Hello,大家好,今天我們來聊聊什么是先進封裝中的Bumping?
Bumping:凸塊,或凸球,先進封中的基礎工藝。
Bumping,指的是在晶圓切割成單個芯片之前,于基板上形成由各種金屬制成的“凸塊”或“凸球”。晶圓凸塊為倒裝芯片或板級半導體封裝的重要組成部分,已成為當今消費電子產品互連技術的標準。凸塊在管芯和襯底之間提供比引線鍵合更短的路徑,以改善倒裝芯片封裝的電氣、機械和熱性能。 倒裝芯片互連可減少信號傳播延遲,提供更好的帶寬,并緩解功率分配的限制。
不同類型的凸塊材料,其互連方法有所不同。凸塊按照材料成分來區分,主要 包括以銅柱凸塊(Cu Pillar)、金凸塊(Au Bump)、鎳凸塊(Ni Bump)、銦凸塊(In Bump)等為代表的單質金屬凸塊和以錫基焊料為代表的焊料凸塊(Solder Bump)及聚合物凸塊等。凸塊互連相關技術包括材料選擇、尺寸設計、凸塊制造、互連工藝 及可靠性和測試等。不同的凸塊材料,其加工制造方法各不相同,對應的互連方法和互連工藝中的焊(黏)接溫度也不盡相同。
晶圓凸塊技術制作過程復雜,需要清洗、濺鍍、曝光、顯影、電鍍去膠、蝕刻和良品測試等環節,其對應材料需求為清洗液、靶材、電鍍液、光刻膠、顯影液、 蝕刻液等。主要的工藝步驟如下:
1.采用濺射或其他物理氣相沉積的方式在晶圓表面沉積一層鈦或鈦鎢作為阻擋層,再沉積一層銅或其他金屬作為后面電鍍所需的種子層。在沉積金屬前,晶圓先進入濺射機臺的預清潔腔體,用氬氣等離子去除焊盤金屬表面的氧化層。
2.在晶圓表面旋涂一定厚度的光刻膠,并運用光刻曝光工藝,以改變其在顯影液中的溶解度。光刻膠與顯影液充分反應后,得到設計所需的光刻圖形。
3.晶圓進入電鍍機,通過合理控制電鍍電流、電鍍時間、電鍍液液流、電鍍液溫度等,得到一定厚度的金屬層作為UBM(Under Bump Metallization,凸點下 金屬化層)。在有機溶液中浸泡后,圓片表面的光刻膠被去除;再用相應的腐蝕液去除晶圓表面UBM以外區域的濺射種子層和阻擋層。
4.在植球工序中,需要用兩塊開有圓孔的金屬薄板作為掩模板,位置與晶圓表面UBM的位置相對應。在植球前,先用第1塊金屬掩模板將助焊劑印刷到UBM 表面;再用第2塊金屬掩模板將預成型的錫球印刷到UBM上;
5.晶圓經過回流爐使錫球在高溫下熔化,熔化的錫球與UBM在界面上生成金屬間化合物,冷卻后錫球與UBM形成良好的結合。
采用電鍍的方式也可以得到焊球凸塊,即在電鍍UBM完成后,接著電鍍焊料; 去除光刻膠和腐蝕濺射金屬后,經過回流,得到焊球凸塊。電鍍方式也是銅柱凸塊和金凸塊加工的常用方法。
凸塊(bumping)工藝流程的主要8個步驟(來源華進半導體)電子器件向更輕薄、更微型和更高性能進步,促使凸塊尺寸減小,精細間距愈 發重要。凸塊間距(Bump Pitch)越小,意味著凸點密度增大,封裝集成度越高,難度越來越大。行業內凸點間距正在朝著20μm推進,而實際上巨頭已經實現了小于 10μm 的凸點間距。如果凸點間距超過 20μm,在內部互連的技術上采用基于熱壓鍵合(TCB)的微凸塊連接技術。面向未來,混合鍵合(HB)銅對銅連接技術可以 實現更小的凸點間距(10μm以下)和更高的凸點密度(10000個/mm2),并帶動帶寬和功耗雙提升。隨著高密度芯片需求的不斷擴大帶來倒裝需求的增長,Bumping 的需求將不斷提升,相關材料需求也將不斷提升。
-
芯片
+關注
關注
459文章
51845瀏覽量
432520 -
晶圓
+關注
關注
52文章
5064瀏覽量
128928 -
先進封裝
+關注
關注
2文章
444瀏覽量
434
原文標題:什么是先進封裝中的Bumping?
文章出處:【微信號:深圳市賽姆烯金科技有限公司,微信公眾號:深圳市賽姆烯金科技有限公司】歡迎添加關注!文章轉載請注明出處。
發布評論請先 登錄
相關推薦
盤點先進封裝基本術語
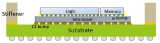
傳統封裝和先進封裝的區別
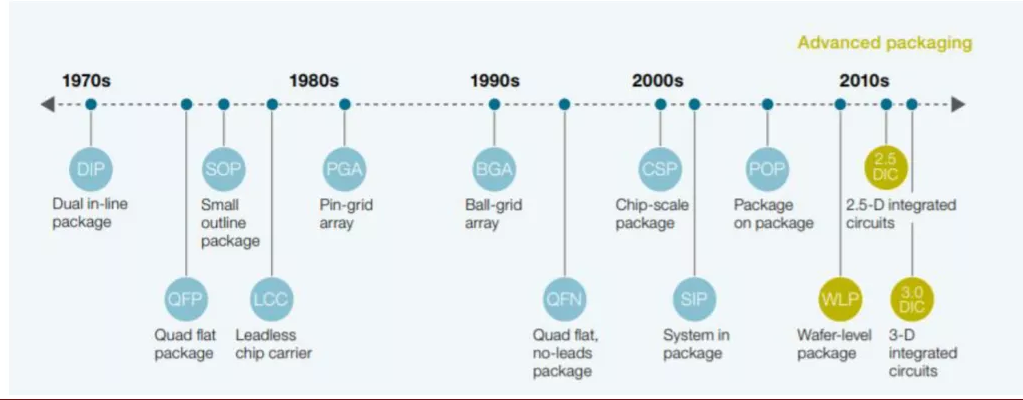
先進封裝技術及發展趨勢
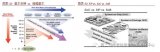
先進封裝對比傳統封裝的優勢及封裝方式
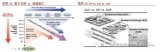
先進封裝呼聲漸漲 Chiplet或成延續摩爾定律新法寶
什么是先進封裝技術的核心
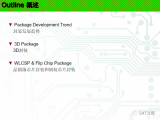
淺析先進封裝的四大核心技術
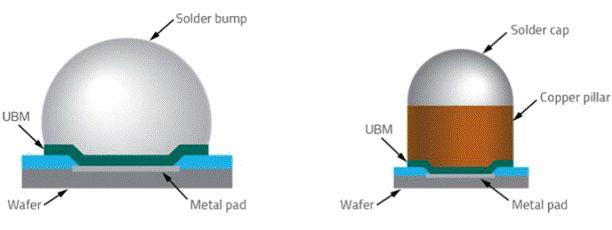
Bumping工藝流程工作原理 光刻工藝原理和流程
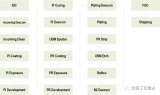
什么是先進封裝?先進封裝技術包括哪些技術
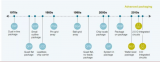
先進倒裝芯片封裝
半導體先進封裝技術
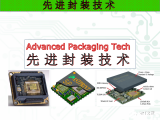
Bumping工藝升級,PVD濺射技術成關鍵推手
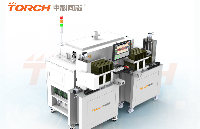
評論