第七代工業IGBT模塊已成功開發用于650V和1200V級,以滿足高效率、高功率密度和高可靠性等重要電力電子系統要求。與低損耗第七代芯片組結合的SLC技術在熱循環能力、無“泵出故障”封裝和低熱阻等方面的卓越表現,是第七代NX型IGBT模塊成功的關鍵原因。為了將該技術擴展到1700V級IGBT模塊,已經改善了SLC技術IMB的絕緣能力和熱導率。
第七代650V和1200V級工業IGBT模塊已在市場上推出。在這一新一代IGBT模塊中,采用了最新的芯片技術,以滿足工業電力電子應用的需求。所有應用都利用了第七代NX型IGBT模塊的優越特性,包括緊湊性、高功率密度、高可靠性、高效率和合理的成本。為了將適用范圍擴展到1700V級模塊,作為SLC技術關鍵元素的IMB(絕緣金屬基板)得到了改善。
SLC技術具備高熱導率和絕緣特性
Al2O3基板通常用作功率模塊中的絕緣層。然而,三菱電機在第五代和第六代IGBT模塊中采用了氮化鋁(AlN)基板。由于使用AlN而非Al2O3所實現的優越熱導率,芯片與基板之間的總熱阻Rth(j-c)降低了約35%(見圖1)。
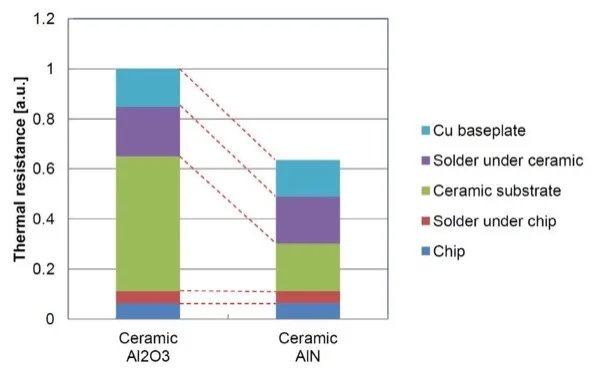
然而,進一步提高陶瓷的熱導率是困難的。此外,由于這些材料的熱膨脹系數(CTE)不匹配,在熱循環過程中,陶瓷層與金屬層之間的互連會受到應力。然而,使用更薄的陶瓷基板以提高熱阻并不總是最佳選擇。
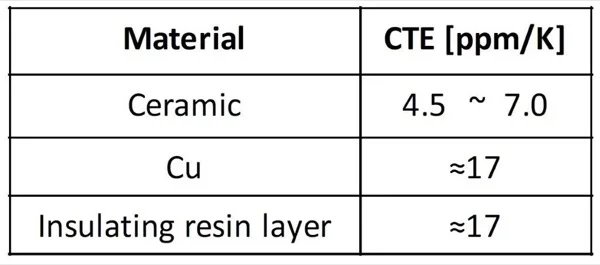
基板越薄,因機械應力而受到損壞的敏感性就越高。為了解決這個問題,開發了具有IMB結構的SLC技術。這一新結構的橫截面如圖2所示。
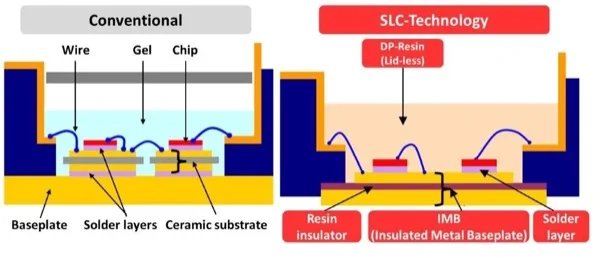
通過選擇IMB絕緣樹脂層的CTE值接近上下金屬層的CTE值,可以減少由于CTE值不匹配引起的機械應力。因此,與使用陶瓷隔離基板的傳統結構相比,IMB中的絕緣層厚度可以減少,而金屬層的厚度可以相應增加。通過這種方法,可以選擇一個較厚的金屬層作為底部,替代金屬基板,消除傳統模塊中基板與陶瓷基板之間的大焊料層區域。因此,熱阻和熱循環能力得以改善。
與陶瓷基板上可用于芯片安裝的表面積相比,新開發的IMB的表面積可以增大,因為IMB沒有陶瓷基板所固有的尺寸限制。消除這一尺寸限制后,IMB的大小和形狀設計更加靈活。因此,通過消除多個隔離基板之間的互連線,可以在模塊中實現更高的芯片安裝密度。此外,上側金屬層的厚度可以增加,從而降低電氣引線的電阻。這使得可以設計更窄電流通路的頂部金屬化模式,從而進一步增加可用于芯片安裝的面積,提高模塊的功率密度。
通過增加上側金屬層的厚度,獲得的第二個積極結果與熱擴散效應相關,這促使“Rth(j-c)”的熱阻和“Zth(j-c)”的瞬態熱阻因熱容量的增強而進一步降低。
IMB特性優化以實現更高的絕緣電壓
第七代NX型IGBT模塊的完整系列如表2所示。650V和1200V級模塊的絕緣電壓規定為Viso=2.5kV AC 1min,而1700V級模塊的絕緣電壓為Viso=4kV AC 1min。
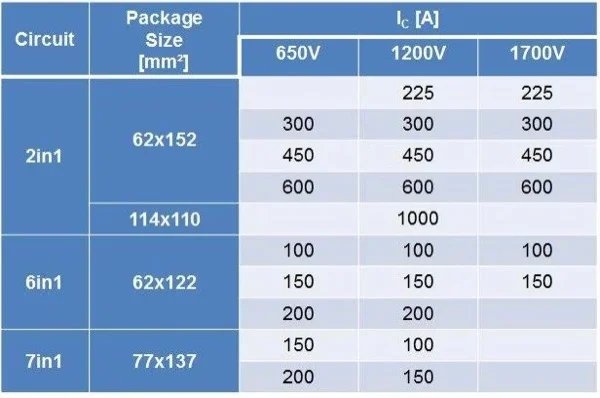
模塊封裝的示例如圖3所示。對于650V、1200V和1700V電壓等級的600A 2合1模塊,采用相同的封裝尺寸(62mm x 152mm)。
在相同的封裝尺寸(62mm x 152mm)下,IMB必須在Vces=1700V和Viso=4kV時改進,以實現同樣的600A額定模塊電流。必須提高絕緣樹脂層的比熱導率,以補償Viso=4kV所需的額外絕緣層厚度。
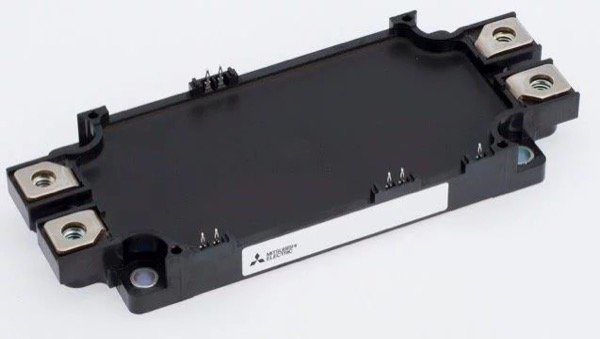
IMB的絕緣層由樹脂和陶瓷顆粒組成。為了提高熱導率,必須增加絕緣層內的導熱路徑面積,即陶瓷顆粒與樹脂數量的比率。如果增加陶瓷顆粒與樹脂數量的比率,樹脂的數量就會減少。樹脂數量的減少導致粘度降低,因此在IMB制造過程中需要在較高的壓力下進行(需要去除氣泡)。如果顆粒體積濃度超過臨界值,介電擊穿電壓能力和熱導率會因陶瓷顆粒之間的氣泡而降低。陶瓷顆粒的數量、樹脂數量和陶瓷顆粒大小的分布需要優化,以減少氣泡、保持高流動性并在模壓時保持所需的壓力,通過這種優化,可以增強熱導率和耐壓特性。
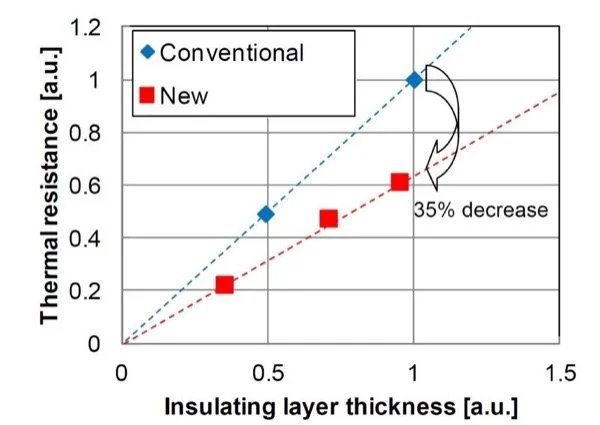
圖4顯示了IMB的熱阻與樹脂絕緣層厚度的測量結果。與傳統IMB相比,IMB的總熱阻約改善35%,因為樹脂絕緣層的熱導率提高了50%。新IMB的局部放電起始電壓(PDIV)對層厚度的依賴性幾乎與傳統IMB相同。因此,所提議的IMB在具有改進的熱導率的同時,已確認具有相當的PDIV和絕緣特性。
圖5展示了通過改進IMB實現的封裝尺寸縮減示例。對于之前的第六代和第七代600A/1700V 2合1模塊,封裝面積分別為114mm x 114mm和62mm x 152mm,相當于49%的減少。
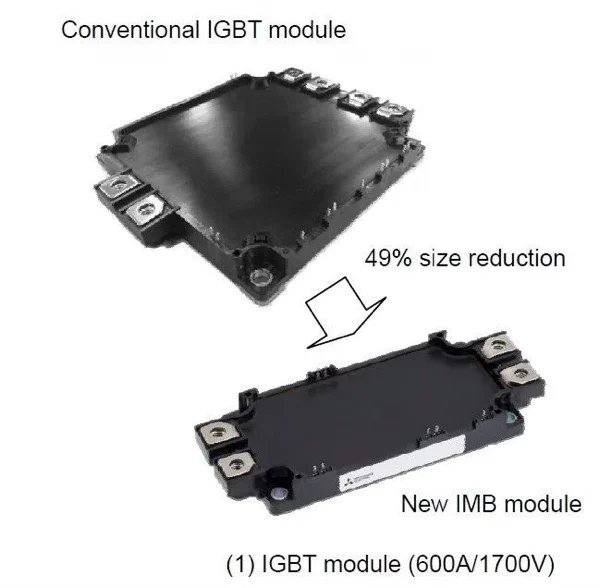
圖6總結了新IMB與傳統IMB的特性。經過驗證,新IMB在1700V模塊的熱阻約比傳統IMB在1200V模塊的熱阻改善5%。
另一方面,新IMB也可能降低650V和1200V級IGBT模塊的熱阻。將低損耗第七代芯片與所提議的改進SLC技術結合,將進一步提高模塊的電流密度。該選項目前正在研究中。
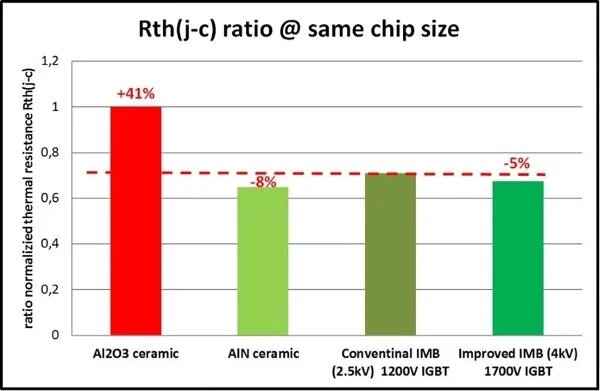
高熱循環能力
SLC技術利用匹配CTE值的層,如前所述。此外,環氧樹脂封裝可以減少芯片下焊料層的應變。這確保了熱循環和熱循環中的高可靠性。圖7顯示了在初始進行的熱循環測試(-40~+125攝氏度)下的掃描聲學層析成像(SAT)圖像,經過300次和600次循環后,傳統結構的陶瓷基板下焊料層出現退化。另一方面,采用DP封裝的新結構僅在芯片下有焊料層,經過600次循環后未觀察到退化。這一結果表明,消除了基板焊料層并利用了環氧樹脂層的效果。
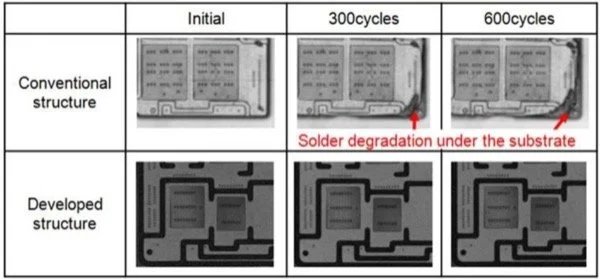
圖8顯示了熱循環測試的結果(ΔTc=80K(+45~+125°C))。新開發的結構經過40k次循環測試,至今沒有出現故障。另一方面,傳統結構的基板下焊料層出現了退化(類似于熱循環的結果)。由此可見,采用DP樹脂和IMB的新封裝相較于傳統結構顯著提高了熱壽命循環能力。這一方面得益于消除了絕緣層下的焊料層,從而減少了芯片下的焊料層應變。
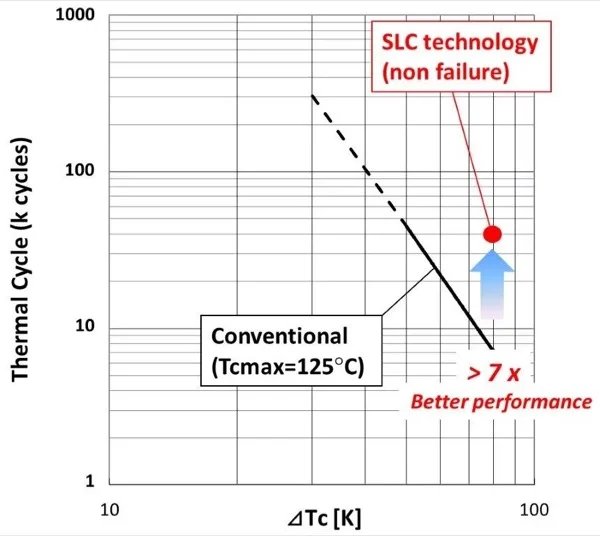
SLC技術提供無“泵出故障”的封裝
通過改進IMB,結與外殼之間的熱阻得到了成功降低。為了實現更高的功率密度和高可靠性,必須優化基板與散熱器之間的熱阻Rth(c-s)。
通常,在模塊的基板與散熱片之間應用熱界面材料,以增強熱接觸。必須注意,這些參數(如厚度、性能、材料性質)對熱散耗能力和可靠性有影響。另一方面,眾所周知,功率模塊的基板形狀會因IGBT和二極管芯片的功率損耗而產生溫度變化而變形。這種小但重復的基板變形會擠出熱界面材料,被稱為“泵出現象”。為了確保熱界面材料的長期穩定性,需要開發一種先進的封裝結構,能夠防止在連續溫度循環下基板的翹曲。
傳統的功率模塊結構如圖2所示,其組件及熱膨脹系數(CTE)在表1中描述。在這一結構中,陶瓷、焊料和銅基板作為模塊基礎的組成部分,具有不同的CTE值。當因各個IGBT/FWDs的操作產生熱量而使外殼溫度變化時,每個組件因不同的CTE值而以不同的程度膨脹和收縮。最終,各層之間的差異應變導致差異變形,類似于典型的雙金屬結構。這種現象是基板翹曲的原因。

功率模塊中的重復溫度變化會導致基板的重復翹曲,如圖9(a)和(b)所示。這種翹曲擠出了熱界面材料。這種泵出現象導致基板與散熱片之間的熱接觸不良,從而造成Rth(c-s)和功率模塊的熱散耗能力退化。其結果將是功率模塊的加速老化,在最壞的情況下,當結溫超過絕對最大額定值時,模塊可能發生熱失效。
新的封裝結構通過匹配組件材料的CTE值,可以顯著減少模塊材料之間的差異應變。封裝的內部結構及其CTE值分別在表1和圖2中描述。這一與CTE值相符的結構與傳統結構相比,導致因溫度變化而造成的基板變形顯著減少。圖10顯示了基板組件(傳統結構和新結構)的應力分析結果(有限元法)。圖10中位移的大小經過相同的放大因子處理,以使差異更加明顯。
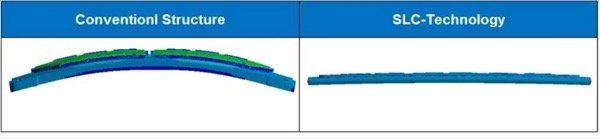
模擬結果表明,采用樹脂材料的新結構在溫度變化期間,對基板變形的響應得到了改善。
為進行實驗驗證,在氣候室(也稱為環境室)控制的三個不同環境溫度下,測量了基板中心點的垂直位移。參考長度為91mm(縱向方向)。在25°C到125°C的溫度變化中測得的位移僅為13.4μm,這意味著基板沒有顯著的翹曲。在與典型的熱界面材料進行的實際評估中,經過300次熱循環(-40°C ~ +125°C)后未發現泵出現象。
確認新型功率模塊結構在相鄰層之間具有匹配的熱膨脹系數,能夠在溫度循環期間最小化基板的翹曲,從而顯著降低泵出故障事件的可能性。
總結
改進的SLC技術使得第七代NX系列IGBT模塊的產品線擴展到1700V級,利用了改進IMB的較高絕緣電壓和優越的熱導率。這項技術使我們能夠開發出122x62mm2尺寸的600A/1700V模塊。
SLC技術還提供了顯著改善的熱循環能力,同時消除了泵出故障。第七代芯片通過降低功率損耗提供了卓越的效率。將該芯片與SLC技術結合,新開發的第七代NX系列IGBT為高效率、高功率密度和高可靠性等電力電子系統的要求提供了優秀的解決方案。
-
模塊
+關注
關注
7文章
2707瀏覽量
47474 -
IGBT
+關注
關注
1267文章
3793瀏覽量
249021 -
電力電子
+關注
關注
29文章
564瀏覽量
48885 -
slc
+關注
關注
0文章
49瀏覽量
22724
發布評論請先 登錄
相關推薦
如何在高功率密度模塊電源中實現低損耗設計
650V IGBT采用表面貼裝D2PAK封裝實現最大功率密度
基于德州儀器GaN產品實現更高功率密度
氮化鎵GaN技術怎么實現更高的功率密度
高功率密度的解決方案
功率密度的基礎技術簡介
探究功率密度基礎技術
如何提高4.5 kV IGBT模塊的功率密度
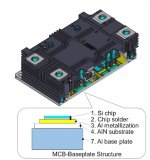
評論