歡迎了解
孔靜 李巖 高鴻 劉媛萍 張磊 閻曉蕾 朱旭斌
文摘
金絲材料應用于航天器小型化微波模塊等產品的電路封裝中,金絲鍵合界面受高低溫環境影響易產生性能變化從而影響服役可靠性。本文對金絲界面高低溫特性的演化規律進行了研究,包括空間溫度環境模擬試驗后的界面與成分遷移、界面層厚度變化、鍵合金絲拉伸剪切力與失效模式演變,得出不同溫度條件處理后的金鋁鍵合界面微觀組織變化規律。結果表明高低溫循環試驗后金絲界面仍保持較高的結合強度,一定程度的金屬間化合物生長提高了鍵合界面強度。高溫貯存試驗中,隨著貯存時間的增加,金絲界面層IMC(Intermetallic Compound)厚度和金屬間化合物不斷增長,失效破壞位置越來越多地出現在鍵合界面處,鋁金屬化層附近的金含量因擴散而增高,金鋁鍵合界面處IMC界面層厚度的增加降低了界面結合強度。
0 引言
金絲應用于集成電路和半導半導體分立器件的引線鍵合封裝,由于該工藝制造成本低且具有較高的通用性,成為電子產品封裝互聯的關鍵技術。新一代高密度互聯用金絲材料越來越多地應用于小型化微電子產品中,如基于一體化MCM(多芯片組件)技術的射頻鏈模塊多芯片組件,其封裝可靠性直接關系到微波信號傳輸質量。電子產品小型化、模塊化以及高集成化的發展趨勢,要求鍵合金絲具有更加優異的鍵合穩定性和可靠性。鍵合金絲的焊接工藝一般基于熱超聲鍵合,金絲與芯片之間的金屬化層之間通過原子間的擴散形成鍵合界面,鍵合界面的牢固性對微波電路互聯可靠性起著至關重要的作用,界面層金屬間化合物的過度生長會使接觸電阻和熱阻增大,并且降低鍵合點機械性能。
微波電路在航天器中應用廣泛,對鍵合金絲的耐高低溫特性具有較高要求。金絲在微波電路中使用數量多,鍵合界面復雜,界面多為金—金金屬化、鋁—金金屬化層。航天器在發射和在軌運行過程中服役溫度范圍達到-65~150 ℃,所產生的熱載荷對微波電路互聯用金絲界面組織性能產生較大的影響。在高溫條件下,鍵合金絲和各類不同基板構成的多芯片組件產品在金-鋁鍵合界面中會生成Kirkendial空洞,或產生脆性相金屬間化合物,鍵合強度降低,
甚至脫焊。國內外研究表明高溫貯存產生的熱應力和金屬間化合物脆性相容易造成鍵合焊點的脫落或斷裂,但對金絲界面空間高低溫特性演化的規律仍缺乏系統性研究,為提升金絲材料長期空間服役可靠性,本文通過鍵合金絲的高低溫界面顯微組織變化分析、成分和界面層遷移分析、界面結合性能表征,對金絲及其鍵合樣件的機械特性以及鍵合界面高低溫特性演變規律進行研究,獲取金鋁鍵合界面性能退化規律,擬為微波電路互聯用鍵合金絲的封裝可靠性評價提供技術支持。
1 實驗
1. 1 材料
金絲材料采用純度 99. 99% 以上的金,經過熔鑄、拉拔和退火工藝形成用于鍵合的金絲。熔鑄過程中適當添加微量元素以增加其力學性能與應用可靠性,微量元素總和<0. 01%的前提下,采用拉絲工藝和退火工藝以保證金絲的焊接強度、熱穩定性,并提高絲材的耐熱性和成球性。
采用金絲球焊設備在硅芯片鋁焊盤上鍵合高密度金絲形成金鋁鍵合的試驗樣件,其鍵合位置如圖1所示。
1. 2 試驗過程
金絲鍵合界面微觀組織結構分別采用金相顯微鏡和JSM-6360LV掃描電子顯微鏡(SEM)觀察,采用掃描電子顯微鏡能譜儀(EDS)分析鍵合點金屬間化合物成分與界面遷移、元素擴散情況,參照 GB/T34895—2017、GB/T 17359—2012、GB/T 16594—2008中的方法進行測試。采用CMT5105微機控制電子萬能試驗機測試鍵合前絲材拉力,采用 Series 4000-0拉力剪切力測試儀測試金絲鍵合后拉力。
高低溫交變循環試驗采用CY-0瑞萊沖擊試驗箱進行測試,采用低溫(-65±5) ℃到高溫(150±5) ℃之間的溫度轉換,高、低溫之間轉換時間間隔小于5s,達到最高最低溫度后保溫10 min,溫度循環次數分別為100次、300次、500次。高溫貯存試驗箱采用電熱鼓風干燥箱,加熱溫度為 150 ℃,樣件分別貯存100、500、1 000 h后取出,樣品取出后分別對金絲單絲在不同貯存時間點的拉伸性能、鍵合金絲樣件的鍵合拉力和Si芯片金鋁鍵合試驗樣件界面組織結構的變化進行測試。
2 結果與討論
2. 1 球焊工藝成球質量
為評價球焊工藝成球質量,在薄膜陶瓷鍍金基板上焊接金絲,采用45倍金相顯微鏡觀察焊點外觀,如圖2(a)所示,金絲鍵合焊點均無起翹、脫落現象。抽樣10個焊點在光學顯微鏡下進行焊點尺寸測量,球焊鍵合點直徑在2~5倍金絲直徑之間。將球焊過程中燒成的金絲球取下來,采用掃描電鏡觀察金絲球的外觀質量,如圖 2(b)所示,金絲球成規則的球形,表面光滑,無沾污、凹坑等缺陷,金絲球兩個方向上的直徑分別為71. 32和70. 99 μm,對10個燒成金絲球直徑進行統計,其平均直徑為71. 1 μm。
2. 2 高低溫交變環境后的界面組織演變
對金鋁(AuAl)鍵合樣件進行高低溫交變循環試驗并進行試驗后的界面性能分析,得到的AuAl鍵合界面微觀組織結構如圖3所示。圖3(a)為試驗前鍵合界面金相圖,從圖中沒有觀察到明顯的界面金屬間化合物(IMC)層;圖3(b)~(d)分別為高低溫交變循環試驗100次、300次、500次后的金絲鍵合界面金相圖,可以看出AuAl界面層呈點狀或條帶狀分布,厚度不均勻,且隨循環次數的增多而逐漸變得明顯。
SEM對高低溫交變循環試驗后鍵合點界面層厚度、成分與界面遷移、元素擴散情況分析結果如圖4所示。溫度交變試驗100次后,AuAl鍵合界面已經形成了金屬間化合物層,從圖4(b)可以看出,界面分為兩層,分別進行EDX能譜分析得到,靠近金絲球的A點Au和Al原子比約為4∶1,靠近Al金屬化層的B點Au和Al原子比約為5∶2,由原子體積分數百分比推出靠近金絲球的主要成分為 Au 4 Al,靠近 Al金屬化層的主要成分為Au 5 Al 2 。溫度交變循環試驗300次后,界面層C部位的主要成分接近于Au 4 Al。溫度交變循環試驗500次后,界面層D部位的成分主要為Au 4 Al。具體情況見表1。
由于 AuAl鍵合不同溫度交變循環次數后的界面層在電鏡中觀察并不呈連續排布,對厚度測量數值進行統計,其分布情況如圖5所示。100次溫度循環后的IMC層厚度分布在1. 3~2. 2 μm,且IMC層厚度多在低厚度值范圍內分布;300 次溫度循環后的IMC 層厚度約為 1. 7~2. 3 μm;500 次溫度循環后的IMC 層厚度約為 2. 1~3. 3 μm。可見隨循環次數增加,焊接界面微觀組織結構中IMC界面層逐漸變厚。Au-Al界面層厚度和金屬間化合物種類隨著元素、晶界、空位等的擴散而變化,隨著高低溫循環次數的增加,鍵合點靠近Si芯片Al金屬化層附近的金屬間化合物由于Au元素的擴散由最初生成的Au 5 Al 2 逐漸轉化成 Au含量較高的 Au 4 Al,同時靠近金絲球的界面逐漸出現了Kirkendial孔洞,因Au向Al中擴散速率比Al向Au中擴散速率大,從而使得靠近界面的金球附近逐漸出現空位聚集并出現孔洞。
2. 3 高溫貯存后的界面組織演變
將金鋁(AuAl)鍵合樣件在 150 ℃(允許+5 ℃正偏差)環境溫度下保持1 000 h,設置中間檢查點100、500 h,試驗后分別利用金相顯微鏡和掃描電鏡進行AuAl鍵合界面形貌分析,并得到焊接界面微觀組織結構和界面遷移、元素擴散演變情況。圖6(a)~(c)分別為高溫貯存100、500、1 000 h后的金絲鍵合界面金相圖,高溫貯存100 h后,AuAl鍵合界面已經形成,界面層厚度不均勻且隨高溫貯存時間的增加而逐漸變厚。利用掃描電子顯微鏡對高溫貯存試驗后鍵合點界面金屬間化合物層的厚度、成分與界面遷移、元素擴散情況進行分析,如圖7所示。
高溫貯存100 h后,圖7(b)中靠近金絲球的A點Au和Al原子比約為5∶2,靠近Al金屬化層的B點Au和Al原子比約為2∶1,表明靠近金絲球的金屬間化合物主要成分為Au 5 Al 2 ,靠近Al金屬化層的金屬間化合物主要成分為Au 2 Al。高溫貯存500 h后,圖7(d)界面層C點的成分接近于金屬間化合物Au 5 Al 2 。高溫貯存1 000 h后,圖7(f)中靠近金絲球的E點Au和Al原子比約為77∶23,靠近Al金屬化層D點的Au和Al原子比約為74∶25。與圖7(d)相比,Au元素隨高溫貯存時間的延長,逐漸向靠近Si芯片的Al金屬化層附近擴散。具體情況見表2。
對不同高溫貯存時間后的AuAl鍵合IMC界面層厚度值進行統計,其分布情況如圖8所示。高溫貯存100 h后 IMC層厚度為 2. 2~3. 6 μm;高溫貯存 500 h后的IMC層厚度為6. 7~7. 2 μm;高溫貯存1 000 h后的IMC層厚度為8. 3~9. 8 μm。隨著高溫貯存時間的增加,焊接界面微觀組織結構中IMC界面層厚度增長較明顯,說明在150 ℃溫度條件下AuAl金屬間化合物的生長較快。
Au-Al金屬間化學物生長厚度一般滿足以下經驗公式:
式中,δ為金屬間化合物厚度,K為金屬間化合物的生長常數,t為老化時間,n為時間指數。
根據普遍研究認為:當n=1時,金屬間化合物的生長為界面反應控制,此階段屬于初步反應階段;當n=2時,金屬間化合物的生長為擴散控制,Au原子通過Al金屬化層的孔隙和晶界擴散與Al結合形成金屬間化合物;當n≥3時,金屬間化學物的生長為選擇擴散控制,一種金屬原子無法通過金屬間化合物介質層與另一種原子結合,只能從金屬間化合物的晶界擴散到另一種金屬中,隨著反應時間的增加,n值逐漸增大,反應速率不斷減小。
圖9為150 ℃的條件下,Au-Al金屬間化合物的IMC層平均厚度隨高溫貯存時間變化的曲線圖,對IMC厚度與老化時間的關系進行非線性擬合,由擬合結果得出,當 n=2 時,擬合的匹配度為 R 2 =0. 990 5,Au-Al金屬間化合物的生長符合拋物線的擬合。因此,高溫貯存條件下,金屬間化合物的生長為擴散控制,說明AuAl鍵合IMC界面層的反應機理為Au、Al金屬的相互擴散并結合成金屬間化合物為主,與圖7中焊接界面微觀組織結構中不同高溫貯存時間后AuAl鍵合界面金屬間化合物層的成分與界面遷移、元素擴散情況的分析結果相符。
2. 4 金絲鍵合拉力及失效模式演化
圖10顯示AuAl鍵合拉伸斷裂載荷隨不同交變溫度循環次數變化不大,溫度循環后鍵合拉力略有升高,其中300次溫度循環后,鍵合拉力升高,一定程度的金屬間化合物生長可以提高鍵合界面的硬度和強度,但隨著金屬間化合物的繼續生長,鍵合點機械性能降低。如表3所示,金絲鍵合失效模式以鍵合點(AuAl鍵合界面處)失效和中間引線斷裂為主,15個抽樣測試點中,100次和500次溫度循環后分別出現一次鍵合點失效。與溫度循環試驗前相比,溫度循環后金絲鍵合拉力的離散性減小,說明溫度循環對拉拔后金絲的力學性能均勻性起到促進作用,這可能與拉拔后金絲殘余應力的降低有關。
圖11顯示隨高溫貯存時間的延長,金絲AuAl鍵合拉力呈現逐漸下降的變化規律。高溫穩定性試驗中在貯存不同時間后,對金絲絲材的拉斷力進行測試并與金絲鍵合后的拉力進行對比,說明隨著高溫貯存時間的增加,金絲鍵合拉力破壞位置越來越多地出現在鍵合焊點界面處,鍵合界面因產生越來越多的金屬間化合物脆性相且界面IMC層厚度不斷增大,引發鍵合界面強度的降低。但經過150 ℃條件下1 000 h貯存試驗后,金絲鍵合拉力仍高于2 gf,符合航天器微波電路組件的設計使用要求。
金絲與Al焊盤反應形成的金屬間化合物IMC在一定程度上能夠使焊接接頭更加牢固,起到鍵合作用,焊點界面處形成彌散分布的微小金屬間化合物可以改善焊料的抗疲勞能力或連接強度,但是由于金屬間化合物通常為脆硬相,延性較差,較多的金屬間化合物會導致鍵合拉力的降低。如表4所示,高溫貯存500 h后的IMC層厚度與100 h相比,增長了約2. 2倍,鍵合點失效個數明顯增加,導致鍵合拉力的降低。高溫貯存1 000 h后,失效主要發生在AuAl鍵合界面處,界面強度成為影響引線材料互聯封裝可靠性的主要因素,而較厚的IMC界面層在外力作用下容易在界面處產生應力集中,降低了界面結合強度。
3 結論
(1)通過金絲球焊工藝成球質量分析,發現金絲鍵合焊點均無起翹、脫落現象,球焊鍵合點直徑在2~5倍金絲直徑之間,焊合良好。球焊過程中燒成金絲球呈規則的球形,表面光滑,無沾污、凹坑等缺陷,金絲球的平均直徑為71. 1 μm。
(2)隨高低溫交變試驗循環次數的增加,AuAl鍵合界面層厚度逐漸增加,且隨著Au、Al化學元素的遷移在界面處生成金屬間化合物,隨著高低溫循環次數的增加,鍵合點靠近Si芯片Al金屬化層附近的金屬間化合物由于Au元素的擴散由最初生成的Au 5 Al 2 逐漸轉化成Au含量較高的Au 4 Al。300次溫度循環后,鍵合拉力略有升高且離散性減小,一定程度的金屬間化合物生長提高了鍵合點的可靠性,此外,溫度循環對拉拔后金絲的力學性能均勻性起到促進作用。
(3)高溫貯存試驗后的鍵合界面層厚度隨貯存時間增長較快,由于Au元素的擴散Al金屬化層附近的界面組成由Al含量較高的相逐漸向Au含量較高的相轉變,鍵合界面因產生越來越多的金屬間化合物使界面IMC層厚度不斷增大。
(4)通過金絲鍵合拉力及失效模式演化分析,獲取了金鋁鍵合界面金屬間化合物生長與鍵合拉力和鍵合點失效模式的變化關系,隨著高溫貯存時間的增加,因界面層IMC層厚度的增大,金絲鍵合拉力破壞位置越來越多地出現在鍵合焊點界面處,引發鍵合界面強度的降低。當金絲在高溫環境中長期使用時,應注意界面特性變化對微波電路互聯金鋁界面結合強度的影響,在金絲材料的選用與產品設計過程中,應充分考慮溫度對鍵合界面結合性能的影響,根據試驗結果確立金絲高溫應用邊界條件。
通過對金絲界面空間高低溫特性演化規律研究,可為微波電路及其他集成電路的設計研制、失效分析及材料應用驗證等工作提供借鑒和參考。
審核編輯 黃宇
-
集成電路
+關注
關注
5388文章
11562瀏覽量
362041 -
微波電路
+關注
關注
2文章
59瀏覽量
17419
發布評論請先 登錄
相關推薦
耐高低溫對于工業級連接器為什么“不可或缺”?解讀DH系列連接器寬域耐高低溫性能
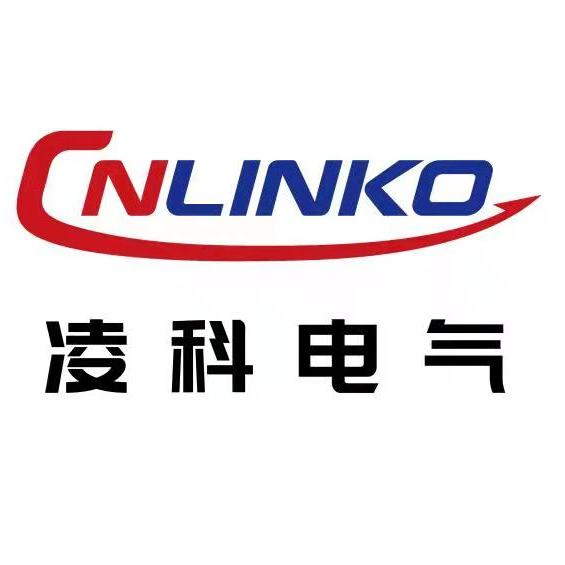
高低溫試驗箱降溫原理是什么
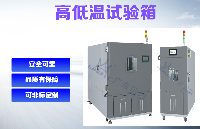
淺析高低溫環境測試設備的使用與維護
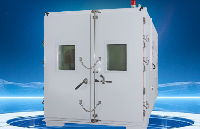
電源模塊高低溫試驗的必要性與應用
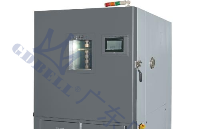
高低溫交變試驗箱:科技的溫控先鋒
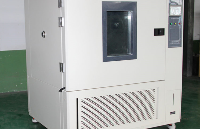
防爆高低溫試驗箱有什么標準?
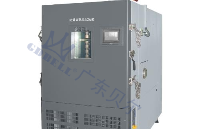
怎樣選擇一款合適的高低溫試驗箱?高低溫測試設備采購指南
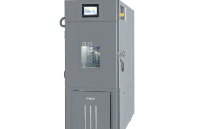
電源模塊高低溫老化測試方法與步驟
工藝參數對鍵合金絲質量影響的研究
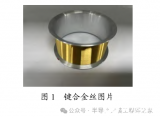
如何讓高低溫沖擊試驗箱的壽命更長
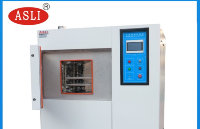
評論