隨著減少汽車二氧化碳排放的需求不斷增加,對輕質線束的需求一直很高。通過用鋁線代替傳統的銅電線,可以有效地減輕重量。然而,鋁線具有幾個缺點,例如導電性低、抗拉強度低、可加工性差,以及表面上的強絕緣氧化膜和電偶腐蝕。為了解決這些問題,我們開發了一種具有改進的導電性、抗拉強度和可加工性的鋁合金導體。我們還開發了一種獨特的鋸齒狀端子結構。
01
介紹
在汽車工業中,隨著二氧化碳排放法規的日益嚴格,對輕量化的需求也在增加,此外,部分原因是銅價飆升價格,我們開始研究鋁制線束,將線束中的電導體從銅中更換成鋁以減輕重量和價格。鋁線主要用于架空電力線和汽車電池電纜,其中導體的截面導體面積大,可承受大電流。同時,線束的導體截面積通常不超過2.5 mm2。我們開發了用于汽車應用的此類鋁制線束。圖1顯示了導線、端子和鋁線束防腐。本文報告了在其開發過程中使用的技術。
圖1 鋁線、端子及防腐技術的發展
02
汽車鋁線
用于制造汽車鋁線的鋁合金需要表現出高抗拉強度和高導電性。該開發項目旨在實現抗拉強度為110MPa、電導率為58% IACS的材料性能目標。這些值是為了使0.75mm2的鋁線代替傳統上廣泛用于低壓電源電纜的0.5mm2銅線。因此,住友電氣的電子與材料研發實驗室和住友電工集團旗下的AutoNetworks Technologies,Ltd.共同致力于開發用于汽車電線的鋁合金。
2-1
合金設計
一般工業用途的純鋁(1060: 純度99.6%)具有62% IACS的高電導性。然而退火后,它表現出70MPa的低抗拉強度。對于汽車線材應用,有必要通過合金化來提高其抗拉強度。固溶體強化可有效提高金屬抗拉強度。但是,這種方法會導致電導率明顯下降。同時,更大的失配應變(MS)也有望提高金屬的抗拉強度。對于汽車線材應用,有必要抑制電導率的降低并提高抗拉強度。因此,如果一種元素在低固溶體量下提供大的MS,則它被認為是有效的合金元素。用第一次原理測定了各種鋁合金元素室溫固溶體的MS值和最大含量。
通過第一性原理計算。對計算結果進行分析后,選擇Fe作為合金元素(表1)。進一步研究二者之間的關系揭示了鐵的合金化和鋁鐵合金的材料性能性能目標是可以實現的,如果合金化鐵的質量百分比為1.5%或更高(圖2)。
表1 MS和與各種元素合金化的鋁的最大固溶體量
圖2 鐵添加量對材料性能的影響
通過傳統的坯料鑄造和擠壓制造的線材結晶出粗鋁鐵化合物。它們的延展性和可加工性較差。相反,住友電工集團旗下住友電工富山株式會社生產的線材具有優異的加工性。這些線材是通過Properzi方法生產的,在鑄造和軋制過程中使用高冷卻率,無需再加熱。該過程將化合物控制在精細狀態下,并保持合金的高延展性。盡管如此,汽車電線的股徑對于鋁線來說非常小,在0.15到0.5毫米之間。當Fe的質量百分比超過1.2%時,線材的可加工性降低,由于機加工限制,線材在拉伸和絞合過程中斷裂,如照片1所示。為了解決這個問題,我們尋找了第二種合金元素,它可以部分取代Fe。
照片1斷鋁絞線
在不影響可加工性的情況下提供更高的抗拉強度。
由于Al-Fe合金以相對較大的余量滿足了電導率目標,因此允許在一定程度上降低合金的電導率。為了用作第二種合金元素,我們選擇了一種MS含量低(這對加工性產生不利影響)的元素,盡管導電性有所下降,但固溶液的含量卻很高。
表1中所示元素的比較表明,Mg是最合適的。下一步是找到元素添加的最佳量。
結果得到以下成分(質量%):Al-1.05%Fe–0.15%Mg。該成分提高了可加工性和性能,并實現了120MPa的拉伸強度和60%的IACS電導率,遠遠超過了目標(圖3)。
圖3 新開發合金的成分和性能2.2鋁線系列
2-2
鋁線系列
表2顯示了當前可制造的鋁線的排列以及用鋁線代替傳統銅線的效果。傳統的銅線可以合理地用比銅大一個尺寸的鋁線代替。
表2 鋁線系列
03
鋁線端子
如圖4所示,汽車線束中的大多數連接部分都使用將帶有壓接導線的端子插入連接器的結構。為了廣泛的應用鋁制線束,住友電工開發了一種特殊的端子,可以通過壓接與鋁線連接。
圖4 連接器和壓接電線
3-1
開發挑戰
壓接是一種連接方法,將絕緣層剝離的電線壓接在端子上被稱為“線筒”的U形截面中,以確保電線的電氣連接和保持力,如圖5所示。
圖5 壓接連接
圖6顯示了使用傳統銅端子的銅線和鋁線的壓接特性。壓接條件繪制在X軸上,向左更強地卷曲(高壓縮)。更高的壓縮通常導致更穩定的電連接。然而,線材保持力在過高的壓縮范圍內減小。因此,線束制造中的壓接條件設定在兩種性能都滿足規范的范圍內。鋁與銅的不同之處在于它覆蓋著一層堅固的絕緣氧化膜。它的接觸電阻保持不穩定,除非它比銅壓接得更牢固。強壓接會降低導線的保持力。因此,要確保鋁線壓接條件比銅線壓接條件更緊密。為了通過壓接可靠地連接鋁線,需要在低壓縮范圍內穩定鋁線的接觸電阻,或者在高壓縮范圍內提高鋁線保持力。
圖6 壓接強度、接觸電阻和導線保持力
3-2
壓接性能改進
(1)提高電氣連接性能
為了提高壓接鋁線的電氣連接性能,我們從因果圖中選擇了一些因素,并重點關注端子上的鋸齒,鋸齒是指在端子的線筒中形成的凹凸。銅線的端子通常具有三個凹槽。圖7顯示了沒有鋸齒的端子的壓接特性。使用這種的端子,無論壓接條件如何,接觸電阻都保持不穩定。這證明了鋸齒的有效性。
圖7 鋸齒對電連接性能的影響
從壓接端子上取下鋁線進行表面觀察,以檢查端子接線情況。如圖8所示,在與鋸齒邊緣相對應的位置觀察到端子鍍層材料錫的粘附。
圖8 壓接導線表面觀察
此外,我們使用CAE分析了壓接過程中施加到電線上的載荷。如圖9所示,靠近鋸齒的區域的載荷特別高。根據這一觀察結果,鋸齒被認為有利于在靠近鋸齒的位置發生氧化膜破裂。
圖9 利用CAE進行壓接模擬
根據上述觀察結果,推測鋁線壓接的機理為:在壓接過程中,由于端子上的靜電使鋁線發生較大變形,導致鋁線上的絕緣氧化膜斷裂;并且由于在鋸齒邊緣額外施加載荷,電線和端子的新暴露表面被連接(錫附著在鋁線上),從而確保電氣連接。因此,我們在端子開發指南中規定要增加鋸齒邊(端子與電線的接合部分)的體積。
(2)提高導線保持力
為了通過壓接實現鋁線連接,在高壓縮范圍內提高電線保持力也是有效的,如圖6所示的壓接特性之一。
因果圖分析結果表明,與電氣連接一樣,可以通過重新設計鋸齒來提高導線的保持力。在更寬范圍內的精細凹凸被證明是有效的。
3-3
鋁線壓接端子
圖10顯示了新開發的鋁線壓接端子。該端子只需通過修改鋸齒形即可確保連接性能。設計要求是:(1)足夠多的鋸齒邊緣以提高電連接性能
(2)在更寬的范圍內放置精細的粗糙度以提高電線保持力。
考慮到制造和性能裕度,對形狀進行了優化。
圖10 鋁線壓接端子
圖11顯示了新開發的端子的壓接特性。電連接和電線保持力都得到了改善,并且確保了與傳統銅線相當的壓接條件。在基于惡劣車輛環境的各種耐久性評估中,也證實了與銅線等效的連接可靠性。
圖11 鋁線端子的壓接性能
3-4
總結
為研制鋁制線束,研制了一種專用端子。這種端子可以通過壓接連接鋁線,這是一種用于制造線束的通用技術。該端子可用于與傳統銅線線束相同的線束制造工藝。
此外,該端子可與銅線配合使用,有望提高銅線連接的可靠性。由于車輛功能的復雜化和電子元件的使用增加,連接器和壓接線被設想放置在惡劣的環境中。新開發的技術是一種有效的可靠性改進技術,適用于上述環境。
04
防腐技術
4-1
鋁的雙金屬腐蝕
當電解溶液(如鹽水),接觸銅(高天然電極所在的部分電位)和鋁(低自然電極電位)時,形成一個局部電池,銅作為陰極,鋁作為陽極,引起雙金屬腐蝕(電偶腐蝕),導致大量的鋁洗脫(圖12)。
圖12 銅和鋁的雙金屬腐蝕
4-2
鋁的防腐技術
我們檢查了電解液接觸鋁線端子壓接部分時的腐蝕進展。圖13顯示了將 5% 鹽水施加到鋁導體上并將該導體在炎熱潮濕條件下放置一段時間時的狀態。鋁被完全洗脫,這表明接觸即使是少量的電解液也會造成深度腐蝕。因此,我們假設通過防止電解液進入與壓接部分的接觸,即通過防止進入卷曲部分的水分,來實現防腐。
圖13 鋁線壓接部分腐蝕
濕氣可以通過所示的路徑到達褶邊見圖14。路徑1是暴露在鋼絲桶前端的鋁導體。路徑2是暴露在鋼絲桶之間的鋁導體。這些路徑包括沒有被端子覆蓋的鋁導體部分。此外,濕氣可以通過間隙進入在導線和端子之間,即路徑3。
圖14 濕氣到達鋁線壓接處的路徑
因此,我們認為有必要嚴格保護端子的后端以及鋁導體的暴露部分。考慮到上述因素,我們決定用樹脂完全覆蓋壓接部分和端子后端,作為一種防腐技術。從與端子的附著力、填充性能和耐熱性等方面對樹脂材料進行了優化。通過耐久性和嚴格的測試對樹脂進行了評估,以實現實際的車載安裝。最后,設計了圖15所示的模具結構,以建立鋁的防腐技術。
圖15 鋁線壓接段模具結構
05
結論
開發了鋁線、端子及防腐蝕技術,以便在車輛中使用鋁線束。預計銅價將上漲或保持高位。如果線束中使用的所有銅線都更換為鋁線,則線束將約輕25%。由于這些因素,針對對鋁制線束的需求將增加。
-
導電
+關注
關注
0文章
226瀏覽量
21535 -
鋁線
+關注
關注
0文章
13瀏覽量
10861 -
汽車
+關注
關注
13文章
3515瀏覽量
37318
發布評論請先 登錄
相關推薦
線束市場發展前景看好
誠聘車載線束工程師!!!歡迎您的加入!
住友(Sumitomo)連接器供應商型號6187-3801大量庫存
為什么銅線與鋁線不能連接在一起?
【Altium小課專題 第183篇】什么是線束,怎么使用原理圖的線束?
廣東駿亞擬購住友電工FPC業務
關于尼龍扎帶與鐵芯束線帶和束線的運用差別
新能源線束市場值得跟風?
線束固定扎帶的布置原則
未來線束的發展趨勢之一——小線徑鋁導線的應用
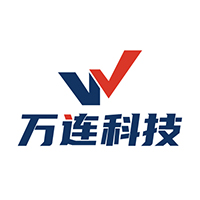
一探古河電工的鋁線束的秘密
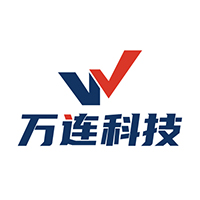
評論