隨著新能源汽車市場需求的變化,電驅系統的集成化、輕量化發展趨勢明顯。高度集成的電驅系統成為研究熱點,特斯拉model 3動力總成代表的油冷電驅系統成為新能源高端汽車的重要方向。電驅系統中用于潤滑減速器齒軸和軸承的潤滑油還需用于冷卻電機。潤滑油量的確定要同時兼顧機械本體的潤滑,還要考慮電機散熱以及系統效率等諸多因素的影響。相較于傳統減速器,油冷電驅系統油量的確定是一個技術上的難點,缺少實用的經驗。本文分析了影響油冷電驅系統冷卻與潤滑的機理,在綜合考慮系統的冷卻、潤滑和效率最優的前提下,建立了一套油冷電驅系統油量的設計原則。基于該設計原則,分析了某款160 kW油冷三合一電驅系統的基本油量的設計過程,并通過效率試驗分析得到了該驅動系統的最佳油量。
1 油冷電驅系統冷卻與潤滑
通常油冷電驅系統包括驅動電機、電機控制器和變速器三部分。電驅系統的冷卻直接影響系統的使用壽命和運行的可靠性;變速器的齒輪傳動通過加強潤滑措施可以有效地防止或者減輕齒面點蝕、齒面膠合的現象出現;軸承的潤滑情況的好壞直接影響了軸承的壽命。永磁同步電機在運行時,當系統溫度超過一定的限值,由于電機中一般絕緣材料的耐熱等級是最差的,會損壞繞組的絕緣,輕則加速絕緣層的老化過程,縮短電機壽命,重則絕緣層碳化變質,對電機造成功能性損傷[1]。過高的溫升不僅會破壞繞組的絕緣,還會造成定轉子鐵心破損和永磁體熱退磁等后果,降低電機的使用壽命[2-4]。故油冷電驅系統的油路設計必須要充分考慮齒輪、軸承的潤滑[5],同時還要考慮電機各部件的冷卻需求,使其電驅系統的溫度保持在合理范圍內,以確保系統安全高效地運行。
1.1 油冷電驅系統功率損耗的來源
本文研究的油冷電驅系統區別于傳統的水冷電驅系統,驅動電機和變速箱共腔體,并共用一套冷卻潤滑系統。故油冷電驅系統的油量設計需要同時考慮電機和減速器的相關影響因素。
驅動電機的功率損失主要包括鐵損耗、繞組損耗、機械損耗、雜散損耗等;減速器的功率損失主要包括齒輪損耗、軸承損耗、油泵損耗和油封損耗。這些損耗絕大部分都轉化為熱能,表現為總成溫度的升高[6]。
驅動電機中機械損耗、鐵損耗、部分雜散損耗與電機負載大小無關,為固定不變的損耗;另外一部分比如繞組損耗和剩余雜散損耗,是會隨著電機負載和電流變化的。所以油冷電驅系統的注油量必須要保證電機得到充分的冷卻。油泵損耗是采用油冷電驅系統才有的功率損耗;另外三部分是傳統的機械損耗。變速器對于溫度要求沒有電機嚴格,但是由于其功率損耗的來源主要是機械損耗,而充分的潤滑能夠有效的減少機械損耗,進而達到減少功率損耗的目的。所以油冷電驅系統的注油量必須要滿足變速器的潤滑需要,油冷電驅系統的油量設計必須同時考慮到電機的冷卻和變速器的潤滑。
1.2 油冷電驅系統的潤滑冷卻原理
本文的油量研究對象是某三合一油冷電驅系統。該套系統的冷卻系統不但考慮了冷卻電機,還考慮了齒輪、軸承的潤滑,該系統的油量從冷卻、潤滑和效率三個方面情況進行綜合考慮。
某油冷三合一電驅系統外形如圖1所示。該油冷三合一電驅系統的冷卻系統是由動力泵提供動力,殼體、端蓋、轉軸、集油環和油管等組成油路。動力泵將冷卻油輸送到設計的位置,以實現電機的定子鐵芯、繞組端部、轉子鐵芯、電機軸承、變速器輸入軸軸承和中間軸軸承等零件的冷卻和潤滑。油路循環從油泵開始,冷卻油通過油泵入口進入冷卻油路,途經過濾器、散熱器,然后油路一分為二,一路進入電機,冷卻油沿著定子沖片上的油路冷卻定子鐵心、電機兩端繞組外側;另一路冷卻油一部分潤滑變速器輸入軸和中間軸的后軸承,另一部分沿著油路冷卻電機轉軸芯部、轉子鐵心和電機兩端繞組內側,同時潤滑變速器輸入軸和中間軸的前軸承;最終,冷卻油由于重力作用回到箱體的最低位置,即油泵的入口位置,循環結束。油路走向如圖2所示。
圖2 油路走向
通過對該油冷電驅系統油路的分析可知,與傳統的減速器不同,系統的油量不僅需要滿足變速器的齒輪、軸承等零件的潤滑,還要滿足電機冷卻。如果該套系統的油量過多,在電驅系統高速運行工況段,變速器部分產生的攪油損失,會嚴重降低系統效率;如果系統的油量偏少,則會造成潤滑不足、冷卻不足,影響系統的使用壽命。本文為如何確定油冷主動潤滑電驅系統的油量提供了一種解決思路。
2 油冷電驅系統油量設計原則
根據油冷電驅系統的冷卻系統的作用原理,先考慮滿足系統油冷和潤滑的基本油量,進而考慮系統效率最優,最終確定油冷電驅系統的油量。在油冷電驅系統中添加的介質油是需要同時滿足電驅系統的冷卻和潤滑。文中的冷卻油和潤滑油均指的是介質油。
2.1 測試工況
由于電驅系統的使用外部條件直接影響電驅系統的性能表現,為了客觀評價電驅系統的性能表現,首先要確定電驅系統后期測試的條件。為了對電驅系統的性能分析能夠相對全面,選定的性能測試主要考察瞬態表現和穩態表現兩部分[7]。電驅系統的瞬態表現的考察主要依據整車的耐久試驗工況,比如新歐洲駕駛循環測試(New European Driving Cycle, NEDC)工況和世界輕型測試循環(World Light Vehicle Test Cycle, WLTC)工況進行考量。從本質上考慮,NEDC側重于穩態工況,WLTC更注重瞬態和過渡工況,如圖3所示。在綜合考慮工況本身、市場選擇等因素的情況下,選擇WLTC工況作為瞬態工況考察日常行駛時電驅系統的散熱性能測試更具意義。
圖3 WLTC工況
在高速工況下,電驅系統的減速器部分攪油損失達到最大,減速器的飛濺潤滑和外部殼體的散熱效果也是達到極致的工況。在高速工況下,電驅系統在額定功率下,以最高輸入轉速運行,持續運行2小時。與高速工況不同,高扭工況下電機、各機械零部件的發熱量很大,而外部散熱條件和減速器飛濺潤滑條件一般,能夠最大程度地考驗電驅系統的冷卻能力。在高扭工況下,電驅系統在額定功率下,以最大輸入扭矩運行,持續運行2小時。根據以上分析,在設計油冷電驅系統時,綜合考慮WLTC工況、高速工況和高扭工況三種工況來進行系統的油量設計。
2.2 理論基本油量
本文研究的油冷電驅系統是現在市面上最為常見的電機和減速器共一套冷卻潤滑系統,控制器單獨一套冷卻系統。故油量設計不需要考慮控制器的冷卻。油量設計只需要考慮電機和減速器部分。由于油冷電驅系統中的電機部分對溫度最為敏感,而以機械結構為主的減速器對潤滑要求相對較高。雖然電機也存在很大部分的機械結構,但是由于內置主動冷卻系統的設置,機械結構的潤滑狀況相對于以前外置冷卻系統而言,已經有了質的改變,基本潤滑條件是可以得到保證的。而減速器由于齒輪嚙合、軸承摩擦也會產生大量的熱。但是考慮到此類機械結構的材料都是耐高溫的,而且減速器的最高許用溫度也是遠低于電機的發熱溫度,故減速器的冷卻不需要單獨考慮。綜上,將電驅系統的冷卻簡化為電機的冷卻,將電驅系統的潤滑簡化為減速器的潤滑。
本文將滿足電驅系統的冷卻簡化為滿足電機的冷卻。考慮到電機部分的冷卻系統的復雜性,選擇從電機的總功率損耗進行分析,得到電機的發熱量,進而求得電機需要的散熱量,最后依據電機設計的平衡溫度和冷卻油的冷卻能力,估算得電機冷卻需要的油量。電機的損耗主要包括鐵心損耗、繞組損耗、機械損耗、雜散損耗等[3]。油冷冷卻系統的散熱形式跟其他冷卻系統不同,是以傳導散熱為主,結合輻射散熱和對流散熱?;谟邢拊?,對本文研究樣機的電機流場和溫度場進行計算,估算得電機內部各點的溫度值,具體的計算原理和方法見參考文獻[1]。該電驅系統在峰值功率運行時,電機發熱最嚴重且對溫度最為敏感的端部繞組的溫度分布情況如圖4所示。本文以該工況下的端部繞組的溫度為電機冷卻的目標,作為系統理論基本油量設計的冷卻部分的油量參考。
圖4 電機端部繞組溫度分布示意圖
關于電機發熱功率,結合電機的設計綜合效率90%,求得電機發熱功率。由于電機的主要冷卻方式是傳導散熱,為了簡化計算,假設電機的散熱完全依賴電驅系統的冷卻系統的散熱功能,即電機產生的熱量全部由冷卻介質帶走,同時在油泵正常運行時,冷卻循環的油道充滿潤滑油,根據公式(1),計算油泵的流量Q。結合油道結構長度L,考慮到潤滑油回油需要時間,故提出回油系數CL,取1.1;根據公式(2),計算滿足電機冷卻需求的基本冷卻油量V1:
?(1)
V1=Q?L?CL(2)
由于電驅系統的潤滑轉化為變速器的潤滑。本文研究樣機中潤滑方式還是以飛濺潤滑為主,主動潤滑為輔。飛濺潤滑的油量確定方法可以依據傳統變速器的潤滑油確定原則,減速器靜置時,最低油液面要淹沒豎直方向上位置最低齒輪的輪齒的齒頂圓,如圖5所示,將數模導入計算流體動力學(Computational Fluid Dynamics, CFD)仿真軟件nanoFluidX,計算得滿足變速器潤滑需要的基本潤滑油量V2。
圖5 最低變速器潤滑液面高度
綜上所述,滿足電機冷卻的油量V1和滿足變速器潤滑的油量V2,兩部分油量之和為油冷電驅集成系統的理論基本油量V0。
V0=V1+V2(3)
一般電驅系統在結構設計完成后,系統效率就基本確定。為了進一步優化系統效率,同時也能有效控制產品成本,優化油冷電驅系統油量有著重要的意義。在滿足電驅系統冷卻和潤滑的基本需求之后,如何進一步提高效率是下面探討的問題。由于需要綜合考慮電機發熱、變速器潤滑和齒輪攪油等對電驅系統綜合效率的影響,考慮到CFD流體仿真模型跟多偏向于定性的分析,故采用試驗的方法來進一步優化油冷電驅系統的油量。
3 優化系統油量試驗
優化系統油量試驗,建立在系統效率最優的前提之下,基于傳動系統效率試驗的試驗方法,采用WLTC工況、高速工況和高扭工況三種工況結合作為試驗工況進行試驗。
在三合一綜合試驗臺對本文研究的樣機進行試驗。試驗依據主要是《純電動乘用車用減速器總成技術條件》(QC/T 1022-2015)和《S1T40A三合一電驅系統傳動效率試驗大綱》,樣機的基本參數如表1所示。
表1 160 kW油冷三合一電驅系統的基本參數表
上文計算的理論基本油量為2.3 L,試驗分五組進行,基于控制變量法,確保五組試驗條件的區別僅在于試驗箱中的注油量,五次傳動效率試驗的試驗油量分別是2.3 L、2.4 L、2.5 L、2.6 L、2.7 L,試驗結果如表2所示。本樣機在油量為2.5 L時,系統的平均綜合效率最高。
表2 不同油量下,樣機的平均綜合傳動效率對比
4 結論與展望
本文基于某160 kW的油冷三合一電驅系統的油量進行設計分析,建立了一套適用于油冷電驅系統的油量設計方法,詳細說明了該套方法在實際產品上的應用,得到該套系統的最佳油量。
審核編輯:黃飛
-
電機
+關注
關注
142文章
9021瀏覽量
145494 -
集成系統
+關注
關注
0文章
44瀏覽量
9810 -
變速箱
+關注
關注
4文章
171瀏覽量
18735 -
驅動電機
+關注
關注
9文章
410瀏覽量
30730 -
電驅系統
+關注
關注
0文章
113瀏覽量
2384
原文標題:關于油冷電驅系統油量的分析
文章出處:【微信號:EDC電驅未來,微信公眾號:EDC電驅未來】歡迎添加關注!文章轉載請注明出處。
發布評論請先 登錄
相關推薦
空調系統分類及分別適用于哪些場合?
1206封裝貼片電適用于哪些產品上
適用于在1GHz以下頻段以EnOcean無線電標準進行通信的系統
eDM電驅模塊概述
適用于PDA的PLC編程系統開發
適用于直驅式風電系統的Crowbar電路分析
適用于汽車冷起動應用的雙開關降壓/升壓技術
油冷器管板腐蝕的原因及解決方法
冷油器管板如何防腐
UltraFAST設計方法指南(適用于Vivado Design Suite)
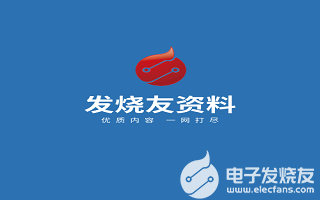
UltraFAST設計方法指南(適用于Vivado Design Suite)
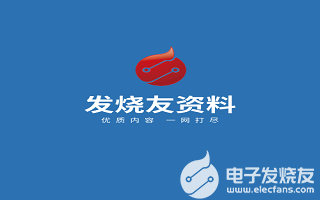
評論