共讀好書
王強翔 李文濤 苗國策 吳思宇
摘要:
本文重點研究了金屬陶瓷功率管膠黏劑封裝工藝中膠黏劑的固化溫度、時間、壓力等主要工藝參數對黏結效果的影響。通過溫度循環、濕熱實驗對封裝可靠性進行驗證,并以密封性能、剪切強度作為量化指標來表征,同時討論了膠黏劑封裝工藝中的常見缺陷及其改進方法。經研究分析得出:功率管膠黏劑封裝在適合的固化溫度、時間及壓力條件下,可以獲得優異的封裝質量。
電子封裝中,管殼為內部芯片電路提供了可靠的電氣連接、機械支撐及工作環境。為了保障芯片擁有良好的工作環境,防止水汽、污染物及有害氣體對芯片造成損傷,通常需要提供相對密封的環境,即密封封裝 [1] 。目前,可以通過多種途徑實現密封封裝,如基于釬焊工藝的錫封、基于電阻焊工藝的平行封焊、基于熔焊工藝的激光封焊以及樹脂灌封工藝和膠黏劑封裝工藝。各種密封工藝均有著其各自的適用場合,其中金屬陶瓷管殼封裝、金屬LCP封裝均采用了膠黏劑封蓋的封裝結構,如圖1所示。相較于其他封裝結構,這種封裝結構的特殊之處在于內部無填充,I/O引腳位于封裝界面。與其他封裝結構一樣,膠黏劑封蓋工藝也需要能夠經受老化、溫沖、震動加速度、耐濕等可靠性試驗的考核,因此其結構設計、膠黏劑選用及封蓋工藝過程對封裝的整體可靠性有著重要的影響。在功率管膠黏劑封裝工藝中,經常會出現一些典型問題,如密封不良、強度低和尺寸一致性較差等,本文將針對這些常見問題進行功率管膠黏劑封裝工藝研究。
1 膠黏劑封裝
電子元器件的封裝工藝有很多,常見有以下幾種封裝類型:(1)非填充型封裝。如中空式金屬盒體封裝、陶瓷封裝,一般在高導熱高可靠情況下應用。(2)填充型封裝。如塑封,常見的DIP、QFP、QFN、BGA等器件的封裝均采用填充型塑封工藝,塑封工藝的特點為質量可靠、成本低、效率高、可大規模生產。
目前功率管的一種封裝方式為非填充型的金屬陶瓷封裝。這種封裝方式采用金屬管殼及陶瓷蓋板,通過膠黏劑將兩種或兩種以上同質或異質的材料連接在一起 [2] 進行黏結封裝,內部無填充材料 [3-4] 。其主體結構為陶瓷蓋板和金屬管殼,一般在陶瓷蓋板的裝配界面預涂膠黏劑,與管殼裝配后經固化完成封裝,如圖1所示。陶瓷蓋板一般采用氧化鋁白陶瓷,金屬管殼由引線框架和導熱熱沉組成。下文即以該種結構器件為樣品針對膠黏劑封裝工藝參數及封裝可靠性進行實驗研究。工藝對主要材料膠黏劑的一般要求為:(1)密封性好,保證內部器件工作環境不受外界影響;(2)無有害揮發物,不會對內部器件造成損壞;(3)黏結強度高,保證封裝體整體機械強度;(4)可靠性高,耐溫度循環、濕熱環境等 [5-6] 。
2 實驗研究
2.1 實驗準備
實驗用封裝器件為表面鍍金的銅金屬基板(模擬管殼)、氧化鋁陶瓷蓋板,如圖2所示,其中銅金屬基板的結構尺寸為20 mm×10 mm×1 mm,氧化鋁陶瓷蓋板的結構尺寸為19.5 mm×9.6 mm×2.5 mm。實驗采用人工裝配,通過標準砝碼施加壓合力,使用熱臺加熱。本研究使用密封性能、剪切強度及封裝尺寸作為評價標準:(1)密封良率使用國家軍用標準GJB 360B—2009《電子及電氣元件試驗方法》中方法112條件D進行密封檢測,對于電子器件,密封條件可以為產品內部的芯片提供良好的工作環境,避免受到外界環境或污染物影響;(2)剪切強度使用推拉力測試儀(Dage4000)進行檢測,剪切強度是保證器件結構完整性的最基本指標;(3)封裝尺寸使用平面輪廓儀進行尺寸檢測。定義以上三方面的評價指標后,理想的封裝效果為密封效果好、強度高、尺寸一致性好、可靠性高,封裝完成的器件如圖3所示。
2.2 封裝實驗
實驗膠黏劑預涂于陶瓷蓋板表面。在膠封工藝中存在預熱過程、裝配過程、固化過程。按各過程的各個階段,膠封工藝的主要參數有預熱溫度Tx、預熱時間tx、固化壓合力F、壓合時間ty、固化溫度Tz、固化時間tz。一般膠黏劑的固化溫度Tz和固化時間tz為定值推薦,本實驗不做研究,均設定為膠體的推薦值。實驗針對預熱溫度Tx、預熱時間tx、固化壓合力F、壓合時間ty進行研究,參數如表1所示。采用溫度循環及濕熱加速實驗評價黏結可靠性,具體條件如表2所示。其中,溫度循環實驗每100次抽取10只樣品進行密封和剪切強度測試,濕熱加速實驗每24 h抽取10只樣品進行密封和剪切強度測試。
2.3 結果與分析
2.3.1 預熱工藝實驗
預熱工藝實驗研究的工藝參數主要為Tx、tx,實驗結果如表3所示。結果表明,要合理地設計預熱溫度和時間才能獲得較高的密封良率,溫度越高對應的時間越短,但過高的預熱溫度會帶來較短的工藝時間窗口。在工程應用中,可以選取適中的預熱溫度來提供充足的工藝時間窗口,如實驗中160 ℃的預熱條件下,時間窗口為2 min,而125 ℃的預熱條件下,時間窗口有4 min以上。不充分的預熱過程和過度的預熱過程均會導致密封成品率下降,前者是因為膠體固化程度過低,仍具有較高的流動性,無法形成較穩定的形態,在壓合過程中極易出現氣孔;后者是因為膠體固化程度過高,流動性過低,在壓合過程中對界面的潤濕能力下降,甚至已經固化無法潤濕黏結界面,導致密封不良。需要注意的是,不充分的預熱過程僅對密封良率產生影響,只要壓合力合適,封裝后的器件仍具有較高的剪切強度,而過度的預熱過程不僅影響密封良率還會影響剪切強度。
2.3.2 壓合工藝實驗
壓合工藝實驗研究的工藝參數主要為F、ty。膠黏劑中的環氧樹脂在固化時需要施加一定的壓力,主要原因是樹脂固化時,分子間發生化學反應,自由體積縮小,在黏結界面會產生固化收縮現象,這時需要從外界施加壓力彌補固化收縮,確保黏結界面緊密貼合。圖4為不同壓合力固化條件下制作的樣品,從左至右壓合力逐漸增大,使用平面輪廓儀掃描蓋板可以得到其表面輪廓尺寸,通過制作截面樣品可以得出膠層厚度尺寸。實驗結果如表4所示,結果表明:(1)隨著壓合力的增加膠層厚度變小,剪切強度提升,在壓合力達到100 g以上時,膠層厚度和剪切強度進入穩定區間;(2)在較低的壓合力下,除了黏結剪切強度低之外,還有黏結面不平整問題;(3)表5為不同壓合時間下的樣品剪切強度測試表,結果表明需保持一定的壓合時間才能保持黏結狀態,若壓合時間不足,膠體固化程度很低,仍處于可流動狀態,壓合力撤銷后,蓋板將在膠體中“浮起”,導致膠層厚度發生變化,最終影響剪切強度和表面平整度,嚴重的情況下甚至可能發生單側翹起,如圖5所示。
2.3.3 可靠性工藝實驗
可靠性工藝實驗結果如表6和表7所示。結果表明:(1)濕熱對黏結質量影響巨大,隨著濕熱實驗的進行,密封性能和剪切強度大幅下降,96 h濕熱實驗后,密封成品率下降50%,剪切強度下降40%;(2)溫度循環對黏結質量影響較小。封裝膠黏劑作為一種環氧樹脂,具有良好的黏結性、力學強度、耐化學介質、電絕緣、尺寸穩定性以及工藝性等優勢,但也存在環氧樹脂的缺點——耐濕熱能力差。水分子由于體積小,在濕熱環境下很容易進入環氧樹脂內部,降低已經固化形成的化學結構的穩定性,如導致局部化學鍵斷裂,破壞分子間作用力,降低交聯度。其次水分子進入后會對樹脂產生溶脹,使整個系統的自由體積增大,分子間距離增大,進一步降低結構的穩定性,最終導致密封失效,強度大幅降低 [7] 。
2.4 常見問題
在功率管膠黏劑封裝過程中,常見問題有:(1)氣孔,造成密封不良,表現形式為局部位置的微小孔洞,如圖6(左)所示。其主要的產生原因是在固化過程中內部氣體受熱膨脹并向外部排出進而形成貫穿型通道,從外部觀察即為微小孔洞。設定壓合前預熱溫度為T0,壓合后固化溫度為T1,根據理想氣體狀態方程PV=nRT,初始壓強為P0,壓合后固化溫度下壓強為P1,隨著溫度的升高(T1>T0),其內部氣壓升高,當ΔP(=P1-P0)達到一定程度時,即可突破膠層形成氣流通道,導致密封不良。因此,可以通過降低ΔP來降低氣孔的發生概率。設計合適的預熱溫度和時間可以減小壓合前、后過程中器件的內外壓差,進而降低氣孔密封不良的發生概率。(2)裂紋,造成密封不良,表現形式為局部區域細微裂紋,如圖6(右)所示。在溫度循環實驗后的失效樣品中可以發現,其由環氧膠體固化后硬脆,在溫度交替變化的條件下與金屬、陶瓷之間產生應力失配導致。基于此,對不同膠層厚度的樣品進行單獨的溫度循環實驗,發現裂紋更容易在膠層較厚的樣品中出現,如表8所示。(3)強度不足。在不考慮膠體自身材料因素的情況下,黏結強度低的主要原因為黏結界面污染、膠層過厚和固化不充分,可以通過增加壓合力和優化固化溫度曲線來保證黏結強度。
3 結論
膠黏劑封裝具有成本低、效率高和應用范圍廣的特點,其工藝過程中的常見缺陷為密封不良和黏結強度低。本文通過實驗研究得出金屬陶瓷功率管膠黏劑封裝在適合的固化溫度、時間及壓合力條件下,可以獲得優異的封裝質量,具備較高的黏結強度和密封成品率。其中,壓合力(膠層厚度)是影響剪切強度的主要因素;預熱溫度和預熱時間是影響密封成品率的主要因素;膠黏劑封裝耐濕熱能力一般,經過濕熱實驗后其剪切強度和密封效果大幅下降,在應用中需要充分考慮環境條件。
審核編輯 黃宇
-
封裝
+關注
關注
126文章
7902瀏覽量
142966
發布評論請先 登錄
相關推薦
功率模塊封裝工藝

功率模塊封裝工藝有哪些

芯片封裝工藝集成工程師的必修課程指南
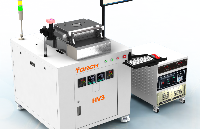
mos封裝工藝是什么,MOS管封裝類型
閑談半導體封裝工藝工程師
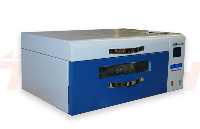
紅外探測器封裝秘籍:高可靠性鍵合工藝全解析
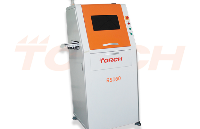
半導體封裝工藝的研究分析
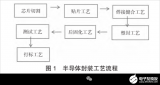
微波等離子處理對導電膠可靠性的影響
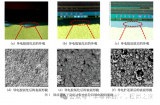
RFID各向異性導電膠類型和可靠性
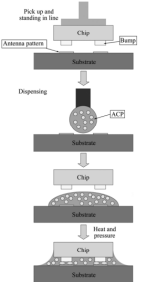
評論