摘要:在最近的半導(dǎo)體封裝中,采用硅通孔 (TSV) 技術(shù)已成為集成 2.5 和 3D Si芯片以及中介層的關(guān)鍵。TSV 具有顯著的優(yōu)勢(shì),包括高互連密度、縮短信號(hào)路徑和提高電氣性能。然而,TSV 實(shí)施也存在電氣損耗、基板翹曲和高制造成本等挑戰(zhàn)。相比之下,基于玻璃的玻璃通孔 (TGV) 具有良好的特性,例如出色的絕緣性能、成本效益和可變的熱膨脹系數(shù) (CTE) 值,可減輕堆疊器件的翹曲。此外,它們還有助于小型化并支持高頻應(yīng)用。本文概述了半導(dǎo)體封裝發(fā)展中玻璃基板、TGV 鉆孔技術(shù)、功能層沉積和銅填充工藝的最新進(jìn)展。
1 簡(jiǎn)介
隨著移動(dòng)設(shè)備和物聯(lián)網(wǎng) (IoT) 的發(fā)展,人們正在開展三維 (3D) 封裝技術(shù)的研究,以實(shí)現(xiàn)更小更薄的封裝尺寸和更高的電氣可靠性。盡管半導(dǎo)體傳統(tǒng)上采用硅基板,但為了滿足移動(dòng)電子設(shè)備和物聯(lián)網(wǎng)等先進(jìn)電子元件的要求,對(duì)玻璃基板的需求也在增加。2022 年玻璃通孔 (TGV) 基板的市場(chǎng)規(guī)模估計(jì)為 6000 萬美元,預(yù)計(jì)到 2029 年將達(dá)到 4.805 億美元,2023 年至 2029 年預(yù)測(cè)期內(nèi)的復(fù)合年增長(zhǎng)率為 34.2% 。玻璃具有低介電常數(shù)、低電損耗和可變的熱膨脹系數(shù) (CTE),被認(rèn)為是射頻通信和中介層應(yīng)用的合適材料,需要形成精確的 TGV 來實(shí)現(xiàn)芯片之間的電連接。圖 1顯示了以玻璃和 TGV 作為中介層的 2.5D 半導(dǎo)體封裝應(yīng)用的示例。
圖1 適用于 2.5D 半導(dǎo)體封裝的玻璃中介層
與傳統(tǒng)的引線鍵合相比,TGV 可實(shí)現(xiàn)更密集的互連,從而能夠在有限的空間內(nèi)放置更多的電信號(hào)。在玻璃基板上實(shí)施的 TGV 有助于抑制串?dāng)_和插入損耗等問題,這些問題在硅基 TSV 中很常見。玻璃出色的 RF 透明度使高頻信號(hào)能夠輕松通過 TGV 傳輸,從而實(shí)現(xiàn)高頻下的低電氣損耗和在無線通信和雷達(dá)應(yīng)用中的高性能。此外,玻璃基板的剛性和絕緣性、低成本以及厚度約 100 ? 的超薄柔性玻璃基板的好處在電子封裝領(lǐng)域具有優(yōu)勢(shì)。而且,玻璃基板的熱穩(wěn)定性和機(jī)械穩(wěn)定性可實(shí)現(xiàn)更密集的互連和可擴(kuò)展性,從而提高半導(dǎo)體性能。
優(yōu)化 CTE 對(duì)于實(shí)現(xiàn)可靠的 3D 封裝至關(guān)重要。與硅不同,非晶玻璃具有可變的 CTE,這可最大限度地減少因與其他材料的 CTE 不匹配而導(dǎo)致的翹曲。圖 2顯示了 2.5D 封裝中因 CTE 不匹配而導(dǎo)致的翹曲:(a) 顯示硅中介層的翹曲,而 (b) 演示了如何調(diào)整 CTE 以最大限度地減少玻璃和基板之間的翹曲。
圖2 使用不同中介層材料的 2.5D 封裝,(a) 硅中介層,(b) 玻璃中介層
翹曲也是先進(jìn)封裝領(lǐng)域面臨的一大難題,如具有高集成度和優(yōu)異散熱特性的扇出型晶圓級(jí)封裝(FOWLP)。與傳統(tǒng)封裝相比,F(xiàn)OWLP 的厚度更薄,并且是在晶圓級(jí)進(jìn)行加工,因此其翹曲程度遠(yuǎn)高于芯片級(jí)。玻璃材料可調(diào)節(jié)的CTE可最大程度地減少因基板變薄變大而引起的問題,在先進(jìn)3D封裝領(lǐng)域具有很高的適用性。另一方面,也需要解決與Si相比熱導(dǎo)率較低、表面缺陷導(dǎo)致裂紋等難題。近日,隨著英特爾在Semicon Japan展會(huì)上宣布以TGV及相關(guān)技術(shù)實(shí)現(xiàn)“先進(jìn)半導(dǎo)體封裝基板技術(shù)的下一代發(fā)展”,相關(guān)各類技術(shù)領(lǐng)域也都取得了重大進(jìn)展。
本研究將探討玻璃基板上半導(dǎo)體3D封裝的高性能、可靠的TGV形成技術(shù)及相關(guān)研究。
2 TGV 形成技術(shù)
2.1 激光誘導(dǎo)選擇性蝕刻(LISE)
LISE 是一種 TGV 形成技術(shù),該技術(shù)使用激光局部蝕刻照射區(qū)域以形成圖案。使用脈沖寬度極短(從飛秒到皮秒)的激光,可以在很短的時(shí)間內(nèi)集中照射高能激光脈沖。在玻璃基板上形成 TGV 的過程中,激光在短時(shí)間內(nèi)將高能量局部傳送到玻璃表面。這會(huì)引起熱機(jī)械效應(yīng),從而改變玻璃的表面膨脹和密度,從而產(chǎn)生對(duì)化學(xué)蝕刻敏感的區(qū)域。在這些區(qū)域用 KOH 等溶液進(jìn)行化學(xué)蝕刻會(huì)形成納米衍射光柵結(jié)構(gòu)(稱為納米凹坑),從而改變玻璃的表面。通過調(diào)節(jié)激光照射的脈沖能量和化學(xué)蝕刻條件,可以控制納米凹坑的大小,并獲得所需的通孔形狀。
利用LISE在熔融石英基底中制備納米衍射光柵結(jié)構(gòu)也有報(bào)道。Jia等人使用波長(zhǎng)為1030nm的單脈沖飛秒激光以不同的脈沖間隔照射平行線圖案,然后用85°C的KOH溶液進(jìn)行5小時(shí)的選擇性蝕刻。脈沖持續(xù)時(shí)間為290fs,脈沖重復(fù)頻率為1MHz。SEM測(cè)量表明,在脈沖間隔為1μs和2μs時(shí),由于熱積累和擴(kuò)散,沒有發(fā)生選擇性蝕刻,導(dǎo)致納米結(jié)構(gòu)分散。從3μs的脈沖間隔開始,熱能擴(kuò)散到周圍環(huán)境,從而觀察到規(guī)則且連通的納米衍射光柵結(jié)構(gòu)。然而,超過5,000μs的脈沖間隔后,雖然出現(xiàn)了納米衍射光柵,但它們并不互連,從而阻止了蝕刻的進(jìn)行。總之,據(jù)報(bào)道,納米衍射光柵結(jié)構(gòu)的產(chǎn)生和連接是飛秒激光選擇性蝕刻過程中圖案形成的主要機(jī)制。
Kim 等研究了超短脈沖激光持續(xù)時(shí)間和脈沖波形對(duì)硼硅酸鹽玻璃中 TGV 形成速率的影響。實(shí)驗(yàn)中采用間隔為 213ps、10ns 和 500ms 的單脈沖和雙脈沖。每個(gè)脈沖輻照 0.2至 1ps 后,使用 KOH 溶液,通過 OM 和 SEM 的橫截面比較形成的 TGV。比較表明,隨著脈沖持續(xù)時(shí)間從 0.2ps 增加到 1ps,TGV 的直徑減小,深度增加,但只有間隔為 10ns 的雙脈沖顯示出一致的深度。這是因?yàn)椴煌妮d流子相關(guān)現(xiàn)象主要取決于脈沖之間的時(shí)間間隔。在間隔為 213ps 的雙脈沖中,由于電子接收能量,激活載流子處于激發(fā)態(tài),此時(shí)會(huì)有額外的光子輻射,從而增加電子的動(dòng)能,進(jìn)而增加光子的穿透深度。然而,對(duì)于間隔為 10ns 的脈沖,電子會(huì)返回基態(tài),并且會(huì)有額外的光子輻射,導(dǎo)致熱擴(kuò)散占主導(dǎo)地位。在這種情況下,熱擴(kuò)散的長(zhǎng)度不會(huì)隨脈沖持續(xù)時(shí)間而發(fā)生顯著變化,因此 TGV 的深度保持一致。
脈沖寬度為1ps時(shí),間隔為213ps的雙脈沖形成的TGV孔最深,為22.39 ?,并觀察到厚度為156±22 nm的納米衍射光柵。綜上所述,間隔為ps的雙脈沖可以通過增強(qiáng)電子的動(dòng)能來提高TGV的形成速率,證明了提高電子的動(dòng)能比熱擴(kuò)散更有利于加工。
蝕刻液濃度也是影響TGV輪廓的主要因素,Chen等報(bào)道通過調(diào)整硼硅酸鹽玻璃中HF蝕刻液的濃度可以改善TGV側(cè)壁的錐度。實(shí)驗(yàn)所用的激光器為皮秒單脈沖激光器,脈沖能量為55μJ,脈沖寬度為16ps。用單脈沖激光束輻照的三個(gè)相同樣品分別用10%、5%、3%濃度的HF溶液蝕刻,通過橫截面測(cè)量TGV側(cè)壁的角度。對(duì)于表面直徑為60 ?的TGV,隨著HF溶液濃度從10%降低到3%,通孔側(cè)壁的角度從80.65°增大到84.18°,有效改善了TGV輪廓。同時(shí),隨著脈沖數(shù)從1增加到10,通孔側(cè)壁的角度從80.65°增加到81.13°,但增加幅度很小。圖3為實(shí)驗(yàn)中所采用的LISE技術(shù)的示意圖及所形成的TGV的橫截面。
圖 3(a)LISE工藝示意圖,(b)硼硅酸鹽玻璃上TGV結(jié)構(gòu)的橫截面圖
2.2 電火花加工法(EDM)
EDM 是一種利用放電的 TGV 形成技術(shù),利用高電壓和電流在玻璃基板上形成精確的結(jié)構(gòu)。該技術(shù)涉及分兩個(gè)步驟將玻璃保持在兩個(gè)對(duì)齊的電極之間。首先,集中放電并產(chǎn)生熱量,從而局部降低玻璃的粘度。其次,通過焦耳加熱提取玻璃,形成一個(gè)孔。與傳統(tǒng)的 TGV 形成方法相比,EDM 工藝可以在相對(duì)較短的時(shí)間內(nèi)形成具有高縱橫比的孔。EDM 僅使用放電,但也使用諸如 ECDM(電化學(xué)放電法)之類的方法,該方法通過添加電解質(zhì)將放電與化學(xué)反應(yīng)結(jié)合起來。
Harindra 等人使用 KOH 電解液的 ECDM 工藝在熔融石英基板上形成 TGV,并制作了 3D 電感器。由于硅基板上的電感器電阻率低,因此需要沉積絕緣層的工藝。另一方面,在玻璃基板上制作的電感器不需要絕緣層,簡(jiǎn)化了工藝,而且玻璃的透明光學(xué)特性使其更容易在生產(chǎn)過程中發(fā)現(xiàn)缺陷。實(shí)驗(yàn)在直徑 2 英寸、厚度 520 ? 的熔融石英基板上進(jìn)行,使用 2x5 和 2x2 陣列的不銹鋼多尖端形成孔。測(cè)得的 140±10 ? 尺寸多尖端形成的 TGV 的平均頂部和底部直徑分別為 580±71 ? 和 286±45 ?。制作了螺旋電感和環(huán)形電感,測(cè)得的電感電阻分別為 338 mΩ 和 168 mΩ。這項(xiàng)研究證實(shí)了 TGV 工藝在 3D 電感制作中的適用性。圖 4是在熔融石英基板上制作 3D 電感的工藝示意圖。
圖 4 在熔融石英襯底上制造 3D 電感器的示意圖,(a) 熔融石英襯底,(b) 通過 ECDM 制造的 TGV,(c) 粘合到載體襯底的襯底,(d) 電鍍銅,(e) 拋光掉銅種子層,(f) 兩側(cè)沉積 Ti/Cu 層,(g) 兩側(cè)光刻以確定 RDL 模具,(h) 電鍍銅、光刻膠去除和種子層濕法蝕刻
已經(jīng)開展了研究,利用添加劑或激光加工來改善由 EDM 和 ECDM 形成的 TGV 的特性。
Zhixiang 等通過在 KOH 電解液中添加非轉(zhuǎn)移功能 (NTF) 電解液聚丙烯酰胺 (PAM)進(jìn)行了一項(xiàng)研究,以提高 ECDM 形成的 TGV 的均勻性和重復(fù)性。NTF 電解液不具有高電傳輸特性,用于控制 ECDM 工藝中的電效應(yīng)。與傳統(tǒng)的 KOH 電解液不同,使用 NTF 電解液可以實(shí)現(xiàn)阻尼和限制效果。阻尼效果是指減少 ECDM 工藝中產(chǎn)生的振動(dòng)。在 ECDM 加工過程中,由于電解液和電極之間的放電,玻璃表面會(huì)產(chǎn)生微振動(dòng),從而對(duì)精密加工產(chǎn)生負(fù)面影響。限制效應(yīng)是指限制 ECDM 加工過程中發(fā)生放電的區(qū)域,從而實(shí)現(xiàn)精密加工。通過限制效應(yīng)使放電集中在特定區(qū)域,可以形成精確的 TGV。實(shí)驗(yàn)中,將濃度為 0.1 wt% 至 0.9 wt% 的 NTF 電解液添加到 KOH 電解液中,并在鈉鈣玻璃基板上進(jìn)行 ECDM 加工。結(jié)果表明,使用 0.5 wt% NTF 電解液制成的 81 個(gè)微孔陣列的過切標(biāo)準(zhǔn)偏差為 3.34 ?,與僅使用 KOH 電解液的標(biāo)準(zhǔn)偏差 9.79 ? 相比有顯著改善。TGV 形成過程中產(chǎn)生的熱影響區(qū) (HAZ) 寬度也減少了 64.81%,證明了 NTF 電解液在 ECDM 工藝中的有效性。
Harmesh 等人進(jìn)行了研究,以使用添加碳納米管 (CNT) 的電極來提高 EDM 的性能。在實(shí)驗(yàn)中,在主要由碳和鉻組成的鋼基體上使用納米粉末形式的 CNT,并且在 EDM 過程中將 CNT 顆粒與電介質(zhì)混合,產(chǎn)生火花并有助于提高工件的侵蝕速率。火花均勻分布在 CNT 顆粒之間,提高了工件的材料去除率 (MRR) 和表面粗糙度 (SR)。結(jié)果表明,與傳統(tǒng) EDM 相比,添加 4g CNT 的 EDM 工藝的 MRR 高 80%,SR 低 67%。總之,添加的 CNT 的濃度是顯著影響 EDM 工藝中 MRR 和 SR 的關(guān)鍵參數(shù)。
Zhao 等對(duì)激光輔助 (LA) ECDM 進(jìn)行了研究,該技術(shù)將激光加工與 ECDM 相結(jié)合。實(shí)驗(yàn)中,采用波長(zhǎng)為 1064 nm、脈沖持續(xù)時(shí)間為 12 ps 的 Nd:YVO 4激光器,激光輻照后在 NaOH 電解液中進(jìn)行 ECDM。結(jié)果表明,由于限制效應(yīng),激光輻照后進(jìn)行的 ECDM 加工精度有所提高。此外,僅用激光加工的孔呈 V 形,錐度較大。在 LA-ECDM 中,孔的輪廓從 V 形轉(zhuǎn)變?yōu)?U 形,錐度明顯改善。
通過電化學(xué)放電加工形成TGV具有在短時(shí)間內(nèi)制造大量TGV的優(yōu)點(diǎn),但加工過程中產(chǎn)生的熱量引起的電極磨損會(huì)對(duì)TGV輪廓產(chǎn)生負(fù)面影響。電極磨損直接影響加工精度和形成的TGV的可靠性,由于EDM加工成本的約70%歸因于電極更換,因此減少磨損至關(guān)重要。
Jafferson 等進(jìn)行了通過低溫冷卻減少電極磨損的實(shí)驗(yàn)。實(shí)驗(yàn)中,以-185°C 的液氮作為低溫冷卻材料,以銅和鎢為電極材料,以 1 mm 厚的不銹鋼為基體。結(jié)果表明,鎢電極的工具磨損率 (TWR) 降低了 58%,銅電極降低了 35%,表明低溫冷卻顯著降低了工具磨損。此外,對(duì)經(jīng)過低溫處理的電極進(jìn)行維氏硬度測(cè)試表明,鎢電極的硬度增加了 120%,銅電極的硬度增加了 17%,證明了低溫冷卻的有效性。
3. 功能薄膜形成及TGV中的Cu填充
3.1 TGV內(nèi)壁功能薄膜涂覆
功能薄膜是薄薄的沉積或涂層薄膜,旨在提供特定的物理、化學(xué)或電氣特性。這些薄膜具有各種功能,并用于眾多技術(shù)領(lǐng)域。每種功能薄膜都是根據(jù)其應(yīng)用領(lǐng)域的要求設(shè)計(jì)的,在 TGV 制造過程中起著至關(guān)重要的作用。
薄膜的用途包括(1)種子層:用作填充金屬(如Cu和Au)的平滑電鍍涂層,(2)絕緣層:用于電隔離TGV并防止相鄰TGV之間的電流泄漏和干擾,以及(3)粘附層:用于加強(qiáng)種子層和絕緣層之間的結(jié)合。
在玻璃基板上形成薄膜時(shí),包括濺射在內(nèi)的干法很常見,但在高縱橫比 TGV 中實(shí)現(xiàn)均勻的膜厚存在挑戰(zhàn)。相比之下,濕法涉及將玻璃基板浸入溶液中形成薄膜,可在 TGV 和玻璃表面上均勻一致地形成薄膜。如果種子層未在 TGV 內(nèi)壁上正確形成,則隨后可能會(huì)出現(xiàn)諸如 Cu 填充不完整等缺陷。
Chen 等人使用 Ni 活化和化學(xué)鍍 Ni-P 在 TGV 中形成金屬種子層。實(shí)驗(yàn)使用由 Li-Al-Si 組成的光反應(yīng)性玻璃;Ni-P 鍍層中的化學(xué)反應(yīng)如下(等式 1、2)。
Ni-P鍍層試件在200~450℃空氣中退火30min,150℃以下升溫速率為120℃/h,150℃以上升溫速率為60℃/h。結(jié)果表明,350℃以上退火后,鍍層結(jié)合力明顯提高,400℃以上形成氧化膜,使電阻增大。另據(jù)研究報(bào)告,Ni-P種子層在熱處理后結(jié)晶,顯示Ni和Ni3P相。Ni-P相以非晶態(tài)為主,退火后出現(xiàn)類似樹枝狀結(jié)晶,提高了與TGV的結(jié)合力。因此,鎳種子層可以有效涂覆長(zhǎng)寬比為10:1的通孔,平均層厚度約為200nm,通孔內(nèi)部表現(xiàn)出均勻的電鍍特性。
Inoue 等采用濕鍍法,即先化學(xué)鍍一層 Cu 薄膜,然后再進(jìn)行電鍍,在玻璃基板上形成 Cu 種子層。結(jié)果表明,在 Na 玻璃基板上,Cu 的附著強(qiáng)度為 0.6 kN/m,在無堿玻璃基板上,Cu 的附著強(qiáng)度約為 0.4 kN/m。
Takayama 等提出了一種將低真空高速濺射與電鍍相結(jié)合在無堿玻璃基片中TGV內(nèi)部形成Cu種子層的方法。高速濺射時(shí),膜壓為0.5-5 Pa,功率為35 kW,濺射時(shí)間為28 秒,在TGV基片平坦部分形成3? Cu膜,在TGV中心形成0.29? Cu膜,長(zhǎng)寬比為3.75(通孔直徑80?,深度300?)。濺射后采用硫酸和焦磷酸鍍液進(jìn)行電鍍,焦磷酸對(duì)Cu的附著強(qiáng)度超過1.0 kN/m。
Yiu 等人通過施加溶液基金屬氧化物的粘附促進(jìn)層 (APL),在熔融石英襯底上實(shí)現(xiàn)了高縱橫比 TGV 填充。APL 通過旋涂沉積在 TGV 的側(cè)壁上,然后進(jìn)行 Cu 層的化學(xué)鍍和使用直流電流的電鍍。結(jié)果表明形成了沒有空隙的 HAR-TGV,其長(zhǎng)度為 345 ?,直徑為 25?。APL 層可以通過浸涂和旋涂等多種方法沉積,并且在直流波形而不是復(fù)雜的 PPR 波形下實(shí)現(xiàn) HAR-TGV 凸顯了其重要性。
同時(shí),Shigeo 等人提出了一種濕鍍工藝,該工藝可以在玻璃上直接形成銅膜,而無需在銅和玻璃之間添加粘附層。首先,對(duì)無堿玻璃基板進(jìn)行超聲波清洗、堿性脫脂和紫外線照射,以去除玻璃表面的有機(jī)材料并增強(qiáng)粘附性。通過濕鍍工藝鍍上3 ? 銅層作為種子層,然后通過電鍍和SAP(半加成工藝)在TGV的側(cè)面、正面和背面涂覆15 ?厚的銅。結(jié)果表明,濕鍍銅種子層和電鍍銅均鍍層均勻,實(shí)現(xiàn)了0.35 kN/m的高粘附強(qiáng)度和玻璃優(yōu)異的表面平整度。測(cè)得的TGV 電阻低于平均值6.71 mΩ /via。TGV鍍膜濕鍍可應(yīng)用于大型玻璃基板,且無需額外的功能性薄膜鍍膜即可進(jìn)行工藝,具有廉價(jià)、高效的優(yōu)點(diǎn)。
Hariki 等人還提出了一種薄膜附著和封閉電鍍方法,以在 TGV 中填充 Cu,而無需在內(nèi)部形成種子層,并報(bào)告了在通孔內(nèi)部成功填充 Cu。
3.2 TGV 和 TSV 填充鍍銅
TGV、TSV的Cu填充主要采用電鍍法。電鍍是通過電流將金屬離子移動(dòng)到陰極,在特定表面鍍上目標(biāo)金屬的方法。在Cu電鍍過程中,電流通過含有Cu離子的鍍液,Cu離子移動(dòng)到陰極,在陰極獲得電子并被還原為銅。還原后的Cu離子沉積在TSV、TGV表面,形成鍍層。
TGV 和 TSV 內(nèi)部通過電鍍形成的金屬層受施加的電流密度和波形影響。在 DC(直流)Cu 填充中,通孔開口處的電流密度較高,導(dǎo)致頂部鍍層比底部厚,使通孔開口首先與 Cu 連接,使其容易在通孔內(nèi)部出現(xiàn)空洞和接縫等缺陷。可以通過施加脈沖電流、使用添加劑優(yōu)化電鍍?nèi)芤阂约笆褂贸暡▉砀纳拼祟惾毕荨?/p>
用于優(yōu)化電鍍液的添加劑包括抑制劑、促進(jìn)劑和整平劑。抑制劑和促進(jìn)劑控制電鍍過程中金屬沉積的速度,而整平劑則誘導(dǎo)均勻的金屬沉積,從而提高電鍍質(zhì)量。
關(guān)于添加劑,Ling 等研究了抑制劑和促進(jìn)劑對(duì) TGV 中 Cu 填充的協(xié)同作用。在實(shí)驗(yàn)中,使用深度為 150 ? 的錐形通孔,頂部直徑為 50 ?,底部直徑為 20 ?。所用電鍍液為 99.7 g/L CuSO?、10 g/L H?SO?和 50 ppm Cl?,添加新型抑制劑 A、促進(jìn)劑 B 和整平劑 C,沉積電流密度為 0.5 ASD(安培每平方分米)、1 ASD 和 1.5 ASD。在第一個(gè)實(shí)驗(yàn)中,抑制劑、促進(jìn)劑和整平劑的比例為 501.25,在 1 ASD 下 2.25 小時(shí)內(nèi)通孔完美填充,無空洞。在抑制劑濃度較低時(shí),抑制劑和加速劑的協(xié)同作用導(dǎo)致通孔表面厚度增加,從而增大了通孔頂部和底部之間的表面厚度差異。然而,隨著抑制劑濃度的增加,抑制劑 A 分子優(yōu)先吸附在通孔表面,從而減慢了沉積速率。結(jié)果,通孔表面厚度減小,頂部和底部的表面鍍層始終保持不變。因此,在抑制劑、加速劑和整平劑比例為 601 的情況下,在 1.5 ASD 的較高電流密度下,通孔在 1.5 小時(shí)內(nèi)完美填充,沒有空洞。
Jin 等研究了 TGV 填銅過程中用作整平劑的 PVP (聚乙烯吡咯烷酮) 的分子量對(duì) Cu 表面抑制層形成的影響。實(shí)驗(yàn)采用含有 0.94 M CuSO?、0.31 M H?SO?、2 mM HCl 的水系電解液,其中抑制劑為 PEG (聚乙二醇)、促進(jìn)劑為雙(3-磺丙基)二硫化物 (SPS),整平劑 PVP 的分子量分別為 10,000、29,000、360,000 和 1,300,000 g/mol。實(shí)驗(yàn)中使用的 TGV 高度為 400 μm,為錐形結(jié)構(gòu),開口直徑為 80 μm,中點(diǎn)直徑為 40 μm。結(jié)果表明,分子量較小的PVP(10,000 g/mol)在Cu表面形成了更致密的抑制層,有效地抑制了Cu電極的電鍍并實(shí)現(xiàn)了無缺陷填充。相反,分子量較大的PVP(360,000 g/mol)層致密性較差,含有許多可容納促進(jìn)劑的缺陷。這表明吸附的PVP分子之間的空間位阻隨分子量的增加而增大,阻礙了隨著分子量的增加在Cu表面形成致密的抑制層。研究發(fā)現(xiàn)聚合物添加劑的分子量會(huì)影響吸附物的結(jié)構(gòu)和競(jìng)爭(zhēng)吸附,這凸顯了選擇合適的聚合物添加劑對(duì)增強(qiáng)Cu填充過程性能的重要性。
在穩(wěn)定的直流電流波形下,通過添加劑優(yōu)化電鍍液對(duì)防止缺陷有很好的效果。然而,由于直流電流的性質(zhì),當(dāng)施加大電流時(shí),由于通孔位置的電流密度差異,完全防止空洞的產(chǎn)生具有挑戰(zhàn)性。為了解決這個(gè)問題,目前正在使用采用PPR(周期性脈沖反向)波形的電鍍方法。PPR波形由脈沖電流、反向脈沖電流和關(guān)閉脈沖周期組成,通過重復(fù)脈沖和反向脈沖電流與關(guān)閉脈沖,實(shí)現(xiàn)通孔的超共形填充。在脈沖電流周期內(nèi),Cu鍍?cè)谕變?nèi),在反向脈沖周期內(nèi),過鍍的Cu層溶解回來。在關(guān)閉脈沖期間,銅離子擴(kuò)散回電鍍液中,平衡通孔內(nèi)的離子濃度,防止表面優(yōu)先鍍銅。
激光加工的 TGV 通常具有錐形通孔結(jié)構(gòu),根據(jù)激光鉆孔方法的不同,通孔的一側(cè)或兩側(cè)可以具有斜坡。研究人員使用 PR 和 PPR電流研究了直通孔和錐形 Si 通孔中 Cu 的填充程度。在相同的 PR 電流條件下,電流密度為 2.29 mA/cm2 時(shí),直通孔的填充率最高為 45%,而電流密度為 3.04 mA/cm2 時(shí),錐形通孔的最大填充率為 71%,這表明錐形通孔的填充率高于直通孔。
在 PPR 電流波形中,錐形通孔在平均電流密度為 5.85 mA/cm2 時(shí)顯示出 100% 的 Cu 填充率,總體而言,PPR 波形的填充率高于 PR。圖 5是根據(jù) PR 和 PPR 波形中的電流密度表示垂直和錐形通孔的 Cu 填充率。
圖 5 根據(jù) PR 和 PPR 電流密度計(jì)算的直通孔和錐形通孔的 Cu 填充率(電鍍時(shí)間:1小時(shí))
關(guān)于使用 PPR 波形進(jìn)行電鍍,研究人員進(jìn)行了一項(xiàng)分階段 PPR 研究,使用三種電流密度水平來改善處理時(shí)間。在初始階段,采用低電流密度對(duì)通孔的入口、壁和底部進(jìn)行保形電鍍。在中間階段,采用中等電流密度對(duì)通孔內(nèi)部進(jìn)行超保形電鍍,最后采用高電流密度將通孔完全填充為銅。因此,最后階段補(bǔ)償了初始階段和中間階段在低電流密度下所花費(fèi)的時(shí)間,實(shí)現(xiàn)了缺陷最小化的銅電鍍。這些結(jié)果證明了優(yōu)化電流波形對(duì)于快速可靠地填充銅的重要性。
在TSV的Cu填充中,采用不添加任何添加劑的PPR電流波形實(shí)現(xiàn)了無空洞填充。Zhu等的實(shí)驗(yàn)中,對(duì)直徑 50? 的TSV施加 0.4 A/dm2 的脈沖電流和 -0.8 A/dm2 的反向脈沖電流,可得到V型銅層生長(zhǎng)并實(shí)現(xiàn)無空洞超共形電鍍。根據(jù)電流波形比較結(jié)果可知,以與脈沖電流相同的 0.4 A/dm2 進(jìn)行的直流電鍍內(nèi)部存在較大的空洞。反向脈沖有助于Cu的溶解,有助于銅層的V型生長(zhǎng),而負(fù)脈沖延長(zhǎng)了銅離子的擴(kuò)散時(shí)間,使通孔內(nèi)的離子濃度保持平衡。然而,在使用PPR電鍍Cu時(shí),電流密度的增加會(huì)導(dǎo)致通孔底部形成倒V型結(jié)構(gòu),從而產(chǎn)生空洞。圖 6是在 (a) 高電流密度和 (b) 低電流密度下使用 PPR 進(jìn)行 Cu 填充的示意圖。隨著電流密度的降低,通孔頂部形成的直接 V 結(jié)構(gòu)增加,并且在低電流密度下,直接 V 結(jié)構(gòu)優(yōu)于倒 V 結(jié)構(gòu),從而實(shí)現(xiàn)無空洞填充。
圖 6采用 PPR 電流的 Cu 填充過程示意圖,(a) 高電流密度,(b) 低電流密度
Inoue 等人通過化學(xué)鍍 Cu 薄膜形成和鍍 Cu 證實(shí)了 8 英寸無堿玻璃晶片上的 TGV 中 Cu 的均勻填充。
前人研究多為自下而上的分段電鍍方式,Cu從底部向頂部積累,而Ke等研究了一種雙面電鍍工藝。雙面電鍍是一種同時(shí)對(duì)靶材兩面進(jìn)行電鍍的方法,適用于需要在基材兩面進(jìn)行電鍍的情況。實(shí)驗(yàn)中以Ti作為擴(kuò)散阻擋層,Cu作為種子層,通過調(diào)節(jié)電流密度、添加劑、鍍液等參數(shù)實(shí)現(xiàn)均勻無空洞的TGV填充。雙面電鍍工藝存在鍍液流速不均、基材兩面存在差異等問題,需要在電鍍的各個(gè)階段調(diào)整電流和參數(shù)。但與分段電鍍相比,雙面電鍍有填充時(shí)間更快、適用于兩面圖案不同的基材等優(yōu)勢(shì)。
4. 結(jié)論
由于采用 TSV 技術(shù)集成 2.5D 和 3D 硅芯片和中介層,高密度、高性能半導(dǎo)體封裝領(lǐng)域取得了重大進(jìn)展。雖然 TSV 具有增加互連密度和縮短信號(hào)路徑等優(yōu)勢(shì),但人們?nèi)栽谂朔淙秉c(diǎn),包括電氣損耗、基板翹曲和高制造成本。作為解決 TSV 技術(shù)缺點(diǎn)的替代方案,基于玻璃的 TGV 在絕緣性能、成本效益和高頻域適用性方面具有優(yōu)勢(shì)。此外,由于其可變的 CTE 值,它們可以有效緩解堆疊設(shè)備(例如 2.5D 和 3D 結(jié)構(gòu))中的翹曲。因此,它作為下一代半導(dǎo)體封裝技術(shù)備受關(guān)注,目前正在進(jìn)行大量研究。由于玻璃基板、TGV 鉆孔技術(shù)、功能層涂層和 Cu 填充工藝的不斷進(jìn)步,該技術(shù)有望提高半導(dǎo)體封裝領(lǐng)域的性能、可靠性和成本效率。
-
半導(dǎo)體
+關(guān)注
關(guān)注
334文章
27363瀏覽量
218712 -
封裝
+關(guān)注
關(guān)注
126文章
7901瀏覽量
142959 -
基板
+關(guān)注
關(guān)注
2文章
276瀏覽量
23014
原文標(biāo)題:高性能半導(dǎo)體封裝TGV技術(shù)最新進(jìn)展
文章出處:【微信號(hào):深圳市賽姆烯金科技有限公司,微信公眾號(hào):深圳市賽姆烯金科技有限公司】歡迎添加關(guān)注!文章轉(zhuǎn)載請(qǐng)注明出處。
發(fā)布評(píng)論請(qǐng)先 登錄
相關(guān)推薦
先進(jìn)封裝中互連工藝凸塊、RDL、TSV、混合鍵合的新進(jìn)展
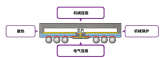
揭秘超以太網(wǎng)聯(lián)盟(UEC)1.0 規(guī)范最新進(jìn)展(2024Q4)
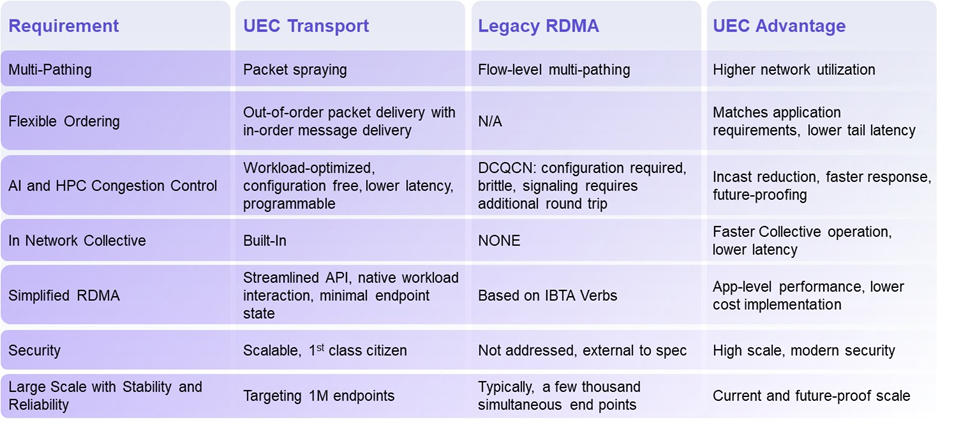
Qorvo在射頻和電源管理領(lǐng)域的最新進(jìn)展
芯片和封裝級(jí)互連技術(shù)的最新進(jìn)展
高燃回顧|第三屆OpenHarmony技術(shù)大會(huì)精彩瞬間
5G新通話技術(shù)取得新進(jìn)展
華源智信榮獲2024世界半導(dǎo)體大會(huì)兩大獎(jiǎng)項(xiàng)
百度首席技術(shù)官王海峰解讀文心大模型的關(guān)鍵技術(shù)和最新進(jìn)展
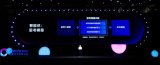
綜述:高性能銻化物中紅外半導(dǎo)體激光器研究進(jìn)展
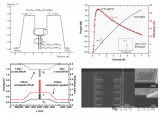
開啟高性能芯片新紀(jì)元:TSV與TGV技術(shù)解析

面向先進(jìn)封裝的電鍍技術(shù)新進(jìn)展
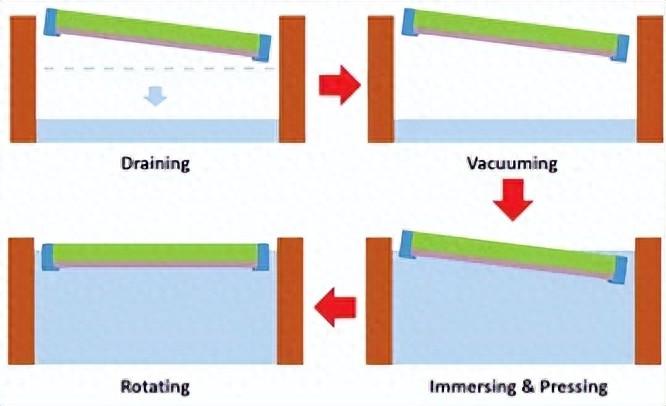
評(píng)論