共讀好書
閆旭冬 李文浩 王雁
摘要:
針對微電子管殼類產品的高氣密性封裝,總結了對不同型號產品使用全自動平行縫焊機進行焊接過程中出現的質量問題,并提出了相應的監測及解決方案。采用此方法后經現場生產批量驗證,切實降低了管殼產品的廢品率。 同時總結了全自動平行縫焊設備在設計過程中關于降低靜電危害的措施。 此質量控制方法對微電子封裝工藝中提高良品率具有一定的借鑒意義。
全自動平行縫焊設備是微波器件、混合集成電路及光電器件等高氣密性封裝工藝的后道必需設備,可滿足電子器件小型化、高可靠及長壽命等管殼封裝工藝技術要求。
使用全自動平行縫焊設備對產品進行陣列封裝時,需要實時對產品的焊接質量進行監測。這是因為如果在焊接過程中發生焊接質量問題,勢必會影響核心部件電極輪的表面質量,進而造成后續產品連續報廢。
因此,本文總結了陣列焊接過程中經常出現的質量問題,提出了相應的監測及解決方法,為降低產品在設備傳輸過程中被靜電擊穿的風險,在設備整機設計過程中提出了需要增加相應的措施。
1 平行縫焊工藝
平行縫焊是一種電阻焊,是熔化焊的一種,采用雙點平行焊方式,通常用 2 個錐形的滾輪電極與金屬蓋板接觸后形成閉合回路。焊接過程中焊接電流的流動方式如圖 1 所示。焊接電流形成的脈沖電流在接觸電阻 R 1 處 (即電極與蓋板接觸處)產生大量的熱,由于熱量集中,使接觸處鍍層熔化,而產品母材不熔化,凝固后形成一連串外部及內部均為互相交疊的焊點,進而形成氣密性封裝 [1-2] 。焊接后實物產品如圖 2 所示,在管殼邊緣形成一道致密的相互重疊的連續焊點,從而保證管殼整體具備很高的氣密性。
2 常見縫焊質量問題及解決方法
2.1 打火導致產品報廢
由于電極輪焊接打火而造成的產品報廢,如圖3 所示,可明顯觀察到在長邊方向有一處較大的焊痕異常。陣列縫焊過程中,若電極輪在隨機焊接某只產品時發生嚴重打火情況(原因可能是蓋板表面臟污或電極受力不均勻導致兩個電極輪壓到產品上的壓力差過大),電極輪的焊接圓錐面將發生嚴重損害,如發生坑狀損壞。如不及時更換新的電極,將對后續所有產品焊接質量造成不可逆的影響,造成產品連續報廢,最終嚴重影響成品率。
基于上述產生不良品情況,本文提出對陣列焊接過程中對每只產品焊接過程中施加的電特征
參數及電極受反向壓力波動進行采集并做數據分析,進而總結出正常焊接和異常焊接對應的數據范圍,最終當出現焊接質量異常時,通過異常數據實時作出反饋。為驗證解決方案的可行性,進行了工藝現場驗證。
工藝現場使用絕緣膠對試驗用空管殼某一邊表面施加不同面積大小的人為污損,并進行焊接,通過數據采集得到如下結論:當人為涂抹絕緣膠的面積較小時,會發生較小程度的打火情況,反饋的電流及電壓信號的尖端波動值較小。反之,當人為涂抹絕緣膠的面積較大時,會發生較大程度的打火情況,反饋的電流及電壓信號的尖端波動值隨之增大。
對應圖 3 中產品發生較大程度打火時,對反饋電流、電壓、電阻、功率等數據進行采集記錄,如圖 4 所示。由圖 4 可清晰地看出,電流及功率參數在焊接過程中出現了突變數據。
通過對客戶現場某種產品上千組焊接參數的采集分析,最終選用電阻標準差用于判斷打火報
警狀態。生產現場根據不同產品焊接正常與異常狀態下電阻標準差大小,確定該值的最佳閾值。當實時值高于此閾值時,上位界面出現報警,提示操作人員進行相關手動操作(更換電極輪耗材)。報警解除后,繼續批量焊接產品。
2.2 焊痕均勻性不穩定
平行縫焊焊接產品某一對邊時,正常焊接成品的焊痕是均勻的魚鱗紋排布(見圖 2)。但在焊接某些大尺寸產品時,會出現某一邊的焊痕不清晰,甚至出現焊痕斷裂排布的情況 [3] 。如圖 5 所示,管殼左右兩側的焊痕寬度不一,另外焊痕的致密程度也發生不一致的情況。
通過壓力試驗分析,平行縫焊過程中如果施加到管殼長邊(或短邊)兩端的壓力與設定值差距較大,最終縫焊會造成一次縫焊而兩端焊痕明顯不一致的情況發生,因此縫焊過程中對焊接壓力的監控尤為重要。尤其是當施加到管殼兩側的壓力差大于 50g 后,焊痕一致性的問題更加突出。
通過對客戶現場某產品的兩側焊接壓力進行全程實時監控,設定二者差值變化閾值(如 50 g),當實時值超出此閾值時,上位界面出現報警,提示操作人員進行相關手動操作。報警解除后,繼續批量焊接產品,如圖 6 所示為焊接壓力監控界面。
此外,對于某些大尺寸產品,尤其需要采取大能量焊接的產品,由于焊接過程中自身存在較大幅度的持續震動,勢必引起與焊接電極輪相接觸的彈簧產生大幅度的共振波動,從而造成長邊(或短邊)兩端的焊接壓力差值差異變大。因此,如果在現場工藝許可的情況下,可將彈簧施加焊接壓力的方式更換為定額砝碼方式,此方法的優勢在于電極輪在滾動焊接過程中,始終以恒定的壓力作用于產品兩側。另外值得注意的是,砝碼施加壓力的方式在部分進口設備中得到廣泛使用。
2.3 產品電性能測試失效原因分析
通過對大批量產品焊接后電性能的測試,發現產品內部芯片存在失效的情況。經過對蓋板拆除后進行清零分析,部分電性能不達標的根本原因在于產品在設備內傳輸過程中受到較大靜電影響,導致芯片被擊穿。因此產品在設備內部傳輸及焊接過程中,需要對設備自身的防靜電有所規范。尤其是與產品直接接觸的工裝表面電阻值應該滿足行業標準 104~109 Ω。
為了滿足行業標準,需要對以下項目做嚴格規范:針對鋁制工裝,可對其表面進行硬質氧化處理,鍍層厚度控制于 30~50 μm,圖 7 所示為工裝表面電阻值的測量情況。此工裝表面鍍層厚度為 30 μm,經測試表面電阻值為 3.28×10 8 Ω,滿足行業標準。此外,設備內(含門板、外殼)固定金屬部件接地電阻小于 4 Ω,移動金屬部件接地電阻小于 100 Ω。如圖8 所示,對設備內仰視視覺系統結構進行接地電阻測試,電阻值為 0.8 Ω,滿足行業要求。
最后需要經過對各運動在靜止及運動狀態下進行 EMI 測試,峰值均應小于 15 V,尤其需要注意設備處于運動狀態下的測試值。如圖 9 所示,對上料部分移動單元以 5 mm/s 進行運動,記錄運動過程中該部件的 EMI 值,整個運動過程中,峰值為 10 V,滿足行業要求。若該值即使在接地處理后仍然不滿足要求,需要對電機等動力線增加磁環屏蔽。
上述檢測方法及微電子行業標準要求同樣適用于管殼前道工藝,如高精度貼片、引線鍵合等生產過程中。整個封裝工藝過程中,需保證設備自身的防靜電規范,從而降低管殼產品被擊穿的風險,保證最終的成品率。
3 結束語
本文總結了全自動縫焊設備生產過程中影響產品質量的主要原因。并且針對性地提出了相應的解決方案,經驗證提高了管殼高氣密性封裝的成品率。
審核編輯 黃宇
-
焊接
+關注
關注
38文章
3135瀏覽量
59771 -
微電子
+關注
關注
18文章
382瀏覽量
41204
發布評論請先 登錄
相關推薦
PCBA加工常見質量問題揭秘:焊接不良與解決方案
熱拔插對產品的影響及解決方法
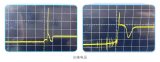
柔性測斜儀數據異常故障分析及解決方法
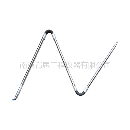
BGA封裝常見故障及解決方法
艾體寶干貨 如何使用 IOTA?解決網絡電話(VoIP)質量問題
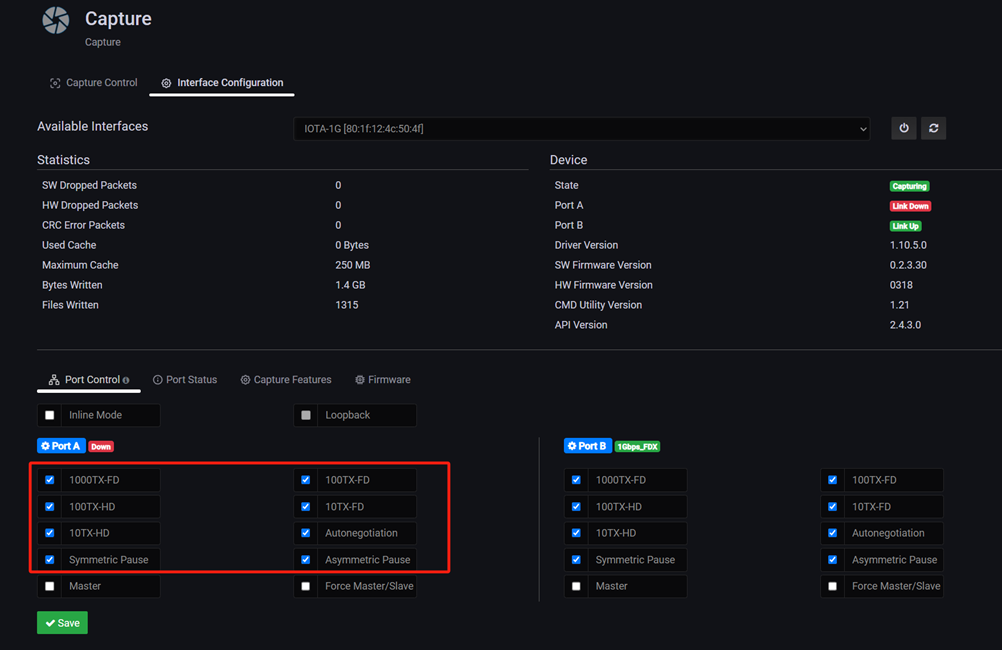
邏輯分析儀的常見故障及解決方法
電能質量問題包括哪些現象
單片機振蕩電路晶振不起振原因分析與解決方法
SMT加工中常見的錫膏印刷質量問題有哪些?
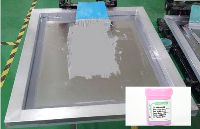
淺談電極對平行縫焊質量的影響
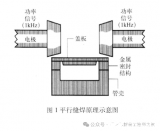
評論