在當今競爭激烈的制造業領域,鍛壓設備工廠面臨著諸多挑戰,從成本控制到生產效率提升,每一個環節都關乎著企業的生死存亡與長遠發展。而數字孿生技術的出現,宛如一盞明燈,為眾多鍛壓設備工廠照亮了一條通往降本增效的光明大道。明達技術集團級IOT平臺基座通過定制化開發、部署,可實現設備工廠場景數字化重建,助力企業降本增效。
數字孿生,打造虛擬與現實的精準映射
數字孿生,簡單來說,就是為現實世界中的物理實體創建一個數字化的虛擬模型,這個模型不僅有著和物理實體一模一樣的外觀、結構,更重要的是它能夠實時反映物理實體的狀態、性能以及運行數據等。對于鍛壓設備工廠而言,一臺臺龐大且復雜的鍛壓設備都有了它們的 “數字雙胞胎”。從設備的整體框架到內部的每一個零部件,從液壓系統的壓力變化到電機的運轉參數,所有的一切都能在虛擬模型中清晰呈現并且實時更新。
數字化改造,優化生產流程
借助明達技術的數字孿生技術開啟的數字化改造,讓鍛壓設備工廠的生產流程得到了前所未有的優化。
例如,在生產過程中,數字孿生模型實時監測設備的運行狀態,如果發現某個零部件有磨損加劇或者即將出現故障的趨勢,系統會立即發出預警。維修人員可以提前準備好相應的零部件,在設備還未出現故障停機之前就進行精準維護,大大減少了因設備突發故障而導致的生產中斷時間,降低了維修成本。而且,基于數字孿生的大數據分析,還可以對設備的操作參數進行動態調整優化,進一步提高產品的質量穩定性,減少因質量問題帶來的返工成本。
降本增效,收獲實實在在的成果
數字孿生帶來的降本增效成果,在鍛壓設備工廠的運營中體現得淋漓盡致。
成本方面,設備維護成本得到了顯著降低。過去那種定期大規模檢修、預防性更換零部件的方式耗費了大量的人力、物力和財力。而現在通過精準的故障預測和針對性維護,減少了不必要的零部件更換和維修工時。
在效率提升上,生產效率有了質的飛躍。設備的整體運行時間更加合理,停機時間大幅縮短,產能得到了充分釋放。以一家中等規模的鍛壓設備工廠為例,在引入數字孿生技術進行數字化改造后,年產能提升了近 30%,訂單交付周期也縮短了不少,極大地增強了企業在市場上的競爭力,贏得了更多客戶的信賴和訂單。
總而言之,數字孿生技術正在成為鍛壓設備工廠實現數字化轉型、降本增效的有力武器。越來越多的工廠通過擁抱這一前沿技術,打破傳統生產模式的局限,在激烈的市場競爭中脫穎而出,書寫著屬于自己的高質量發展新篇章,也為整個鍛壓設備制造業的升級注入了強大動力。相信在未來,會有更多的工廠踏上這條數字化改造之路,共同邁向更加高效、智能的制造新時代。
-
數字化
+關注
關注
8文章
8820瀏覽量
61994 -
IOT
+關注
關注
187文章
4225瀏覽量
197219 -
數字孿生
+關注
關注
4文章
1341瀏覽量
12298
發布評論請先 登錄
相關推薦
MBox20邊緣計算網關助力各種數字化升級
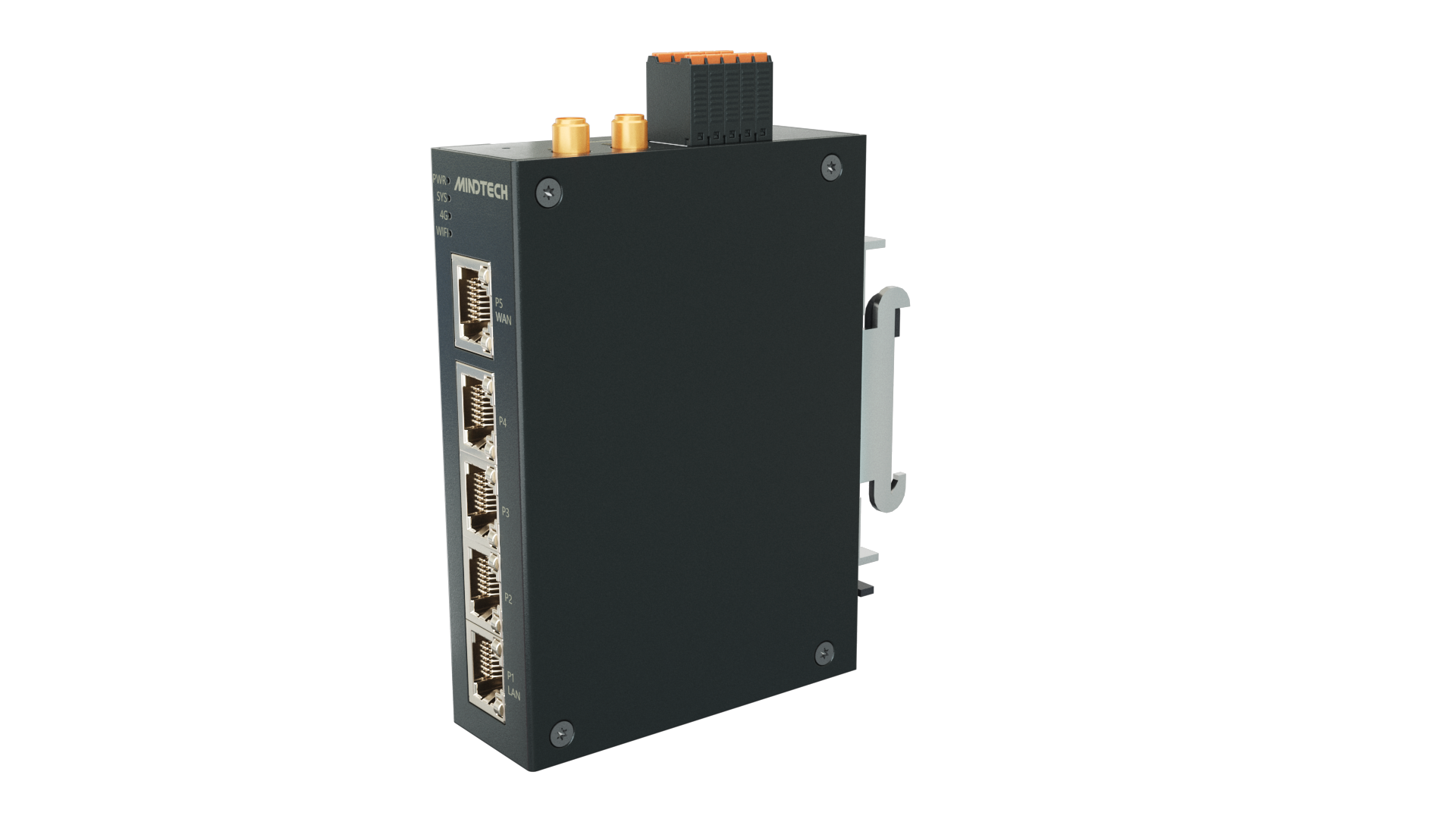
數據輕松上云——明達Mbox邊緣計算網關
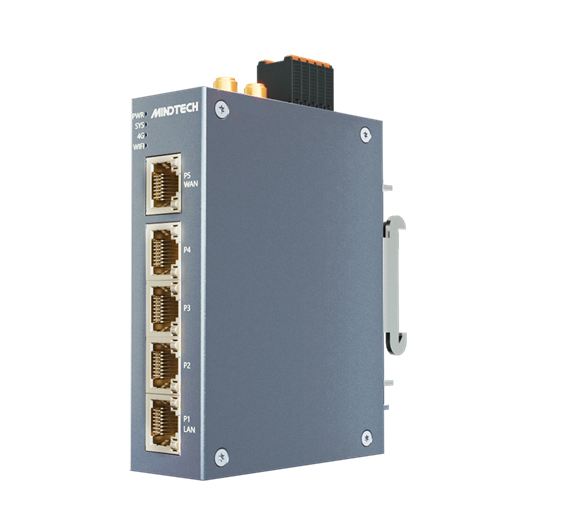
在"雙碳"目標下,如何實現工廠的數字化改造升級
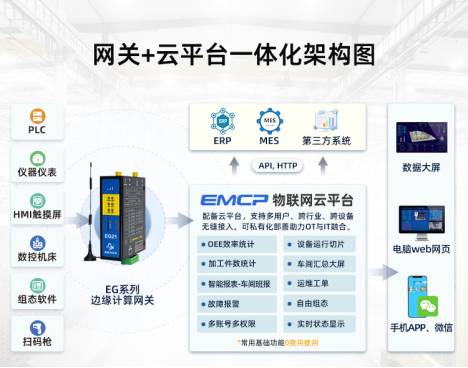
評論