對一交互模式下,信息的傳輸、解析具有一定的先后次序,而實際裝配設備、測試設備的生產節拍往往會影響這種順序。
在實際總體裝配過程中,會存在三種生產情況:前驅生產對象生產時間小于、等于或大于后繼生產對象的生產時間。根據生產模型存在正常作業、空閑待機和阻塞等待三種運行狀態的切換過程,建立前驅、后繼生產對象運行狀態切換的時間關系。前驅生產對象生產時間小于后繼生產對象生產時間(不存在待機時間):
前驅生產對象生產時間等于后繼生產對象生產時間(不存在待機和阻塞時間):
前驅生產對象生產時間大于后繼生產對象生產時間(不存在阻塞時間):
式中,Tpw,Tpe,Tpb 分別為前驅生產對象正常作業、空閑待機和阻塞等待時間;Tsw,Tse,Tsb 分別為后繼生產對象正常作業、空閑待機和阻塞等待時間。同時,依據前述三種運行狀態切換的時間關系,采用同步運行機制實現狀態信號的傳輸與解析。
3.3 互斥優先機制
由于單位生產時間內,一個前驅對象僅能產生一個物料,同時該物料只能被一個后繼對象作用。所以在一對多交互模式下,多個前驅對象間及多個后繼對象間均存在競爭關系。由此需建立互斥優先機制來實現一對多交互模式中多個孿生模型間的物料傳遞、信息交互。一對多交互模式如圖3a 所示,單一前驅對象與多個后繼對象相連時,前驅對象將作業完成的狀態信號傳遞給生產狀態處于優先級最高,且當前為空閑待機狀態的后繼對象;如果前驅對象已完成該狀態信號傳輸,其余后繼對象則無法再次獲得該狀態信號,最終達成了狀態信號的互斥解析。多對一交互模式如圖3b 所示,多個前驅對象與單一后繼對象相連時,當所有前驅對象在同一時間完成作業并在信息通道中傳入信號時,后繼對象通過獲取其前驅對象的生產狀態,從處于優先級最高的前驅對象中獲取狀態信號,并進行解析;而其余前驅對象的生產狀態信號則繼續保留在其相應的信息通道中,由此完成了狀態信號的優先傳遞。
04
虛實產線數據互聯和雙向交互機制
傳統的工業級產線仿真往往僅根據產線結構、運行機理或者某一生產因素完成建模仿真,此種方法得到的仿真效果較差?,F場產線的狀態會因訂單變動、設備故障等發生不可預估的變動,離線進行的產線仿真模型難以及時、準確地反映裝配產線的現場生產狀態。由此建立虛實產線數據互聯和雙向交互機制,從而達到物理產線和數字產線虛實融合的目的,采集物理實體生產數據更新仿真模型,使模擬結果更符合生產實際狀態;同時, 仿真模型結果分析又可用于指導產線調整,提升設備利用率,保證產品交付,如圖4 所示。
利用歷史數據完成模型訓練,并對模型進行綜合評估、篩選和優化。在客戶端,將現場裝配設備、測試設備的PC 工控機軟件的端口號和IP 地址與工控機的軟件建立連接,啟動數據采集來獲取設備的工作數據,傳送到客戶端完成數據解析后,將生產數據輸入到產線模型中來驅動仿真。在神經網絡和多目標遺傳算法的基礎上, 對生產過程中的各類生產資源參數進行動態分析,獲得生產控制的最優解,最終反饋到管理系統中,以實現對總裝產線的控制。同時,將問題發現后才開始被動解決轉變為主動調整產線參數,為總裝產線優化、自主決策提供可能。
05
結束語
基于目前機載武器總裝產線建設存在的問題,本文進行了總裝產線的數字孿生產線模型構建和仿真理論研究,構建了生產線建模、數字孿生模型仿真規則、虛實產線數據互聯和雙向交互規則,建設了一條數字化產線。目前正在投入應用,實現了產線設計方案的預驗證,有效縮短了總裝產線設計定型周期,為目前的總裝產線建設起到正面、積極的推動作用。同時,為該機載武器企業的其他產線建設起到示范作用,推動企業朝著智能制造方向快速轉型升級。
-
智能化
+關注
關注
15文章
4884瀏覽量
55381 -
模型
+關注
關注
1文章
3243瀏覽量
48842 -
數字孿生
+關注
關注
4文章
1325瀏覽量
12254
原文標題:基于數字孿生的總裝產線模型構建及仿真技術研究
文章出處:【微信號:CADCAM_beijing,微信公眾號:智能制造IMS】歡迎添加關注!文章轉載請注明出處。
發布評論請先 登錄
相關推薦
基于設計數據共享的板級熱仿真技術研究(一)
基于dSPACE_MATLAB_Simulink平臺的實時仿真技術研究
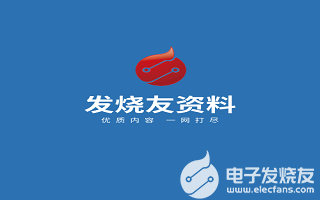
評論