摘 要
為綜合評估SiC功率模塊的液冷冷板散熱效果,設計了串聯、并聯與串并聯三種冷板流道結構, 從器件溫升、系統能效、散熱性能三個方面共計10項指標評估了冷板性能,基于ICEPAK仿真分析了液冷 系統流場與溫度場的穩態分布特征,從節能角度給出了液冷散熱方案的工程應用選擇與優化建議。研究結果表明,冷板內部串聯流道設計的溫升與散熱性能指標更優,但其能效表現系數僅為并聯設計的 1/5,散 熱表現的提升以增加冷板內部壓力損失為代價,降低了其能效表現;冷卻液流量提高3倍而冷板的能效表現系數下降約24倍,提高冷卻液流量并非改善散熱的首選。實際工程應用中,在器件的溫升允許范圍內, 應優先選擇冷板內部的并聯流道設計與多冷板間并聯的散熱方案,以提高散熱系統的節能性。
0 引 言
SiC MOSFET與傳統的硅基相比具有更高的 電子遷移率、更高的開關速度以及更寬的帶隙, 使其在高溫、高頻及高功率方面具備更好的應用前景。然而,隨著其芯片尺寸的小型化以及更 高電壓和電流帶來的功率密度的提升,產生了更 高的熱通量,因而帶來了對低成本、輕量化以及 更高效的散熱解決方案的需求。
功率模塊的熱性能表現直接關系到其工作的可 靠性和使用壽命,功率器件的散熱方式主要包括空 冷、液冷、相變冷卻等,其中液冷散熱是應用最廣泛、技術最成熟的一種方式。目前,對于液冷冷 板的研究主要集中在流道設計與優化方面。張嘉偉、 宋全剛等分別使用了內部為柱狀翅片結構的流道設計和并聯的多管流道設計,以熱阻和冷板壓力損 失為設計目標,基于響應面方法的優化設計來尋找 最優的結構參數。傅航杰等在傳統蛇形槽道流道 基礎上,采用水滴擾流翅柱流道方案進行散熱強化, 并對比分析了兩種流道結構下的器件溫升與冷板壓 力損失。何海斌等使用矩形翅片的U型水道結構, 基于回歸分析法,同樣以溫升與冷板壓降為設計目 標,給出了翅片的結構優化設計。楊剛等設計了 一種串并聯流道冷板,以冷板壓力損失、器件溫升、 溫度分布標準差、換熱系數為評價指標,從冷板的 流動與換熱特性兩個方面評價了冷板的散熱表現。段會強等設計了一款熱管嵌入式水冷散熱器,同時分析了圓柱翅片與矩形翅片結構的散熱作用。
綜上所述,目前對于冷板性能的評價指標多 集中于熱阻、壓力損失以及器件的溫升或溫度分 布方面,而關于冷板的節能效果評價則較少。本 文在傳統電子器件散熱評價指標的基礎上,通過 計算泵功率重點探討了不同冷板設計下的能效表 現系數,以節能性為評價核心,從節能角度給出 了冷板流道的優化建議,并結合工程實際應用給 出了多冷板散熱系統的選擇方案。
1 液冷散熱系統設計
以某電機控制器的半橋SiC MOSFET功率模 塊為研究對象,其結構示意圖與實物圖如圖 1 所 示。功率模塊由多層結構構成,芯片部分為 MOSFET 或肖特基二極管(SBD),此處因功率 損耗而產生的熱量由芯片焊層、絕緣基板、基板 焊層、底板、粘接層、水冷板依次傳遞至冷卻液,利用冷卻液的流動將熱量帶走,從而實現散 熱。其中,芯片為碳化硅;絕緣基板的上下層為銅,中間層為氮化鋁;底板為銅;粘接層為導熱 硅脂;水冷板為鋁合金;冷板內部的冷卻液為體 積分數25%的乙二醇水溶液。
利用器件廠商提供的ROHM Solution Simula‐ tor 計算出額定工況下(電壓 800 V,輸出電流 100 A,開關頻率 60 kHz)的單個 MOSFET 的損 耗為 51. 5 W,單個 SBD 的損耗為 3. 9 W,功率 模塊中共計16個MOSFET與16個SBD,因此總 損耗為 886. 4 W。實際應用中將 6 個功率模塊并 聯構成電機控制器的一相,因此單個冷板所承載 的功耗為 5 318. 4 W。設散熱系統的工作環境溫 度為 35 ℃,冷卻液在冷板出入口的溫差控制在 10 ℃以內,由式(1)可計算出此溫差條件下所需 的冷卻液流量為8. 2 L/min。
式中:Vf為體積流量,m3 /s;Pd為總功耗,W;ρ 為冷卻液密度,kg/m3 ;cp 為冷卻液比熱容,J/(kg·K);tfout為冷卻液的出口溫度,℃;tfin為冷 卻液的入口溫度,℃。基于功率模塊中的芯片分布情況,設計了 3 種水冷板流道結構,如圖 2 所示。冷板尺寸為 498 mm×150 mm×20 mm,考慮到功率模塊在 冷板上的固定,將冷板的入口與出口流道放置于 冷板的兩側位置以避開功率模塊的固定螺孔,圖 中左側為入口,右側為出口,出入口的尺寸為 14 mm×14 mm。流道的主體由3段平行的流道組 成,流道寬度為26 mm,高度為5 mm,為了增加 冷卻液的對流換熱面積,3 段主體流道內增加了 5 行翅片,翅片厚度與翅片間距均為 2 mm。3 段 流道經串聯(見圖2(a))、并聯(見圖2(b))和串并 聯(見圖 2(c))后,構成了 3種流道結構,圖 2(d) 為內部細節示意圖。
2 散熱表現評價
為評估上述 3 種冷板結構的散熱效果,從器 件溫升、系統能效、散熱性能三方面共計10項指 標來完成統計分析。
2. 1 器件溫升指標分析
分別統計 6 個功率模塊中 MOSFET 與 SBD 的最高結溫(tjmax,℃)與最低結溫(tjmin,℃),以評 估器件的溫升上限;進一步分析功率模塊中的溫 差(tjmax-tjmin,℃),用以評估功率模塊中的溫度分 布 特 性 , 同 時 計 算 功 率 模 塊 中 的 器 件 均 溫 (tave,℃),由公式(2)給出溫度的標準差,用于評 估溫度分布的均勻性。
式中:σ為溫度標準差,℃;n為數量;下標j表示結。
2. 2 系統能效指標分析
基于流場計算結果可以給出冷板流道出入口 之間的壓力損失為 Δptotal,進而可由式(3)計算出維持冷板入口流量所需的泵功率 Ppump,該功率僅 為冷板入口的泵功率,并非實際使用的水泵功 率。由于熱設計過程中,對于節能的考慮同樣十 分重要,因此,將上述泵功率代入式(4)可計算 出散熱系統的能效表現系數(CP),該值越大表明 散熱系統在滿足散熱需求的同時只需更低的水泵 功率,其節能效果越好。
2. 3 散熱性能指標分析
熱阻是用于評價散熱性能的一項重要參數, 式(5)為假設一維、穩態傳熱條件下的熱阻計算方法
式中:Rth為熱阻,℃/W;Δt 為基于參考溫度的 溫升,℃;l 為沿傳熱方向的材料厚度,m;k 為 導熱系數,W/(m·℃);A 為導熱面積,m2。因 此,采用基于溫升的計算方法,從冷板表面至冷 卻液間的熱阻為
式中:Rsf為冷板熱阻,℃/W;tsmax為冷板表面溫 度峰值,℃。將整塊冷板等效為一個換熱器,則 由式(7)~式(9)可計算出冷板的換熱效率為
式中:Qact為冷板實際換熱功率,W;Qmax為冷板 理想條件下的最大換熱功率,W;ε為換熱效率。
3 數值模擬與仿真分析
采用 ANSYS-ICEPAK 完成液冷散熱系統的 流固耦合仿真。仿真設置:1)忽略熱輻射與自 然對流,僅考慮散熱系統內部的熱傳導與熱對流 過程;2)流動與傳熱由連續性、動量和能量方 程描述;3)采用 FLUENT 求解器和 SIMPLE 算 法,流動與湍流選擇一階迎風格式,冷卻液為不 可壓縮流;4)除芯片外,忽略溫度對其它材料 物性參數的影響,導熱硅脂與冷卻液的導熱系數 分別為 3 W/(m·℃)和 0. 505 W/(m·℃),其余材料由軟件材料庫提供;5)在考慮出入口的冷卻液溫差為10 ℃的情況下,循環流入冷板的冷卻液溫度為45 ℃,流道內的雷諾數經軟件計算為9772,因此需要考慮湍流,湍流模型選擇標準的k-ε兩方程模型,流道入口為流量邊界,流道出口為壓力出口邊界;6)為提高迭代計算的穩定性,設定動量項的松弛因子為0. 6,殘差設置能量項為10-7,其余為10-3,迭代步數設置為1200步。
計算域內的網格采用ICEPAK提供的六面體占優網格,通過控制并調整3個方向的網格最大尺寸,對3種不同網格數(1 012 726,1 196 222,1 564 758)進行了網格無關性驗證,以流道A設計下的MOSFET器件最高結溫為對比參數,3種網 格 尺 寸 下 的 結 溫 分 別 為110. 8,109. 9和110. 1 ℃,誤差在1%以內,因此,后續仿真均采用上述中等數量的網格劃分。
針對湍流模型的選擇,對比分析了5種不同湍流模型的計算結果,冷板采用流道A設計,計算獲得的MOSFET器件最高結溫數據見表1。計算結果表明,不同湍流模型下的結溫變化較小,誤差在1%以內,因此,本文后續的仿真計算種均采用常用的標準k-ε模型。
將功率模塊沿流道入口向出口方向依次編號 為1號至6號模塊,圖 3 為3種冷板的功率模塊溫 度云圖,圖中左側流道口為入口。計算結果表 明,由于 MOSFET 的功耗較高,因此,高溫區 域主要集中在 MOSFET 芯片所在的位置,其中 流道 A 和 B 的溫度峰值均位于 6 號功率模塊內, 6 個功率模塊依次排列呈溫度遞增的分布趨勢, 溫度峰值分別為109. 9 ℃與115. 8 ℃。流道C的整 體溫度分布規律與前兩種不同,其溫度峰值位于 1號功率模塊內,溫度峰值為 111. 2 ℃,6個功率 模塊的溫度峰值依次呈高-低-高-低的交錯分 布特征,該現象是由冷板中部增加了兩列并聯支 路所造成的。圖 4 為 6 個功率模塊的銅底板外表 面的平均溫度分布曲線,其中流道 A 和 C 的均溫分布規律較為接近,1號至5號模塊的底板均溫變 化較小,靠近出口的 6 號模塊均溫略高。流道 B 的溫度分布呈單向遞增變化,1號模塊均溫最低, 為70. 4 ℃,6號模塊均溫最高,為79 ℃。
表 2 和表 3 分別為 MOSFET 和 SBD 的溫升 指標數據。計算結果表明,流道 A的溫度峰值最 低,溫差最小,溫度的標準差也最小,而流道 C 的 溫 升 指 標 次 之 , 流 道 B 的 各 項 指 標 中 除 MOSFET的器件溫差指標略好于流道C外,其余 指標均表現最差。流道A與B相比,MOSFET與 SBD 的結溫峰值分別下降了 5. 1% 和 5. 4%,溫 度標準差分別下降了11. 4%和14. 9%,僅從溫升 指標對比分析,串聯流道設計在溫升抑制與芯片 溫度分布的一致性方面表現最好。
表 4 為冷板的能效與散熱性能的指標數據。計算結果表明,雖然流道 A的冷板熱阻最小,換 熱效率最高,但其壓力損失達到 30. 5 kPa,因而 其需要更大的泵功率。進一步分析表明,較好的 散熱性能指標建立在更大的壓力損失基礎上,即 提高了泵功率而降低了其能效指標,這樣散熱系 統的成本也會隨之增加。流道 B 的能效表現系數 為 6 407,是流道 A 的 5 倍,從節能的角度考慮, 采用并聯結構的流道設計,能效表現遠超另兩種流道結構。
4 工程應用分析
某實際電機控制器的三相系統共需要18個功 率模塊,其中 6 個模塊并聯控制一相,因此,將 相同的 3 塊水冷板進行并聯或串聯,從而形成該 電機控制器的最終液冷散熱方案。如果采用冷板 間并聯,進出口冷卻液溫差要求不變,仍為 10 ℃,冷卻液總流量為3塊冷板之和24. 6 L/min, 并聯散熱方案的冷板散熱效果可使用第 3 節仿真 獲得的各項指標數據;如果采用冷板間串聯,則 單個冷板的進出口溫差限定在3. 33 ℃,因而計算 獲得的冷卻液流量需求也為 24. 6 L/min,3 塊冷 板的入口溫度分別為 45,48. 33 和 51. 66 ℃。使 用上述參數進一步開展多冷板串聯方案下的散熱 性能評價,并與冷板并聯方案形成對比。
表 5 為 3 塊冷板串聯后的關鍵能效與散熱性能指標數據,圖 5 為3塊冷板串聯后的MOSFET 結溫峰值分布曲線。
表 5 和圖 5 的計算結果表明:串聯后的每塊冷板的壓力損失以及計算獲得的能效表現系數與 換熱效率是相同的,冷卻液的入口溫度僅影響溫 升指標,與能效及散熱性能指標無關。串聯冷板 按照冷卻液流入的先后順序編號為1~3號,其器 件 結 溫 峰 值 按 編 號 依 次 升 高 , 3 號 冷 板 的 MOSFET 結 溫 峰 值 在 3 種 流 道 結 構 下 分 別 為105. 7,109. 6 和 107. 0 ℃,與冷板并聯方案相比 分別下降了 3. 8%,5. 4% 和 3. 8%,溫升指標略 有提升,但能效與散熱性能出現了大幅的下降, CP下降約24倍左右,ε下降約43. 7%~46. 8%。
5 結 論
本文通過對溫升、能效與散熱性能的多指標評 估,綜合分析了3種冷板流道結構下的散熱效果, 并結合工程應用,重點考察了冷板的節能表現,給 出了實際應用中的液冷散熱系統方案選擇與優化建 議,在本文計算條件下的主要結論如下:
1)冷板內部串聯流道設計的溫升抑制與散熱性能最佳,但其能效表現較差;并聯流道設計可 大幅降低冷卻液的壓力損失,其能效表現系數是 串聯流道設計的 5 倍。因此,熱設計時,在器件 溫升的允許范圍內,可優先考慮并聯流道設計。
2)冷卻液的入口溫度僅影響冷板的溫升指標,與能效、散熱性能指標無關,因此,在器件 溫升的允許范圍內,可考慮適當增加冷板進出口 的冷卻液溫差,從而進一步提高液冷散熱系統的 能效與散熱性能。
3)冷卻液的流量影響全部的溫升、能效、散熱性能指標,流量提高3倍,器件結溫峰值可下降約 3. 8%~5. 4%,但冷板的COP下降約24倍左右, 從節能與經濟性方面考慮,提高流量并非改善散熱 性能的首選,應尋求在最小流量條件下,通過優化 冷板內部結構設計來適當增加換熱面積,或使用更 高熱導率的材料及冷卻液的方法。
4)工程應用中的多冷板散熱系統,應首選冷板間的并聯方案,與串聯方案相比,雖然有少量 的器件溫升提高,但其節能效果更符合實際工業 需求。
來源:寬禁帶半導體技術創新聯盟
審核編輯:湯梓紅
-
MOSFET
+關注
關注
147文章
7164瀏覽量
213307 -
功率器件
+關注
關注
41文章
1770瀏覽量
90442 -
SiC
+關注
關注
29文章
2814瀏覽量
62650 -
功率模塊
+關注
關注
10文章
467瀏覽量
45110
原文標題:SiC功率模塊的液冷散熱設計與節能分析
文章出處:【微信號:芯長征科技,微信公眾號:芯長征科技】歡迎添加關注!文章轉載請注明出處。
發布評論請先 登錄
相關推薦
SiC功率模塊和SiC MOSFET單管不同的散熱安裝形式
動力電池的液冷散熱解決方案
SiC功率元器件的開發背景和優點
搭載SiC-MOSFET和SiC-SBD的功率模塊
SiC功率模塊的特征與電路構成
SiC功率器件概述
易飛揚發布通用液冷光模塊技術適用于任何規模和速率的液冷數據中心
具有集成3相SiC MOSFET的液冷模塊
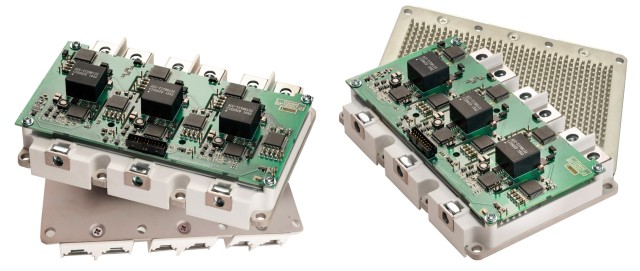
igbt模塊散熱基板的作用及種類 車規級IGBT功率模塊散熱方式
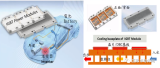
影響IGBT功率模塊散熱的因素
DOH新材料工藝封裝技術解決功率器件散熱問題
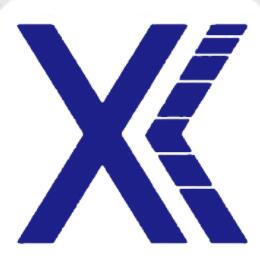
評論