在現(xiàn)代制造業(yè)中,CNC 加工技術(shù)廣泛應(yīng)用于各類精密零部件的生產(chǎn)。然而,傳統(tǒng)的 CNC 上下料方式多依賴人工操作或簡單的自動化設(shè)備,存在諸多局限性。隨著科技的不斷進(jìn)步,復(fù)合機器人的出現(xiàn)為 CNC 上下料帶來了創(chuàng)新性的解決方案,它集成了多種先進(jìn)技術(shù)與功能,正逐漸成為制造業(yè)智能化轉(zhuǎn)型的關(guān)鍵推動力量。
什么是復(fù)合機器人?
復(fù)合機器人通常融合了移動機器人的自主導(dǎo)航與運動能力、工業(yè)機器人的高精度操作能力以及智能感知與控制系統(tǒng)。這種集成化設(shè)計使其能夠在復(fù)雜的工業(yè)環(huán)境中靈活穿梭,并精準(zhǔn)地完成各類上下料任務(wù),極大地提高了生產(chǎn)的柔性與自動化程度。
某汽車零部件制造企業(yè)
項目背景
某大型汽車零部件制造企業(yè)擁有多條 CNC 生產(chǎn)線,主要生產(chǎn)發(fā)動機缸體、缸蓋等關(guān)鍵部件。以往采用人工上下料方式,面臨著工人勞動強度大、生產(chǎn)效率難以進(jìn)一步提升、產(chǎn)品質(zhì)量受人為因素影響較大等問題。同時,隨著訂單量的不斷增加,企業(yè)急需提高產(chǎn)能并降低生產(chǎn)成本,以滿足市場競爭的需求。
解決方案
系統(tǒng)配置
該企業(yè)引入了一套由移動機器人底盤、六軸工業(yè)機器人手臂、視覺識別系統(tǒng)以及智能控制系統(tǒng)組成的復(fù)合機器人系統(tǒng)。移動機器人底盤采用激光導(dǎo)航技術(shù),可在車間內(nèi)自主規(guī)劃路徑,靈活穿梭于不同的 CNC 機床之間;六軸工業(yè)機器人手臂具備高精度重復(fù)定位能力,能夠精準(zhǔn)抓取和放置零部件;視覺識別系統(tǒng)用于快速識別待加工零部件的位置與姿態(tài)信息,確保機器人抓取的準(zhǔn)確性;智能控制系統(tǒng)則負(fù)責(zé)協(xié)調(diào)各部分的協(xié)同工作,實現(xiàn)整個上下料過程的自動化與智能化。
工作流程
在生產(chǎn)過程中,當(dāng) CNC 機床加工完成后,發(fā)出下料信號。復(fù)合機器人接收到信號后,移動機器人底盤根據(jù)預(yù)先規(guī)劃的路徑迅速移動至機床旁。此時,視覺識別系統(tǒng)啟動,對機床工作臺上的已加工零部件進(jìn)行快速掃描與定位。獲取準(zhǔn)確位置信息后,工業(yè)機器人手臂按照預(yù)設(shè)程序精準(zhǔn)抓取零部件,并放置到移動機器人底盤上的物料架中。隨后,復(fù)合機器人移動至物料緩存區(qū),將加工好的零部件卸下,并同時抓取待加工的毛坯件。最后,復(fù)合機器人再次移動至 CNC 機床旁,將毛坯件準(zhǔn)確地放置到機床工作臺上,啟動機床開始新一輪的加工。
應(yīng)用效果
1.生產(chǎn)效率顯著提升
采用復(fù)合機器人進(jìn)行 CNC 上下料后,該企業(yè)每條生產(chǎn)線的生產(chǎn)效率提高了近 30%。由于機器人能夠 24 小時不間斷工作,且上下料速度快、動作精準(zhǔn),大大縮短了單個零部件的加工周期,有效提高了設(shè)備利用率。
2.產(chǎn)品質(zhì)量穩(wěn)定性增強
復(fù)合機器人的高精度操作有效避免了人工操作可能帶來的誤差與損傷,使得產(chǎn)品的加工精度和質(zhì)量穩(wěn)定性得到了顯著提升。產(chǎn)品的廢品率從原來的 3% 降低至 1% 以內(nèi),極大地減少了原材料浪費和質(zhì)量成本。
3.人力成本大幅降低
原本每條生產(chǎn)線需要配備多名工人進(jìn)行上下料操作,引入復(fù)合機器人后,每條生產(chǎn)線僅需少量工人進(jìn)行設(shè)備監(jiān)控與維護,人力成本降低了約 50%。同時,也緩解了企業(yè)招工難、用工成本高的問題。
審核編輯 黃宇
-
機器人
+關(guān)注
關(guān)注
211文章
28418瀏覽量
207097 -
CNC
+關(guān)注
關(guān)注
7文章
312瀏覽量
35164
發(fā)布評論請先 登錄
相關(guān)推薦
智能柔性制造:AMR 復(fù)合機器人賦能 CNC 加工行業(yè)
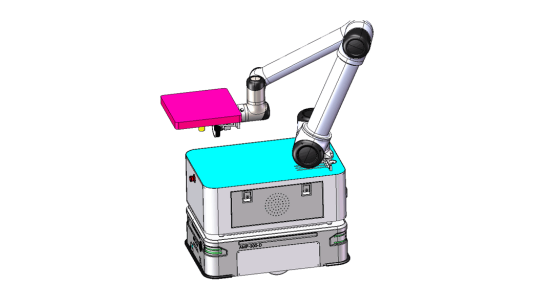
新技術(shù)解決方案 復(fù)合機器人 CNC 自動上下料
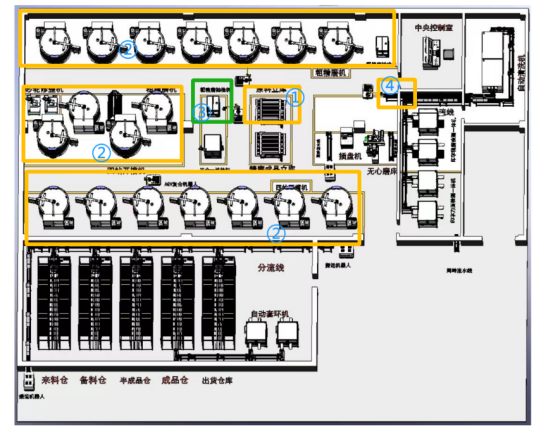
技術(shù)方案 復(fù)合機器人應(yīng)用在cnc數(shù)控加工行業(yè)
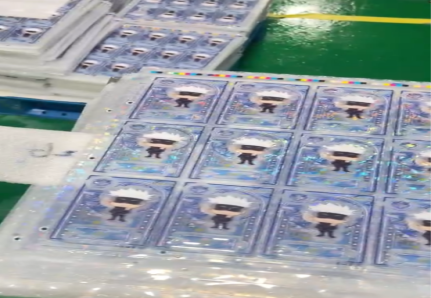
復(fù)合機器人:CNC 行業(yè)上下料的高效變革者
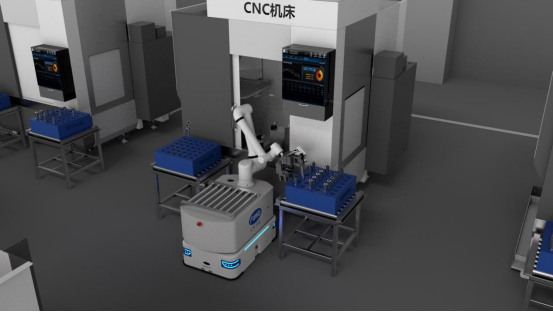
復(fù)合機器人在3c電子行業(yè)的應(yīng)用
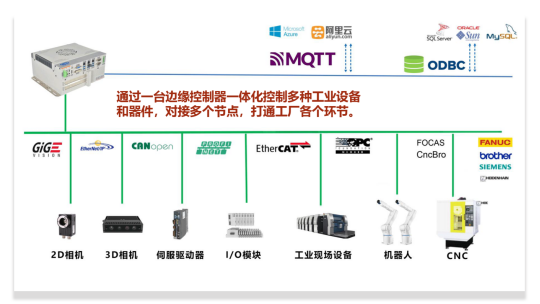
AMR復(fù)合機器人:鋁板CNC加工線上的智能‘搬運工’
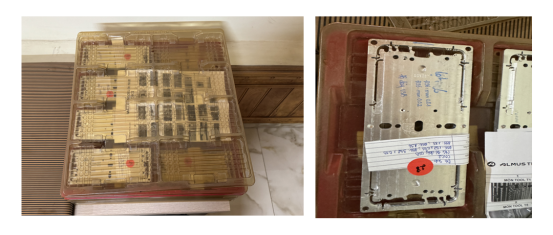
復(fù)合機器人在汽車零部件上下料中的應(yīng)用
復(fù)合機器人在CNC行業(yè)的成功案例:革新生產(chǎn)方式的里程碑
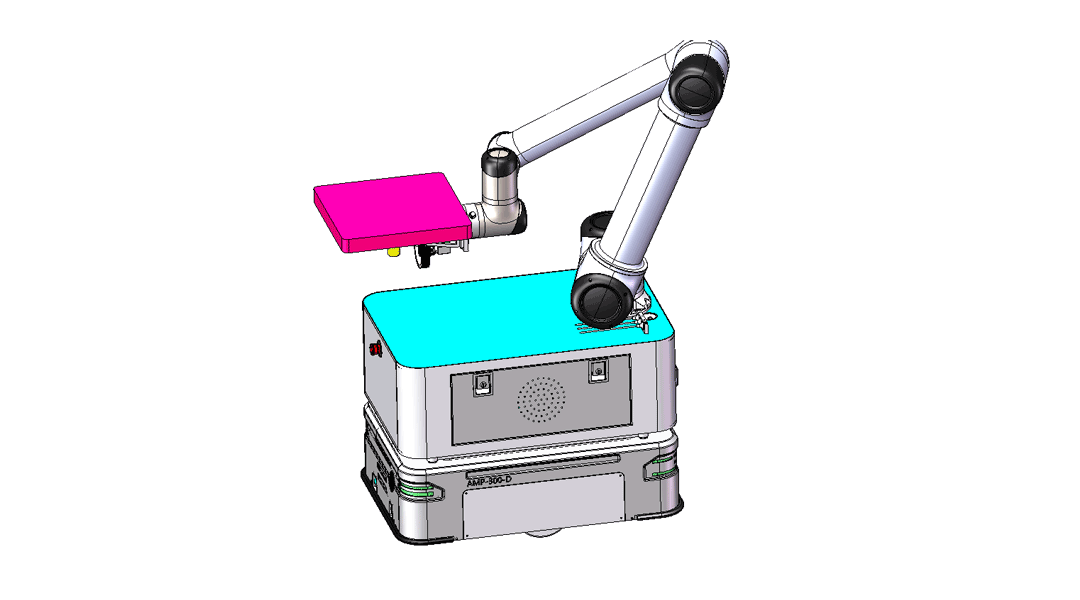
CNC機床加工上下料自動化解決方案
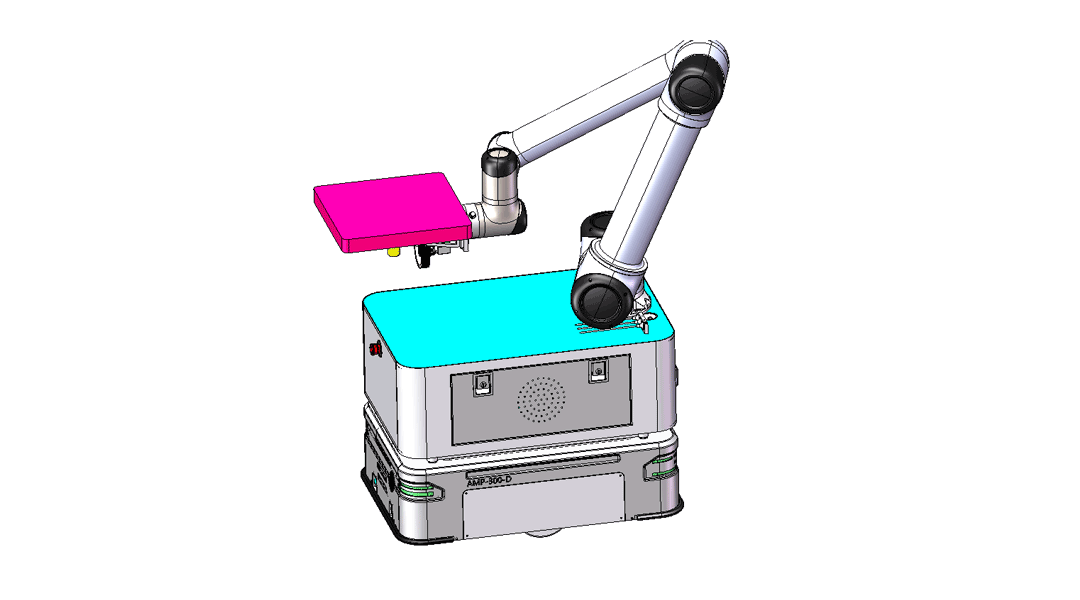
AMR復(fù)合機器人助力CNC加工行業(yè)解決人力成本問題
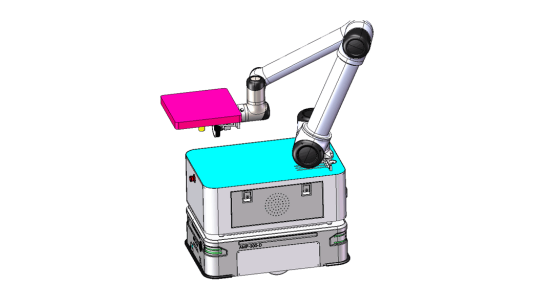
解決方案|AMR復(fù)合機器人亞克力板CNC上下料
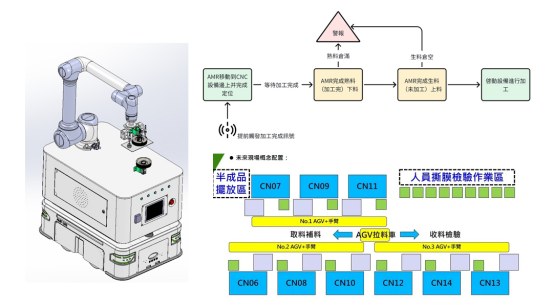
復(fù)合機器人CNC柔性上下料
富唯智能復(fù)合機器人CNC自動上下料解決方案
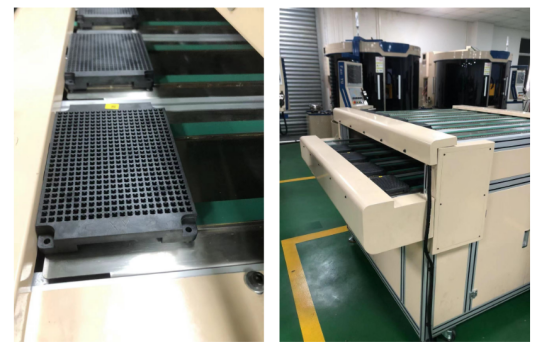
復(fù)合機器人在磁鋼上下料中的應(yīng)用及其優(yōu)勢分析
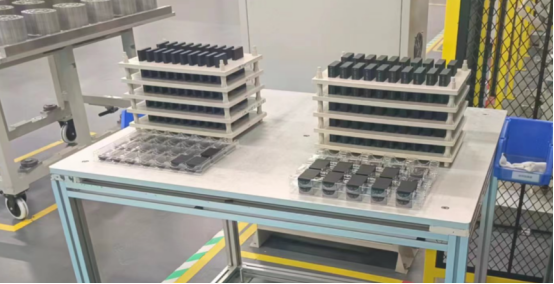
評論