統的硅功率器件工藝中,高溫擴散和離子注入是最主要的摻雜控制方法,兩者各有優缺點。一般來說,高溫擴散工藝簡單,設備便宜,摻雜分布輪廓為等向性,且高溫擴散工藝引入的晶格損傷低。離子注入工藝復雜且設備昂貴,但它可獨立控制摻雜元素的濃度和結深,雖然也會給襯底引入大量的點缺陷和擴展缺陷。
碳化硅功率器件摻雜工藝中,常用的摻雜元素有:N型摻雜,主要為氮元素和磷元素;P型摻雜,主要為鋁元素和硼元素,它們的電離能和溶解極限見表1(注:hexagonal (h) and cubic (k))。
▲表1. SiC中主要摻雜劑的電離能和溶解極限
圖1是SiC和Si中主要摻雜元素的擴散系數隨溫度變化圖。摻雜元素在硅中的擴散系數較高,所以在1300℃左右就可以實現高溫擴散摻雜。與硅中擴散系數相比,磷、鋁、硼和氮元素在碳化硅中的擴散系數都很低,因此碳化硅中需要2000℃以上的溫度才能得到合理的擴散系數。高溫擴散會帶來很多問題,如引入多種擴散缺陷會惡化器件的電學性能,無法使用常見的光刻膠作掩膜等等,所以離子注入工藝成為了碳化硅摻雜的唯一選擇。
▲圖1. SiC和Si中主要摻雜雜質的擴散常數對比圖
在離子注入過程中,離子因為與襯底晶格原子碰撞逐漸失去能量,同時會將能量轉移給碰撞原子。這些轉移的能量會使碰撞原子從晶格的束縛能中釋放出來。這些獲得自由的原子在襯底內繼續運動,并會與其他的晶格原子繼續碰撞,將其他原子從晶格中碰離出來。這些過程將持續進行,直到沒有任何一個自由原子有足夠的能量把其他晶格原子釋放出來為止。
因為離子注入過程中離子總數非常大,以至于襯底中靠近表面部分造成大量的晶格損傷,損傷的效應與劑量、能量等離子注入參數有關系,一般來說會隨著劑量與離子能量的增大而增大。如果注入的劑量過高,靠近襯底表面的離子射程內,襯底的晶體結構會完全破壞而變成非晶態。這種晶格損傷必須在退火過程中修復成單晶結構并激活摻雜物。
在高溫退火過程中,原子可以從熱能中獲得能量并進行快速熱運動。當運動到單晶晶格位置中具有最低自由能,它就會停留在此位置。所以被破壞的非晶態中的碳化硅與摻雜原子,將在靠近襯底界面位置,通過落入晶格位置并且被晶格能束縛后完成了單晶結構構建。這樣晶格修復和提高激活率是在退火過程中同時完成的。
有研究報道了在SiC中摻雜元素的激活率與退火溫度的關系(圖2a)。其中外延層和襯底均為N型,在外延層上分別注入氮、磷元素,注入深度0.4μm,總注入劑量為1×1014cm-2。從圖2a可以看出氮元素在1400℃退火后激活率小于10%,在1600℃退火可以達到90%的激活率。磷元素的情況類似,只有退火溫度達到1600℃時,激活率才能達到90%。
▲圖2a. SiC中不同退火溫度下,不同元素的電激活率
對于P型的離子注入工藝,由于硼元素的異常擴散效應,一般都使用鋁元素作為摻雜劑。和N型注入類似,當退火溫度達到1600℃,可以顯著提高鋁元素的激活率。但Negoro等人研究發現,即使在500℃下高溫離子注入鋁元素,測量到的方阻在3000Ω/square達到飽和(圖2b),即使繼續加大注入劑量,方阻也沒有進一步降低,這說明鋁元素已經不再電離。所以目前使用離子注入制作P型重摻雜在工藝上還是一個挑戰。
▲圖2b.SiC中不同元素的電激活率與注入劑量的關系
摻雜元素的結深和摻雜濃度是離子注入工藝最要的因素,它直接決定了后續器件的電學性能,必須要嚴格控制。二次離子質譜儀(SIMS)可以用來測量離子注入后的摻雜元素的結深和摻雜濃度。
審核編輯:湯梓紅
-
半導體
+關注
關注
334文章
27563瀏覽量
220315 -
功率器件
+關注
關注
41文章
1781瀏覽量
90515 -
SiC
+關注
關注
29文章
2845瀏覽量
62759 -
碳化硅
+關注
關注
25文章
2786瀏覽量
49136
原文標題:碳化硅離子注入和退火工藝介紹
文章出處:【微信號:芯長征科技,微信公眾號:芯長征科技】歡迎添加關注!文章轉載請注明出處。
發布評論請先 登錄
相關推薦
鉺離子注入碳化硅后的射程分布和射程離散
碳化硅深層的特性
碳化硅MOS的結構與優勢
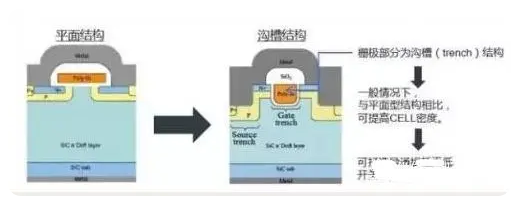
6.2.3 濕法腐蝕∈《碳化硅技術基本原理——生長、表征、器件和應用》
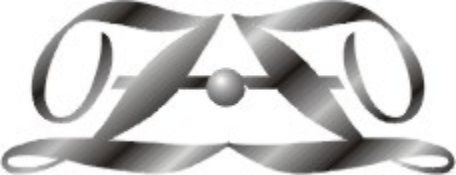
6.1.4 半絕緣區域的離子注入∈《碳化硅技術基本原理——生長、表征、器件和應用》
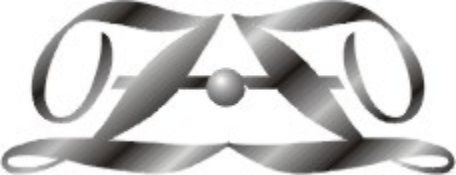
6.1.3 p型區的離子注入∈《碳化硅技術基本原理——生長、表征、器件和應用》
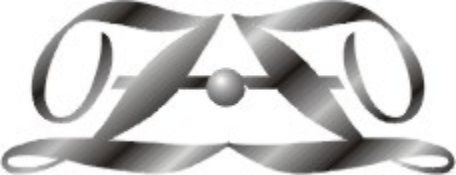
6.1.1 選擇性摻雜技術∈《碳化硅技術基本原理——生長、表征、器件和應用》
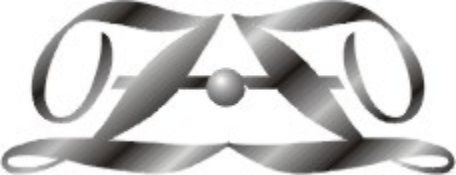
6.1.5 高溫退火和表面粗糙化∈《碳化硅技術基本原理——生長、表征、器件和應用》
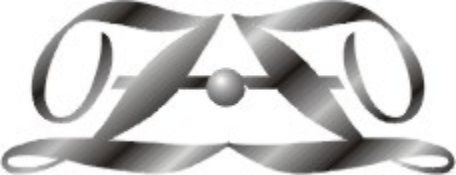
6.2.1 反應性離子刻蝕∈《碳化硅技術基本原理——生長、表征、器件和應用》
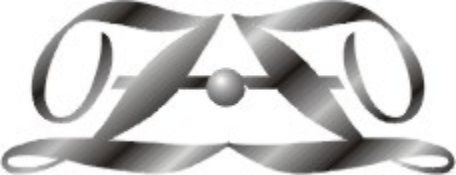
6.2.2 高溫氣體刻蝕∈《碳化硅技術基本原理——生長、表征、器件和應用》
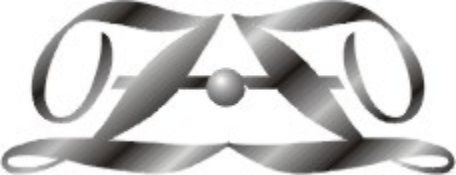
評論