在當今的半導體產業中,封裝技術的重要性不言而喻。它不僅保護了脆弱的芯片,還確保了電子信號的正確傳輸。但是,在封裝過程中可能會出現一些缺陷,如空洞、裂紋等,這些缺陷會影響電子設備的性能和可靠性。為了實現更高質量的封裝檢測,二維X光和三維X射線顯微鏡成為了兩種關鍵的檢測手段。
二維X光設備相對經濟,這使得它在眾多中小型企業中得到廣泛應用。在操作上,二維X光系統通常操作較為簡便易于培訓,且成像速度快,適合在線實時檢測。然而,這種技術的缺點也很明顯,由于只能提供單一平面的圖像,對于復雜的三維結構,如堆疊芯片或者細間距的封裝,二維X光可能難以準確捕捉到所有的內部信息。此外,當遇到密度相近的材料時,二維X光的對比度往往不足以分辨出細微的缺陷(如圖1-2)。
▲圖1 芯片封裝二維X光測試圖
▲ 圖2 BGA焊球二維X光測試圖
相較之下,三維X射線顯微鏡則提供了更為全面的細節揭示能力。通過旋轉樣品或者X光源,收集多個角度的二維影像,再借助先進的計算機重建算法,可以構建出樣品的三維模型。這樣的三維成像技術,不僅能夠展示出物體的外部輪廓,還能夠深入到內部,觀察到封裝體中的細微結構。這對于分析封裝內部的復雜互連結構、焊點質量、層間連接等至關重要。三維X射線顯微鏡技術的優勢主要體現在以下幾個方面:首先,它能提供更為清晰的立體視圖,讓檢測人員能夠準確判斷組件間的相對位置和連接狀態;其次,三維成像可以揭示微小裂紋或空隙等瑕疵,這些是傳統二維檢測難以發現的;此外,它還可以進行層間分析,對多層堆疊結構的質量控制尤為重要;最后,三維數據有助于逆向工程學的研究,為設計改良提供直觀的參考(如圖3-4)。
▲圖3 2.5D封裝模塊三維重構圖
▲圖4 多層基板層間尺寸測量
三維X射線顯微鏡的分析案例:
在BGA焊球失效分析領域,三維X射線技術能夠深入到封裝內部,對焊球與焊盤間的連接狀態進行無損檢測。例如:故障模塊接口出現故障,初步懷疑是故障點在芯片內部bump引腳間的路徑上。通過掃描發現bump層與上部分的銅柱有10-19um的位移差(如圖5),這種現象(如圖6)多集中在芯片的邊緣位置。
▲圖5 Bump層與銅柱偏移量測量圖
▲圖6 焊球偏移位置分布圖
另外從截面的切片可以觀察到Bump與基板連接處有斷裂的現象,涉及的寬度為60um,高度約為10um(如圖7)。通過對焊點形態、位置以及尺寸的精確測量,技術人員可以清晰地識別出虛焊、冷焊、裂紋等常見缺陷。這種非破壞性的檢測方式不僅節省了拆解和重組的時間成本,更重要的是,它能夠在不破壞樣品的前提下,提供更為全面和直觀的內部信息,幫助研發人員找到潛在的設計或工藝問題,從而優化產品的性能和可靠性。
▲圖7 Bump層底部斷裂觀察圖
同樣,在硅光模塊的耦合失效分析中,三維X射線技術展現出其獨到的優勢。硅光模塊作為集成光學器件,一般需要光纖與芯片進行精密的對準。當光波導與光纖之間出現耦合效率下降,甚至失效時,利用三維X射線成像技術可以準確地觀察耦合區域的結構情況。例如:通過掃描垂直耦合模塊,可以觀察和測量垂直耦合的平整度和傾斜角度。同時能觀察水平耦合是否對準和灌膠是否充分等現象(如圖8-9)。無論是由于物理位移、污染還是結構變形所導致的耦合不良,三維X射線都能給出清晰的圖像,為失效原因的診斷提供了直接而準確的依據。
▲圖8 垂直耦合傾斜偏移量測量
圖9 水平耦合對準與灌膠形貌觀察
三維X射線技術在半導體領域的應用具有多方面的重要意義。它不僅能夠提供深入的內部視圖,幫助工程師們理解材料的特性,還能夠進行精確的缺陷檢測和質量控制,確保產品的可靠性和性能。隨著半導體技術的不斷進步,三維X射線技術將繼續發揮其不可替代的作用,推動半導體行業的發展。
審核編輯 黃宇
-
半導體
+關注
關注
334文章
27518瀏覽量
219841 -
封裝
+關注
關注
127文章
7948瀏覽量
143108
發布評論請先 登錄
相關推薦
電動變倍自動對焦顯微鏡:半導體芯片檢測的精密之眼
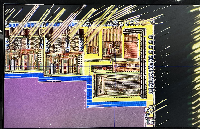
優可測超景深數碼顯微鏡AH-3000系列 產品手冊
掃描電子顯微鏡用在半導體封裝領域
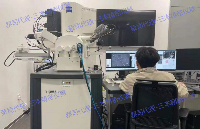
開爾文探針力顯微鏡檢測的是什么信號
共聚焦顯微鏡:成像原理、功能、分辨率與優勢解析
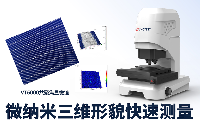
ZEX-MD3三維視頻顯微鏡(4K)
共聚焦、光學顯微鏡與測量顯微鏡的區分
用于材料領域的共聚焦顯微鏡可以看到什么?
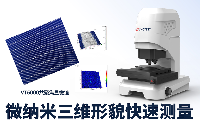
共聚焦顯微鏡和激光共聚焦顯微鏡的區別詳解
共聚焦顯微鏡和激光共聚焦顯微鏡的區別詳解
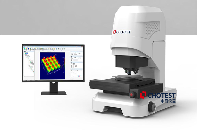
Argolight熒光顯微鏡校準載玻片簡介
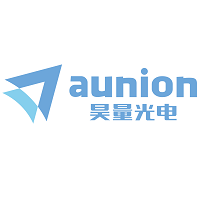
顯微測量|共聚焦顯微鏡大傾角超清納米三維顯微成像
顯微測量|共聚焦顯微鏡大傾角超清納米三維顯微成像
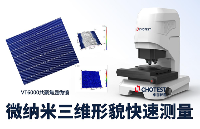
評論