通過對混合集成電路產品數字化研制方面開展了積極的技術研究與應用實踐,探索實施基于模型的混合集成電路全要素、全領域、全過程數字化研制模式轉型。
前言
混合集成電路是電子技術中的重要組成部分,其發展趨勢是智能化、高效化、可靠化。混合集成電路是由半導體集成工藝與薄(厚)膜工藝結合而制成的集成電路。混合集成電路是在基片上用成膜方法制作厚膜或薄膜元件及其互連線,并在同一基片上將分立的半導體芯片、單片集成電路或微型元件混合組裝,疊加封裝形成。與分立元件電路相比,混合集成電路以其高密度、高性能、高可靠性和輕重量、小體積等明顯的優勢廣泛應用于電子裝備系統。
混合集成電路行業具有典型的品種門類多、組裝密度大、質量等級高、定制化程度較高等特點,產品型號研制任務日益增長,功能性能要求不斷提高,并伴隨功能集成度、專業融合度、系統復雜度不斷提升,研發周期和質量要求日趨嚴苛,以及開展研制工作過程中數字化平臺間的數據、流程交互的需求越來越迫切。混合集成電路企業面臨嚴峻復雜的發展環境,亟需打造數據互聯、模型傳遞和流程貫通的新模式,實現研制任務各階段高效協作已成為業務急需和創新發展的必由之路,為全面推進企業數字化轉型奠定堅實基礎。
1 數字化研制目標和思路
混合集成電路產品數字化研制目標為:在構建各類產品研制數據庫和知識庫基礎上,對產品研制全壽命過程涉及的產品實體、管理活動和外部空間進行數字化表達,形成以產品譜系模型、單件產品模型、各類管理評估模型為核心的數字模型體系,在統一數字空間開展產品方案論證、設計研發、生產制造、試驗鑒定等產品研制管理活動,逐步由物理空間的產品研制活動向數字空間的轉移、拓展和映射,通過在數字空間并行開展、提前開展甚至是替代開展實體空間的產品研制及應用活動,并形成一整套數字化管理和研制規范,助力產品研制工作提質增效。
混合集成電路產品數字化研制總體思路是:堅持“模型”是核心、“模型貫穿”是主線、“模型構建與仿真驗證”是主要抓手的總體思路。面向產品研制全壽命周期的數字化建模應用,重點開展基于模型驅動的數字化研制平臺建設,增強產品數字化模型設計構建能力以及在虛擬空間的模型驗證能力,對應于產品需求模型、數字樣機模型的構建與驗證,尤其是對數字樣機模型進行細化分解,并加強模型貫穿與仿真驗證條件建設,支持在復雜應用環境下實現混合集成電路產品應用場景遍歷和功能性能的充分驗證評估,切實提升對物理空間的反哺能力,減少基于實物驗證的迭代反復,有效提升方案論證、設計研發、生產制造、試驗鑒定等階段的效能。
圖1 混合集成電路數字化研制模式轉型示意圖
2 數字化研制模式實施策略
圍繞實施數字化轉型戰略、支撐企業建設的目標,公司推進構建了混合集成電路產品數字化研制業務和管理模式的變革重構,從組織機構、流程架構、共性支撐平臺、標準規范、工作機制等方面堅定不移推進數字化研制工作。
2.1 成立數字化工作推進組織機構
數字化研制貫穿產品研制全過程,涉及產品型號、技術、管理等多個方面,是一項復雜的系統工程。為切實推進數字化研制工作落地見效,加快培育數字化專家,探索建立適應數字化轉型需要的新型數字化組織,逐步打造一批政治素質好、業務水平高、創新能力強的高水平技術團隊。明確各部門主要領導牽頭主抓數字化研制工作推進責任體系,及時協調解決問題和困難,確保各項工作沿著正確方向前進,為數字化研制模式轉型提供了有力的組織保障。
2.2 構建科學完整的流程架構
建立完備的研制流程架構,橫向貫通產品研制全生命周期各階段,縱向打通研發設計、工藝制造、試驗鑒定、售后服務等各業務域,解決分散割裂、數據斷點等問題,實現端到端的貫通,支撐業務流程的持續建設和優化。踐行以客戶為中心的理念,運用流程管理的方法論開展業務流程設計,集成管控基礎要素,實現業務流程規范化、標準化,促使產品獲得市場與客戶的認可。加強業務流程和信息化平臺的深入融合,構建統一的業務架構和端到端的業務流程,保障各系統間的優化整合和集約高效。結合先進的信息化技術,驅動業務模式變革與創新,實現業務數字化,助力企業高質量、高效率、高效益發展。
2.3 統籌謀劃共性支撐平臺建設
共性支撐平臺是面向企業科研生產和企業管理的統一支撐平臺,能夠為各類科研生產和企業管理應用系統構建提供統一的共性應用支撐服務。為實現資源的高效集約使用,對資源進行最大化共享復用,積累推廣優秀的成果經驗,堅持國產替代、安全可控相結合的基礎上,從公司頂層統籌謀劃專業軟件工具平臺建設、數據/模型資產等資源,探索設計共性支撐平臺。聚焦產品論證、設計研發、生產制造、試驗鑒定等關鍵業務環節提供統一支撐,一體解決跨專業、跨部門傳遞模型帶來的障礙,沉淀共性能力和資源,打造共用能力底座,構建資源共享體系,促進各領域、各部門協同發展,確保數字化研制工作高效集約推進。
2.4 建設數字化工作標準規范體系
數字化研制標準規范是實施混合集成電路產品數字化研制的基本要求,應充分參考或遵循國際標準、國家標準、行業標準,建立科學、合理、規范的數字化研制標準規范體系,涵蓋基礎、管理、技術等多個方面。鑒于標準規范編制周期長、審查程序嚴謹,為滿足產品研制過程中面臨的迫切需求,按照“示范先行、規范跟進”的推進思路,以試點示范項目為引領,先行開展專用規范、專屬標準等制度建設,結合各類產品研制實際工作情況不斷完善相應規范,最終總固化形成通用標準,以有效積累沉淀數字化研制成果,并指導設計、工藝、制造等相關人員規范開展研制工作。
2.5 建立健全數字化研制推進工作機制
數字化研制模式是一種全面提升業務效率、支撐業務模式創新的新模式。為全力保障產品數字化研制工作的順利實施,構建“行政指揮線+技術指揮線”的兩線協同管理機制,壓實數字化推進任務責任,加強企業內外部智庫團隊、領域專家通力合作,形成工作合力,確保任務全面落實。建立健全一盤棋統籌推進工作機制,通過專題工作會、專項研討會、評估考核等方式,形成“過程跟蹤、督促指導、績效考評”的閉環管理機制,對存在的問題和不足進行動態識別和精細管控,促進數字化轉型工作有效落地、整體推進、全面發展。
3 數字化研制模式轉型研究
面向數字化研制模式轉型目標,聚焦混合集成電路產品論證、設計研發、生產制造、試驗鑒定等研制模式轉型方向,開展產品數字化研制模式轉型研究與實踐,遵從共性的新模式開展各階段數字化活動,持續提升產品研制數字化能力水平。
3.1 產品論證數字化
通過在數字空間開展虛擬仿真試驗,精準分析產品方案合理性、經濟可行性、技術成熟度的分析與方案尋優,準確生成產品需求,提升產品立項決策能力,實現低成本,高置信的產品論證方案,著力解決傳統產品方案論證過程中存在的研究不夠充分、產品效能評估不夠準確、產品設計指標不夠科學等問題,為后續研制工作提供準確輸入。
探索推進產品論證由定性向定量轉變。現有的產品論證方式基于同類實體產品設計經驗開展,性能指標與技術路線不能充分優選,反復論證、效率低下。數字化產品論證方式具備成本低、周期短、性能指標與功能模塊充分優化,技術路線論證充分等優勢。在立項方案階段,面向產品研制合同、技術協議、用戶研制需求等外部輸入,開展電路需求、結構需求、可靠性需求等需求模型建模工作,梳理得到定量的電性能、引出端、外形尺寸、環境要求、安裝方式、檢驗試驗需求等參數要求,形成準確的產品研制任務需求目錄。利用建模設計工具繼承已有的架構設計結果,綜合產品需求目錄,開展模型化概念方案設計,通過功能劃分、指標審校,實現場景化、體系化的定量優化設計。通過對接用戶側綜合仿真平臺,開展模型推演仿真,實現對概念方案設計結果驗證,確保產品滿足配套裝備的應用需求,并實現體系貢獻度的最大化。
3.2 設計研發數字化
圍繞模型構建、數據驅動的研發模式轉型,依托數字化設計平臺工具,構建數字樣機模型,通過多領域間模型要素傳遞,實現整體設計快速分解,各功能模塊設計的準確集成,大幅提升迭代效率。通過多學科間模型要素傳遞,支撐多專業聯合優化設計,進一步提升產品效費比,從而解決當前產品設計過程中存在的設計迭代效率不高,設計優化不全面等問題,實現產品設計從局部最優向整體最優轉變。
探索推進設計研發由文檔傳遞向模型協同轉變。現有的產品設計往往基于文檔開展,各種文檔編制、流轉、審閱耗時長易出錯,導致溝通效率低下,設計差錯率居高不下;基于文檔的設計往往囿于設計師重點關注的若干專業開展,尚未完整覆蓋產品研發涉及的各個學科領域及多學科交叉領域,難以實現指標的綜合優化;基于文檔的設計難以做到設計復用、知識復用,設計效率提升難度較大。數字化產品設計研發具有交互效率高、技術指標全局優化、知識復用率高、設計規則約束作用大等優勢。數字化研發模式下,重點開展產品電路設計、版圖設計、可靠性設計、結構設計以及投產準備。采用電學參數級仿真模型細化為六大標準單元IP模型及其它元器件模型,由濾波電路、功率轉換、高頻變壓器、輸出整流、控制驅動、輸出反饋等電路模塊承載產品具體參數信息及電特性。通過電路產品及六大標準單元協同技術論證、方案設計、詳細設計,形成產品的多專業設計方案,同步開展基于模型的多專業設計驗證,迭代優化設計指標;對模型數據實施管理、歸檔,形成企業級模型庫,實現模型復用,全面提升后續同類產品的設計效率。
3.3 生產制造數字化
生產制造階段主要開展工藝設計、物料齊套、自制件生產與整件產品微組裝等,形成實體產品,為內部檢驗試驗、外部試驗鑒定做準備。通過將數字空間的產品模型與生產要素相關聯,大幅提升產品制造效率。依托數字化制造平臺,開展全三維全數字工藝設計,打通工藝、結構數據傳遞堵點,實現工藝設計的迭代提升,支持變批量混合生產,有效縮短微組裝周期,解決當前產品制造過程中存在的工藝優化不深入、產線建設周期長等問題,促進產品制造的周期縮短與質量提升。
探索推進生產制造由人工主導向智能主導轉變。現有的生產制造依賴于人工操作和手工控制,導致生產過程效率低下。數字化生產制造具有生產效率高、成本低、靈活性高、一致性優等諸多特點。數字化生產制造模式下,建立產品工藝器件的高精度模型,實現電路產品工藝設計環節的數字化仿真評估。通過車間管理系統、高級排程、物流配送、設備監控等數字化平臺工具,實現高效排程調度、精準配送物料、制造自動執行、工藝流程優化;通過自動操作、控制,有效提升生產效率,降低返工返修率,節約生產成本;采用模塊化、柔性化生產系統,可更好適應不同的產品類型與規格,提升生產的靈活性;通過信息系統集成,實現不同工序環節的數據共享,提高生產管理效率;采用自動化手段降低人員參與的風險,保證產品質量一致性。
3.4 試驗鑒定數字化
試驗鑒定階段重點開展試驗計劃、試驗任務、試驗資源、綜合信息和試驗數據的集中管理、交互共享、合理使用,確保試驗數據的完整性和安全性,為完成定型、用戶驗收和產品交付做好準備。通過將在數字空間構建產品模型檢驗試驗環境,通過虛擬環境、產品要素的快速迭代,洞悉產品的真實能力,推動產品的性能優化與質量提升,滿足產品數字化試驗鑒定需求。試驗人員宜采取虛實結合的檢驗試驗方法,綜合利用仿真驗證平臺、仿真算法、實測數據,構建高逼真度的虛擬試驗環境,通過數實迭代保證數字域模型能夠真實反映產品實體能力,以數實動態演化促進數字域等效實體域,窮舉遍歷產品使用的各種邊界條件,著重解決產品試驗驗證主要采用實物試驗手段,存在試驗效率低、成本高、安全隱患大等問題,打破現實大規模體系化應用場景模擬試驗的局限。
探索推進試驗鑒定由產品實物驗證向虛實融合驗證轉變。現有的試驗鑒定往往采用基于實物的測試驗證,周期長、成本高,難以全面摸清產品指標性能底數。基于實物的試驗方式往往資源受限,造成次數有限,較難遍歷產品使用邊界條件。試驗過程中存在高低溫、強電壓、抗輻照、機械沖擊等環境因素,給參試人員帶來一定的安全風險。數字化試驗鑒定具有成本低、周期短、結果更可信以及安全性更好等諸多優勢。數字化試驗鑒定模式下,采用虛實結合的半實物驗證手段,面向實際應用領域構建各種典型使用場景,在數字樣機基礎上形成數字實體模型,基于產品應用場景開展功能指標評估和性能邊界考核,充分驗證產品在復雜環境下的運行狀態。通過在數字空間構建虛擬的試驗場景,大幅減少試驗所需的人力和物力;通過復雜試驗環境配置、邊界條件遍歷與大樣本模擬試驗,摸清產品各項指標底數,提升試驗結果的可信度;通過建立專業的試驗數據采集工具進行數據自動采集、處理與分析,提高試驗鑒定效率,降低試驗鑒定成本。
4 數字化研制模式轉型展望
通過對混合集成電路產品數字化研制方面開展了積極的技術研究與應用實踐,探索實施基于模型的混合集成電路全要素、全領域、全過程數字化研制模式轉型。經過前期的研究與實踐已取得初步實效,但整體數字化轉型速度和成效尚無法滿足全面推廣一體化全數字化設計與制造模式的發展要求。數字化研制支撐條件機制不完備,阻礙了企業數字化能力快速提升。后續,將重點關注數字化技術的發展方向,積極開展理論研究與工程實踐,推進多學科集成仿真技術研究,進一步擴展產品協同設計范圍。深化技術發展聯盟、產業生態等領域協作聯合,積極推進領域間數字化成果交流學習,促進資源要素互補,推動聯合資源開發,輔助提升業務能力,實現數字化技術與產品研制工作的深度融合,為數字化研制模式轉型升級和企業跨越式發展提供堅實保障。
審核編輯:黃飛
-
集成電路
+關注
關注
5388文章
11547瀏覽量
361836 -
管理系統
+關注
關注
1文章
2499瀏覽量
35927 -
半導體芯片
+關注
關注
60文章
918瀏覽量
70632
原文標題:面向混合集成電路的數字化研制模式研究與實踐
文章出處:【微信號:可靠性雜壇,微信公眾號:可靠性雜壇】歡迎添加關注!文章轉載請注明出處。
發布評論請先 登錄
相關推薦
混合集成電路的EMC設計
薄厚膜混合集成電路前景怎么樣
混合集成電路EMC設計產生的原因闡述
混合集成電路電磁干擾產生的原因是什么
混合集成電路,混合集成電路是什么意思
混合集成電路,什么是混合集成電路
混合集成電路綜述
關于混合集成電路電磁兼容的設計
芯片設計中數模混合集成電路的設計流程是怎么樣的
混合集成電路的EMC設計詳細說明
如何設計混合集成電路的電磁兼容
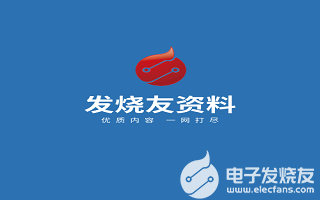
評論