作為資金和技術雙重密集型的現代化產業,汽車行業歷經百余載的發展,已漸漸構筑起一條宏偉的產業鏈,成為世界上最大規模和最高產值的產業之一。
數據顯示,2023年,我國汽車產業以年產3016.1萬輛、銷售3009.4萬輛的輝煌成績,連續15年穩坐全球汽車產業的頭把交椅,彰顯出強大的產業實力和蓬勃的發展活力。汽車行業不僅是國民經濟的重要驅動力,更是人們出行方式不斷進化的關鍵支撐。而且,隨著智能制造技術的深入推進,汽車生產的自動化與智能化轉型已成為不可阻擋的趨勢。
而在汽車制造的復雜流程中,質量檢測至關重要。傳統的檢測方法在面對日益多樣化的汽車零部件和不斷更新的設計制造技術時,逐漸暴露出諸多局限性,AI視覺檢測技術的出現,為汽車行業帶來了全新的檢測理念和高效的解決方案。
汽車行業進行視覺檢測的現有難點及升級AI的困局01
復雜背景下的檢測挑戰
汽車零部件的結構復雜,背景多樣,傳統算法在處理這些復雜背景時往往面臨較大的挑戰。
例如,發動機缸體在鑄造過程中可能產生的砂眼、裂紋等細小缺陷,這些缺陷用肉眼很難觀察到,傳統的觸摸檢測和超聲波檢測也無法進行全面的檢測和評估;而在輪胎檢測中,其表面的復雜紋理和顏色變化會影響檢測;在汽車外觀漆面檢測中,車身結構復雜、角度多樣以及人員檢測標準不同等,都容易導致缺陷產品流入后續工序。
02
多變的缺陷類型
汽車零部件在生產過程中可能出現多種類型的缺陷,如絕緣紙卷入、絕緣紙破損、端板破損、銅線偏位、磁材表面損傷、銅線損傷等。這些缺陷形態特征各異,傳統的視覺檢測方案難以兼顧所有類型的缺陷,尤其是在型號切換時效率較低。
03
數據標注與模型訓練
AI視覺檢測技術依賴于大量的標注數據進行模型訓練,然而,獲取高質量的標注數據是一個耗時耗力的過程,特別是在汽車零部件檢測中,需要專業的技術人員進行細致的標注。此外,模型訓練過程中還需要不斷調整參數,以確保模型的準確性和魯棒性。
04
系統集成與兼容性
將AI視覺檢測系統集成到現有的生產線中,需要解決與現有設備和系統的兼容性問題。例如,智能相機需要與生產線的控制系統、數據庫等進行無縫對接,以實現數據的實時傳輸和處理。此外,系統的穩定性和可靠性也是重要的考量因素。
05
成本與投入
引入AI視覺檢測技術需要較大的初期投入,包括購買高性能的攝像頭、計算設備和軟件平臺等。對于中小企業來說,這是一筆不小的開支。盡管長期來看,AI視覺檢測能夠顯著提高生產效率和產品質量,但在短期內仍需克服資金壓力。
06
技能要求與培訓
AI視覺檢測技術的應用需要專業的技能和知識,操作人員需要具備一定的編程能力和數據分析能力。對于現有的生產線工人來說,這可能是一個新的挑戰。企業需要投入時間和資源對員工進行培訓,以確保他們能夠熟練操作新的檢測設備。
基于行業現狀,阿丘科技在汽車行業的 AI 視覺檢測解決方案具有獨特優勢,其深度學習算法在處理復雜檢測場景,適應不同車型和零部件的多樣化檢測需求,且在檢測準確性、效率提升和人力成本降低等方面成效顯著。
典型場景案例01
差速器螺栓涂膠質量檢測:守護行車安全的重要防線
差速器是汽車傳動系統中的一個重要部件,負責將動力從發動機傳遞到車輪,并允許左右車輪以不同的速度旋轉,從而在轉彎時保持車輛的平穩行駛。而差速器螺栓作為汽車變速箱中的關鍵部件,差速器螺栓涂膠是一種在汽車制造過程中重要的工藝步驟,即將特定的膠液均勻地涂抹在螺栓上,以增強螺栓與螺母之間的連接強度,防止因振動或沖擊而導致的螺栓松動,從而有效保障汽車的行駛安全。
所以,涂膠質量會直接關系到行車安全,一旦螺栓出現缺膠或斷膠等不良情況,在車輛行駛過程中,螺栓可能會逐漸松動甚至脫落,無疑是一顆隨時可能引爆的 “安全炸彈”。
此前,某工廠采用傳統算法的視覺傳感器進行檢測,雖然能夠在一定程度上檢測出缺膠問題,但對于斷膠的檢測效果卻不盡人意,漏檢現象嚴重,導致客戶投訴頻發。同時,傳統算法在參數調節過程中繁瑣復雜,嚴重干擾了正常生產秩序。
常見相關檢測舉例:
少膠檢測:檢查螺栓螺紋部分是否完全涂覆了膠水,確保沒有未涂膠的區域
斷膠檢測:檢查膠水是否有斷裂或不連續的情況,確保膠水層的完整性和均勻性
厚度檢測:測量膠水的厚度,確保其在規定的范圍內,既不過薄也不過厚
固化檢測:檢查膠水是否完全固化,確保其具備足夠的強度和粘接力
阿丘科技針對這一難題,精心打造了一套基于深度學習智能相機的檢測方案。
采用阿丘科技的深度學習智能相機,其集成了成像、圖像處理和通信功能于一體,結構小巧,僅需通過網絡連接到PC端,即可迅速啟動檢測工作。該相機具備高精度的成像能力,能夠清晰捕捉螺栓涂膠部位的細節信息。利用智能相機對螺栓進行分4次旋轉拍攝,確保能夠覆蓋螺栓一周的涂膠區域,不放過任何一處可能存在缺陷的地方。
基于阿丘科技的AIDI檢測算法,針對差速器螺栓涂膠可能出現的缺膠和斷膠等不良情況,重點學習這些缺陷的特征。通過大量包含正常涂膠和各類缺陷涂膠的螺栓圖像數據,讓算法深入理解不同涂膠狀態的特征模式。同時,運用數據增廣工具擴增數據,例如對原始圖像進行旋轉、翻轉、縮放等操作,增加數據的多樣性,使算法能夠更好地適應實際生產中螺栓涂膠的各種變化情況,有效提高缺陷的識別率。
阿丘科技的方案能夠精準地檢出任意位置的缺膠和斷膠不良情況,并及時提示人工進行補膠操作,為汽車安全裝上了一道堅固的防護鎖,有效杜絕了因螺栓涂膠問題引發的客戶質量投訴。從操作層面來看,簡便易行,3天內即可完成上線部署,投入使用后檢測穩定可靠,無需人工頻繁干預。與傳統檢測方法相比,漏檢率降至0%,過檢率控制在0.1%以內,檢測精度和穩定性實現了質的飛躍。
02
發動機裝配檢測:精密協作,確保發動機完美組裝
汽車發動機堪稱汽車的“心臟”,其裝配過程涉及眾多復雜的部件,對尺寸、形狀和位置等參數的精度要求極高,且涵蓋多個部件的組裝與調試,以確保發動機能正常、高效運行。主要裝配內容如:零部件清洗與預處理、曲軸飛輪組裝、活塞連桿組裝配、氣缸蓋及配氣機構裝配、潤滑與冷卻系統裝配、進排氣系統裝配、發動機附件裝配等。為保證發動機裝配質量,裝配過程中及裝配完成后需進行關鍵檢測,比如檢測是否所有裝配安裝到位,以及各零部件的有無情況。
然而單純依靠傳統算法進行發動機裝配檢測,仍面臨著以下挑戰。
1、特征提取困難:難以全面且準確地提取復雜的特征,例如一些細微的缺陷、復雜的形狀或紋理特征等。
2、對復雜環境適應性差:例如光照變化、物體遮擋和背景干擾等情況,可能導致檢測準確性下降。
3、對特殊材質或復雜形狀產品檢測難度大:現有的算法和模型可能無法有效識別這些情況下的缺陷。
4、泛化能力較弱:對于不同類型的發動機或部件,可能需要大量的調整和重新設計算法,無法像深度學習那樣較好地泛化到新的情況。
5、無法自動學習和適應新任務:需要大量的人工干預和重新編程來適應新的檢測任務。
6、難以發現隱性問題:對于數據間的高階、復雜關聯的把握能力有限,可能無法發現一些隱性的質量問題。
基于種種現實挑戰,某設備商與發動機廠商在依靠傳統算法聯合研發裝配檢測設備時,由于發動機型號繁多,每種型號的檢測項目又各不相同,再加上復雜的背景干擾,開發工作困難重重,開發周期漫長,且檢測結果的可靠性難以保證,無法為發動機制造廠提供有效的算法解決方案。
阿丘科技將AIDI各算法模塊與傳統算法巧妙融合,在檢測過程中,利用AI技術發揮其強大的定位功能,迅速鎖定部件位置。由傳統算法基于顏色、位置等特征進行二次判定,二者相輔相成,共同應對復雜的檢測環境。此外,阿丘科技還創新地設計了多個工位共用檢測流程的方案,這一舉措不僅簡化了方案設計,還極大地便于項目實施,有效提高了生產效率。
此方案成功為發動機裝配檢測設備開發出完整的檢測方案,助力檢測系統順利上線并實現批量部署,顯著提升了產品良率,為發動機制造企業的生產質量提供了堅實保障。阿丘科技充分發揮了AI及傳統算法各自的特色,有效解決了汽車裝配檢測中的復雜需求,推動發動機裝配檢測向智能化邁進了一大步。同時,減少了人工檢測的比例,降低人力成本,提高了企業的生產效益和市場競爭力。
-
AI
+關注
關注
87文章
30894瀏覽量
269085 -
視覺檢測
+關注
關注
2文章
377瀏覽量
19250 -
汽車
+關注
關注
13文章
3515瀏覽量
37311
發布評論請先 登錄
相關推薦
啟明信息榮獲全國首屆汽車行業智能制造創新成果三等獎
智能制造在汽車行業的應用
軟件與半導體技術重塑汽車行業:新思科技助力提升汽車智能化與可靠性
Orin芯片在汽車行業的應用
汽車行業迎來新的飛躍:芯粒成為創新動力
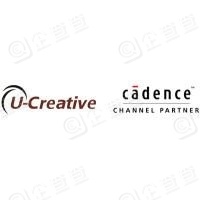
SAP賦能汽車行業:駛向數字化轉型的快車道
Modbus轉Profibus網關在汽車行業的應用
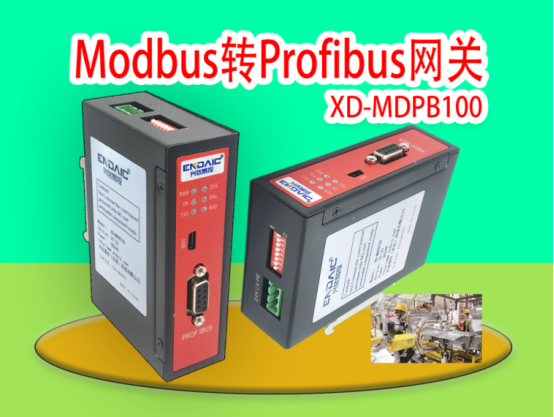
行業案例:這些新能源汽車行業廠商,都在用agv叉車降本增效
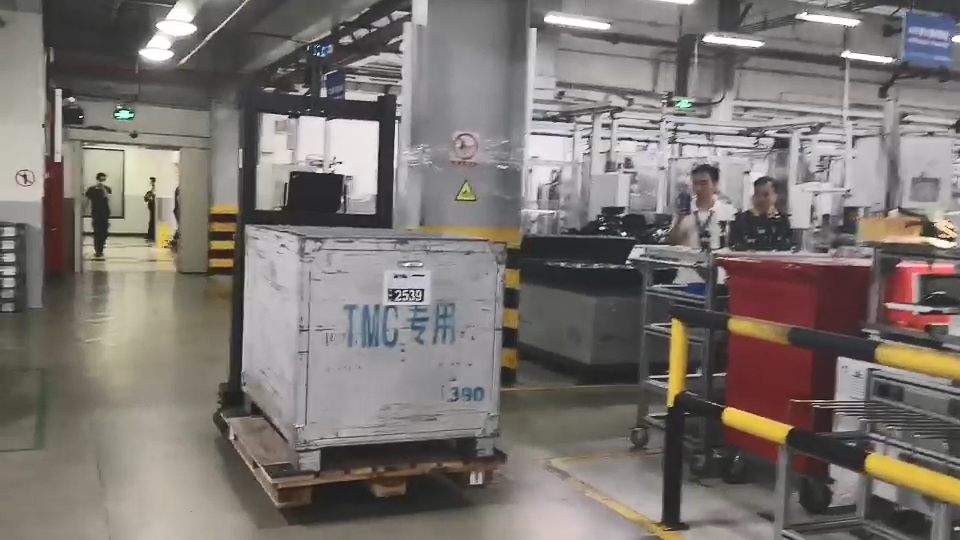
評論