本文介紹載帶自動焊接技術所用到的材料與基本工藝流程等。
TAB技術是將芯片組裝到金屬化的柔性高分子聚合物載帶(柔性電路板)上的集成電路封裝技術。屬于引線框架的一種互連工藝,通過引線圖形或金屬線連接芯片與外部框架或基板上的焊區。
載帶按照層次結構分為單層帶、雙層帶和三層帶。實際應用中以雙層帶和三層帶居多。載帶寬度有多種標準,包括35mm、70mm、8mm、16mm、45mm、158mm等,不同寬度適用于不同規模的集成電路。
載帶的基本材料
基帶材料
定義:基帶材料是帶狀絕緣薄膜,其上覆有銅箔刻蝕的引線框架,用于芯片封裝焊接。
形狀:類似于老式相機的膠卷或電影膠卷。
標準寬度:35mm、45mm、70mm。
厚度:50~100μm。
電路長度測量:以鏈輪距離為準,每個鏈輪節距約4.75mm,16個節距約76mm。
特點:耐高溫、與銅箔黏結性好、熱匹配性好、收縮率低、抗腐蝕性強、機械強度高、吸水率低。
常用材料:聚酰亞胺薄膜(最早廣泛使用,價格略高)、聚酯類材料薄膜、苯丙環丁烯薄膜。
組成:沖孔、剪切線、芯片、引線框架、聚酰亞胺薄膜、內引線和外引線。
金屬材料
定義:用于制作載帶引線圖形的材料。
用途:內引線和外引線用于制作載帶引線圖形。
特點:導電性能好、強度高、延展性強、表面平滑、與基帶材料黏結牢固、易于刻蝕精細復雜圖形、易于電鍍焊接。
常用材料:銅箔(最常用,寬度有18μm、35μm、70μm、158μm,其中35μm應用最多)、鋁箔。
凸塊材料
定義:用于在芯片焊墊上制作凸塊,再與銅箔內引線焊接的材料。
凸塊金屬材料:金、銅/金、金/錫、鉛/錫。
焊墊金屬:一般使用鋁膜制作,需先沉積黏附層金屬和阻擋層,防止外層凸塊材料和鋁材料互相擴散。
結構:可在芯片鋁焊墊層將凸塊制作在載帶焊接的銅箔引線上,稱為BumpTAB(凸塊載帶自動焊),凸塊結構呈梯形或矩形。
載帶自動焊接的工藝流程
載帶自動焊接是一種高效的集成電路封裝技術,其工藝流程主要包括以下幾個步驟:
制作引線框架:
在聚酰亞胺薄膜的基帶材料上,通過刻蝕等工藝制作引線框架。引線框架包括內引線和外引線,用于與芯片和基板進行電氣連接。
芯片對位放置:
將芯片精確地對位放置在引線框架上,確保芯片的焊墊與引線框架的內引線對準。
熱電極一次性焊接:
使用熱電極或超聲波焊接設備,一次性將所有的引線鍵合完成。這個過程實現了芯片與載帶之間的電氣連接。
標準化卷軸作業:
使用標準化的100m卷軸長帶進行作業,實現自動化的多點一次性焊接。芯片的貼裝和外引線的焊接電鍍已經實現了自動化,支持大規模生產。
內引腳鍵合與點膠:
內引腳通過鍵合工具將內引線與芯片的凸塊鍵合。使用點膠機將芯片點膠完成包封,再經過烤箱烘烤使膠硬化。
外引腳沖壓成型與沖斷:
當芯片完成了內引腳的鍵合和點膠之后,將外引腳沖壓成型。使用鍵合工具將載帶對位對齊后進行沖斷,將封裝后的芯片從載帶上完整地取下來。
載帶自動焊接的關鍵技術
載帶自動焊接的關鍵技術包括芯片凸塊的制作、載帶的制作、內外引線的焊接等。
芯片凸塊的制作:
凸塊是連接芯片焊墊與載帶內引線的關鍵結構。凸塊的形狀有蘑菇形和柱形(方形或圓形),設計原則需確保壓焊區的金屬全部被凸塊金屬所覆蓋,避免腐蝕和損傷。
凸塊制作形式主要分為在單層載帶上制作凸塊和在芯片焊墊上制作凸塊兩種。傳統的電鍍凸塊工藝流程復雜,技術難度高,生產成本也高。凸塊轉移技術可以簡化這一過程。
載帶的制作:
載帶是承載芯片和引線框架的柔性高分子聚合物。載帶的制作需要確保材料耐高溫、與銅箔的黏結性好、熱匹配性好等特性。載帶的寬度和厚度等參數需根據芯片規格和設計要求進行選擇。
內外引線的焊接:
內外引線的焊接是實現芯片與基板電氣連接的關鍵步驟。焊接過程需要確保焊接質量,防止虛焊、短路等問題。焊接方式包括熱壓焊接、超聲波焊接等。
凸塊轉移技術:
凸塊轉移技術是一種簡化凸塊制作過程的創新技術。
該技術通過在玻璃基板上先制作完成凸塊,然后將凸塊轉移到載帶的內引線上。凸塊轉移技術可以大大提高凸塊制作的一致性和生產效率。
載帶的制作工藝
載帶作為集成電路封裝中的重要組成部分,其制作工藝直接關系到封裝的質量和性能。以下是對載帶制作工藝的詳細分述:
載帶材料的選擇與設計
銅箔厚度:銅箔厚度的選擇主要由圖形的精細程度和引線的強度決定。一般來說,單層帶選擇厚度為50~70μm的銅箔以保持引線在制作和加工中的強度,以及引線焊點的引腳不共面。對于雙層、三層或雙金屬載帶,由于有聚酰亞胺的結構支撐,可以選擇厚度為18~35μm或更薄的銅箔。
焊接區鍍層:載帶的焊接區要有良好的鍍金層或鍍錫層,以提高焊接質量和可靠性。鍍層厚度一般為1μm左右。
引線寬度與間距:載帶的引線寬度通常為50μm,相鄰引線中心線的距離為100μm。這些參數的設計需根據芯片凸塊的精確位置、尺寸和間距來確定。
載帶類型選擇:根據用戶的要求及輸入輸出引腳的數量、產品的性能和成本來確定選擇使用單層、雙層、三層或雙金屬的載帶。
單層帶制作工藝
引線圖形成型:利用設計好的制版進行光刻、曝光、顯影及刻蝕處理,形成所需的引線圖形。
電鍍:在引線圖形上電鍍一層金屬,以提高引線的導電性和耐腐蝕性。
雙層帶制作工藝
制版準備:提前為兩面的制作做準備,一面刻引線圖形,另一面刻聚酰亞胺。
刻蝕處理:分別進行光刻、曝光、顯影及刻蝕處理,形成引線圖形和聚酰亞胺層。
電鍍與聚酰亞胺層結合:完成電鍍引線圖形后,與聚酰亞胺層結合,形成雙層載帶。
PA(Polyacrylate)涂層是聚丙烯酸酯類織物膠,具有防水、阻燃等多種功能,可用于雙層帶的某些特定部位以增加其性能。
三層帶制作工藝
材料準備:由銅-黏結劑-聚酰亞胺三層材料結合而成。銅箔厚度為18~25μm,黏結劑厚度為20~25μm,聚酰亞胺膜厚為70μm。
模具制作:先沖壓聚酰亞胺定位孔和框架孔,再涂黏結劑、涂敷銅箔,加熱加壓以黏附銅箔。
切割與沖壓:切割沖壓三層帶,形成所需的形狀和尺寸。
引線圖形制作:利用光刻、曝光、顯影及刻蝕處理,制作引線圖形。
雙金屬帶制作工藝
支撐框架制作:在聚酰亞胺薄膜上沖壓出引線圖形的支撐框架。
銅箔黏附:在兩面黏附銅箔。
雙面光刻:使用雙面光刻的方法在兩面制作出引線圖形。
局部電鍍:對兩個圖形聚酰亞胺框架之間的穿孔進行局部電鍍,實現上下金屬帶之間的金屬互連。
銅淀積與電鍍加厚:在框架的兩面先使用銅淀積工藝,再使用電鍍加厚法形成雙層銅箔。
光刻刻蝕:使用光刻法刻蝕出所需要的引線圖形。
載帶制作中的注意事項
引線寬度與間距的均勻性:確保引線寬度與間距的均勻性,以避免在焊接過程中產生短路或斷路現象。
鍍層的均勻性:鍍層應均勻附著在引線圖形上,以提高焊接質量和可靠性。
材料的選擇與匹配:根據具體的應用場景和要求選擇合適的材料,并確保各層材料之間的良好匹配。
制作工藝的精確性:在制作工藝過程中,應嚴格控制各個環節的工藝參數和條件,以確保載帶的質量和性能。
-
芯片
+關注
關注
456文章
50936瀏覽量
424665 -
TAB
+關注
關注
0文章
16瀏覽量
11562 -
自動焊接
+關注
關注
0文章
28瀏覽量
6391
原文標題:一文了解載帶自動焊接(TAB)技術
文章出處:【微信號:bdtdsj,微信公眾號:中科院半導體所】歡迎添加關注!文章轉載請注明出處。
發布評論請先 登錄
相關推薦
SMT貼裝基本工藝流程
倒裝晶片的組裝工藝流程
印制電路板制作工藝流程分享!
回流焊接技術的工藝流程詳解
SMT貼片加工的工藝流程及作用
機器人焊接工藝流程
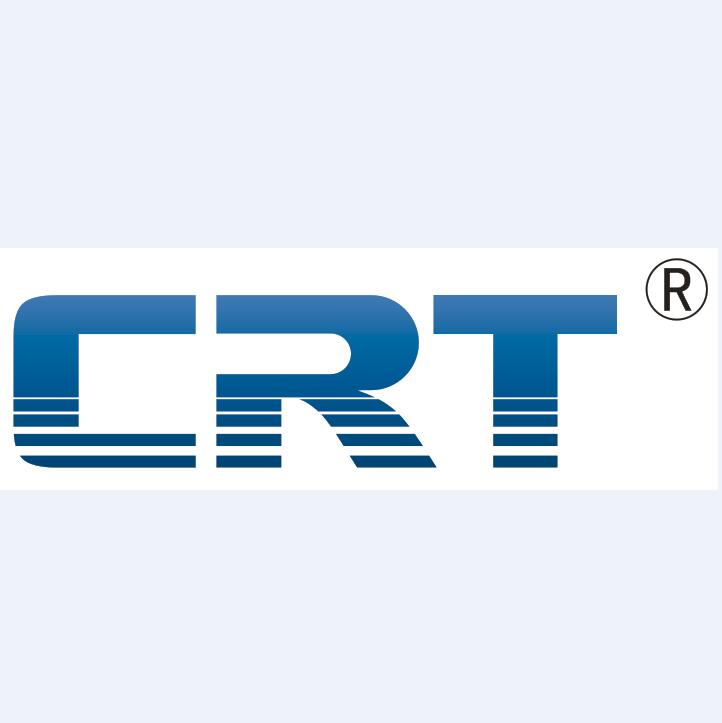
評論